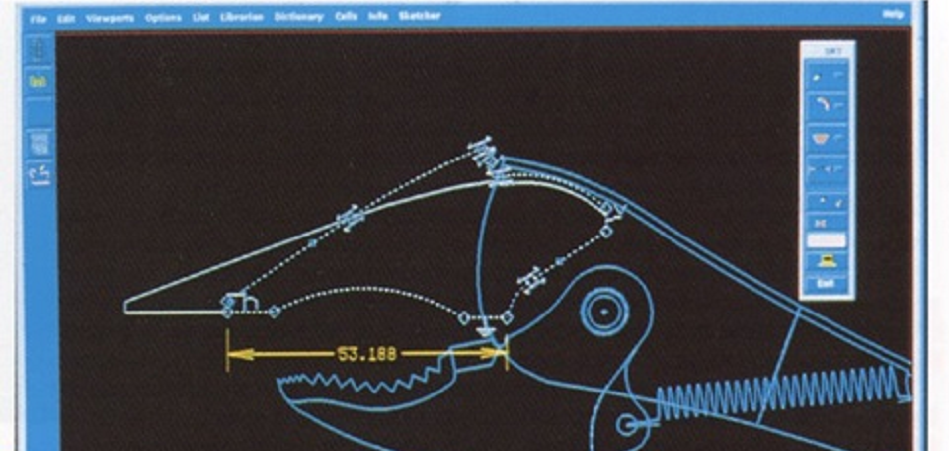
Applicon was founded in 1969 as Analytics, Inc. in Burlington, Massachusetts by a group of programmers from MIT’s Lincoln Laboratory where they had been working on advanced interactive graphics technology. The four principals, all of whom had Ph.D.s, were Gary Hornbuckle, Fontaine Richardson, Richard Spann and Harry Lee. Their work at Lincoln Lab included the development of a technique for command entry that involved sketching a pattern on a tablet with a stylus. Tablet pattern recognition for command entry would become one of the defining characteristics of the company’s products throughout its life time.
According to Richardson,[1] the founders frequently had lunch together at Lincoln Lab and often discussed Wall Street’s infatuation with technology startups. Many people forget that the late 1960s saw a high-tech boom similar to, although smaller, than what we would see repeated several times over the next three decades. One of the group’s models was Digital Equipment Corporation which had been started by Lincoln Lab engineers in 1957 and by 1969 was a major player in the computer industry. Professor Edward Roberts of MIT’s Sloan School did a study of startups, including those started by former Lincoln Lab employees. He presented his findings during a lecture at the Lab with a statement that 80 percent of the earlier startups were still viable five years later. This was like throwing gasoline on a fire and the four became determined to start a company.
The casual lunches turned into evening and weekend meetings with the conclusion that they should start a company that focused on their personal expertise and experience – software for designing electronics. After substantial discussion, Hornbuckle became the company’s president, Lee the chairman of the board, Spann the vice president of sales and marketing, and Richardson the vice president of product development. In reality, all the founders had a hand in developing the company’s early products.
Initial funding was provided by W. R. Grace and Company which arranged for an initial bank loan and subsequently purchased one sixth of the company for $400,000 in late 1969. General Electric invested in the company in 1972 and 1973 at the encouragement of early Applicon users within the company. Eventually, GE’s investment would represent a nearly 28 percent ownership of Applicon prior to the company’s initial public offering. J. H. Whitney, a venture capital firm that would later play a major role in Computervision’s demise, invested in 1974. Shortly after the company’s founding, they were informed that the name “Analytics” was already being used by another company.
Applicon was a made up name that was a contraction of the word “application.” The Computer Science Department at the University of Illinois at UrbanaChampaign has a short biography of Richardson on its web site. In 1968 he was the second person to receive a Ph.D. in computer science from that institution. According to this web site, Applicon’s plan was to develop a suite of four products. “One was for designing integrated circuit photomasks, one was for digital circuit simulation, one was for frequency domain circuit synthesis, and one for microwave circuit analysis.” Except for the mask layout program which required a stand-alone computer system, the software was intended to be sold on a timesharing basis. When a recession hit in 1969-1970, potential customers found it difficult to purchase software on an as-used expense basis. Applicon dropped the timesharing software and focused on the integrated circuit mask layout system which could be sold as capitalized equipment. This product soon became known as the “Design Assistant.” The company’s firstcustomer was Matsushita in Japan.[2]
The company’s initial interactive graphics solutions for designing printed circuit boards and integrated circuits used IBM’s 1130 computer with terminals consisting a storage tube display, keyboard and tablet. The terminals were designed and built by Computek, another MIT spin-off based in Cambridge, Massachusetts. The IBM 1130 was selected because it could be rented as well as sold, a financing issue the Applicon founders thought would help in some sales situations. About eight or ten of these systems were sold. Shortly thereafter, Applicon switched to Digital Equipment Corporation’s new PDP-11 and the company worked almost exclusively with Digital until well into the 1990s.
Applicon System Almost Goes Up in Smoke
The following story was related to the author by Fontaine Richardson In the early days, we had to deliver the system and get the installers to the site to make the installation and conduct the training. The customers paid the freight to transport the system, so, the obvious choice was to rent a truck, drive the system to the site, install the system and train the customers before driving home. Our first DA 700 system (The PDP-11 version of the product) was purchased by GE for Waynesboro, Virginia. It was delivered in late August 1971. Jim, the field service technician and I loaded the system in the back of the rental truck about 6:00 PM on a Sunday evening in Burlington, Massachusetts and drove south, intending to drive all the way through the night and deliver the system the first thing Monday morning. We got as far as Philadelphia when, in a driving rain, neither one of us could stay awake at 2:00 AM. We decided to find a hotel and get some sleep and go on the next morning. Jim was driving. I told him to drive under the hotel awning so I would not get wet when I went in to inquire if there were rooms available. The truck was taller than the awning and we hit it at about 5 miles per hour. This got the hotel’s night clerk’s attention. Despite this rude arrival, he did have a room for us. We parked the truck and started toward the hotel. I happened to look back at the truck and noticed an unusual amount of steam rising from the hood of the truck. This struck me as unusual and I went back to check on what was going on. I put my hand on the truck’s hood and it burned my hand. I didn’t think that this was typical. I looked into the front grill of the truck and saw flames. Always the person to avoid the risky work, I told Jim to stay at the truck and get the hood opened.
I ran to hotel to call the fire department and see if I could find a fire extinguisher. I awakened the hotel clerk again and asked him to call the fire department. I ran through the hotel until I found a soda acid type fire extinguisher and ran out to the truck. Jim had not been able to get the hood open and was of the opinion that a truck explosion was imminent. Our first and only system was in the back of the truck and I knew that I would have a difficult time explaining to the customer and the folks back home that I had let the system perish in a fire.
I turned the fire extinguisher upside down to activate it and pointed the hose through the grill of the truck at the base of the fire. I was able to put out the fire in what seemed like an eternity.
In the morning, we determined that there was a black scorch mark on the hood of the truck that had not been there when we left Burlington, so we hadn’t dreamed the fire. We looked under the hood and discovered that the gas line was loose and was dropping gas onto the hot engine manifold. This was less of a problem at highway speed, but flared up after the truck was parked.
We drove on to Waynesboro without further distraction. The scorched truck hood gave our story some credibility, although our customer was still skeptical.
Early marketing into the electronics industry tended to focus on the conceptual design departments of the target companies. This differed sharply from competitors such as Calma and Computervision which focused more on the production drafting groups at these companies. Sales grew from about $500,000 in 1971, to over $9 million in fiscal 1975 (company’s fiscal year ended on April 30th) and to over $18 million in 1978. A major financial bump in the road occurred in 1978 when sales stagnated and the company incurred a $700,000 loss.
Two key members of the company’s board of directors, Alex Daignault of W. R. Grace and Don Ackerman of J.H. Whitney, believed that the company was struggling to generate sales and needed a new product strategy if it were to be competitive in the future. They explored the possibility of the company being acquired but there were no acceptable offers. The other option was to bring in a new management team. Don Feddersen, who was recruited by Ackerman, had been president of Entrex, a vendor of educational software, until it was acquired by Nixdorf. Feddersen had also been general manager of Gould’s Data Systems Division. He became president and CEO of the company on April 19, 1978.
As a result of this management change, Applicon went from being a technology driven company to more of a business driven enterprise. Its primary competitors at the time were Computervision and Calma and to a lesser extent, Auto-trol Technology and M&S Computing (Intergraph). Feddersen controlled expenses fairly tightly – perhaps too tightly. One project he curtailed was the development of a stand-alone workstation using a TI-9900 microprocessor and raster graphics. Started in 1977, it would have been one of the first workstation products in the CAD industry.[3]
Hornbuckle left Applicon later that year. Lee had left the company fairly early and Spann, who had taken on the responsibility for advanced development and engineering, had left in 1976. Richardson, the last of the founders, stayed the longest, until shortly after the company went public in 1980. Hornbuckle founded a new graphics company, Impress, Inc., in 1980. Impress developed a system capable of scanning and editing engineering drawings, primarily for technical illustration. Around the same time, Spann joined Adage, a manufacturer of computer graphics terminals, as vice president of operations. He became CEO of Adage in 1978 and held this position until 1988. Both Spann and Richardson ended up in the venture capital industry. Spann founded PreFund Associates while Richardson was a long-time general partner at Eastech.
Description of early Applicon systems
During the 1970s and early 1980s Applicon’s products used the AGS nomenclature. AGS stood for Applicon Graphics System. The typical Digital PDP-11 system supported up to four terminals.
The key characteristic of Applicon’s AGS software was its pattern recognition command entry or what the company called Tablet Symbol Recognition. As an example, if the user wanted to zoom in on a specific area of a drawing, he would simply draw a circle around the area of interest with his tablet stylus and the system would regenerate the image displaying just the area of interest. A horizontal dimension was inserted by entering a dot followed by a dash while a vertical dimension line was a dot followed by a short vertical line. The underlying software was command driven and these tablet patterns simply initiated a sequence of commands. The system came with a number of predefined tablet patterns but users could create patterns to represent any specialized sequence of operations desired.
The initial AGS software was written in assembly language and for the most part, Applicon did not use a Digital provided operating system for its PDP-11 systems. This changed around 1978 when the company moved to the RSX-11M real time operating system and programming was increasingly done in FORTRAN. Also in 1978, Applicon introduced its first raster display terminal as an alternative to the storage tube. These early units had relatively poor resolution compared to storage tube terminals but they did not require images to be fully redrawn whenever something was moved or deleted. Shortly thereafter, Applicon was one of the first CAD companies to offer color raster terminals which added a new dimension to the visualization of design and analysis images.
The key system component at this time was a Digital PDP-11/34 minicomputer. Applicon repackaged this computer in its own cabinet along with its Graphics 32 processor and referred to the combined system as the AGS/895 Central Processing Facility. In addition to 208KB of main memory, the AGS/895 included a 200MB disk drive (expandable to 800MB) and a dual density (800/1600 bpi) magnetic tape drive. The Graphics 32 had its own 64KB memory and performed vector to raster conversion and patterned area filling for up to four terminals. The AGS/895 was capable of supporting four terminals plus four background tasks such as PCB routing. In the 1980 time period, Applicon offered ten different storage tube and color raster terminals for use with the AGS/895. (Applicon’s marketing department also used the “Image” nomenclature to describe these systems.) A typical system, probably with two or three terminals, sold for $300,000.
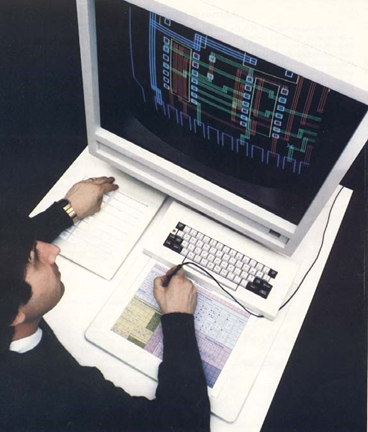
The basic system the company offered was called the AGS/900 Multi-Tasking Operating System which incorporated the AGS/895 Central Processing Facility running Digital’s RSX-11M operating system. The AGS/900 was the software framework for the company’s Interactive Multi-Activity Graphics Environment or IMAGE which enabled a single system to run both two-dimensional and three-dimensional software at the same time. The specific application-oriented products were called the AGS/870-I two dimensional and the AGS/880-I three-dimensional systems. The AGS/870-I was targeted at electrical design tasks, particularly the schematic and physical design of printed circuit boards while the AGS/880-I was intended for mechanical design and drafting. Numerous task-specific applications modules were available for these systems including PCB placement and routing, wire list generation, photoplotter output, bill of material generation, nesting and flame cutting flat pattern development and numerical control. The first mechanical system was sold to General Motors.
In addition to the AGS/900 systems, Applicon also offered the AGS/860 VLSI Graphics Application System which incorporated two-dimensional software tailored for the design and editing of VLSI circuit masks. It used the same interactive techniques of other Applicon systems plus a number of optional output packages specifically implemented to support VLSI artwork generation. The AGS/860 utilized the same AGS/895 Central Processing Facility as did the AGS/900 systems except that it supported a more limited number of terminals.
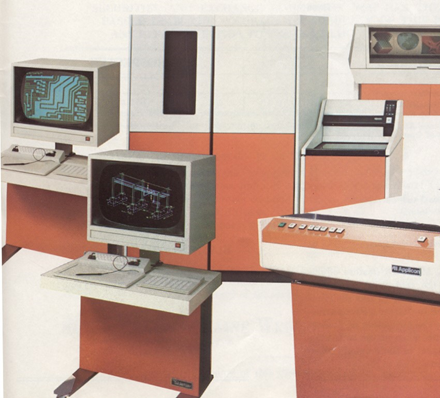
A key software component of the AGS/860 was the AGS/1610 Designer/MOS interactive design package. It provided a set of tools for designing and editing integrated circuits that took advantage of Applicon’s color graphics technology. Other specialized AGS/860 software included a Design Rule Check Package (AGS/862) which was used to verify the geometric layout of VLSI designs prior to producing specialized output. There were also output packages to support CalComp, Xynetics, Versatec and Applicon plotters as well as Mann and Electromask optical pattern generators. At the time, this was one of the leading integrated circuit design systems on the market, along with similar products offered by Calma and Computervision. Within a few years it would be overshadowed by a new generation of systems from companies such as Daisy and Mentor Graphics which introduced new design procedures that relied on logical definitions of circuits rather than pure graphics representations.
By 1981, over 90 percent of the company’s terminal shipments were raster devices, many of them color units. Applicon developed its own graphics processor – a 32-bit bit-sliced microcomputer system – that handled graphic tasks independently of the system’s central processor.
Like most other turnkey system vendors of that era, Applicon was interested in manufacturing as large a portion of the systems it sold as was feasible. This led Applicon to design and manufacture the industry’s first continuous ink jet color image plotter in 1977. The company had been approached by Walter Carnes from Arthur D. Little, a management consulting firm in Cambridge, concerning “Drop on Demand” ink jet technology that had been developed in Sweden by Helmut Hertz, the grandson of Heinrich Hertz, the German physicist who gave his name to our current measure of electronic frequency. ADL was looking for a licensee to manufacture and market a color plotter using this technology and Applicon was receptive to the offer. The expectation was that it could be sold to the company’s customers to produce plots of integrated circuits and maps.
The Applicon color plotter used three specially formulated inks (magenta, yellow and cyan) to produce plots with a resolution of 300 dots per inch. The paper ( up to 36inches by 48-inches) was held on a rotating drum and the print head was moved laterally from one end of the drum to the other with a stepper motor controlled lead screw. The rotation speed of the drum was user controlled and at its fastest speed it was capable of generating a 22-inch by 34-inch plot in as little as 8.5 minutes although high quality plots could take as much as five times as long to produce.
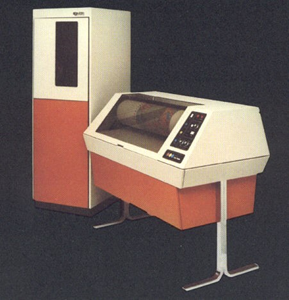
The plotter was not an on-line device but was controlled from a magnetic tape drive. Part of the system was Applicon’s COLOR software system, also licensed from a Swedish developer, which converted traditional vector and spatial data into the raster format required for plotting and placed that data on magnetic tape. The software could produce over 5,000 different color shades. The company promoted the color plotter for mapping, seismic data analysis, printed circuit board design and graphic arts applications but not as a mechanical design tool. It made up about six percent of the company’s revenue in 1980.
In the late 1970s Applicon established co-operative development and marketing agreements with several other companies. One of these was with Structural Dynamics Research Corporation (SDRC) that facilitated the integration of Applicon’s mechanical design software with SDRC’s Computer-Aided Engineering (CAE) software. See Chapter 17. This integration only worked on Digital PDP-11 systems running RSX-11/M software. A second agreement was with University Computing Company (UCC) which had developed its own APT software for programming machine tools called UCC-APT. In this environment, Applicon users could design parts and produce NC machining instructions and then use that information to generate either an APT source file or an APT CL (Cutter Line) file. This data was then processed by UCC’s APT software and library of post-processors to produce a control tape for a specific machine tool.
Even with the limited functionality of 1980 era Applicon software and the hardware performance limitations at the time, users were seeing significant productivity improvements. Customers such as Hughes Tool, Houston, Texas, were publicly stating that new designs were being completed in half the time as before.[6] Productivity was a big issue in 1980, particularly in the United States. The country was experiencing record inflation at the same time that the growth in productivity was unusually low. At the time, not many people linked the two issues together. Twenty years later, the country would experience very low inflation and high growth of productivity, a significant portion of which was due to the explosive use of CAD/CAM technology.
Public offering then Schlumberger acquisition
Feddersen came on board in April 1978 and by early 1980 he had Applicon back on track. Revenue for the year ending April 30, 1980 was up 78 percent to $50.8 million from the prior year and earnings were up nearly five-fold to $3.1 million. While the company’s strongest market segment was the electronics area, it clearly recognized that the greatest potential was for mechanical CAD systems.[7] Revenue and earnings for fiscal years ending April 30th were:
By 1980 there were over 500 Applicon systems in use, the staff had increased to 785 people and the company was building a 120,000 square foot manufacturing plant. This appeared to be an excellent time to go public and the company did so on July 22, 1980 by selling 1,045,000 shares at $22 per share. At the same time, investors who owned preferred shares and warrants converted their shares into common stock. Nearly a quarter of the money raised went to pay off bank loans the company had incurred to finance its rapid growth during the prior two years while the balance went to finance future expansion.
Key personnel as of mid-1980 were:
Donald Feddersen – President and CEO
Don Ackerman – Chairman of the board
David Barber – Vice president of marketing
Steven Cheheyl – Vice president of finance and treasurer
Richard Diephuis – Vice president of system development
Thomas Genova – Vice president of engineering
Robert McCormick – Vice president of international marketing
William Mason – Vice president of operations
Albert Moulton – Vice president of program product development
James Nitz – Vice president of sales
Fontaine Richardson – Vice president of industry marketing Prior to Applicon’s public offering, General Electric offered to buy the 72 percent of the company that it did not already own for $20 per share, or approximately $66 million.[8] When this offer was rejected, GE went shopping for another CAD/CAM vendor and eventually acquired Calma. GE, under pressure from the Federal Trade Commission, then sold its Applicon stock in mid-1981 in a secondary offering. At the same time, Applicon sold another 260,000 shares of stock at $33 per share. In mid-1981 Richardson left Applicon to become an independent consultant and visiting scientist at MIT.
When Applicon went public, about 20 percent of its revenue was from international customers. Half of this business was from Europe while Japan and the rest of the world made up the balance. Domestically, the company had 23 sales offices split into five sales regions as well as sales offices in six European countries. Applicon’s distributor in Japan was Marubeni Electronics. Overall, there were 192 people engaged in marketing, sales and sales support worldwide.
On September 7, 1981, Applicon shocked most industry observers when it announced that the company was being acquired by Schlumberger in a stock deal valued at approximately $232 million. Schlumberger was a French controlled company, chartered in the Netherlands Antilles and headquartered in New York. It was then and still is today a major supplier of various services to oil and natural gas producers. It also owned Fairchild Semiconductor and earlier in 1981had acquired MDSI, a vendor of numerical control software. With the acquisition of Applicon, MDSI withdrew its low cost COMPDRAW IV turnkey system from the market and reduced development work on solids modeling, leaving these areas to Applicon. The two companies became the core of what Schlumberger called its Computer-Aided Systems Group. Eventually Schlumberger would merge Applicon with MDSI and move the combined company’s headquarters to Ann Arbor, Michigan where MDSI was located, but that didn’t happen for several years. Initially, there was very little cooperation between Applicon and MDSI. Each company went its own way and that fit in with Schlumberger’s style of highly decentralized management.
In an attempt to broaden its mechanical product line, Applicon had earlier signed the previously mentioned development and marketing agreement with SDRC. Under this agreement Applicon was reselling SDRC’s Supertab finite element modeling software and SDRC had set up half a dozen automated design service centers in the United States and Europe that were equipped with Applicon systems. Customers could rent these systems for $50 per workstation hour or hire SDRC designers and drafters to do the work for them. By early 1982, the working relationship between the two companies had become somewhat strained. At the same time, a group of SDRC managers were considering establishing their own company to develop and market CAE software. This group consisted of Dick Miller, Rex Smith, Paul Vollbracht and Vic Nicolas as well as Jim Brown who was with General Electric, an SDRC business partner as discussed in Chapter 17.
The group approached Feddersen with an offer to develop CAE software for Applicon. Eventually, Jason (Jack) Lemon, the CEO of SDRC, found out that Smith was involved in this endeavor and accused him of planning to leave the company. Smith relayed that information to the other individuals who then contacted Feddersen to see if he was the one who had told Lemon. Feddersen’s response was an offer to hire the group as Applicon employees and set up an office for them near Cincinnati. Shortly after hiring this group in the spring of 1982, Feddersen also hired Russ Henke, SDRC’s then president and COO. Henke’s job at Applicon was to head up the company’s mechanical activities. After Henke came on board he asked Miller to move to Boston and become marketing manager for the mechanical group and Smith to take over software development. Smith basically commuted to Boston rather than relocating.
Introduction of solids modeling software
In June 1981, Applicon made its first move into solids modeling by licensing a software package called Synthavision from MAGI (Mathematical Applications Group, Incorporated) located in Elmsford, New York. The software, called simply Solids Modeling by Applicon, ran on Digital’s VAX 11/780 and 11/750 systems. The actual implementation was somewhat awkward, however. The user created a wireframe threedimensional model on Applicon’s PDP-11 AGS system and then transferred the data to the VAX computer where Synthavision created a solids model based upon the transferred data using 14 different primitive shapes, an operation that typically took several minutes. The model could then be viewed on a color terminal attached to the VAX. The data transfer was via DECnet, which was by now a standard Applicon product, or on magnetic tape.
Once the model was generated in Synthavision, the user could cut cross sections through it to reveal internal components as well as calculate mass properties such as weight, volume and center of gravity. The user could also define which views should be converted to drawings. That data was then returned to the AGS system as wireframe images with hidden lines removed or shown as dashed lines in order to produce typical engineering drawings. Changes to the model could not be made on the VAX system, however. The user had to make those changes using the AGS software and then regenerate the changed model on the VAX. In general, the intent was not to design interactively with solids but to use the technology to enhance analysis, visualization, and interference detection.
This software was first shown at the 1981 NCGA Conference in Baltimore, MD. According to The Anderson Report, “The demos Applicon ran at the NCGA Conference in Baltimore were real show stoppers.”[9] Applicon was the first turnkey CAD system vendor to offer solids modeling as a standard package. It was fairly expensive at $50,000 per copy and needed a VAX computer in addition to the PDP-11 running the AGS system. The company took the interesting step of trade marking the term “Solids Modeling.” As far as can be told, this latter action either never held up in court or the company did not attempt to enforce the trademark.
At the same time Applicon introduced its first solids modeling package, it also introduced a new PCB routing and placement package designed to run on VAX 11/750 and 11/780 computers. The primary result of moving this software to the VAX was to achieve improved performance over the PDP-11/34s currently being used to run the company’s software. Applicon claimed a 50 to 400 percent improvement in routing and placement speed. Interactive creation of schematics was still done on the PDP-11 using the company’s Video PCB System software. Net lists were then extracted from that database and transferred to the VAX via DECnet or on magnetic tape much like the way the solids package worked. The placement software provided the user with the choice between automatically placing components or doing it interactively. The routing software was priced at $40,000 while the placement software was $10,000.
In November 1981 Applicon announced a new PCB packaging and placement program that supplemented the software announced in June. A month later the company introduced a new package called Designer Logic which automated many tasks related to the creation of integrated circuit schematics and the extraction of data needed to run logic simulators.
Also in November 1981, Applicon introduced new technical documentation software. In reality, this software did not address the drawing tasks of professional illustrators as did similar software offered by Auto-trol Technology. What it did do was enable a user to merge text and graphics and then output page images to either an Autologic APS-5 Digital CRT Phototypesetter or a Xerox 9700 Electronic Printing System. These software interfaces sold for $17,500 each.
Applicon also had a moderate presence in the AEC sector of the CAD industry and offered software for applications such as process plant piping design. An internal Applicon document written in November 1982 by Kevin Cavenaugh in the company’s international marketing department described a competitive benchmark against Intergraph that the company participated in for a European chemical company. In addition to using Applicon’s Piping Design package to do traditional plant design, two application engineers spent a week building a solids model of the plant. This model showed that there were several critical flaws in the prospect’s proposed design including a pipe running through two large girders and a stairway running through another major pipe. Supposedly, the company was sufficiently impressed that it planned to purchase an Applicon system rather than Intergraph even though the latter was installed at another company site. We don’t know if this ever came to pass since the prospect was not identified in the memo. In general, Applicon never became a major factor in the AEC market space.
The VAX era begins
Applicon had been deeply committed to using Digital computers since shortly after it started developing CAD systems. When the VAX 11/780 was introduced, the company’s technical and marketing people certainly saw this as a logical extension of the AGS product line. At $250,000 per unit, the 11/780 was pricey for the company’s customers. When Digital announced the future availability of the lower cost VAX 11/750, that changed the equation and the company began to seriously work towards adding the machine to its suite of products. With the VAX introduction on the horizon, Applicon shied away from adding more powerful PDP-11 machines such as the PDP-11/70 to the company’s product line. At AUTOFACT in Detroit in November 1981, Applicon let the media know that implementation of a VAX-based system was running more than a year behind schedule. At the same trade show, the company showed a glimpse of its new raster workstation behind smoky glass panels.[10]
The company restructured its computer product line in April 1982 when it announced the 4000 Series. It started with the 4225 Graphics Processing Facility which consisted of a PDP 11/34 system, an 80MB disk drive, one monochromatic workstation, a 32-bit graphics display processor and basic application software priced just under $100,000. The 4245 added a 300MB disk and a magnetic tape unit with prices starting at $160,000. The top of the line 4275 was based on a VAX 11/751 computer which the company claimed would support up to 12 terminals compared to the four the PDP-11/34 supported. The VAX-based 4275 apparently ran most of the 16-bit PDP-11 code in emulation mode although some early 32-bit beta code may have been included with this product announcement.
According to CAD/CAM Alert, Applicon’s sales force did a particularly good job of keeping a lid on the introduction of the 4275 since premature marketing of this unit would have frozen sales of the company’s existing PDP-11 products.[11] (For anyone confused by the 11/751 nomenclature, this was the OEM version of the VAX 11/750. As far as I can tell there were no differences other than the model number.) Applicon’s statement that the VAX 11/751-based 4275 could support 12 terminals was overly optimistic and a reasonable configuration would eventually prove to be more like two to four unless the users were simply doing very basic drafting tasks.
The company also added SEED, a commercial database management package, to its product line as well as a user programming language. A communications protocol called DGN for Distributed Graphics Network supported communications between the VAX and PDP-11 computers. With a VAX computer in the product line, users of Applicon’s solids modeling software could now run it on the same computer although the need to translate data between Synthavision and the company’s CAD software still remained.
At the same time, Applicon introduced a new color raster workstation with 768 by 576 resolution and optional hardware anti-aliasing.[12] The latter technique smoothed out non-orthogonal lines and made them look less jagged. This was a major problem with early raster display terminals and one of the reasons that a number of vendors still offered storage tube terminals. The anti-aliasing option was called PERL for Perception Enhanced Resolution Logic. The color version of this terminal sold for $70,000 while the monochromatic unit was $40,000.
The state of Applicon in mid-1983
As Applicon prepared to introduce a new generation of mechanical design software, it is probably worthwhile to review where the company stood technically and business-wise in mid-1983. The company advertised the fact that it was in three market segments; electronic design of PCBs and integrated circuits, mechanical design and AEC. As mentioned earlier, it was not a major factor in the AEC space as compared to Intergraph, Auto-trol, Calma and Computervision and there is little evidence that the company was planning to put significant resources into developing new architecture and civil engineering software. Likewise, it was obvious that its interests were switching from electronics design where it had been a major factor for a number of years to the mechanical market which was perceived by many to be where the most significant future growth would occur.
The company’s business model was predicated upon building a significant portion of the systems it sold. VAX and PDP-11 computers were purchased from Digital and resold to customers although the company did not sell the larger VAX 11/780, only the mid-range 11/751. Terminals were a major source of revenue and were predominately manufactured in-house. By this time, virtually all the units being shipped were raster units, many of which were color and included the company’s proprietary 32-bit graphics processor. Other than software, this was probably the most profitable part of Applicon’s business. By 1983, it appears that the company was no longer producing the color ink jet plotter it had launched in 1977 and was reselling plotters from companies such as CalComp. Most of the company’s products were produced in a 170,000 square foot manufacturing plant in Billerica, Massachusetts.
The company sold its products through a direct sales force with more than 30 sales offices. Regional headquarters were located in Chicago, Philadelphia, Dallas and Santa Clara. European headquarters were in Paris, France along with sales offices in Germany and England. Other parts of the world such as Australia and Japan were handled by distributors. By this point in time, the company had an installed base of 1,500 systems supporting over 3,000 interactive workstations. Two workstations per system was a much lower ratio than what one found with most competitive systems. At this point in time, Applicon offered several hundred specialized application packages. Since the company used standard Digital computers, the entire library of third party software packages available for those machines were also available to Applicon’s users.
Key personnel included:
- Don Feddersen – President and CEO
- Russ Henke – Vice President –effectively second in command
- Dr. Jack Horgan – Director of planning and technology
- Dick Miller – Director of marketing
- Rex Smith – Director, Ohio Development Center
- James Kotanchik – Director of systems software
- Richard Tarulli – Vice president, U.S. sales
A new generation of software
In 1981, Applicon began development of what would eventually prove to be its most important software product, BRAVO!. At the time, it was expected to be an 18 month project – it ended up taking 42 months and $22 million in R&D funds when it was formally announced on June 28,1983. The software was written in PL/1 for Digital’s VAX product line, including the 11/730, 11/751 and 11/780. This was new software, not simply the PDP-11 version of the company’s CAD/CAM software converted to run on the VAX. At the same time, Applicon offered its CAD/CAM software unbundled for customers who purchased VAX 11/780 computers directly from Digital. The launch of BRAVO! did much to re-energized the company which in 1983 was loosing market share at an alarming rate. Unfortunately, the software was released a number of months before it was ready for prime time and early users struggled with some of its functionality.
BRAVO! included a new database manager, a new user interface with on-screen menus, an integrated interactive solids modeler (Solids Modeling II) and mechanical engineering tools. The interactive two-dimensional and three-dimensional design and drafting module retained the Applicon Editor nomenclature as well as the Tablet Symbol Recognition capability of earlier software. Finite element modeling and analysis was available as an option. The solids modeler supposedly responded to most input commands in five seconds or less, but was able to do so only by using limited colors. When the user wanted to see a realistic rendering of the model, that could be done but it took more time. BRAVO! also included a new user programming toolkit called the AGL (Applicon Graphics Language) Programming Package.
Applicon’s initial solids modeling package described earlier generated solid models in a batch mode on a VAX computer using wireframe models created on the AGS’ PDP-11/34 computer. This was good for visualizing models and calculating mass properties but was not an interactive design tool. Solids Modeling II, on the other hand, was a true interactive solids modeling program. Users were able to build models of individual parts and assemblies using geometric primitives such as spheres, cubes, cones and even objects incorporating free-form surfaces and surfaces of revolution. Once a model was completed, wireframe images with hidden lines removed could be extracted from the model and used to produce engineering drawings. Changes made to those drawings could not be used to change the solid model – it was a one way path.
While most users probably had a difficult time adapting to the concept of solid modeling, Applicon’s Surface Modeling Package was more immediately useful to the typical BRAVO! customer. This surface modeling software was more tightly integrated with traditional wireframe design than was the solids package. Users could create surfaces ranging from simple spheres, cones and cylinders to surfaces of revolution and warped B-spline surfaces. Models built with these surfaces could be used by other applications such as finite element modeling and NC part programming. This process was not as fully automatic as the sales literature would have one believe and there continued to be a substantial amount of data re-entry.
Model data could also be used by the Applicon Editor to produce drawings. Productivity improvements when drafting cross sections were said to be particularly impressive. Prior to the eventual merger with MDSI, Applicon was never a major factor in the high-end NC market space. Dick Miller remembers a major effort to develop a five-axis machining capability for a Martin-Marietta customer site only to find out that this facility had no five-axis machine tools and that the requirement was for a “future possibility.”
The Database Manager was designed to handle all graphic and attribute information with individual applications accessing whatever data was needed. The intent was to eliminate all translation of either graphics or attribute data between applications. With Solids Modeling II and the new Surface Modeling Package, Applicon had one of the industry’s first hybrid modeling capabilities where users could work in a combination of wireframe, solids and surface geometry. The company also announced pre and postprocessors for IGES, the Initial Graphics Exchange Standard, which was quickly becoming a system prerequisite for most large user organizations.
This new software was offered only on the VAX platform meaning that existing customers had to replace their PDP-11 systems if they wanted to use BRAVO!. Applicon sold complete turnkey VAX 11/730 and 11/751 systems with prices starting under $120,000 for a single workstation 11/730 system. This did not include either the Solids Modeling II or Surface Modeling packages. If a customer wanted to use a VAX 11/780, that system had to be purchased directly from Digital and the software and workstations from Applicon. This semi-unbundled model did not include the ability to use nonApplicon terminals to utilize the Applicon software. Prices for many packages varied based upon the size of the VAX computer being used. As an example, the AGL Programming Package cost $10,000 for the 11/730, $20,000 for the 11/751 and $30,000 for the 11/780. This 1-2-3 pricing ratio was also used for other BRAVO! modules.
In addition to Solids Modeling II and Surface Modeling, the company introduced three additional mechanical engineering packages; GRAFEM (Graphic Finite Element Modeling), IFAD (Integrated Finite Element Analysis and Design) and Mechanisms. GRAFEM was a finite element analysis pre and post-processor that facilitated creating viewing and editing finite element models and viewing analysis results. IFAD used the models created by GRAFEM for linear static and dynamic analysis. Both of these were developed internally by Applicon. The Mechanisms package calculated static equilibrium and time response data for two and three-dimensional rigid body mechanical systems. It used software licensed from Mechanical Dynamics Incorporated (MDI). While IFAD provided a basic analysis capability some users apparently wanted more comprehensive finite element analysis software. To meet this need, Applicon signed a marketing agreement with MacNeal-Schwendler Corporation to license that company’s MSC/NASTRAN software for use on BRAVO! VAX-based systems. GRAFEM could still be used for pre and post-processing in this latter situation.
These were not inexpensive packages. For the VAX 11/780 Solids Modeling was $75,000, Surface Modeling was $30,000, GRAFEM was $52,500, IFAD was $37,500 and Mechanisms was $30,000. In addition the Editor software cost $7,500 per workstation. The result was that a six color workstation VAX 11/780 system equipped with the full spectrum of design and analysis software could easily cost close to $1 million.
The reality was that most early Bravo! customers used the software for twodimensional drafting rather than building solid models. According to the November 1984 issue of Computer Aided Design Report, Bravo! 1.0 had two major problems associated with it – it was slow and files sizes were excessively large. Fisher Controls, one of the early Bravo! installations stated that for some drafting tasks it was 20 to 30 times slower than earlier versions of Applicon’s software. Another customer stated that drawing files were between six and 18 times the size identical drawings were on older systems. In late September 1984, Applicon began delivering Bravo! Version 1.5 which corrected many of the performance issues with two-dimensional drawings but did not address file size problems or solids modeling performance. Computer Aided Design Report recommended that customers considering installing Bravo! should definitely purchase the floating point option for the VAX 11/750, should buy an 800 MB disk drive as well the maximum amount of main memory and should install Applicon’s new display list memory option in all terminals.[13] Two years later, performance issues, especially in regards to solids modeling, would still be haunting Bravo!.
Some users, however, were making progress with solids modeling, although not necessarily with Bravo!. The Endevco division of Becton Dickerson, a manufacturer of instruments for measuring vibration in aircraft engines and turbines started using Applicon’s Solids Modeling software in early 1983. The company found that it could design transducer packaging in a third the time prior techniques took and that outside suppliers could produce more accurate prototypes faster.[14] It would be another decade before this attitude would become widespread within the mechanical design community.
As part of this round of product introductions Applicon also launched two low cost graphics terminals. The 4620 Desktop Color Raster Workstation included a keyboard and tablet combined into a single unit as shown in Figure 7.4 and a 13-inch monitor eight-color monitor with 672 by 504 resolution. The 4620 used an Intel 80186 microprocessor and included 256KB of program memory expandable to 756KB. An optional floppy disk drive was also available. This unit sold for just $17,500 which made it probably the lowest cost color raster terminal offered at the time by a major turnkey CAD/CAM system vendor. It was intended to be used by casual users rather than full time CAD operators. When this terminal was introduced in mid-1983, Applicon’s announced plan was to upgrade it to support the CP/M-86 operating system in 1984 so that it could support application programs independent of the host processor.
A second workstation, the 4630 Modular Color Raster Workstation, was introduced at the same time. This unit also had a 13-inch monitor but with the same 768 by 576 resolution provided with the company’s higher-end terminals. It was priced at $33,000 and was intended to be used by full-time operators as well as casual users.
Applicon also introduced a new 4265 Graphics Processing Facility utilizing an upgraded VAX 11/730 computer with 2MB of main memory, a dual density (800/1600) magnetic tape drive and a 160MB disk drive. Without any terminals this unit was priced at $85,000, a substantial reduction from the price of the earlier VAX 11/730 systems offered by the company. The VAX 11/751-based 4275 Graphics Processing Facility was also repackaged with more memory and a lower price. VAX 11/780 customers needed to purchase two additional software modules in order to use BRAVO!, a Workstation Interface Module for $15,000 and a Peripheral Support Option for $5,000. The company claimed that an 11/780 system would support eight to ten workstations.
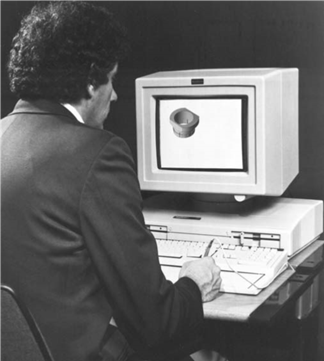
There was one aspect of BRAVO! that would eventually prove to be Applicon’s Achilles’ heel. Early in its development, the decision was made by the company’s software personnel to write BRAVO! in a new programming language called PL/1 that was being touted by many, including IBM, as being the programming language of the future. While a PL/1 compiler was readily available for VAX computers running the VMS operating system, similar compilers were not available for most other computer systems. As a consequence, this inhibited Applicon from porting BRAVO! to other platforms later in the 1980s and throughout the 1990s.
Mid-1980s – tumultuous time for Applicon
BRAVO! started off on a fairly positive note, at least publicity-wise. The company began shipments in July 1983 and later that year Fortune magazine named it a “Product of the Year.”[15] The February 1984 issue of CAD/CAM Alert had an article discussing the successful implementation of BRAVO! by two long-time Applicon customers, Fisher Controls International in Marshalltown, Iowa and Gardner-Denver Compressors Division in Quincy, Illinois. Both were using the Solids Modeling II package, but not necessarily as their primary design tool. Moving data from legacy PDP11/34 system required a translation process. Users with large databases of older design data such as Fisher Controls translated the data on an as-needed basis rather than trying to do it all at once. That company found that translation of geometric data went well while there were problems with the translation of textual attribute data. Apparently this article was written before Fischer Controls began experiencing the performance problems discussed in the Computer Aided Design Report article mentioned earlier.
Jim Sutton, the CAD/CAM project manager at Gardner-Denver wished that Applicon would “associate wireframe geometry with solids modeling in the database … to be able to make changes on the solid and have the wireframe be automatically updated.” Apparently the concept of an integrated database was not as far along as Applicon inferred during the product’s launch.[16] In early 1984, Applicon began shipping its new 4620 workstation with the CP/M-86 operating system. This enabled the unit to function as a PC when it was not doing CAD tasks. It does not appear that a user could be doing both types of tasks at the same time.
Don Feddersen was appointed general manager of Schlumberger’s ComputerAided Systems Group in early 1984. In this role, he took a plan to Schlumberger management to more closely integrate MDSI and Applicon but was told that the corporate position was to break up organizations, not combine them. Shortly thereafter, Feddersen left to become a general partner at Charles River Ventures, a venture capital firm. Since 1997 he has been a private investor in high technology firms and has been a director of a number of such firms as well as a partner at Bessemer Venture Partners beginning in 2001. He has also been a long time director of Parametric Technology.
Feddersen’s resignation was the first of a number of management changes that would take place at the company as Schlumberger tried to determine the best model for its CAD/CAM businesses. Feddersen was initially replaced by Michael Pinot and eventually, as president of Applicon, by Alex Beavers, the former general manager of General Electric’s Intelligent Vision Systems Division. The hiring of Beavers was probably one of the reasons that led to Russ Henke leaving in October to become president of Gould’s Imaging and Graphics Division.
Beavers reported to Jimmy G. Lee, an executive vice president at Schlumberger who was responsible for the company’s Computer-Aided Systems Group. Other management changes included Edward Oakley joining the company from HewlettPackard as vice president of sales and a few months later and Jeffrey Simon joining as vice president of marketing. Dick Miller left the company in the summer of 1984. Miller, Jack Horgan and Jerry Sabath formed Aries Technology along with two others who had left Applicon earlier, Art McCray and Jerry Christopher. Aries was funded in part by Fontaine Richardson who was with Eastech and Art Reidel, a former vice president of engineering at Applicon who was with Alex-Brown and Company.
In the fall of 1984 Applicon began laying the groundwork for a workstation-based product. At the time, Apollo and Sun Microsystems were making inroads in the CAD/CAM industry through companies such as Auto-trol Technology, Calma, Mentor Graphics and Computervision. The first such product the company introduced was the Aria, a stand-alone color workstation that incorporated a Digital VAX 11/730 minicomputer. It appears to have been very similar to the previously introduced 4265 Graphics Processing Facility with a 3MB main memory and a 13-inch 4620 Desktop Color Raster Workstation. See Figure 7.5.
Including database management, two-dimensional and three-dimensional design and drafting software, the Aria was introduced at $65,000 through the end of 1984. The initial price was expected to increase to $85,000 on January 1, 1985. After its initial introduction, several 19-inch color raster display terminals were added to the Aria product line. This was followed up at NCGA in April 1985 by the Aria II which replaced the VAX 11/730 with a MicroVAX II and support for a variety of Applicon terminals. The base price of the Aria II was $85,000 with shipments expected to start mid-summer. With a high resolution 19-inch display, an Aria II sold for as much as $125,000. At the same time, Applicon announced support for the new Digital 8600 “super VAX”, VAX clusters and an interface to IBM mainframes.
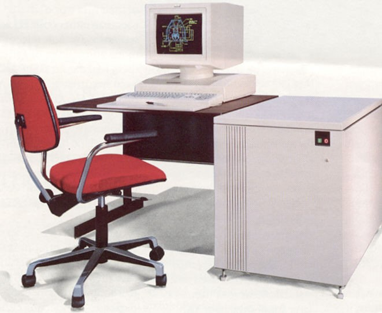
The February 2, 1985 issue of the Boston Globe contained an extensive article on Schlumberger and its Applicon subsidiary that described in depth how the company’s CAD/CAM market share had slipped precipitously since the Schlumberger acquisition. Lee was upbeat about the future claiming that it would take five years for Schlumberger to turn the business around and that they were only three years into the process. Lee had been with Schlumberger for 25 years and was a cigar chomping representative of the company’s oil field roots.
Stanley Klein, who was then publisher of the S. Klein Computer Graphics Newsletter, was quoted as saying “What seems to be lacking at Applicon is entrepreneurial motivation. The question is whether a company with an abundance of resources can succeed in an extraordinarily fast-changing marketplace where the ground rules shift every six months.”[17] Although the company was increasingly focused on the mechanical market, in March 1985 it established a new electronic design unit and hired Kenneth Jenkins to head it up.
The major issue for Schlumberger was how to structure Applicon and MDSI as complementary parts of the same business enterprise. In April 1985, MDSI announced that its Equinox NC software would be available on BRAVO! systems. MDSI also moved into the workstation market with a product called the Expert Station targeted at sheet metal design and fabrication. The company was also still balancing its mechanical and electronic software product lines. New Bravo! VLSI and PCB software that focused on graphical layout was introduced in mid-1985. This was at a time when the competition was making progress with systems that took a more logic-centric approach.
By July 1985 Applicon had shipped 100 BRAVO! systems but the company’s market share was continuing to slip. While it had once been second only to Computervision, the company was now seventh in the industry with annual revenues of about $148 million.[18] Then Schlumberger decided it was time to reshuffle the deck once again. Applicon and MDSI were merged into a single company with Applicon becoming the name of the combined entity. By this point in time, the company was increasingly focused on the mechanical market and secondarily on electronic design. AEC applications were no longer a significant factor.
The company’s headquarters were moved to Ann Arbor, Michigan, the home of MDSI, and Dick Mohrman who had been the general manager of MDSI became the vice president and general manager of the combined Applicon. Alex Beavers, the previous president of Applicon stayed with Schlumberger, but as vice president of marketing for the parent company’s Computer-Aided Systems Group. During 1985 employment at Applicon dropped from 1,300 to about 600 in October.[19] Then in November, Rex Smith, who had joined Applicon in 1983, left to become president and CEO at CADSI, a vendor of mechanical analysis software.
Applicon product line in early-1985
This section describes the Applicon product line prior to the merger with MDSI. By early 1985, Applicon had stopped selling Digital PDP-11/34-based systems and was focused entirely on the VAX computer product line and BRAVO!. The VAX 11/730based 4265 Graphics Processing Facility described earlier was now known as the 4130 BRAVO! Processing Facility. The company suggested that it could support four workstations which it probably could if they were simply doing drafting or wireframe design. If the systems was being used to support solids modeling, two workstations was a more realistic configuration.
In a similar manner the VAX 11/751-based 4265 Graphics processing facility was now known as the 4150 BRAVO! Processing Facility. The unit was being sold both as a BRAVO! platform and to provide VAX support for installed PDP-11/34 systems. The company claimed it would support eight workstations but four to six was probably a more practical limit. When Applicon introduced VAX-based systems, it only offered 11/730 and 11/751 computers as turnkey system components. Customers who wanted the larger 11/780 needed to purchase that computer directly from Digital. By early 1985, the company’s sales strategy had changed and it now offered both 11/780 and 11/785 computers as the 4180 and 4185 BRAVO! Processing Facility.
The prices of color raster workstations (these were really terminals, not free standing or networked workstations) were starting to come down precipitously. In early 1985, the company was offering a variety of desktop and console units with either 13inch or 19-inch color raster monitors. While monochromatic units may have been available, Applicon clearly was pushing color displays. The lower cost units had a resolution of 672 by 504 while the more expensive units were 768 by 576. As described earlier, the company offered an optional display processor called PERL that smoothed out jagged lines. It was good technology, but it did slow down the time required to generate a display. Most of the company’s competitors were moving to higher resolution displays, specifically 1024 by 780 resolution units, to minimize the jagged line problems. In addition, the Applicon workstations did not support dynamic dragging of elements and the range of colors these units displayed was quite limited. The basic units were capable of just seven colors, preset by the factory. A 256 color option was available and necessary if the user wanted to visualize solid models.
One other problem with these terminals was that the link to the VAX was just 1.56 megabits per second. Generating new images was somewhat time consuming. Also, little was being heard from Applicon concerning the CP/M-86 operating system that was supposed to be available with the 4620 Desk Top Workstation. It did, however, emulate the Tektronix 4113 terminal, enabling the unit to support MDSI’s NC graphics software on the VAX. The company was continuing to support the stand-alone ARIA but it did not seem to be a major element in Applicon’s product line.
In early 1985, BRAVO! was still a work in progress. Early releases of the software had performance problems and data files were excessively large when compared to what was required with competitive systems. While performance improved with subsequent releases, the file size issue was intrinsic in the software. Both the performance and size issues can probably be traced to the fact that Applicon was using its Database Management package to store both graphics and attribute information. This software was based upon the SEED package described earlier but rewritten by Applicon in PL/1. It took some time to work out the bugs.
The Editor was the key user module. It was derived from the company’s earlier Image package and retained that software’s tablet recognition capability except that it now also supported on-screen menus. The on-screen menus were supplemented by a function keyboard with 64 buttons. Editor could display eight views of a design model and had geometric associativity as well as dimensional associativity. When an individual part was updated, all the assemblies that used that part were updated. Solids Modeler II used the same user interface as Editor. It was a CSG (Constructive Solids Geometry) modeler with eleven solid primitives.
Interactive images were generated using a faceted representation with the degree of faceting controlled by the user. The finer faceting used, the slower the responsiveness of the software. To perform hidden line removal, produce detailed shaded images or generate a boundary representation for drafting still required a conversion to Synthavision. The Synthavision boundary representation of the model could not be converted back to a CSG model.
Finite element and mechanism analysis has been described earlier. One application area where Applicon was having problems was with numerical control software. The solution was to implement MDSI’ Compact-II NC part programming package on the VAX and interface it to BRAVO!. A package that would work directly with the BRAVO! database was slow in coming. This software did not have many of the capabilities competitors offered such as color-coded feed rates, dynamic tool motion or anti-gouging algorithms. Other applications available at this time included flat pattern generation, nesting and flame cutting, and technical documentation. The company had ported its PCB and integrated circuit design software to the VAX but it is not clear to what extent this was still original16-bit PDP-11/34 code versus rewritten 32-bit VAX code. The same comments apply to the company’s architectural drafting and piping design software.
While prices were coming down, these were still expensive systems. A 4150 VAX 11/751 cost around $150,000. The workstations ranged in price from $17,500 to $42,500. In addition the Editor software cost $9,500 per workstation. In a departure from its previous software pricing strategy, Applicon no longer varied the cost based upon the size of the computer being used. Instead, it charged a flat amount per CPU and an additional amount per workstation. As an example, Solids Modeling II had a base cost of $20,000 plus $5,000 per workstation using the software. While this was probably competitive with other system running on VAX 11/780 or 11/785 computers, it was fairly expensive for smaller 11/730 and 11/750 configurations.
Applicon becomes Schlumberger CAD/CAM Division
At the May1986 NCGA Conference in Anaheim, California, Applicon announced a new release of its software product line, Bravo3 (apparently this was the new nomenclature for Version 3.0 of Bravo). At the same time it launched a series of new software packages for printed circuit board and integrated circuit design. When Schlumberger combined Applicon and MDSI into a single organization in July 1985, it had split the electronic portion of Applicon’s product line off and assigned that business activity to another corporate organization, Factron, a manufacturer of electronic test equipment. That combination probably made sense to executives who were several levels removed from the technology and business issues of this industry but it was not an effective relationship. By early 1986 it was back as part of Applicon but the portion of the company’s revenue represented by electronic design applications had slipped to around 10 percent.
The new Bravo3 electronic design software included schematic capture, design analysis, and the physical design of PCBs and integrated circuits. The PCB routing software was developed by Algorex, a PCB design and manufacturing company. This new software was introduced as being available on Sun Microsystems’ workstations as well as on the VAX systems Applicon had traditionally supported.[20] A typical four seat VAX system sold for $600,000 including the routing software. [21] The company’s objective, and one that it continued to pursue for a number of years, was to offer an integrated suite of electrical and mechanical design software. As an example, the combination of electrical and mechanical software could be used to design individual circuit boards, the product that these circuit boards were to be used in and then do a thermal analysis of the mechanical and electrical components. While this combination was attractive to companies designing electro-mechanical products, companies designing complex electronic systems, especially large-scale integrated circuits, were moving to more specialized software products offered by companies such as Mentor Graphics, Cadence and Daisy. One exception was Fairchild Semiconductor which was also a Schlumberger company.
Bravo3 was the nomenclature Applicon applied to the integrated database that supported the company’s suite of design, analysis and manufacturing applications. By this point, Applicon had integrated the MDSI Equinox manufacturing software to work with Bravo3. All of these packages were available on the VAX VMS platform but only some, mostly electronic design-related, were also available running under UNIX on the Sun platform. The hardware portion of the product line consisted of two groups of products, the 4600 series which used Digital computers and the 4700 series which were Sun workstations with Applicon enhanced graphics. A color Sun-based unit, the 4735, sold for $59,900. One terminal being offered for VAX systems was the 4670 which had 1536 by 1157 resolution and supported 1,793 colors. This unit incorporated an Applicon built graphics processor capable of displaying 100,000 random three-dimensional vectors per second. An optional shaded image generator rendered up to 25,000 polygons per second. The basic unit sold for $59,000 while the shaded image option was an additional $9,000.
A few months later, at AUTOFACT ’86, Applicon introduced Bravo3 3-D Mechanisms dynamic analysis software. This package tightly integrated Mechanical Dynamic’s ADAMS (Automatic Dynamic Analysis of Mechanical Systems) and Bravo3 with a consistent user interface. A 2-D Mechanisms package incorporating MDI’s DRAM (Dynamic Response of Articulated Machinery) software was also available from Applicon. Revenue at Applicon was up 18 per cent in 1986 from the prior year and Mohrman claimed the company made a profit for the year, its first in five years.[22] While it was striving to regain its former sales momentum, management of Applicon was still in turmoil. Apparently 1986’s financial results did not satisfy Schlumberger’s management. In February 1987 Mohrman was replaced as vice president and general manager of Applicon by another Schlumberger executive, Bruce McCann, who had been with the company’s North American Wireline operation. Like General Electric and its management of Calma, Schlumberger seemed to believe that general management experience was more important than specific knowledge of the CAD/CAM industry and its technology.
In what would eventually be seen as a significant move, Applicon decided to unbundle its software and price it separately from the hardware it also sold. This enabled customers to purchase standard computer systems and workstations from Digital and Sun and then purchase the software from Applicon. The problem with this approach was that Digital ’s workstations were loosing the price/performance race compared to other workstation vendors and only a limited amount of Applicon’s software ran on anything other than VMS systems.
At this point in time, the company was having a hard time getting the Bravo3 VLSI software off the ground and sales of that product was suspended in April 1987.
According to Jerry Robertson, vice president of sales and marketing, “We are going to bite the bullet and hold off marketing Bravo3 VLSI until we are able to provide an efficient migration path for our existing users of IMAGE 860 systems.”[23]
In March 1987 Applicon announced that it would market Sun-based UNIX systems starting at $12,900 for a system with a 19-inch monochromatic display and either drafting or three-dimensional design software. This was apparently a diskless node that required either a server or larger workstation in the network in order to function. The Sun version of the software was not pushed very aggressively and before 1987 was over Applicon was once again supporting just Digital hardware. At the same time it announced the Sun-based product, Applicon introduced the GW4790 workstation that incorporated a Digital MicroVAX II computer. It was priced from $45,000 with just basic operating system software to $95,000 with solids-based design and drafting software.
Schlumberger continued to periodically reorganize its computer-related business units. Around August 1987, the group referred to as Computer Aided Systems was eliminated and a new organization called Schlumberger Technologies was established consisting of Applicon, ATE (semiconductor test equipment) and Benson (plotters). Then in November, the Applicon name was dropped and it became simply Schlumberger CAD/CAM.
For the next year or so, there were few significant product or business announcements from the company. Finally, in September 1988 Schlumberger announced a number of new manufacturing-related software packages including BravoNC which was billed as “the first major technological advance in NC programming since APT.”[24] What was significant was that this software could take a part that was made up of a number of independent surfaces and generate tool paths that smoothly machined across the intersections of these surfaces. The package sold for $19,800. Proceeding along this manufacturing path the company also introduced a new coordinate measuring machine programming package as well as a new sheet metal design and fabrication package. Schlumberger tried to get the message out that manufacturing was a core focus of the company by establishing a special interest group for users of its COMPACT II and BravoNC software. The group’s first meeting was held in October in Dallas.
Schlumberger launches MacBRAVO!
In the late 1988 time frame it was not a foregone conclusion that the IBMcompatible personal computer running a Microsoft operating system would dominate the PC market. Apple had some very good products at the time and controlled a substantial share of the market, mostly due to its introduction in 1984 of the Apple Macintosh. The Macintosh is widely credited with being the first successful computer product that incorporated a graphical user interface, albeit one that the company appropriated from Xerox’s Palo Alto Research Park.
While PC manufacturers were committed to using Intel microprocessors, Apple decided to use the far more powerful Motorola 68000 series chips in its products. In March 1987 Apple introduced the Macintosh II with a 16-MHz 68020 processor – the same processor being used by Apollo, Sun Microsystems and other manufacturers for high-end engineering workstations. With 1MB of main memory and a 40MB hard disk, the early Macintosh II sold for $5,500. The monitor was extra. Performance-wise it didn’t quite compete with the more expensive workstations, but it was clearly superior to most PCs.
Schlumberger used the availability of the Macintosh II as an opportunity to launch a new software product line called MacBRAVO! Launched with much fanfare at AUTOFACT on October 31, 1988, the initial release consisted of two modules, MacBRAVO! MODELER and MacBRAVO! DETAILER. At the time, both Schlumberger and Apple felt that this was a significant announcement, sufficiently significant that both Euan Baid, Schlumberger’s CEO and John Scully, Apple’s CEO both showed up for the press conference where MacBRAVO! was introduced.
The two MacBRAVO! Software modules along with an IGES translator had a combined price of $3,295. It required a Macintosh II with 4 MB of memory so that the combined hardware and software price probably totaled around $11,000, substantially less than what the BRAVO3 system cost including a Digital VAXstation. Schlumberger presented MacBRAVO! as coming from the same code base as its BRAVO3 product line, but the overall functionality was a subset of BRAVO3. Data could be directly exchanged with VAX-based BRAVO3 systems but not with BRAVO3 running on Sun workstations. Also, there was no mention of any of the MDSI manufacturing software being converted to run on the Macintosh II nor of an interface to that software running on other platforms.
MacBRAVO! incorporated the pull-down menus and icons that were integral to the MAC Operating System. Consistent with BRAVO3, the Macintosh software also supported the company’s unique Tablet Symbol Recognition capability although with a Macintosh mouse it was far more clumsy to use than on a workstation equipped with a tablet and stylus. The software supported up to eight windows, one of which could be active at a time. MODELER supported warped, swept and ruled surfaces, offset surfaces and surface intersections. In addition to direct translation between MacBRAVO! and BRAVO3 and an IGES 4.0 translator, Schlumberger also offered a AutoCAD DXF translator.
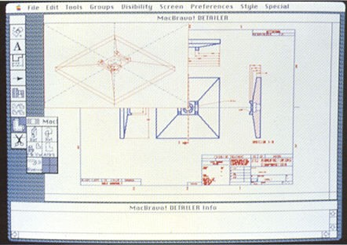
The primary competition for MacBRAVO! was AutoCAD. From a threedimensional design perspective, AutoCAD did not compare to the modeling and surface geometry capabilities Schlumberger was providing. From a pure two-dimensional drafting point of view the two packages were comparable in creating geometric data but, based upon tests performed by Schlumberger, MacBRAVO! was nearly three times faster creating dimensions and other annotation. In addition, users could extract detailed part lists from MacBRAVO!’s three-dimensional models and the Macintosh version of the software could be used as a low-cost system to detail BRAVO3 designs.
Apple continued to market the Macintosh II through late 1993. The final model was the Macintosh IIvx which used a 32-MHz Motorola 68030 processor. Schlumberger, however, ceased promoting MacBRAVO! sometime earlier.
Schlumberger CAD/CAM tries to find its niche
For the most part, large corporations have almost always found it difficult to develop a meaningful CAD/CAM vendor business model. Schlumberger was no exception. The problem is that this was a very rapidly changing industry, especially in the late 1980s and early 1990s, that required managers to have a strong feel for what customers wanted if they were to be successful. Decisions had to be made quickly and there was little margin for error. Large bureaucratic organizations were not amenable to this type of rapid change.
Whether or not they were profitable activities, Schlumberger Technologies apparently realized in early 1989 that it had too many irons in the fire. Having earlier merged Applicon and MDSI into a single organization, the company decided that being in the plotter hardware business did not fit its long term objectives and it decided in March to sell its Graphics Division subsidiary. Originally known as Benson, this operation manufactured and sold electrostatic and pen plotters. In June it was sold to Océ, based in Venlo, The Netherlands. Basically, Schlumberger was getting out of the hardware manufacturing business. In early 1988 it had sold its graphics manufacturing operation in Billerica to a management group headed by Francis Donlan who had been the company’s CAD/CAM manufacturing manager. Renamed Manufacturing Solutions, Inc., it continued to produce high-end graphics workstations that were sold by Schlumberger CAD/CAM.
In 1987, Applicon had introduced facility layout package, Bravo3 Facilities, targeted at large manufacturing plants. This was the first AEC package developed for the Bravo3 product line. It incorporated a variety of features that facilitated the design process including double line walls with automatic cleanup when doors or windows were added, three-dimensional machinery models, and the calculation of the length of electrical wiring. If the model of a piece of manufacturing equipment was changed, all instances of where the unit was used also updated. According to The Anderson Report, Applicon had committed to the development of this software for General Motors several years earlier in exchange for a 100 seat order. In June 1989, Schlumberger announced that it would deliver a Macintosh version of the software by the end of the year. MacBRAVO FACILITIES apparently had similar capabilities to the earlier VAX version of the software but the basic version sold for just $4,900. Including Macintosh hardware, a typical seat cost from $16,000 to $28,000, substantially less than minicomputer or engineering workstation systems from Intergraph or Auto-trol Technology but far more than AutoCAD running on a PC.[25] One of the company’s more interesting marketing moves occurred in the spring of 1989 when Schlumberger CAD/CAM announced that for a limited time it would give buyers of Bravo a “free” DECstation 3100.
A more significant product introductions in this time frame was a software package called BravoMOST (Mechanism Optimal Synthesis Tool). This program could be used to assist in the design of two- and three-dimension mechanical linkages. The designer would create the basic design of such a linkage, indicate the points in space that a particular element of the linkage was to pass through, define which elements of the linkage assemble could be modified by the software and then have the program determine the optimum linkage design. BravoMOST eliminated the need for time-consuming iterative design procedures and physical prototypes. Schlumberger also introduced BravoDRAW, a low-cost mechanical drafting package, and BravoMODEL, a threedimensional wireframe subset of Bravo3.
In mid-1990 Schlumberger CAD/CAM’s relationship with Digital continued to be particularly strong. Other than the Apple Macintosh, Digital was the only platform being supported. Schlumberger was the largest single value-added reseller of Digital hardware. The previous December, the two companies had even agreed to have Digital distribute Bravo3 to its customers. One reason for the strong CAD/CAM relationship was the fact that Schlumberger was a major user of Digital computers for its oil and gas services business. The Anderson Report felt that this relationship had both positive and negative results. On the one hand, since Bravo3 was not available on competitive computer systems, the Digital sales people did not have to be concerned that potential customers might select a non-Digital platform on which to run the software. On the other hand, Digital was not winning many new customers and that limited Schlumberger to selling into Digital’s installed base.[26] At this point, Schlumberger took another step in getting out of the hardware business by selling Digital its hardware test and repair business and turning over the maintenance of existing installed hardware to Digital.[27]
Schlumberger’s European base was beginning to have a positive impact on its CAD/CAM business unit. In 1990, European business increased 25 percent from the prior year and the subsidiary opened six additional sales offices in East Germany, Turkey, Spain, Holland, France and Benelux. Schlumberger CAD/CAM Europe under Hans-Kurt Luebberstedt, vice president of sales and service, had expanded to 300 people handling sales and support.[28]
Overall, the company’s revenue had changed little during the prior six years. From $141 million in 1985 it had peaked at $155 million the following year before dropping to $135 million in 1987. The following three years saw revenue in the $140 to $143 million range. What did change was the hardware/software mix. In 1985 it was 24 percent software and 76 percent hardware. By 1990 this had changed to 55 percent software and just 45 percent hardware. In 1990 mechanical software was 60 percent CAD and 26 percent CAM. Typical software prices per seat in mid-1991 were $15,000 for the basic Editor/Database Manager, $11,000 for Solids Modeler, $9,700 for Surface Modeler, $3,500 for BravoDraft and $15,000 for BravoNC.
The company offered three different sets of products. Bravo3 Version 3 was the full function suite of design, analysis and manufacturing software available on the VAXstation 200 and 3200 and the MicroVAX 3500 and 3600. These machines were available running both Digital’s legacy VMS operating system and that company’s implementation of UNIX called ULTRIX. Schlumberger supported just VMS, however. The core package was Bravo3 Editor which supported both wireframe and solids modeling with shape libraries and feature-based modeling. A surface geometry module that supported NURBS surfaces was also available as were numerous analysis and manufacturing options.
DesktopBravo! was Schlumberger’s initial package that supported ULTRIX. The DECstation systems were Digital’s attempt to provide customers with a UNIX alternative to its VAX products. These machines utilized MIPS processors and ran UNIX but not VMS. Only two ULTRIX packages were initially available from Schlumberger, Detailer and Modeler. While the company promised more software options in the future, they were slow in coming. One problem probably was the lack of a PL/1 compiler for the DECstation which meant that Bravo3 software had to be rewritten, not just recompiled.
The third product line was the Macintosh software described earlier. It was not selling as well as Schlumberger had expected. During the first year it was on the market, only 1,300 seats had been sold. Meanwhile, Autodesk had sold over 300,000 copies of AutoCAD. In addition, the company signed an agreement with Parametric Technology to resell Pro/ENGINEER further confusing the product line in the minds of prospects.
The Morley era begins
In June 1991 Schlumberger switched management directions once again and for the first time brought in an experienced CAD industry veteran to head the CAD/CAM division. Bradford C. Morley had been a senior vice president at SDRC and in charge of its software business when he was recruited by Schlumberger Technologies to reenergize the company’s efforts in the CAD/CAM area. He reported to Clermont Matton, the head of Schlumberger Technologies. Prior to taking over Schlumberger’s CAD/CAM business, Morley had spent seven months at the company’s headquarters in New York as vice president of marketing and business development for Schlumberger Technologies. Upon taking over the helm at Schlumberger CAD/CAM, Morley implemented a five-year plan to re-establish the company’s momentum and to make it a major factor in the industry.
The plan, known as “Cresendo” internally, had seven key elements: multiple computer platforms, modular software, a common geometry engine, ease of use, simulation (analysis) technology, manufacturing software and data management. Gone from the company’s business model was reselling hardware, electronic and AEC applications, and the reselling of other companies’ software such as PTC’s Pro/ENGINEER. The company also was not interested in selling stripped-down entrylevel systems. Two other aspects of Morley’s plan to turn the company around were to reestablish a brand identity and to eventually take the company public once again. After looking at alternatives such as sticking with the Schlumberger name or resurrecting the MDSI label, they concluded that the Applicon name still resonated with the company’s users. So, on September 16, 1992, Schlumberger CAD/CAM once again became Applicon.
On the financial side, the plan was to go public in 1995 with Schlumberger continuing to hold 49 percent of the company’s stock with the balance being sold to employees and the public. The company had revenues in 1992 of $104 million and at this point was a 600-person firm. Overall, the plan made a lot of sense but like all other such plans, the proof would be in the execution.[29] In addition to Morley, key managers included Warren Liu (marketing), Dan Presidio (engineering), Mike Anderson (North American operations), Hans-Kurt Luebberstedt (European operations), and Robin Kerr (Asia/Pacific operations). Within the marketing operation, Jim Fall was responsible for modeling software while Rod Nehring handled data management products and Brian Barton CAD/CAM applications. Software revenues had increased 21 percent in 1991 and the company planned to increase its research and engineering budget by 40 percent in 1992.[30]
The fact that Schlumberger CAD/CAM had over 4,500 customers including 300 new ones in 1991 but only 90 users showed up for the company’s user group meeting in San Diego in April 1992 should have been an indication that something was fundamentally wrong with the company’s marketing and support strategy.[31] The company had three major tasks on its hand at this point in time: 1) keep Bravo technologically competitive with up-and-comers such as PTC’s Pro/ENGINEER, 2) maintain the revenue momentum of legacy MDSI NC software, and 3) figure out a way to port the PL/1-based Bravo code to new computer platforms.
In late 1992 Applicon launched Bravo Version 4 (the Bravo3 designation was dropped with this release) that implemented a new Motif-based user interface for several key Bravo modules including BravoDesigner (Editor), BravoSolids and BravoSurfaces, a geometric modeling technique called Dynamic Modeling, an interactive sketcher and substantial enhancements to most Bravo analysis, manufacturing and database modules. The new user interface featured icons, dialogue boxes, pull-down menus, pop-up tool palettes, and cascading menus. Version 4 was being offered on Digital’s DECstations running ULTRIX and VAXstations running OpenVMS. Digital had earlier launched its new 64-bit Alpha processor and Applicon planned to support the AXP 3000 workstations that used this processor by late 1993.
The company was once again planning to support non- Digital platforms, this time Hewlett-Packard systems. The plan was to work with HP to develop a translator to convert PL/1 source code to C. The two parties believed that this would require less effort than writing a PL/1 compiler for the HP workstations along with all the support code that would be necessary. The project eventually turned out to be both a financial and technical disaster.[32]
The company’s long term platform strategy was to function in a transparent heterogeneous computing environment. This would eventually mean that a customer could have a mixture of workstation from different manufacturers and Bravo data could be exchanged between workstations without user intervention. A major concern was that before this heterogeneous environment was available existing customers would switch to competitive CAD systems which ran on higher performance workstations than the Digital systems the company then supported. In April 1993 Applicon announced four marketing plans to prevent this from happening. LeaseNow enabled customers, for a monthly lease charge, have Applicon take over the responsibility of periodically replacing their workstations with newer, higher performance units. AlphaNow enabled customers to purchase current Digital systems and eventually upgrade to Alpha systems at no additional cost. OpenNow enabled customers to use Hewlett-Packard workstations as client terminals with Bravo still running on a Digital system. MigrateNow was a trade-in program that offer discounts higher than Digital’s standard trade-in discounts. The major problem with this strategy was that the port of Bravo to Hewlett-Packard UNIX workstations was turning out to be taking much longer than planned.
Perhaps the most significant feature of Bravo Version 4 was its new Dynamic Modeling capability. This technology, called Degrees of Freedom Analysis, had been jointly developed by Applicon personnel in Billerica, Massachusetts and the Schlumberger Laboratory for Computer Sciences in Austin, Texas. Most modeling systems at the time used either a propagational methodology where the sequence in which the model was created was critical to making changes, a variational methodology where each geometric constraint involved solving a set of equations or a combination of the two. Applicon’s Dynamic Modeling did not require that a design be created in a specific sequence nor that the model be fully constrained at all times. The result was software that offered a good combination of flexibility and speed. In mid-1993 Dynamic Modeling supported two-dimensional sketching with three-dimensional sketching planned for Bravo Version 5 scheduled for 1994. This new version of Bravo was also expected to incorporate Spatial Technology’s ACIS solids modeling kernel in place of Applicon’s internally developed solids modeling software.
One of the nicer features of the new Bravo user interface was a dynamic slider bar mechanism. The user could select a particular element or dimension of a model to be modified. This element was then represented in a slider bar dialog box with limits initially set to half the current dimension of the item and twice the dimension. As the user mover the slider bar, the model would adapt to the change in the size of the selected element and consistent with previously defined constraints. It was a very slick technique that showed up well in demonstrations and was actually a fairly practical design tool as long as the model was not overly large and complex. See Figure 7.7.
In June 1993, Applicon hired Frank Stefanik as vice president of marketing and business development. Stefanik had been around the CAD/CAM industry for nearly 20 years including a stint at McDonnell Douglas where he was a senior vice president. Except for Morley, he was one of only a few experienced industry executives hired by the company during this period. During an interview in July 1993 for an Engineering Automation Report article, Morley was optimistic about the company’s future. “If we have managed to do as well as we have with limited platform support, imagine what we can do when we are platform independent.”[33] The company aggressively promoted its numerical control experience, stating that its software supported 30,000 machine tools around the world.
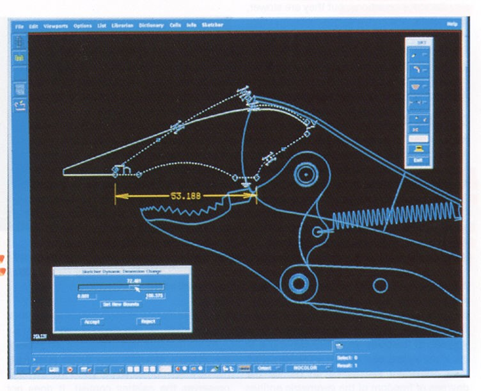
Gores Enterprises acquires Applicon
Within a few months of my visit to Ann Arbor and the upbeat interview with Morley in July 1993, Schlumberger was approached by Alex Gores, the CEO of what was then known as Gores Enterprises and today is called Gores Technology Group, with an offer to acquire the company’s Applicon subsidiary. Based in Los Angeles, Gores mode of operation was to acquire technology-related companies that were subsidiaries of larger companies, pare down the staff and overhead expenses and focus of selling products and services to the acquired organization’s existing customer base. It had previously done just that in early 1992 with GRAFTEK, a division of Unisys, that developed and sold mechanical design and NC software for the tool and die industry. Gores had also recently acquired the service business of NBI, a vendor of specialized word processing systems. In future years, Gores would become a very large buyout firm handling deals as large as Learning Company, the money loosing software maker that Mattel had earlier bought for $3.5 billion.
(As an example of some of the convoluted inter-relationships in the CAD/CAM industry, Gores at one time owned a company called Ventech that developed software products for the building materials industry. Ventech was subsequently sold to MAI Systems which became a key component of MAI Basic Four, the company Bennett LeBow used in his unsuccessful attempt to take over Prime Computer and its Computervision subsidiary.)
The acquisition of Applicon by Gores was announced on September 28, 1993. Schlumberger most likely decided to unload Applicon after twelve years because it didn’t see any light at the end of the tunnel. The CAD/CAM industry was going through a massive transition, moving away from turnkey systems to selling unbundled software. This changed the economic foundation for companies such as Applicon which had seen its annual revenue drop from over $100 million to just $70 million. Most likely, this had resulted in Schlumberger incurring losses which the company no longer was interested in absorbing.
The major concern voiced by industry observers such as Engineering Automation Report was that the new owners of the company would slow down development of new software and stop the fairly costly project to make the software multi-platform. The same day the proposed acquisition was announced, Applicon described Bravo Version 4 Plus which had been undergoing beta testing at customer sites including Figgie International. This version of Bravo was intended to support Digital’s new Alpha workstations running OpenVMS. Figgie reported that the Alpha-based Digital 3000 Model 300 and Model 500 were two to four times faster than the DECstation 5000 when doing graphics tasks and ten times faster when doing computationally intensive work.[34]
When the acquisition was announced, the statement was made that the plan was to operate GRAFTEK and Applicon as separate entities. Within a few months Morley was replaced as president of Applicon by Vance Diggins, a long term Gores associate and most recently president of Gores’ Graftek subsidiary. For the most part, Diggins ran Applicon remotely from an office in Boulder, Colorado and spent a significant portion of his time working on new deals for Gores rather than managing Applicon’s day-to-day business. The latter task increasingly became Stefanik’s responsibility.
The relationship between Gores and Schlumberger got off to a rocky start. Gores felt that Schlumberger had misled it concerning the financial condition of Applicon at the time of purchase and in the spring of 1994, it withheld some payments due Schlumberger. Schlumberger retaliated by sending letters to some Applicon customers requesting that they make maintenance payments directly to Schlumberger and not to Applicon. With users caught in the middle, the two companies renegotiated the terms of the acquisition and this storm soon became history.[35]
One immediate result of the Gores acquisition, however, was a slowing down of software development. Bravo Version 5 was originally scheduled to be released in 1994. In April 1995, the company announced Bravo Version 4.9 with just nominal enhancements. The press release for Version 4.9 promoted features such as the slider bar interface tool described above which had originally been released several years earlier with the initial Version 4 software. Another significant change was that Bravo now supported both its new MOTIF user interface as well as the original Bravo interface, making the transition to the new version easier for user organizations. The company also drastically changed how Applicon systems were sold. It did away with its vice president of sales and shut many of its European and Asian sales offices. These territories were taken over by distributors, some of whom were ex-Applicon employees.
Later in 1995, Michael Oehler, who had been president of Gores’ GRAFTEK subsidiary, was moved over to Applicon as vice president of business development with specific responsibility for sales and marketing activities in the Asia/Pacific area, especially China. It is not clear how much the company shrunk after Gores took over. One publication put the revenue at $35 to $37 million and 185 employees in early 1995[36] while another publication said that the company had nearly $50 million in annual sales and was doing it with 200 employees as of late 1995.[37] Applicon’s target market space consisted of companies that designed and manufactured mechanical machinery – especially industrial equipment built to order or in small to medium volume. About 58 percent of its business was in Europe with Germany its largest single market in that area.
Applicon as a Gores Company
In late September, 1995 Applicon finally released Bravo Version 5.0 which incorporated the ACIS modeling kernel from Spatial Technology. This precise boundaryrepresentation modeler was marketed as a separate module called BravoSolids XL. It supplemented the faceted modeling technology that had been used in all previous versions of Bravo. Legacy faceted models could be directly regenerated as precise models in 5.0 and precise models could be converted back to faceted models. The new software facilitated the creation of hybrid models consisting of wireframe, surface and solid elements. Bravo 5.0 also implemented new NC software for controlling newly introduced mill-turn machine tools. While Bravo 5.0 was a significant improvement over earlier version, it was, for the most part, playing catch-up with the company’s primary competition. In a rather unexpected move, Applicon provided the media with a Bravo development roadmap up through Bravo 7.0 targeted for release in the fourth quarter of 1997, nearly two years in the future.
By early 1996, Gores had turned Applicon into a profitable business enterprise. The company had slimmed down from 600 employees at the time of the acquisition to about 200. Part of this reduction came from the termination of the PL/1 to C conversion project while other layoffs involved a dramatic decrease in the company’s marketing organization. The company claimed that by the beginning of 1996 it had paid off the purchase cost to Schlumberger and that the company was debt free. Revenue was in the $50 million range and the company was profitable.[38] With a smaller staff, developers were able to obtain input directly from users rather than having it filtered by marketing since there was very little marketing left in Ann Arbor.
Under Gores management the on-going conflicts between the MDSI and Applicon forces within the company were finally contained. This was important because, increasingly, Applicon was pursuing small to medium size manufacturers who needed effective NC software. BravoNCG (G stood for graphics) used legacy MDSI Compact II technology that directly linked the part programming process to specific machine tool/controller combinations without the need to use a post processor. This was particularly important in regards to new machine tools and controllers that used complex canned cycles or sequences of operations. One problem at this point in time was that the NC software still used the older Bravo user interface.
The platform portability issue also was becoming more manageable. Instead of continuing the technically difficult PL/1 to C converter development, Applicon was now taking advantage of new compiler development technology. Since many other companies with Digital and IBM PL/1 legacy code were moving to UNIX workstations and servers, a cottage industry had sprung up providing PL/1 compilers for these software firms. Applicon contracted with several of them to provide PL/1 software that would enable the company to port Bravo to Hewlett-Packard’s HP/UX operating system in early 1996 and Microsoft’s Windows NT later that year or early 1997. Engineering Automation Report’s biggest concern about Applicon at this point in time was that although the company had a well thought out product development strategy, the company needed to accelerate its schedule for these developments if it were to remain competitive in a rapidly changing industry.
Gores Enterprises subsequently used Applicon as a vehicle for acquiring several other small technology companies. It set up a subsidiary called Applicon Holdings for this purpose. Two such acquisitions were made in January 1996. The first was, HoSoft GmbH of Munich, Germany, a developer and supplier of engineering data management and product data management software. Applicon had been using HoSoft’s CORA II software as an integral part of its BravoFrame PDM package used by over 120 companies.
The second company was Computer Design, Inc. of Grand Rapids, Michigan, acquired from Masco Corporation. CDI’s key product was U4ia (pronounced Euphoria) which at the time was one of the best software packages available for visualizing fabric material. Use of this software varied from automotive seating design to fashion design. I was hired by Vance Diggins to help evaluate this business opportunity and was very enthusiastic about the potential of merging Applicon’s modeling technology with the visualization tools provided by CDI. For several months, I tried to convince Diggins of the market opportunity for technology that would enable high-end retailers to offer clothing tailored to the shape and size of individual customers. Unfortunately it was an idea before its time and Gores put little money into advancing CDI’s technology and the company soon faded into the background.
In March 1996, Applicon was finally able to announce support of Bravo on Hewlett-Packard Series 9000 UNIX workstations. By mid-1996, Frank Stefanik had the title of executive vice president and chief operating officer. In July, Bravo Version 5.5 was released with support for personal computers running Microsoft’s Windows NT operating system. BravoPiping, which was used extensively by German shipyards, now incorporated the ACIS kernel. Other enhancements included a streamlined user interface, the ability to open large assemblies significantly faster and support for the latest machine tools. In August the company introduced a new NC simulation package using software from Sirius Systems. On September 11, 1996 Stefanik became president and CEO of the company. Diggins was promoted to the position of president of the newly renamed Gores Technology Group.
Several other products were launched around this time including BravoSAT_MFG for importing parts and assemblies from other packages that used the ACIS kernel. The company also indicated renewed interest in DesktopBravo software with improved PC versions of Modeler and Detailer running under Windows NT. A few months later, Applicon announced that it would be utilizing a number of additional Spatial Technology products including Advanced Blending and Local Operations as well as ACIS Shelling from Geometric Software Services. The company’s soon implemented applications using ACIS 2.0 with these capabilities as well as user interface enhancements, three-dimensional piping design on the Windows NT platform, and more extensive use of ACIS modeling capabilities such as variable radius fillets and the shelling of thin-wall parts.
Bravo Version 6.0 was released in early 1997 and then Bravo 6.5 in December 1997 with a number of useful enhancements including dynamic dimensioning, isometric dimensioning, compound blending of solids models, three-dimensional piping isometrics, input and output of STEP AP203 assemblies and a new photorealistic rendering module using NuGraf from a company called Okino.
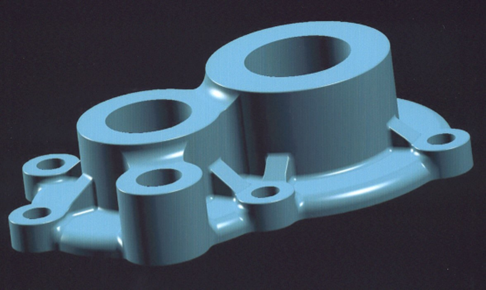
Applicon’s slow fade into the sunset
Over the next two years, Applicon continued to add functionality to Bravo in terms of improved modeling capabilities and new applications with the focus continuing to be a the manufacturing side of the business. Revenue continued to slowly decline as the company had less and less of its income coming from the sale and support of hardware products. By 1998 revenue was down to approximately $40 million annually. There were still approximately 5,000 customers utilizing 40,000 seats of Applicon software. Late in 1998, the company announced Bravo 7.0 that contained a number of enhancements that facilitated the modeling of large assemblies.
Bravo 7.0 also proved users with a “top-down” mode of product design. This methodology enabled users to design individual parts within the context of an assembly. As an example, if a user were to change the size of a particular part, it would be immediately apparent what other parts were affected by this change. The new release also contained a number of new techniques for defining the relations between individual parts in a large assembly. Bravo’s built-in Librarian and its Product Data Management module, BravoFrame, were particularly well suited to managing all the parts that went into large assemblies. According to Engineering Automation Report, one Applicon customer had modeled a complete submarine in solids with 35,000 individual parts.[39] Version 7.0 also saw new sheet metal design and fabrication applications.
By 1998 the CAD industry was becoming divided into two primary camps: the large vendors who sold fairly expensive comprehensive suites of tightly integrated software packages and the mid-range vendors who sold lower cost packages with less functionality than their more expensive competitors. Applicon tried to be a little bit of each. Its software no longer matched the functional richness of its high-end competitors such as PTC, Dassault Systemes or Unigraphics Solutions so the company dropped its prices closer to what the mid-range vendors were charging. Applicon also promoted aggressively the fact that its software was available on PCs running Windows NT as well as on UNIX workstations. Customers were able to mix NT PCs and UNIX workstations in a single design environment and readily share data transparently between the two types of systems.
Announcements and product availability continued to lag. It was March 1999 before the new sheet metal design software began shipping and the manufacturing software was delayed until the second quarter of that year and then further delayed to summer. Once Engineering Automation Report got a chance to review Applicon’s latest Version 7.5 sheet metal design software it was particularly impressed with its capabilities.[40]But other than the new sheet metal software there was little of significance happening at Applicon by this point.
The end of the road
The end of the road for Applicon came in August 1999 when Unigraphics Solutions (now a Siemens subsidiary) announced that it was acquiring Applicon. Gores’ management had decided to sell Applicon and they approached UGS with an offer to acquire Applicon’s engineering personnel as well as the company’s customer base which nicely complemented UGS’ own customers. At this point, the company had annual revenues of less than $30 million, much of which was most likely from software maintenance rather than new license sales. UGS reportedly paid less than $10 million for what was left of the one-time number two player in the industry.[41] From a product point of view, the biggest question was how would UGS handle the fact that Bravo was based upon Spatial Technology’s ACIS geometric kernel when it developed and marketed Parasolid, ACIS’ primary competitor?
The ACIS issue did not become important as UGS never seriously tried to take advantage of the Bravo software technology. The key rationale behind the acquisition was that it had acquired 60 programmers who were less than 50 miles from UGS’ major automotive customer base in Detroit at a point in time when it was very difficult to hire competent programmers. Except for some sales people, most of the Applicon personnel stayed with UGS. One exception was Frank Stefanik who stayed with Gores. Initially, the former Applicon employees reported to Raj Khoshoo who was responsible for UGS’ IMAN product data management software. They were cross-trained in I-MAN and other UGS products as well as put to work on some integration projects.
Applicon customers who were on maintenance contracts were given the option to continue using Bravo or switching to UGS software products such as Unigraphics or Solid Edge. UGS came out with one additional release of Bravo, Version 8.0. Eventually most of Applicon’s users switched to Unigraphics while some started using the company’s Solid Edge software which UGS had earlier acquired from Intergraph.