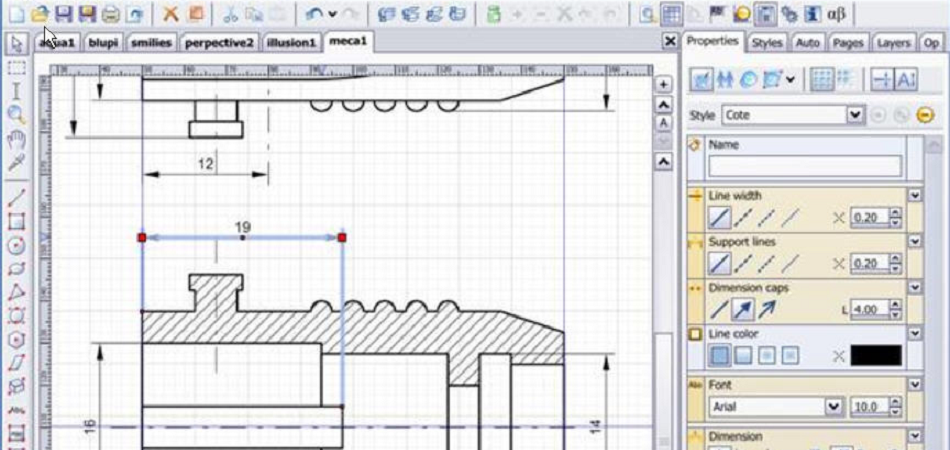
Author’s note: I joined Auto-trol Technology in January 1980, initially as director of product planning. In subsequent years I was director of product marketing, director of AEC application development and director of marketing support where my primary responsibility was competitive analysis. In late 1985 I started a government sales organization, an assignment that lasted until late 1990. During my last year at Auto-trol, I was responsible for both the AEC and Technical Publishing business units. As a consequence, much of this chapter is based upon my own experiences at Auto-trol.
Auto-trol’s evolution as a company
Auto-trol Corporation was founded in 1962 by Bill Barnes and his wife, Tammy, whom I had worked with at the Colorado Department of Highways in 1960. Bill was an extremely creative engineer who was always coming up with novel ideas for new products and markets, some of which were practical and some less so. The company’s name came from “Automatic Control.” Its initial focus was in building industrial control systems, including control equipment for bakeries.
Fairly soon, however, Auto-trol began building large precision digitizers which were used for civil engineering, mapping and electronic design applications. These were about the size of a drafting table and used an optical technique for tracking the cursor position. During the 1960s I would run into Tammy on occasion at trade shows where the company had a booth and would be demonstrating its digitizers. Around 1970, Auto-trol began interfacing its digitizers directly to minicomputer systems, much like Calma was doing at the same time as described in Chapter 11.
Auto-trol never got much beyond about a million dollars in revenues during these early years and in either 1971 or 1972 the Barnes sold the company to Electronic Assistance Corporation (subsequently known as EAC Industries). In May 1973, Howard Hillman purchased a controlling interest in the company. EAC forgave all the loans it had made to Auto-trol except for $150,000 which was repaid later in 1973 and EAC received 2,000 shares of Series A Preferred Stock and 15,000 shares of Class B Common Stock. Hillman paid $50,000 for two million shares of Common Stock and agreed to lend the company additional funds with which to operate and expand.
Howard Hillman’s wealth derived from a large industrial empire headquartered in Pittsburgh, formed early in the 20th century by his father, John Hillman. Howard’s mother, Dora, married John Hillman and John subsequently adopted Howard and his brother Tatnall who were Dora’s children from an earlier marriage. John Hillman, who died in 1959, also had a son from his first marriage, Henry, who is somewhat older than Howard and has run the family business, The Hillman Company, for many years. The Hillman Company was originally involved in heavy industrial commodities such as coke and iron ore including the Pittsburgh Coke & Chemical company but since Henry took over, it has been more involved in real estate development and investments such as Genentech, the first successful biotech company.
Dora Hillman established a trust fund for Howard and his family in 1970 known as the Howard B. Hillman Trust. At one time, this trust fund was sufficiently valuable that Howard was listed by Forbes Magazine as one of the 400 richest people in the United States with a net worth of over $600 million. While Henry, who stepped down as chairman of the Hillman Company in 2002, is still on the list (#68 and worth $2.8 billion in 2006), Howard and Tatnall, who has a similar trust fund, are no longer listed, which probably suits Howard Hillman just fine. It is the Howard B. Hillman Trust which has provided the majority of the funds over the years used to finance Auto-trol. Without the constant infusion of cash from Hillman and the trust, the company probably would have folded in the early 1990s, if not sooner.
For a number of years, this initial $50,000 outlay looked like one of the most brilliant investments in the history of the computer industry. When Auto-trol went public in 1979 at $14 per share, Hillman’s investment was worth $28 million. In the third quarter of 1980, the stock price peaked at $61.50 per share making the $50,000 investment worth $123 million and all the loans Hillman had made to the company up until then had been repaid. It was all downhill from that point. During the next 20 years, Howard invested over $100 million in the company. Most of these funds were initially provided as loans and subsequently converted to equity. In January 2002, the company announced that it was going private at a price which valued Hillman’s investment in the company at less than $12 million.
When the company went public in 1979, the name was changed to Auto-trol Technology. It turns out that there was a company in Wisconsin also named Autotrol that manufactured waste treatment equipment. At some point it the late 1980s, this other company actually became an Auto-trol Technology customer.
Development of early CAD systems at Auto-trol
When Howard bought Auto-trol, it was being run by John Dzien. Dan McNeil was responsible for sales, Lou Coen was marketing support manager and Peter Skaates was in charge of software development. The first interactive graphic system developed by Auto-trol was Auto-Draft which dates back to 1973. (Although the company’s IPO Prospectus says 1970, I believe the company’s earlier systems did not support drafting capabilities but were basically computer-controlled digitizing systems.) Auto-Draft was developed as an AEC and mechanical drafting system as differentiated from comparable systems from Calma and Applicon at the time which targeted integrated circuit mask making and engineering design respectively. The first Auto-Draft system was installed at an Alcan (a subsidiary of Alcoa) facility in Canada. Other early Auto-Draft customers included Exxon, Phillips Petroleum, Allied Chemical and Sylvania.
It was no surprise that Auto-trol selected Tektronix storage tube technology for the graphics portion of this system. Nearly everyone else in this new industry was also using Tektronix terminals. What was somewhat surprising, however, was the selection of Varian Data Machines to supply the minicomputer around which these systems were built. The first Auto-Draft systems used Varian’s 620/L computer. A typical four station system sold for $250,000. To put a few prices from this period in perspective a 5MB disk cost $16,900, a 40” by 60” flatbed plotter cost $39,600 and a Tektronix 4014 terminal was $21,000. The software was priced at $13,650.
Most of the early systems were used for what can best be described as production drafting. As an example, the system at Phillips Petroleum was used to prepare process flow diagrams, electrical schematics, printed circuit board layouts, assembly drawings and perspective drawings. Phillips claimed that it was getting a 3:1 productivity improvement with this system. Auto-trol sales personnel tended to focus on productivity gains although they sometimes got carried away. I have seen documents where the company claimed that a 10:1 increase in productivity could be expected. While this might have been true for some highly repetitive drawings, it is highly unlikely that such gains could be expected over a wide range of work.
Don Smith became president of Auto-trol in 1974 and several years later he hired Jim Starnes as senior vice president for marketing operations. In 1976, the Sperry Univac Division of Sperry Rand acquired Varian Data Machines. At about the same time, Autotrol began the development of a new CAD system called the AD/380, which used Sperry’s V76 and V77 minicomputers. As best as I can tell, the first AD/380 systems were shipped in 1977. Until the introduction of the CC-80 described below, graphics terminals were pretty much standard Tektronix 4014 devices.
The AD/380 was designed to support up to 12 user workstations and, in fact, the company had installed several with 9 or 10 4014s by early 1979. Auto-trol used a fairly standard version of the VORTEX (V77 Omnitask Real-time Executive) operating system which provided effective multi-tasking with dynamic memory management capabilities. As a result, each workstation could utilize a different software application if desired. One of the key features of the AD/380 was that it could run batch programs in background at the same time it was running interactive graphics software. V77 systems could support up to a megabyte of main memory and a range of disk drives including a 300MB removable disk pack unit manufactured by Control Data Corporation. At the beginning of 1980, the standard computer being used was a V77-600. One problem that continually caused the company grief was that the machine had an optional floating point processor that used a different data format than that used by the system’s floating point software subroutines.
By the time I joined the company, Auto-trol had 169 customers with an installed base of approximately 225 AD/380 and Auto-Draft systems. This probably amounted to 1,000 user workstations. A typical system with four workstations sold for about $380,000. That probably did not include the cost of a high-end plotter which could add $40,000 to $50,000 to the price of the system.
In 1976, Auto-trol also began the development of a new graphics workstation called the CC-80. It used a 19-inch Tektronix 619 storage tube display which supported limited refresh capabilities as well as standard storage tube display functions. The CC-80 incorporated a Texas Instruments TI-8800 microprocessor which off-loaded many display tasks from the AD/380 minicomputer. See Figure 9.1.
The CC-80 was one of the finest products ever built by Auto-trol. A significant amount of human factors engineering went into its design. Since CAD systems of that era were designed to be used by full-time operators, motorized height and tilt adjustments were among the features built into the unit. The screen could be raised if it were being used with a digitizer and the operator was standing or it could be positioned for tall or short seated operators.
The CC-80 included a large table on which drawings could be spread out, an alphanumeric display that enabled messages to be displayed without interfering with the drawing being displayed on the storage tube monitor and a 240-button panel called an ACTEC, made up of pressure sensitive switches. These buttons were programmable and typically initiated application-specific functions. The company provided plastic overlays for its different applications. A second optional 240-button panel could be installed when desired. There was also a typical keyboard and a joy-stick cursor control device. Autotrol began shipping the CC-80 in May 1979 and by the beginning of 1980 had delivered 225 units. The CC-80 sold for $35,000 to $40,000.
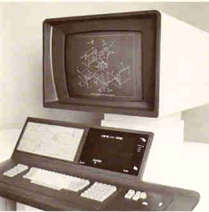
Among the other products Auto-trol manufactured was the OPTEC line of digitizers. These were descended from the original products the company had been making since the early 1960s. The OPTEC digitizers came in a variety of sizes and resolutions with and without backlighting. There were two versions, one which used a gantry arm to restrain the cursor while the other was a free cursor model. Another product was the Mark 4 flatbed plotter. This was a monster of a machine. It was built like a battleship gun mount and the joke around the company was that you could ride on the gantry that carried the pens. It was large enough to plot two E-size drawings side by side. The OPTEC digitizers caused the company few problems compared to the Mark 4. The plotter used a metal band to position the pen carriage horizontally and vertically. These bands were constantly breaking and they were difficult to replace and calibrate in the field. The company spent a disproportionate amount of resources repairing these units.
In general, the AD/380 and the CC-80 were excellent hardware products. There were several problems, however. The most serious from an engineering and support point of view was that every AD/380 system was custom built. Auto-trol purchased basic computers from Sperry and added a substantial amount of its own hardware to each configuration. The design of the system’s wire-wrapped back plane was predicated by the specific peripheral devices attached to that system. One result was that it took several weeks to check out a new system and each one had to have the operating and applications software specifically generated for that configuration.
When Auto-trol came out with a new software release, it could not just be copied and sent to all the customers on maintenance. Instead, the company had to perform a SYSGEN (system generation) operation for each machine and distribute a customized version of the software code to each user. This meant keeping accurate records describing each installed machine, a nearly impossible task. Most of the company’s competitors had eliminated the need to do this years earlier by using standardized computer configurations.
Auto-trol was also different than most of its competitors in regards to how it provided basic training. Customers would actually use the specific system being assembled for their company to learn on. Until the company went to more standardized systems, this seemed to work quite well. When companies were paying $125,000 per seat for CAD systems, they were more than willing to send operators to Denver for two or more weeks of training.
Auto-trol software by 1980
At the beginning of 1979, Auto-trol was offering two software products, GS-100 and GS-200. GS-100 was an expanded version of the original Auto-Draft software implemented on the AD/380 system while GS-200 was the company’s initial stab at creating a mechanical design solution. If an AD/380 system had both suites of software, it was referred to as GS-300. While GS-100 was a very good production drafting package, GS-200 was not ready for prime time. After the company had installed several copies at test sites, it became apparent that Auto-trol had bitten off more than it could chew.
In June 1979 Auto-trol signed a software license agreement with Manufacturing & Consulting Services to use AD-2000 as the basis for a new mechanical design solution to be called GS-2000. See Chapter 15. At the same time, GS-100 was renamed GS-1000 and the combined solution GS-3000. The first GS-2000 installation was made about the time I joined the company at the beginning of 1980.
GS-1000 might well have been the most productive AEC drafting solution then on the market. Over 50% of the installed base of 225 systems was in the petrochemical and architectural and engineering design market space. The company sales organization specifically targeted large petrochemical users. The software had the typical complement of geometry creation and editing functions then found on competitive systems.
GS-1000 used a command language for determining user operations. As an example “R” stood for rectangle and “CC” for circle. Each command had a number of options. For example, with the circle command the user needed to tell the software how the circle was to be defined (center and radius, three points, etc), what line type was to be used for the circle and how the coordinate values were to be defined (keyed in or screen selected). Once a command option was defined, the system would use that information until the operator entered a change. Some commands, such as dimensions, were very extensive with as many as a dozen options.
A complex command, or even a series of commands, could be made part of a macro called a Quick Action and assigned to a button on the ACTEC panel or to a button on a digitizer menu. While it took users up to six months to become proficient with this command language, once they did, they were extremely productive. When you watched some of the company’s better application engineers doing demonstrations, their hands were a blur moving over the keyboard.
GS-1000 supported 256 data layers which was a competitive advantage over M&S Computing (Intergraph) since that company’s software supported just 64 layers.
The software also did an excellent job inserting crosshatch patterns. GS-1000 came with a large set of such patterns. When Autodesk introduced AutoCAD several years later, that software’s set of crosshatch patterns was virtually identical to what Auto-trol had been providing for a number of years. The company also provided fairly extensive sets of application-specific symbols.
What really separated GS-1000 from the competition was the Quick Action macro capability. One of the advantages of a command language system over a pure menubased system is that it is easier to implement a powerful macro capability without it having to be a separate language. A GS-1000 Quick Action or QA could be as simple as a single command or it could contain hundreds or even thousands of steps that would create entire drawings. One customer created a complex QA that literally designed an entire steel rolling mill based upon data the operator entered. Two important aspects of QAs were that they could pause for operator input and that they could be nested much like software subroutines. QAs were a key tool used in developing industry-specific applications.
While GS-1000 was a fairly powerful drafting tool and one Auto-trol could be proud of, the company was quite weak in regards to industry-specific applications. There were a few applications for process plant piping design and electrical schematics as well as a limited architectural floor plan package and some mapping software. One area where Auto-trol had made good progress was in creating a package for technical illustration that was initially called ATIPS. This was one market segment the company has been strong in for over 25 years and one of the few drafting-specific applications it still supports as this is being written.
Product development in the early 1980s
Auto-trol grew from $1.4 million in revenue in 1975 to $50.8 million in 1980. The basic AEC drafting product was solid and the company was sufficiently profitable that there was money available to develop a viable mechanical product line if it was done wisely. The company had gone public a year earlier and its stock had more than doubled since then. Don Smith ran the company on a day-to-day basis as president with Hillman visiting Denver from his home in Connecticut every couple of months.
Smith had hired Jim Starnes several years earlier to run the sales and marketing side of the business. In 1979 Starnes began a fairly blatant effort to replace Smith as president. Starnes felt that the company needed to move more aggressively in developing a raster display capability and in moving into more advanced application areas such as mechanical and electronic design. He quietly began lining up internal support to become president. Just before I joined the company, Starnes made his pitch to Hillman who responded by recommending to Smith that he fire Starnes which he did. Starnes went on to start Graftek in Boulder, Colorado, taking a number of Auto-trol employees with him as described in Chapter 21.
Mike McGarr had been brought on board in late 1979 from Varian to be executive vice president of internal operations. In early 1980 Smith hired Graham King as executive vice president for field operations, filling the vacancy created when Starnes was fired. Graham’s brother, Bob King, was on the company’s board of directors. While on the surface this looked like a good move because King had 15 years of significant sales management experience at IBM. In retrospect it laid the foundation for the gradual disintegration of what could have been a dominating company in the CAD/CAM industry.
As described below, a major factor impacting Auto-trol was the influx of former IBM sales and marketing managers – John Rodgers, Jim Hammock, Gene Barduson, Joe Zemke and others. Even Don Smith was ex-IBM. A number of sales managers in the field including Jim Norrod and Dave Hanna were also brought on board from IBM. They were all good, smart individuals. The problem was that they believed sales and marketing could overcome any product deficiencies a company might have. This was towards the end of an era when people in the computer industry were fond of saying, “on any given day IBM could swap product lines with UNIVAC and within a year, IBM would be back on top.”
One of the byproducts of this focus on sales and marketing, particularly sales, was that new product development did not receive the resources it needed. Perhaps the biggest problem was that the company was excessively focused on the manufacturing aspect of its business. In fact, a few days after I started work, Don Smith told me in no uncertain words to “remember, this is a manufacturing company.” Until 1980 this probably made considerable sense. The margins generated on internally manufactured products served to fund the software development then underway. Software was really a mechanism to help sell more hardware.
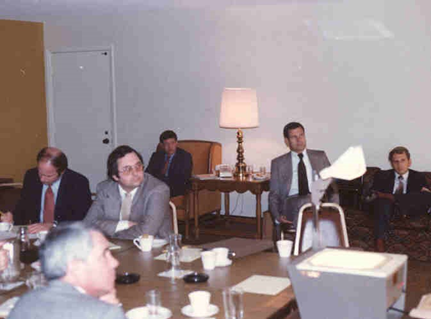
Clockwise from lower left: Mike McGarr, Bob McFarland, Dave Weisberg, Graham King, Don Smith, Art Minich (Note business dress even though this was a weekend off-site meeting)
V77-800 computer transition
A fairly complex project in 1980 was the introduction of the Sperry Univac V77800 minicomputer as a complement and eventual replacement for the V77-600 that had been used up until then to power most AD/380 systems. The first new unit was shipped in early June 1980. The V77-800 was perhaps one of the best 16-bit minicomputers ever manufactured from a performance point of view. Unfortunately, Auto-trol was the only company using the machine for CAD systems and the company was not able to obtain much marketing support from Sperry.
While the AD/380 had been designed from the start to support up to 12 workstations, the reality was that the V77-600 did not have the horsepower to support more than about six without adversely impacting performance. The V77-800 provided the power that enabled the company to sell larger systems. In June 1980, Auto-trol shipped several systems worth over $600,000 each and one that sold for over $700,000.
While Auto-trol was in the process of introducing the V77-800, the company realized that it had to move to the new generation of 32-bit minicomputers which were becoming increasing prevalent for engineering design systems. A major activity throughout 1980 was the evaluation of available computer systems from companies including Sperry Univac, Digital Equipment, Data General, Systems Engineering Laboratories, Prime Computer and Interdata (Perkin Elmer). Eventually, the company decided to go with the Digital VAX product line.
Planning the future of GS-1000
A major project at the same time was determining the future of GS-1000. This software package was primarily written in assembly language for the V77 product line. The company kept looking for a way to convert the code to FORTRAN without having to manually rewrite it. Several questions Auto-trol struggled with for months were whether or not to create a 16-bit V77 FORTRAN implementation or to concentrate on developing a 32-bit version for whatever new computer platform the company selected and the extent to which the new software had to be compatible with the existing GS-1000 program.
In the later area, there was no question that the new version had to be able to import drawing files created with GS-1000. Whether the new files had to be backward compatible with GS-1000 was a different question. It would be a more difficult task to accomplish the latter and the company did not know how important this capability would be for its existing customers. Auto-trol eventually decided to make the new software backwards compatible as well. It proved to be a difficult task and several key users later told the company that it really did not have to be done. By then it was too late. One important decision was that the new program would be able to execute existing QAs without modification. That turned out to be a smart decision.
Mechanical design software
Auto-trol’s mechanical activity, especially in regards to software development, was in turmoil in 1980. The initial development was done under the direction of Ron McElheney who had hired a fairly large staff in a period of just a few months. While Auto-trol produced several GS-2000 brochures in 1980 it is not clear how much of the software was really working on the AD/380. Most of the illustrations in the company’s early brochures appear to be standard AD-2000 screen shots produced by MCS.
In early 1980, McElheney left to go to work with Jim Starnes at Graftek, taking several of the GS-2000 programmers with him. The development group subsequently was managed by Dave Custer, reporting to Art Minch who had replaced Ed Vrablick as vice president-software sciences. Custer had a crew of about 15 people, few of whom had any prior experience working with three-dimensional mechanical design software. Most of the effort actually went into programming an AD-2000 interface for the CC-80 workstation along with adapting AD-2000 to the other AD/380-specific hardware components.
Management changes
Around mid-1980 several management changes occurred at Auto-trol. Gene Barduson, who had been brought in by Graham King as director of national accounts, became director of marketing programs. The title was a misnomer since Barduson’s focus was almost entirely on the mechanical market. During the next year or so, he built up an impressive marketing staff – Jim Newcomb who went on to become a senior manager at Dataquest, Dave Burdick who has had a significant career as an industry analyst at Dataquest and Gartner as well as an independent consultant, Walt Simpson who joined Auto-trol from Computervision and Terry Bennett who also ended up as an industry analyst.
The other change was to split mechanical applications development off from AEC application development. Auto-trol tended to treat application development as a marketing function rather than as an R&D activity. Dick Burkley was brought in to run the mechanical side of this activity. He had been working at IBM on its CADAM software when Auto-trol hired him. Burkley brought with him a level of software management expertise that the company sorely needed.
In another move around mid-1980, Bob McFarland, who had been national sales manager before John Rodgers and was now director of marketing moved to London to run the company’s European operation. As noted earlier, Auto-trol’s sales and marketing activities were taking on a very IBM look and McFarland, apparently, did not fit the mold. He would stay in Europe for about a year at which point, he was replaced by Rodgers.
The biggest change, however, occurred on August 14, 1980 when Graham King replaced Don Smith as president and CEO. Although Smith was expected to stay on for a while as chairman of the board, he soon relinquished that position. King recruited a friend from his IBM days, Joe Zemke, to replace him as executive vice president of marketing.
A missed opportunity
The computer industry is full of stories about missed opportunities. If only company X had done such and such, its future might have been significantly different. In the fall of 1980, Auto-trol had an opportunity to radically change its future and passed. The situation involved Jim Clark, the founder of Silicon Graphics and Netscape.
Bill Brett, Auto-trol’s vice president of engineering had become aware of work being done at California Institute of Technology and Stanford University on the design of advanced integrated circuits using methodologies developed by Carver Mead. Clark was associated with Mead and had some ideas for creating a new generation of graphics processing circuits using Mead’s techniques.
Brett invited Clark to visit Auto-trol one weekend. I remember the meeting clearly because we met that Saturday at my condo. I had previously arranged to have furniture delivered that day and had to be there. We basically put together the outline of a business plan for the development of a new generation of graphic systems. The idea was to set up a separate entity in which Auto-trol and/or Hillman separately would invest and Auto-trol would take the resulting product to market. I was not involved in pitching the concept to Hillman – Brett handled that task. Auto-trol never funded Clark’s idea and he eventually went off and started SGI using roughly the same concepts we had discussed that weekend.
Years later Hillman was asked why he didn’t go along with the plan the three of us had worked up and his response was that it proved to be impossible to pin down what Clark would be responsible for and what Auto-trol would be responsible for. My personal opinion is that the two of them simply couldn’t work out a mutually agreeable financial arrangement. Auto-trol then went on to invest several million dollars in developing a new generation of graphics terminals, products that mostly never made it to market.
Rationalizing Auto-trol’s products
By mid-1981, Gene Barduson was responsible for the company’s mechanical software products. At some point (it could have been earlier in 1980) Auto-trol decided that working with MCS on updates to AD-2000 was becoming impossible and that the company would be better off taking full responsibility for the source code. The problems with MCS were a combination of business and technical issues. For a lump sum payment of $1 million, Auto-trol received the latest version of the AD-2000 source code and full rights to resell it to end users.
While GS-2000 was struggling to gain market traction against companies such as Computervision, Applicon and Calma, GS-1000 was holding its own in the AEC market primarily against Intergraph and to a lesser extent, Computervision. It was becoming increasingly obvious, however, that GS-1000 was loosing its technical edge and that a new 32-bit version written in FORTRAN was the way to go.
Although few in the company admitted it at the time, the lack of a color raster display was also becoming a severe sales detriment. In 1981, machine-independent software was not a well-accepted practice (AD-2000 was an exception) and most software was written for specific computer systems. The initial plan was to develop the new version of GS-1000 for the Digital VAX.
Implementing GS-2000 on the VAX was not a major challenge since the software had already been ported to that machine by both MCS and Tektronix. The major task was developing the interface to the VAX for the CC-80 terminal.
It is interesting to note that in its July 6, 1981 issue, Business Week, ranked Autotrol 4th in the nation in regards to the percent of revenue spent on research and development. We were spending 12% on R&D. That sounds low by today’s standards for high tech companies, but in 1981 it was significant. Auto-trol ranked 3rd in terms of actual dollars per employee spent on R&D, $9,277. In retrospect, Auto-trol may well have achieved its high rating because it included as R&D charges items many other companies allocated to other expense categories.
The first of many layoffs
During most of 1981, it appeared that Auto-trol’s sales were holding up fairly well. Unfortunately, the company had put an expense budget in place that required a even more substantial growth in revenues than what was occurring. Shortly before Labor Day the decision was made that the company would have to reduce staff by 15 percent. This would turn out to be the first of many such layoffs over the years.
The cutbacks led to a moderate reorganization of sales and marketing. AEC application development had been run by Clair Johnson, an extremely outgoing manager who portrayed a cowboy image complete with black cowboy hat and boots. To be as objective as possible, he was in over his head technically and his people did not particularly like working for him. He was one of the few managers let go during the layoffs, ending up a few months later as director of sales and marketing at MAGI, a graphics visualization company. Jim Hammock, who was vice president of marketing, asked me to take over this department as part of the reorganization.
This was a confusing period of time for Auto-trol. The company had started rewriting GS-1000 for 32-bit computer systems but AEC application development was still being done for the 16-bit Sperry V77-600 and V77-800 systems. At the time, the new CAD software was called GSX but was eventually marketed as Series 5000. Some of the other projects underway at the time are described below.
Exploration Mapping – Over twenty years later, derivatives of this software are still in use around the world in the form of a package Auto-trol calls GEOSTATION. Most mapping-related programming at the time was being done at that time by a single individual, Bill Adams, with only a small amount of assistance from other programmers. The primary focus of the mapping software was to assist oil and gas exploration organizations in keeping track of seismic survey and well data. These were often quite large data files covering extensive geographic areas. GS-1000 was particularly well suited for handling this type of information.
Adams had a rather novel idea for managing map data. Up until then, most mapping application done with CAD systems involved storing spatial data as CAD geometric entities and related data as attribute tags. GS-1000 did this about as well as any competitive systems then on the market. The problem was that large maps had to be divided into a number of separate files, each representing a single map sheet. When an area that covered portions of several sheets had to be displayed, the process was both difficult to accomplish and typically very time-consuming. Adams’ idea was to store both the spatial data and the attribute information in a database and simply generate views of this data based upon what the user desired to work with at a particular point in time.
He called this “throw away graphics” since the displayed images were not saved, just the underlying database. It was an efficient technique, even considering the overall performance of the V77 systems the company was using at the time. The most comparable competitive system was probably Intergraph’s. They had a database application, DMRS, that was closely linked to their interactive graphics software, IGDS. The difference was that spatial data was stored in IGDS and only attribute information was stored in DMRS. Where Auto-trol had strong sales and technical support such as in Calgary, Canada, the company was able to compete effectively with Intergraph. For many years, the company’s exploration mapping software was the best selling Auto-trol product in Canada. Eventually, its development and support was moved to Calgary.
Architectural Design – By today’s standards, Auto-trol’s architectural design software was extremely crude. It could just do basic floor plans and disassociated elevation drawings. In spite of the fact that GS-1000 was nothing more than a power drafting system, there were a number of large architectural firms using it.
For several years the company put significant resources into developing architectural space planning software. The concept was that an architect would be able to define which groups needed to be near each other and which did not. As an example, the CEO’s office needed to be near the board room but neither needed to be near the cafeteria.
The software would analytically determine an optimum floor plan layout. Although it sounded like a natural application for GS-1000, it proved to be a more difficult program to write than initially contemplated and the market for this type of software never really developed. The architectural drafting software, on the other hand, eventually turned into a fairly decent product called PLAN, once Series 5000 matured.
Drafting Utilities and Schematic Drawings – One success story was Auto-trol’s introduction of a set of drafting utilities called A-PLUS, developed by Dave Peverley working with Chris McGary. As mentioned earlier, one of the strongest features of GS1000 was its Quick Action capability. A-PLUS consisted of a set of QAs that facilitated production drafting. It was a fairly simple concept yet it was the first time that these functions had been pulled together in a package that was made available to all users.
In late 1981 Auto-trol established a relationship with Jim Fox, an independent software developer living in the San Francisco area. Fox had developed some useful GS1000 software while working as a contractor for Exxon including a package for doing electrical schematics and process and instrumentation diagrams (P&IDs). Auto-trol worked out an agreement with Fox under which the company would sell this software renamed RAP-EL and RAP-ID and pay him a 50% royalty.
The assumption at the time was that this would be an interim solution until Autotrol could develop its own packages in this area. In retrospect, the royalty rate was far too high and the packages needed substantially more cleanup and documentation by Autotrol than the company had contemplated. But Auto-trol needed software in this area fast and this was one way to get there. Those of us involved at the time never expected that ten years later Auto-trol would still be selling Fox’s software and paying him substantial royalties.
In the late 1990s Fox sued Auto-trol claiming the company owed him a substantial amount of money, particularly in regards to maintenance revenue it had collected from numerous government accounts. Eventually, the judge threw out the case because too long a period of time had transpired before Fox sued.
Structural Steel – In the late 1970s Auto-trol sold an AD/380 system to Bancroft & Martin in South Portland, Maine to do steel detailing[1]. They developed some rather good GS-1000 software to handle detailing functions. The two companies worked up an agreement under which Auto-trol would take Bancroft and Martin’s software and productize it. Soon thereafter Auto-trol set to work planning the development of a suite of steel applications that would include the design of steel frameworks, the interface to analysis software, the design of connections and structural detailing.
In mid-1982, Joe Zemke had a meeting with Don Greenberg of Cornell University who was well known for his pioneering work in visualization software. Zemke and Greenberg hit it off well and soon Greenberg was in the process of developing a structural steel design package for Auto-trol. It was very well done with an excellent user interface and it put an end to any internal work in this area.
Called Steel-3D, this package was only loosely connected to the company’s basic AEC CAD software – what eventually became Series 5000. A follow-on package for designing concrete foundations called Foundation-3D was also produced by Greenberg’s team. There was one major problem with Steel-3D – it only handled steel members at a time when customers wanted a structural package that would do reinforced concrete components as well. While the initial software was well done, the informal agreement Zemke had worked out with Greenberg did not call for the level of follow-on activity that was really needed to make the package successful.
One major user of STEEL-3D was Qwens-Corning Fiberglass which used the software to design factory structures. According to Robert Schaefer, who was responsible for installation of the system at OCF, STEEL-3D resulted in saving about 20 percent of the weight of a building’s steel framework. At $2,000 per ton for structural steel in the mid-1980s, this meant a savings of about $60,000 on a 100,000 square foot manufacturing building.[2]
The company Greenberg put together to develop STEEL-3D was called 3D/EYE. In the mid-1990s this company introduced an excellent conceptual design software package called TriSpectives which subsequently became IronCAD. (See Chapter 21.)
Process Plant Design – In the early 1980s, by far the largest market sector for Auto-trol was in process plant design. The company had numerous customers among engineering design and construction firms including Bechtel, Brown & Root and Haliburton as well as the operating companies themselves including Exxon, Shell and Air Products. Most of these customers were using GS-1000 for production drafting. The company offered a few industry-specific applications including an orthographic piping design package which was really little more than a sophisticated symbol library. It did include checking features that ensured that components such as valves, flanges, tees, etc, were compatible with the elements they were connected to.
For some time, Auto-trol had been attempting to define and develop a comprehensive plant design package. One of the company’s problems in this area was that Auto-trol had virtually no marketing or technical people who understood plant design at a high level. This was solved when Jim Hammock hired Tom Curry[3] who had been manager of design engineering at Air Products. Curry came on board in late 1981 and set about defining what a real plant design solution should look like. He subsequently hired as a consultant Michael Leesley who had previously been responsible for process plant software development at Computervision and was the editor of Computer-Aided Process Plant Design, a massive 1,378-page tome covering everything from computer architecture to piping analysis. Leesley was hired as a consultant to advise the company on how it should proceed with developing a state-of-the-art process plant design system. In 1982, Auto-trol decided to have a new company Leesley had established in Texas develop a plant design system from scratch. It was to be funded through a research partnership arranged by Hambrecht & Quist in which Howard Hillman put up some of the money. It was funded to the tune of about $7 million dollars. The rationale behind this form of funding was to isolate Auto-trol from the quarterly R&D expenses involved. Eventually, Auto-trol would market the software and the expectation of the investors was that the company would then buy them out at a nice profit.
Doing plant design development outside the mainstream of the company’s R&D organization proved to be very disruptive to the internal organization. Auto-trol made a costly acquisition of another CAD software company, Tricad, to provide technology that top management perceived could not be developed internally. Leesley proved to be inept at managing a large project and the partnership was eventually terminated with no useful software resulting. As a consequence, Intergraph soon began taking away much of Autotrol’s process engineering business and by the late 1980s, the company had little new business in this sector.
Apollo and Series 5000
In 1981, I began to read about a new computer company, Apollo Computer, that had been founded in 1980 by an MIT classmate, Bill Poduska. Auto-trol’s engineering department had been working on the design of a stand-alone graphics system with emphasis on high performance graphics. Apollo’s system was similar to what Auto-trol was working on except that Apollo incorporated the concept of networking their machines together in what it called a token ring architecture.
In October 1981, a group of Apollo managers including Bill Poduska visited Auto-trol and pitched their new system. My reaction and that of several other Auto-trol managers was that with a few changes, this was just what we were looking for and that it would separate Auto-trol from other CAD companies that were concentrating on using Digital VAX minicomputer systems. The biggest shortcoming of the Apollo hardware at that time was its relatively weak graphics capability. Our thought was if we combined Auto-trol’s graphics expertise with Apollo’s computer and networking expertise we would have a great system. Within a few months, Auto-trol became one of Apollo’s first significant OEM customers.
Porting the GS-2000 mechanical design software to the Apollo platform was not a major task and at the 1982 NCGA conference in Anaheim, California, the company was able to show a prototype of what was now called Series 7000 in operation. It was the hit of the show. Meanwhile, development of Series 5000, the eventual replacement for GS1000, was proceeding at a reasonable pace and it was decided to initially implement the new software on the Apollo platform rather than the VAX. Don Zurstadt was the Series 5000 project manager for this effort.
At this point in time, the Auto-trol management team consisted of:
- Graham King – president and CEO
- Joe Zemke – executive vice president
- Jerry Sisson – vice president/international Gene Barduson – vice president/sales
- Jim Hammock – vice president/marketing
- Paul Jerde – vice president/finance
- Carnig Izmirian – vice president/field engineering
- Bob McFarland – vice president/international
- Art Minich – vice president/R&D
- Bill Taylor – general council
European joint venture
In 1981 Auto-trol established a joint venture with an Italian company, Selenia, to handle the sales and support of the company’s products throughout Europe. This joint venture basically took over all of Auto-trol’s then existing European operations which really were not much. Denny Chrismer was sent to Italy to be Auto-trol’s full-time representative in the joint operation. Although Selenia was headquartered in Rome, the joint venture operated out of Genoa.
Auto-trol’s product line in the mid 1980s
From 1983 through 1985 some of the key development projects included the following:
Advanced Graphics Workstation (AGW) – As mentioned earlier, Auto-trol’s most visually recognizable product was its CC-80 series of workstations as shown earlier in Figure 9.1. When Auto-trol signed an agreement to OEM Apollo workstations, the company’s initial reaction was to maintain the continuity of these workstations by simply replacing the original Auto-trol manufactured control logic with the Apollo computer and graphics controller. The result was a highly productive workstation that was, unfortunately, significantly overpriced for newly emerging market conditions. Eventually, Auto-trol decided that standard Apollo workstations were more price competitive than the repackaged AGW.
Advanced Raster Workstation (ARW) – Before selecting the Apollo platform, Auto-trol had decided to port its software to Digital’s VAX computer. For this, the company needed a color raster workstation. Initially, the plan was to develop its own raster graphics capability. This work proceeded rather slowly under Bill Brett’s direction with much of the design work done by Mho Salim and Jerry Peterson[4]. Eventually, it was decided that third party technology would be a better route to take and the company signed an OEM agreement with Raster Technology in August 1982 to incorporate that company’s graphics hardware in the ARW.
Advanced Personal Workstation (APW/15) – In an attempt to provide Series 5000 software on a PC, Auto-trol created a hybrid system that consisted of a UNIX coprocessor installed in a MS-DOS PC. The objective was to minimize Auto-trol’s programming effort in providing a PC solution. The product was introduced in mid-1985 but never sold in any significant volume. Bob Stevenson, who was responsible for this project, in a recent interview, stated that the major problem was that Hillman insisted that the price be about twice what Stevenson thought the market would support.
Series 5000 – This new graphics system was initially released in 1983 and received good reviews from Auto-trol’s customers. Most were impressed with the compatibility maintained with older GS-1000 systems and with the software’s performance and geometric accuracy. Dave Peverley put together some excellent demonstrations to illustrate the effectiveness of 32-bit data structures. One major problem was that so much effort had gone into developing Series 5000 that there were few resources available for creating new applications that would take advantage of the software. Auto-trol had no concept of working with third party application developers as did Autodesk and did not realize, at the time, the strategic handicap this would be.
Plant Design – The research partnership with Michael Leesley to develop a Process Plant Design (PPD) system was formally launched in early 1984. It started badly and went downhill from there. The basic concept was excellent, comparable to products subsequently sold by Intergraph, CADcenter, Bentley and Rebis. Tom Curry and Michael Leesley put together an extensive business plan for the PPD in December 1982. The problem was not in the concept which was excellent but in the execution of the plan.
It probably didn’t help that it took over a year from publishing the PPD plan to actually starting work on its development. Leesley hired one experienced plant design software manager from Calma, Malcolm Hall, but most of the rest of the team he put together in Austin, Texas had little experience in this area. There were also some problems with Leesley’s management style. According to Curry, Leesley was a little too much of an empire builder and was focused more on personal issues such as a new house he was building in Austin than concentrating on the project.
This lack of plant design experience was compounded by two bad decisions. First, they needed a relational database management package. After surveying what was then available, the team, including Auto-trol personnel, selected EMPRESS. This was not a bad database product, it was just very immature and EMPRESS never gained much marketplace traction. Unfortunately, Auto-trol decided that it would also use this database package for other application development. A lot of things might have turned out differently if the company had selected a more popular database product such as Oracle or Informix.
The second mistake was the decision not to build the plant design solution around Series 5000 but to acquire Tricad as described below. Although this project was supposedly “off the books” because of its research partnership structure, it had a major impact on other activity at Auto-trol. As an example, Dick Burkley spent nearly a year assigned full time to the plant design project, taking him away from important mechanical application development work.
Eventually, Auto-trol and the investment people at H&Q decided to pull the plug on the research partnership. They were a long way from having a workable solution and the money that was left would not have covered what still needed to be done. Some of the work done in Austin was salvaged and was used in developing VectorPipe, a product Auto-trol still sells in Europe.
Tricad – This was an AEC software company Bill Hambrect from H&Q was involved with. Altogether, the VCs had invested $7.7 million over four years. Auto-trol purchased the company for about $2 million in stock in early 1985. Tricad, which at its peak had 65 employees, was down to 15 people when Auto-trol took over. The company’s head of R&D was Roger Sturgeon who had previously worked at Calma. Tricad put together a building design solution that was one of the first to incorporate object-oriented software concepts. Although Auto-trol made the acquisition, the intent was almost entirely to support Leesley’s plant design software project. Tricad had about 20 customers at the time of the acquisition, few of whom remained Auto-trol accounts once they were told that the Tricad software would no longer be supported.
There was one exception. Tricad had sold its software to the U. S. Army at Fort Huachuca, Arizona to do communications network engineering. Dave Hanna thought this was a great business opportunity for Auto-trol and a huge amount of effort was spent in 1985 and afterwards trying to develop a viable communications engineering business for the company. The basic Tricad software was called G-3 while the communications engineering software built on top of it was called TEAMS (Telecommunications Engineering and Asset Management System). One of the few Tricad people who stayed with Auto-trol was the salesman on the Fort Huachuca account, Bud Broomhead.
Mechanical Design – In general, Auto-trol never seemed to be able to generate as much traction in the mechanical CAD area as management had hoped. GS-2000 was renamed Series 7000, the software was ported to the AGW and applications such as sheet metal design and finite element modeling were added to the original AD-2000 software. By late 1983, Series 7000 and related applications made up nearly 60% of the company’s system business.
Auto-trol also licensed a solids modeling package that was only loosely tied into Series 7000. Some aspects of this software, particularly the company’s ability to edit NC tool paths was as good as anything the competition offered. The short-term relative success of the mechanical product line was partially due to the fact that few AEC applications had been ported from GS-1000 to work with Series 5000 as of late 1983, slowing sales in that market for a period of time.
Steel-3D – Although this was perhaps the most visually attractive AEC application Auto-trol had, the company was not able to use it to leverage a significant volume of new systems business. The lack of concrete design capability was one factor but the high price was probably a bigger detriment.
MOSS – In the latter part of 1985 the AEC marketing group negotiated an agreement with England’s MOSS Systems to market their civil engineering design software in North America. This was an excellent package except that it was primarily a batch computer program at the time. MOSS Systems agreed to develop an interactive interface and the Auto-trol people took on the responsibility of integrating it with Series 5000. This took a year or so to accomplish.
Mapping – The oil well posting software described earlier was probably the best internally developed application the company had during this period. Auto-trol had acquired its Canadian distributor, CANDRAFT, several years earlier and under Ken Dedeluk, it was doing very well selling this package in Calgary.
More management changes
Auto-trol went through its share of management changes during the early to mid 1980s. In November 1982 Hillman fired Graham King[5] and Joe Zemke took over as president. Terminating King cost the company over $800,000 to settle outstanding stock options and other obligations. A few months later Jim Norrod became vice president of U.S. sales. Few people have had a more immediate impact on a company’s sales momentum then Norrod did. He was an incredible bundle of energy who got everyone moving at a faster pace. The results during the next several years were impressive.
After he left Auto-trol in 1986, Norrod became president of CGX , a manufacturer of IBM 5080-compatible graphics terminals eventually acquired by Adage. Subsequently he was president of Tellabs and several other high tech companies. In March 2005, he became president and CEO of Segway, Inc., the company formed by Dean Kamen that manufactures the Segway Personal Transporter.
The biggest problem with Zemke running Auto-trol was that it was simply too small a company for his style. His training at IBM had prepared him to run an organization where he had a much larger support group than he had at Auto-trol.
On February 28, 1985, I traveled to Santa Clara, California with Zemke to visit Sun Microsystems. At the time, Auto-trol was considering switching from Apollo to Sun or at least complementing the Apollo portion of the company’s product line with a Sun option. We spent much of the day with Scott McNealy and other Sun executives (at that time it was a 900 person company doing about $120 million annually).
Late that afternoon I drove Zemke to the San Jose airport, supposedly to catch a plane while I went off somewhere else, probably another meeting in the area or in San Francisco. Zemke never told me where he was headed probably because he was not going anywhere. Instead he rented another car and went to an interview with Amdahl. Shortly after returning to Denver, Zemke announced that he was leaving Auto-trol to become president and COO of Amdahl at a salary of $600,000 per year or about three times what he was making at Auto-trol. Within a few months Jim Hammock also left Auto-trol for greener pastures in California.
In less than five years Auto-trol had gone through three presidents, all of them exIBM executives. Hillman decided that before he hired another president, he was going to spend more time in Denver and temporarily run the company himself for a few months. Twenty years later he is still in Denver running Auto-trol although he stopped referring to this as a temporary assignment many years ago.
In either October or November 1985, Jerry Sisson asked me if I would undertake the task of establishing a marketing activity to support the company’s business of selling systems to federal government agencies. His idea was to model what we would do after the government systems group Sun Microsystems had set up under Carol Bartz who subsequently became president of Autodesk in 1992.
It became apparent fairly quickly that there was considerable potential federal government business available and that the competition was fairly well defined. In the mechanical area the primary competition was Computervision with secondary competition from Calma and a little from Applicon. In the AEC area the competition was primarily from Intergraph with secondary competition from McDonnell Douglas.
Autodesk was not yet a factor having just begun shipping PC-based software. Many government agencies which had purchased relatively small first or second generation CAD systems and were now preparing for major expansions of these systems.
Auto-trol under Howard Hillman
Gradually, Auto-trol began to replace the early AGWs which had the Apollo computers repackaged in CC-80 consoles with standard Apollo computer systems. At this point, the company decided to offer its software unbundled as well as bundled with computer hardware. Auto-trol charged a premium of $3,000 to $5,000 for unbundled software to offset the lost margin that resulted from not selling the hardware. At the time, a number of other companies did the same thing and customers seemed to go along with it at first. Auto-trol also had work underway porting its software to run on Sun workstations.
Auto-trol software, including applications as well as Series 5000 and Series 7000, was licensed for a specific piece of computer hardware. These licensing arrangements were controlled by using encryption keys tied to the identification code of the hardware.
This made it difficult for users to move applications from one network node to another. Also, when customers purchased a new Apollo computer, they could not move the software to the new node without Auto-trol’s permission.
The company saw this as an opportunity to generate incremental revenue and the list price for a license transfer was $5,000. This was a hard sell since most customers thought that they had purchased a perpetual license for the software. They had, as long as they wanted to run it on obsolete hardware. If one tries to identify all the little things that eventually led to Auto-trol’s demise, this was a contributing issue. Within a few years customers would look at the $5,000 license transfer fee and decided that they could get along with AutoCAD rather than Series 5000 and save several thousand dollars in the process.
One of the other pricing problems involved software maintenance. Auto-trol had quantity discounts for software that were actually fairly aggressive. In quantities of 12 or more seats, unbundled Series 5000 had a list price of $11,500. The company was much more reluctant to discount software maintenance, however. Auto-trol had three different service zones depending how far the customer’s site was from an Auto-trol field office. The software maintenance cost for Zone III was over $350 per month per node or $4,200 per year just for Series 5000. Either of two things resulted from such steep maintenance pricing, the prospect selected a competitor once they considered multi-year costs or Autotrol ended up with unhappy customers who felt they were being ripped off.
Government sales activity
In the late 1980s, one bright spot for the company was the success it had selling both AEC and mechanical CAD systems to government agencies at the local, state and federal levels. Some of Auto-trol’s major government accounts included:
Western Area Power Administration (WAPA) – Like many other government sales opportunities over the next few years, the incumbent vendor at WAPA was Intergraph. The major complicating issue on this deal was the need to include an X.25 packet switching communications system. Curt Loomis, the salesman on the account, identified communications equipment from GT&E that would handle the task and the company incorporated it into its proposal. It was probably a $150,000 portion of what turned out to be a $4.2 million contract. It was the first time Auto-trol took on this type of systems integration work.
Another issue, as it would be in numerous accounts for the next several years, was that the Request For Proposal (RFP) was oriented around a minicomputer-type solution and Auto-trol had to justify that its Apollo workstations were an equal or better approach. The proposed Series 5000 system included a major installation at WAPA’s Denver facility and smaller systems, some just a single workstation, scatter around most of the West other than California. Altogether, the initial contract in late 1986 was for 29
AGW/22 workstations and 15 NSP/32 servers at 13 separate sites. It included options for 50 additional workstations that had the potential to add another $5 million to the contract value. WAPA never executed all the available options although it did order a significant number of additional workstations from Auto-trol.
WAPA was Auto-trol’s first big win in the government area. They told Loomis that we had won but not to make the fact public until they released the information to the press. Loomis, Hillman and I went out to WAPA’s office in the Denver West Office Park to witness the signing of the contract. When we got back to Auto-trol, Jerry Sisson called all the employees together for a company meeting in the cafeteria. Everyone thought there was another layoff coming and they were extremely pleased when he announced the largest contract award in the company’s history.
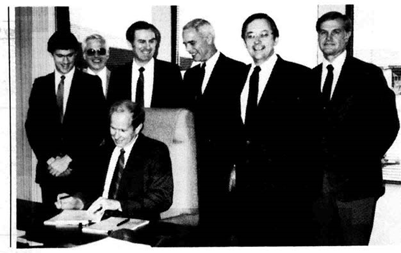
Seated: Don Ray, contracting officer, Western: standing (I-r ): Curt Loomis, senior account manager, Auto-trol; Tom Weaver, assistant administrator for engineering, Western; Bill Clagett, administrator, Western; Howard Hillman, president and chairman of the board, Auto-trol; Dave Weisberg, director of Federal Systems Group, Auto-trol; and Will Jacoby, chairman, technical evaluation panel, Western
U.S. Air Force Logistics Command – Auto-trol had installed its technical illustration software at Hill Air Force Base under a subcontract to Syscon, a San Diegobased system integrator. That project, which involved automating the preparation of aircraft maintenance manuals, was called ATOS or Automated Technical Order System. A Technical Order is the way the Air Force describes a maintenance manual. Similar systems were subsequently installed at other Air Force logistic centers. Separately, the Air Force Logistics Command initiated the procurement of a mechanical CAD system. Auto-trol responded to the RFP and won a $1 million contract by just $4,000 with Calma as the runner-up.
The Air Force proposal was complicated by the fact that the company had to include finite element analysis software as part of its bid. Auto-trol’s intent to bid
NASTRAN from MSC for the FEA portion of the contract was further complicated by the fact that this was a fixed-price lump-sum contract and MSC licensed its software on an annual fee basis. They eventually agreed to a lump sum cost for bidding purposes which was key to Auto-trol being compliant. The contract included a clause that allowed five other Air Force logistic centers to procure systems off the same contract. By the end of 1989, Auto-trol installed nearly 140 Apollo workstations running either Series 5000 or Series 7000 software at six Air Force Logistics Command sites.
Federal Aviation Administration – The major proposal activity towards the end 1987 was a large project for the Federal Aviation Administration. The systems would be installed at nine regional engineering centers around the country. Intergraph already had three small installations at the FAA and the initial specifications were clearly written in their favor. The specifications called for minicomputers and workstations with dual screens, something that only Intergraph offered. After much arguing, these restrictions were loosened allowing Auto-trol to bid.
The FAA came to Denver in early 1988 for a fairly extensive benchmark test. Under Dave Peverley’s direction the company was getting pretty good at these. The benchmark went very well and at the end, one of the FAA managers said, “I don’t know if we want to select Auto-trol to be our vendor or just hire this guy Peverley.” Indicative of how rapidly computer hardware prices were beginning to change, a decisions was made by Auto-trol to increase the memory in each of the proposed AGW/22s from 2MB to 4MB at no additional cost to the FAA. Apollo’s prices had come down enough since the proposal had been submitted a year earlier that the company could do this without adversely impacting the profitability of the deal.
After several months of negotiations, Auto-trol finalized a contract with the FAA on October 3, 1988 for $16.6 million. The FAA eventually issued 20 contract modifications to this initial contract, the last one in September 1996 for a total of probably $30 million.
The next major step was to configure one of the regional engineering office systems and run through an extensive factory acceptance test. The acceptance test went well and by mid-February 1999 Auto-trol was ready to begin shipping equipment to the various FAA regional engineering offices. The contract called for nine regional systems totaling 22 servers and 176 workstations. Each initial configuration had six to ten Apollo workstations, digitizers, a plotter and a substantial amount of software and had a value of between $600,000 and $1 million. Throughout 1999 Auto-trol shipped one such configuration every 21 days like clockwork.
Kennedy Space Center – In late 1987 Auto-trol was awarded a substantial contract by Lockheed Aircraft. The Lockheed operation at the Kennedy Space Center in Florida was responsible for servicing the Space Shuttle between flights. Bill Brett had left Auto-trol several years earlier and gone to work for Lockheed which probably helped the company obtain this business. The contract involved a large number of AGW workstations and Series 5000 software to support this work.
Los Angeles Department of Engineering – An extensive effort was spent in 1989 on a proposal to the City of Los Angeles Department of Engineering. From a technical point of view, it was similar to the FAA project other than the fact that all of the installations were in one relatively small geographic area.
The competition with Intergraph was typical of what was going on between the two companies at the time. Intergraph was in the midst of making the transition from VAX-based systems to their new Clipper workstations but not all the company’s AEC software had been ported. As a consequence, they bid a VAX-based solution with the intent to swap it out in the future for Clipper workstations. No one in the city’s engineering department liked that option. Intergraph actually underbid Auto-trol $2.3 million to $2.6 million for Phase I of the contract. The third finalist, McDonnell-Douglas came in at $3.5 million. With options, the contract amounted to $6.4 million
One of the primary reasons for procuring this system was to support work being done on the huge Hyperion waste treatment facility that was then under construction south of Los Angeles Airport. An interesting sidelight was the fact that the city had a Computervision system that was being used to prepare detailed street and parcel maps of the city. This work was being done in a very laborious manner working from detailed survey data rather than scanning existing hard copy maps even though the city had an Optigraphics system it was very happy with.
Auto-trol and the Navy’s CAD-2 Program
Note: See Chapter 14 on Intergraph for additional discussion of this government project.
At the Defense Computer Graphics Conference in Washington, DC, in December 1985, Dale Christensen gave a briefing concerning a planned major Navy CAD procurement. Subsequently referred to as CAD-2, this project involved multiple procurements for different Navy commands using a basic set of common specifications. The impression in late 1985 was that the CAD-2 procurement would occur in 1986 or 1987 at the latest. In reality, this effort dragged out into the early 1990s before most of it was awarded to Intergraph. During the next five years, Auto-trol spent a large, but manageable, amount of effort tracking CAD-2 and preparing to bid for these very large contracts.
The Navy distributed a Request For Information (RFI) at a pre-bidders conference in White Oaks, MD in February 1986, but then nothing much happened. In 1987 the Navy distributed preliminary specifications and asked vendors to provide written comments. Potential vendors were also individually invited to meetings at the China Lake Naval Weapon Station in California. Auto-trol took the position that the specifications were far too detailed and that the Navy should provide vendors with more opportunity to bid what they felt were the best approaches for getting the job done. Auto-trol also pushed to have more technical illustration functions included in the procurement which the Navy never did.
In early 1987 CAD-2 was restructured into five specific command-centric procurements:
- Ships – Naval Sea Systems Command (NAVSEA)
- Airplanes – Naval Air Systems Command (NAVAIR)
- Buildings – Naval Facilities Engineering Command (NAVFAC)
- Electronics – Space and Naval Warfare Systems Command (SPAWAR)
- Printing – Naval Supply Systems Command (NAVSUP)
The Navy planned to issue a single RFP document with each requirement identified as to its applicability to specific solicitations. In addition to criticizing overly detailed and restrictive specifications (which Auto-trol did every chance it had), the company recommended separate RFP documents for each of the five procurements. In March 1987, the Navy sent out an amendment to the RFI that added a huge number of complex requirements that were specific to ship design. Auto-trol took the position that these requirements went way beyond the capabilities of traditional CAD/CAM solutions and that implementing the tight software integration the Navy was looking for would be nearly impossible.
In April 1987, Christensen visited Auto-trol for a briefing that covered the company’s WAPA installation, numerical control software, database software, industrial facility design and the latest Series 5000 capabilities. As described in Chapter 14, the procurement process then came to a grinding halt. By late 1988, Auto-trol was focused on two of the CAD-2 procurements, NAVFAC and NAVSEA.
Auto-trol was up against some fairly heavy competition. Several large defense contractors announced they were going to bid and talked about budgets in the millions of dollars to do so. As an example, Lockheed was teaming with Newport News Shipyard, Digital Equipment and McAuto. At this point, the company realized it was in over its head and pulled out of the CAD-2 procurement.
Auto-trol becomes a reseller of Auto-CAD
In early 1988, Auto-trol signed an agreement with Autodesk to resell AutoCAD as a complementary product to Series 5000. The company was starting to see some serious competition from AutoCAD but everyone at Auto-trol felt that Series 5000 was a far superior CAD package, which it was at the time. The concept was that when customers wanted copies of AutoCAD to complement their Auto-trol installations, it would be best if they bought the software from Auto-trol instead of a local dealer. This would help the company retain account control.
Except in Canada, Auto-trol never sold much AutoCAD. The company actually tried to sell the software at list price while most dealers severely discounted the package as a loss leader for other business such as selling the PCs AutoCAD ran on. The Canadian sales organization set up a separate group to pursue AutoCAD business while in the U. S. it was treated as just one more item in the price book.
1990 – A year of major changes
Every company goes through a number of inflection points where its business direction changes in sometimes unforeseen ways. Auto-trol went through such an inflection point in 1990.
- Jerry Sisson, who was vice president of sales and marketing, left the company in March 1990 and took a position with Precision Visuals in Boulder.
- Dave Hanna became vice president of marketing and initiated a thorough review of each market segment the company was in. The conclusion was to concentrate on the AEC sector and gradually withdraw from selling mechanical design and technical illustration systems.
- Howard Hillman took over running sales directly.
- In January, 1990 Auto-trol had another layoff and the company went into an aggressive cost containment mode including a 6% salary reduction.
- Hewlett-Packard’s 1989 acquisition of Apollo made it more difficult, but not impossible, to negotiate special deals for computer hardware on large government procurements. Also, with their ME-10 and ME-30 packages, HP was now a competitor in some mechanical deals.
- Much of Auto-trol’s software had been ported to Sun workstations and the company began to bid Sun hardware. Software development also shifted over to the Sun platform causing delays in a number of projects.
Reselling Pro/ENGINEER
In 1989, Auto-trol had signed an OEM agreement with Parametric Technology to resell Pro/ENGINEER. Series 7000 was strong when it came to mechanical drafting and NC but weak from a solids modeling point of view. Pro/ENGINEER was a strong solids modeler but initially had weak drafting and its NC capabilities were just about nonexistent. The company’s thoughts at the time were that it could sell customers a combination of the two packages and they would have the best of both worlds.
Auto-trol did not adequately take into consideration that most prospects would see this as a rather confusing approach and would prefer a single system that could do all three primary functions. Also, the company did not appreciate the fact that with a new system, PTC would be able to add new functionality at a pace far quicker than what Auto-trol was able to do with Series 7000. The result was that by mid-1990, Auto-trol was selling Pro/ENGINEER primarily as a stand-alone solution.
What Auto-trol had not taken into consideration was that PTC would actually end up being its primary competitor. In several situations, the company found itself bidding against PTC for the same business. In other cases, Auto-trol would do the hard work to get the prospect interested in the software and then PTC would declare the prospect to be a house account. They would pay Auto-trol a commission for the first sales but take all of the add-on business directly.
Auto-trol struggles to find direction
In late 1990, Auto-trol began experimenting with the idea of becoming more of a system integration business. A new Integration and Product Services Group (IPSG), managed by Terry Erdle, was established.
As it had for over a decade, Auto-trol was focused on three market segments:
Electronic Publishing Systems (EPS) – By 1991 Auto-trol was selling nearly $12 million annually in EPS systems including hardware, software and maintenance services. The company’s flagship product in this area, Tech Illustrator PLUS, was the best package then available for high-end technical illustration and is still being sold by Auto-trol today. The problem was always that this was a small niche market and there were limited opportunities to expand the demand for high-end systems outside of the defense/aerospace and automotive industries. There were over 600 copies of Auto-trol’s illustration software in use around the world in the early 1990s at companies such as Ford, General Motors, Pratt & Whitney and Boeing.
A major issue involving both the EPS and AEC efforts of the company was that both were dependent upon Series 5000 and there had not been a major release of this software since 1988. In the interim, much of the Series 5000 development resources had been consumed by efforts to port the software to Sun workstations and the implementation of an X-Windows graphics interface.
As an example of development interrelationships, a competitive shortcoming of Tech Illustrator was its inability to handle continuous tone scanned images. In order to add this capability to Tech Illustrator some fundamental enhancements to Series 5000 were needed. One reason for the lack of progress with Series 5000 was that the company had been working for over a year on a replacement to both Series 5000 and Series 7000 called Gemini. Auto-trol had difficulty defining what Gemini should be and the project was never adequately staffed.
While some of Auto-trol’s data translators were quite good, others left much to be desired. The most awkward situation involved IGES which required a user to import the IGES file into Series 7000 and then translate the Series 7000 file into Series 5000 using a direct translator. Although it was possible to make most of these steps transparent to the user, if there was a problem it was nearly impossible to pin down where the error occurred.
In an attempt to increase the EPS market, Auto-trol began marketing a low cost version of its illustration software on top of a stripped down version of Series 5000. Unfortunately, it never did sell well. This was followed in 1991 by a new package called TI EXPRESS which sold for $10,000, about half the cost of TI PLUS.
AEC Business Unit – The AEC side of Auto-trol’s story is more complicated. For the prior four or five years, the company had moved first in one direction then in another. Auto-trol had great plans for database-centric modeling solutions that could be used to design process plants and manage industrial facilities. The problem was that the company simply did not execute well in implementing these ideas. Some of the issues that had adversely impacted Auto-trol’s ability to develop a suite of quality applications included:
- If the money and time invested in the MLC project described earlier had been spent internally on products such as VECTORPIPE the company would have been much further along in developing a quality process plant design solution.
- After the company acquired Tricad there was significant indecision about whether Tricad’s G-3 or Series 5000 should be the CAD platform of the future. This probably cost Auto-trol two releases of Series 5000. As an example, there was an effort to produce a control schematics package built on top of G-3 that never got off the ground. This probably cost the company a year in eventually producing a decent Intelligent P&ID package.
- For a number of years, Apollo workstations had been the company’s primary development platform. When Auto-trol signed an OEM agreement with Sun Microsystems, the company implemented a massive switch to Sun workstations for software development. Most developers felt that it was a less efficient environment than what they had previously been using and the transition burned up a substantial amount of development resources.
- Porting Series 5000 and the AEC applications to the SUN platform and to ULTRIX, Digital’s version of UNIX, had not been managed well. The development team was slow to appreciate the fact that software had to be implemented from the start with the intent that it would be as close to platform independent as possible.
The major problem was that Auto-trol was simply trying to do too many things at once. Nearly everything contributed to the company’s bottom line to some extent so it was difficult to know what activities could be terminated or scaled back. For example, the company was seeing very little success in selling VECTORPIPE and other plant design software packages in the United States, but the same software was selling well in Germany and still does today. The same situation existed regarding its mapping software, GEOSTATION. It always sold well in Canada but never domestically.
Mechanical Business Unit – As mentioned earlier, the major marketing review initiated by Dave Hanna in 1990 had indicated that Auto-trol had little opportunity to become a major player in the mechanical CAD market. Supposedly, this was to result in the company reducing the resources devoted to Series 7000 and related products. Just the opposite happened however. In June 1991, Hillman hired Tom Rafferty as vice president of marketing and applications development, replacing Dick Burkley. Rafferty had previously been a vice president of development at Computervision and later at McDonnell Douglas. He came on board with the idea of developing a totally new CAD system from the ground up which would incorporate an internal database structured around the newly emerging STEP standard. This activity, initially called Monarch, took over the existing Gemini activity and charged off in a new direction.
Trying to regain momentum
If there is one truism about the CAD industry it is that once a company’s revenue starts slipping and earnings turn into losses, it is virtually impossible to turn the situation around. Auto-trol was no exception.
As a group, Auto-trol’s management team spent considerable time discussing and planning the transition of the company to more of a system integrator and consulting firm. The company had shown with its large government contracts and several commercial accounts that there was a viable market for these services. The problem was how to get from point A to point B when the company was experiencing declining sales and incurring significant annual losses. Also, if Auto-trol was intent on making such a transition, why was it investing a considerable amount of money in Monarch?
Erdle was a good choice to head up IPSG, but he never had the resources needed to go out and sell integration services. It appears that, at the time, Hillman did not understand that selling professional services was significantly different than selling hardware and software products. In a consulting environment, the person who typically ends up as the project manager is usually the key person involved in the sales process.
Auto-trol simply was not structured to operate in that manner.
Auto-trol was seeing considerable competitive pressure from Autodesk at this point but it was hard to get Hillman to respond. The previously mentioned agreement to resell AutoCAD had been cancelled by Autodesk in either late 1990 or early 1991. One meeting I participated in was indicative of the attitude. At a senior level sales meeting the conversation got around to competition and Ken Dedeluk, general manager of the company’s Canadian subsidiary, mentioned the increased competition he was seeing from Autodesk in Canada. Hillman became very upset saying “If you are competing with AutoCAD, you are going after the wrong business.” The misconception was that Autotrol, and not the customer, could determine who the competition would be.
Auto-trol in the 1990s and Beyond
Auto-trol’s revenues peaked in 1990 at $79.5 million although the company sustained a $1.3 million loss. In 1991, revenue slipped 19% to $64.4 million and earnings were a negative $7.9 million. This was the beginning of a long slide to where by 2001 the company was doing less than $8 million in annual revenues and still losing nearly $7 million a year.
Dave Hanna was killed in a tragic automobile accident in August 1992. To me, that took the heart out of the company. Howard continued to pour money into Monarch even after Tom Rafferty left the company. Interestingly, Bill Brett was hired back at that point and took over management of Monarch along with much of the rest of R&D.
Around 1993, Auto-trol linked up with a Houston, Texas-based software firm run by Susan Floyd. Floyd had developed a technical information management package while working for Lockheed at the Kennedy Space Center. Auto-trol eventually acquired the Houston operation and marketed the software as CENTRA 2000.
Another current product is KONFIG, a network management package derived from the TEAMS package mentioned earlier. In September 2002, Auto-trol changed the name of Centra 2000 to KONFIG Configuration Management. In fiscal 2001, the last year for which detail data is available, the company sold less than $2 million of software. The balance of Auto-trol’s revenues came from maintenance services related to software and hardware sold in earlier years. Amazingly, the company was still spending nearly $6 million per year on R&D.
Throughout the 1990s, Hillman continued to loan the company money and then convert the loans into stock. By September 30, 2001 he owned 99.4% of the outstanding stock in the company and in early 2002 announced that the company was being taken private. The stock still owned by public shareholders was purchased for $0.20 per share. After a reverse 1:10 stock split several years earlier, that meant a share selling for the equivalent of $615 in 1980 was worth 0.03% of what it had been selling for 22 years earlier.
As this is being written in mid-2007, Auto-trol is still being run by Hillman. The company’s primary software products continue to be the KONFIG configuration management software and Tech Illustrator. Auto-trol continues to sell GIS software, primarily in Canada, and process plant design software, primarily in Germany.