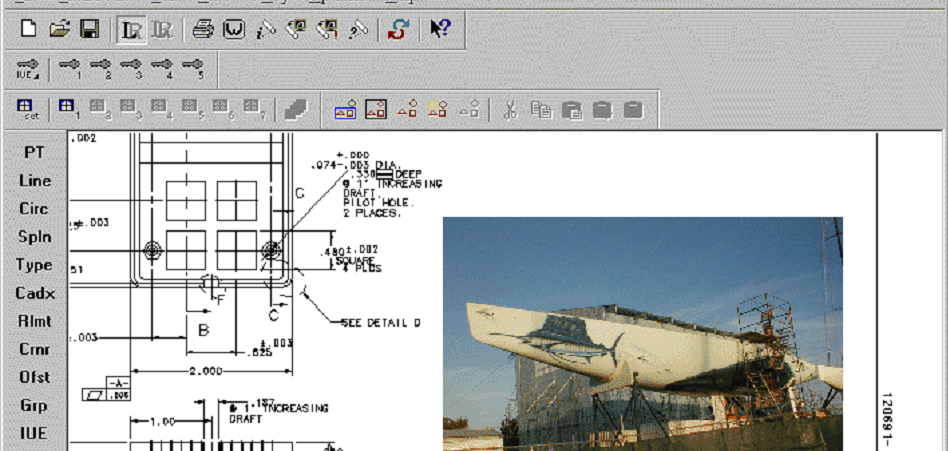
This is probably the most complicated chapter in this book in that it involves a number of different companies involved in an overlapping manner over several decades with multiple different products. It does not follow a strictly chronological format very well. Therefore, I have chosen to cover some of the following subjects over longer timeframes rather the chop them up into time-dependent chunks. Also, this is really the story of CADAM and CATIA and not of IBM per se. As a consequence, I have kept the discussion of IBM to the minimum required to put what occurred with these software products into context. Finally, although Dassault Systèmes acquired SolidWorks in 1997, that company and its products are discussed separately in Chapter 18.
Lockheed’s early development of CADAM
CADAM (Computer-graphics Augmented Design and Manufacturing) began as an internal mainframe application referred to as “Project Design” within Lockheed’s Burbank, California operation in 1965. It was initially implemented on IBM 360 computers using IBM’s 2250 graphics display terminals. From the start, a primary objective was to minimize response time. Working with IBM, the two companies determined that optimum productivity would be achieved if the response time for individual operations could be kept under 0.5 seconds. This was typically accomplished with CADAM although some critics claim that it was done by implementing commands that individually did less than what other systems accomplished with each command. According to these critics, the result was that it took more steps to accomplish a given set of tasks with CADAM than with competitive systems.
One of the first engineers assigned to Project Design was R. Lee Whitney who joined Lockheed-California as an associate engineer in late1965 after a brief stint at Boeing. He went to work for Boeing after receiving a BS in mathematics from Portland State University. He later added an MS in computer science and an MBA while at Lockheed. Whitney represents the most complete repository of information regarding CADAM in that he was associated with this product and MICRO CADAM for over 30 years.
As discussed in Chapter 4, Lockheed’s Marietta, Georgia operation had been an early adopter of CAD/CAM technology using a combination of internally developed software and commercial systems. Lockheed California, however, was reluctant to jump on the bandwagon in that the company felt that it would have to develop its own hardware since adequate graphic systems were not yet commercially available. When IBM introduced the 2250 display terminal in April 1964, this attitude changed and planning for an internally developed software system was initiated.
The first IBM computer system dedicated to computer graphics was installed in Burbank in early 1966 and software testing began in April of that year. The configuration consisted of an IBM 360/50 computer with 512KB of memory, a 2250 Model II display, a Model 2314 disk drive and a flatbed plotter. The initial design software (the name CADAM was not used until 1972) was developed by a team of six programmers working under the direction of Harold Bradley. Bradley was also responsible for the company’s NC activity and for a group doing lofting work. Within a few months this team had implemented basic design capabilities and was producing test NC parts.
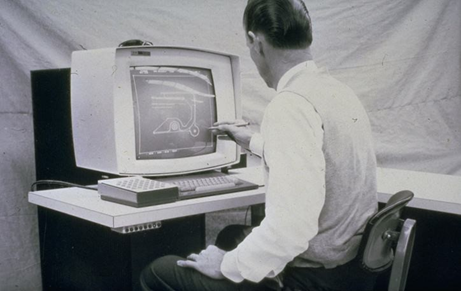
According to Whitney, one of most critical decisions the development staff made was to fit the applications they were working on to the computer environment at hand rather than get carried away trying to build the ultimate design and manufacturing solution. Early focus was on supporting Lockheed’s proposal to the Federal government to build a supersonic transport. One task was to demonstrate the precision of the software to the FAA. A model of the SST was created that enabled a user to zoom in on an ashtray placed between two seats. When the government decided not to pursue the SST in 1967, one result was a massive layoff at Lockheed California. One of the people laid off was Thurber Moffit, another industry pioneer who was acting as a consultant on this project.
The design system programming staff was reduced to just one person, Whitney.1
Lockheed started rebuilding the design project staff in late 1967 and soon it was back to a dozen programmers. Outside consultants included MIT’s Steven Coons and S.H. (Chase) Chasen from Lockheed’s operation in Georgia. Most of the development work was being funded by the Engineering Department at Lockheed.
The mainframe implementation of what eventually became CADAM was forced to live with a number of limitations imposed by the hardware and the time-sharing mode of operation. The latter factor dictated that models had to be kept small, otherwise one or two users working with large models could slow the system down for all the other users.
Early IBM graphics terminals such as the 2250 had only 8KB of refresh memory, limiting how much graphics could be displayed at one time. There were also problems with the floating point format IBM was using in the mid-1960s. It was less precise than the alternate IEEE standard and truncated results rather than rounding. Whitney describes a test in which he rotated a 100-inch line 180 degrees in one degree increments. At the end of the test, the line was just 97-inches long.[1] As a result, careful attention was subsequently paid to avoiding numerical accuracy problems.
As mentioned elsewhere, pointing devices such as light pens only react to seeing light on the display’s monitor. It was not difficult to select elements such as the end of an existing line but it was very difficult for the user to input a coordinate location in a blank area of the screen. Lockheed handled this problem by flooding the screen with rows of the character “R.” The user could indicate a specific location by pointing the light pen at one of these characters. Each row of characters took just one refresh cycle so the user hardly noticed what was being displayed. The programmers called this a “character blast.”
CADAM begins to mature
Bradley died in 1968 in a mountain climbing accident and was replaced by Jean Lucas. One technical change that resulted was increased use of APT for NC work. Bradley had not been a fan of APT while Lucas favored using it. Even though CADAM was not a three-dimensional system in the classical sense, it did have strong NC capabilities. Fundamentally, the software used a two-and-a-half dimensional technique not unlike the descriptive geometry techniques used by traditional drafters.
The software facilitated the creation of multiple views of an object without the need to use temporary construction lines. Using this methodology, it was possible for a user to design elements such as a pocket with sloping sides and then program a five-axis milling machine to cut the sides of this pocket using an approach called swarf cutting.
From the initial 360/50, the CADAM group were provided with increasingly powerful hardware. In late 1968, the system which was used for both software development and actual engineering design was upgraded to an IBM 360/91, one of the most powerful computers IBM had built up until that time. It had a 2MB memory (less memory than what is required today for a high resolution digital photograph.) and was capable of two MIPS performance. The computer had drum, disk and tape memory and fairly soon was supporting 12 display terminals. CADAM used 128 KB partitions to support each terminal and frequently, the system was running several different engineering applications simultaneously.
Eight of these terminals were located 4,500 feet away from the computer center in the engineering department. This was done using a high-speed data link provided by IBM that incorporated cables placed in a helium-filled conduit. According to Whitney, performance of the remote terminals was comparable to those located adjacent to the computer.3
One problem this project had to endure was a high rate of personnel turnover. Whitney states that the first 50 man-years of effort spent on CADAM was done by 50 different people. By 1980 there were about 100 programmers associated with the project.4 After the SST was canceled, Lockheed California’s focus shifted to a new commercial wide-body airliner, the L-1011. CADAM was used extensively on this project, from lofting airframe surfaces to detailing 75,000 electrical connectors.
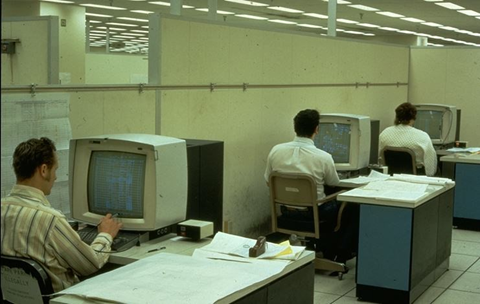
While engineering had access to CADAM terminals during prime shift, other groups could use them during the swing and graveyard shifts. Over a ten-year period, Lockheed designers using CADAM produced over 400,000 electrical diagrams. At one point, they were producing a revised drawing every 15 minutes. Microfilm was used for released drawings while electrostatic plotters were used for check prints. In 1975, Lockheed was using ten 500-foot rolls of paper each day – the equivalent of a mile of check prints. Frank Puhl (president of CADAM, Inc.) once described to me the effectiveness of CADAM on the L-1011 project. “Walk on the plane an look down. The carpet fits while on other aircraft it tends to bunch up. That is because we used CADAM to design the L-1011 carpeting.” A significant shortcoming of CADAM was its lack of any type of macro or user-development language. While the programming staff was able to provided specialized code when requested, this did not provide tools for users to do likewise.
Commercializing CADAM
By 1971, Lockheed Corporation was beset by a host of problems. The L-1011 was not selling well, the Air Force’s C-5A project was suffering huge cost overruns and even the company’s engineering subsidiary was having problems. Eventually the federal government had to step in and provide a $250 million loan to Lockheed to keep it afloat. The company looked around for ways to increase its revenue and top management felt that there was a business opportunity in selling its design software.
Engineering was against this move in that it felt that the software provided them a competitive advantage. They were overruled and in 1972 Lockheed set up a separate organization to continue the development and marketing of the software. This was also the point in time when the software was formally named CADAM.
The first and only head of the CADAM organization within Lockheed was Frank Puhl. He was an accountant who was one of the youngest vice presidents the company had had up until that time. By 1972 he was vice president of finance and administration with several thousand people reporting to him including the company’s computer organization. Supposedly, he was given the choice of running the CADAM project or taking the lead at a different Lockheed company. He chose CADAM.
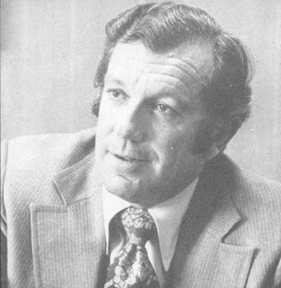
The first three installations outside of Lockheed California in 1974 were IBM Paris (to facilitate selling CADAM in Europe), Lockheed Missile and Space Corporation in Sunnyvale, California and Lockheed Georgia. This was followed the next year by sales to Northrop, Grumman and Dassault Aviation (Avions Marcel Dassault). Unlike most commercial CAD system vendors, Lockheed provided source code to its customers enabling them to make changes to the software.
Customers were soon reporting significant productivity gains using CADAM.
Lockheed Georgia utilized a four-terminal system on a project to produce a stretched C141 aircraft for the Air Force. The original plan envisioned a maximum staff of nearly 70 people working on the project for a period of 18 months. They were able to do the work with a staff of 40 and they did it in 12 months.
CADAM was an expensive solution and many engineering managers were reluctant to make the investment in the mid-1970s. Gradually, the salaries of engineers increased and the cost of the computer hardware per user came down significantly. By 1976 the economics looked much better and usage took off. At Lockheed California, the number of CADAM terminals in use went from about 40 in 1976 to over 220 in 1980.
During the 1970’s the main objectives for CADAM software was to reduce operating costs and increase system reliability. Key elements of CADAM’s system interface code (developed by Dick Bennett and John Saunders) became very useful in developing interactive applications, CATIA at Dassault and NCAD at Northrop.
IBM becomes the primary sales agent for CADAM
IBM fairly quickly realized that CADAM could help it sell lots of large mainframe computers as well as numerous graphics terminals. In 1978 IBM signed a non-exclusive marketing agreement with Lockheed and set up a sales and support staff to promote CADAM running on IBM computer systems. Lockheed also signed similar agreements with Fujitsu in Japan and Perkin-Elmer, a manufacturer of 32-bit minicomputers. The Fujitsu relationship resulted in a meaningful volume of business, particularly in Japan, but the Perkin-Elmer deal never really got off the ground. In 1982, Lockheed established CADAM, Inc. as a separate company to continue the development and marketing of CADAM.
Several CADAM features characterized the early versions of the software. First and foremost, the software was developed to run on IBM mainframe computers using vector refreshed display terminals. At the time, these terminals had very little local computing capability so most graphic manipulations were done by the host computer itself. Since there was little incentive to make the software machine-independent, only about 75 percent of the code was written in FORTRAN. The balance was done in assembly language which resulted in very fast graphic manipulations. This was one way the Lockheed programmers were able to meet the 0.5 second reaction speed mentioned earlier.
At the time CADAM was being developed, most other CAD systems used Tektronix storage tube graphics displays. While they could display a considerable amount of fine resolution data, images could not be selectively erased. The storage tube had very limited capability to display menu-type information. The IBM and compatible vector refresh displays were more expensive than the storage tube devices but could be selectively erased and images could be moved around. They also could rapidly change lists of menu items. The downside was that they could display a limited amount of data before they became overloaded and started to flicker.
IBM and Lockheed were adamant that, overall, the vector refresh devices were preferred over storage tube displays. The selection of displayed entities was very quick because these terminals used a light-pen as the operator input device. With a light-pen the user could directly select entities rather than requiring the computer to indirectly match a coordinate input from a tablet device to the drawing database. CADAM complemented the light-pen with a 32-button programmable function box. Most CADAM users became proficient in using the combination of keyboard, function box, light-pen and on-screen menus to initiate graphic actions.
CADAM was fundamentally a two-and-a-half-dimension system that enabled drafters to create multiple views of complex objects using traditional manual drafting techniques. This enabled users to quickly prepare isometric drawings from these orthographic views. In addition to production drafting, the software was used to automate NC machine tool programming. CADAM could also be used to compute twodimensional section properties.
By 1982, Lockheed began shipping a version of CADAM with three-dimensional capabilities. To produce drawings from the model the user created a two-dimensional projection and then manually added dimensions and notes. The software handled a variety of surface types and could be used to create finite element models although the latter task involved a substantial amount of manual intervention. Automatic meshing was off in the future. Lockheed provided several support modules including a Data Management Module for cataloging data files, a Statistical Data and Report Generator that provided system managers with detailed operating statistics such as system response times, an Accounting Information Modules for recording man-hours spent on specific projects and a Geometry Interface Module that provided an interface to the CADAM database for user developed software.
According to the February 1982 issue of Computer Aided Design Report,
Lockheed had been using the three-dimensional version of CADAM internally for about four years but refused to license it to outside customer in order to protect a perceived competitive advantage. By early 1982, Lockheed had produced 600,000 drawings using CADAM and had about 60,000 of them stored on-line. The system was used to design the F-117 Stealth aircraft (the design of which was shown on a History Channel program) and the Hubble Space telescope. At this time the company was doing about 50 percent of its tool and fixture design work and all its NC programming with CADAM although only about five percent was being done using the software’s three-dimensional capabilities.
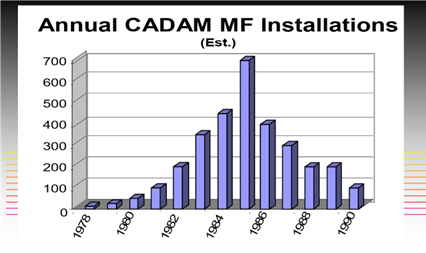
Hardware prices in the 1982 era ranged from about $265,000 for an IBM 4331 Group II computer with two 3251 displays to several million for an IBM 3081 with perhaps 20 or more terminals. A basic CADAM configuration with drafting, data management and hard copy output cost $26,350 plus a monthly fee of $3,200 irrespective of the size of the IBM mainframe it was being run on. As a consequence, adding additional seats only cost the user the price of the display terminal.
As mentioned earlier, IBM obviously was interested in CADAM because it had the potential to help the company sell a large number of expensive mainframe computers and many thousands of 3250 and 5080 graphics terminals. The earlier chart shows the sale of the mainframe version of CADAM over the years.
Most CADAM training and customer support was provided by Lockheed in that IBM had few trained engineers available to support customers. Interestingly, the largest CADAM customer at this time was IBM itself. IBM used a special version of CADAM that included features that the other 190 customers around the world did not have access to. Eventually, some of these features worked their way into the released version of the software. Computer Aided Design Reportconcluded its review with: “CADAM is not state-of-the-art software, but it is a highly reliable system with a long track record of successful use.”[3]
IBM graphics terminals
In order to understand IBM’s mainframe graphics terminals it is necessary to appreciate how these computers were structured in regards to peripheral devices. With the introduction of the System 360 in April 1964, IBM began offering an interface mechanism called a data channel. (There were similar such devices on earlier IBM computers.) This computer module served as the means for transferring data to and from the memory of the computer. To some extent, it was a programmable unit that could be adapted to different input/output devices. Graphic terminals were not connected directly to the data channel. Rather they were interfaced to a display controller that contained the memory and control logic necessary to generate graphic images on the display monitors.
The first generally available IBM display terminal was the 2250 Model I which was introduced with the System 360 in April 1964. The 2250 included a self-contained display and graphics controller. The monitor was a round CRT, 21-inches in diameter, which had a 12-inch square usable area. Resolution was 1024 by 1024. The 2250 was a vector refresh device with display commands stored in the controller’s local memory which was either 4,096 or 8,192 8-bit plus parity words. The basic unit could only display short horizontal, vertical or 45-degree lines. An optional line generator was available which could display lines of any length at any angle. This latter device was required for any meaningful graphics applications.
The major drawback of the 2250 was the flickering which occurred when dense graphic images were displayed. Likewise, there was a finite limit on the amount of detail that could be contained in a given image dictated by the size of the controllers memory although subroutine techniques could be used to extend this capacity. An optional character generator increased the display’s capacity to some extent. User interaction was by means of a light pen and a function keypad. A fully functional 2250 Model I with line generator, keyboard, function keypad and 8KB memory sold for over $100,000 in 1974. The 2250 Model I was followed by the 2250 Model III which was driven by the 2840 Model II controller which had a 16,384 18-bit word memory. A maximum of four 2250 Model III displays could be attached to a 2840. This reduced the cost per seat to about $65,000.[4]
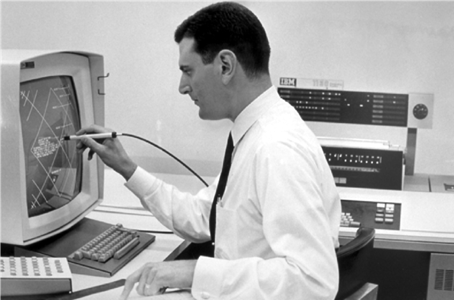
Around 1978, IBM signed an agreement with Sanders Associates of Nashua, New Hampshire to manufacture a replacement for the 2250 called the 3250. The 3250 had more display memory and faster line drawing speed resulting in the ability to display more dense images, perhaps as many as 8,000 individual vectors, flicker free.
IBM introduced its first raster display graphics terminal and display controller, the 5080 and 5085 respectively, in late 1983 with deliveries starting in early 1984. Many graphic functions were now performed by the display system, freeing the host computer of these tasks. The 5080 came in both monochromatic and 256-color versions selling for about $22,000 and $28,000 respectively. This unit maintained IBM’s earlier display products’ square 1024 by 1024 resolution at a time when other display manufacturers were beginning to sell units with a rectangular 1280 by 1024 viewing area.
While the 5080, which used a tablet for user interaction rather than a light-pen, could emulate the older 3250, it had many new capabilities that require new software. It would be some time before CADAM and CATIA were upgraded to use features such as the selective erasing individual entities without updating the entire screen.[6]
In January 1986 IBM introduced new 5085 display controllers replacing the older Model 1. The new units, the Model 1A and the Model 2, had 512KB of display memory and greater local processing capabilities. Prices were reduced to $13,300 for the Model 1A and $18,300 for the Model 2.[7] Subsequently the Model 2A was introduced with a 1.5MB memory.
By 1989 IBM had shipped over 50,000 5080 graphics terminals. As the price of electronic components and semiconductor memory dropped, IBM was able to increase the performance of these units as well as reduce their cost. In early 1989 the 5086 Graphics Processor replace the earlier 5085 with up to twice the three-dimension display performance and a price of just $11,900 compared to a then current price of $14,200 for 5085 Model 2A.[8]
IBM launched a new high-performance, display system, the 6090, in November 1989. It was similar in concept to the 5080 but offered five to ten times the performance at a substantially higher price. The press release introducing this product claimed that it had twice the performance of the Silicon Graphics 4D/210GTX . Ten floating-point graphics processors could transform one million three-dimensional vectors per second or display shaded images at 40 million pixels per second. Shaded images were produced by an optional processor that supported multiple light sources and depth-cueing. The 6090 also handled industry-standard 1280 by 1024 images rather than the 1024 by 1024 images previous IBM raster displays were limited to.
Prior IBM displays required that the host computer handle much of the display generation that could now be handled by the graphics subsystem. From a performance point of view, the 6090 was one of the first commercial devices that could rotate shaded images in real time. There were two 6090 graphics processor models. A basic 6090 system capable of handling two-dimensional 16-color graphics cost $26,650 while a fully loaded system capable of processing complex shaded images with 16 million colors and equipped with 32 MB of memory sold for $72,150. IBM also introduced new channel control units that could handle up to 192 devices each as compared to the prior unit that could handle 32 5080 class displays.
Unlike the 5080, the 6090 could not be used with the RT PC as described below. It was strictly a mainframe device. At the time of introduction the only software that took advantage of the 6090’s new graphics features was SDRC’s CAEDS software. It was estimated that it would take up to a year before CADAM and CATIA would fully take advantage of these features.[9]
Fastdraft and other internally developed CAD systems
Fastdraft was developed by IBM’s Boulder, Colorado Laboratory for internal use under the direction of the facility’s drafting manager, Ron Giese. After using the software internally for about eight years, the company decided to productize it in late 1982 and began shipping it in May 1983. A Fastdraft system consisted of two 3251 monochromatic vector refresh displays, a model 7361 processor (based on the Series 1 minicomputer), a 29MB disk drive, a floppy disk, an HP plotter (relabeled as an IBM device) and drafting software. The price of the system when introduced was $99,890 or about $50,000 per seat. This was at a time when most turnkey systems sold for over $100,000 per seat.
Fastdraft was a fairly basic drafting system. Perhaps its biggest drawback was the small disk drive which severely limited the number of drawings that could be stored online at any one time.[10] Several years later, a revised version of this software was developed by the same lab and sold by Calma as Draftstation. (See Chapter 11). Fastdraft was also sold by Ozalid Corporation, a manufacturer of drawing copier equipment.
In January 1985, IBM reduced the price of a two-station Fastdraft system from $99,000 to $72,900, apparently due to slow sales according to Daratech, Inc.[11] Fastdraft lasted until March 1986 when IBM discontinued it due to slow sales. The product never seemed to have much marketing support within IBM. In reality, Fastdraft probably failed because it was implemented on a minicomputer-based system that was functionally more complete but more expensive than the low cost PCs being used to support competitive packages such as AutoCAD and VersaCAD.
IBM was not about to give up on developing its own CAD package. In August 1986 the company came out with another low cost package, this time for IBM-compatible PCs. Called CADwrite, the software sold for $1,995. Like Fastdraft, it never really took off even though it offered functionality comparable to AutoCAD and VersaCAD at the time. One problem might have been that it only supported IBM’s “Enhanced” and “Professional” graphic displays on the PC. These units had 12-inch displays that were too small for serious drafting. Also, IBM never developed a dealer network that could compete with the one Autodesk had established.[12]
In late 1988, the Boulder group tried once again, this time with IBM CAD, a package that sold for just $995. Computer Aided Design Report liked the softwarebut commented that IBM had much work to do in establishing a distribution network. The newsletter pointed out that this time IBM had made it easier for dealers to add capabilities to the software and perhaps that would make the difference. On the negative side, this package was hard to learn and had little in common with IBM’s mainstream CAD product at the time, CADAM. Like its predecessors, IBM CAD failed to achieve significant market penetration and eventually marketing responsibility was transferred to IBM’s CADAM subsidiary in April 1991.[13]
Alternative CADAM workstations and software solutions
Throughout the 1970s and 1980s, manufacturers of various peripheral devices such as disk drives, tape drives and printers attempted to capitalize on IBM market dominance by marketing devices that could plug directly into IBM mainframe computers. Called Plug Compatible Manufacturers or PCMs, they were able to undercut IBM’s prices by minimizing research and development expenses and operating with lower overhead. One specialty subset of this market was the manufacture of plug compatible graphics terminals. Early leaders in this space were Adage, Vector General and Spectragraphics.
Until it eventually introduced the 5080 color raster display in 1983, customers using IBM graphics terminals were limited to using monochromatic vector-driven displays. Although they had sharp resolution, they would begin to flicker when users tried to display complex drawings. By the early 1980s, color raster technology was becoming more readily available. In June 1982, San Diego-based Spectragraphics began shipping monochromatic and color raster display units called System 1250.
Using typical IBM system architecture, the 1250 consisted of three components, a channel controller that connected to a standard IBM data channel, a display controller and the display itself. Each channel controller supported two display controllers and each display controller supported up to four displays. The 1250 displays had 1024 by 1024 resolution and the color version supported 16 colors.
These units were also capable of functioning remotely. The first unit was somewhat expensive because of all the modules required but average prices went down as more displays were added. A single monochromatic display cost $49,850 while a similar color unit ranged from $79,000 to 89,000 depending upon the amount of memory installed. With the maximum number of displays, costs could be as low as $21,000 per terminal.[14] Spectragraphics subsequently introduced a 16-color raster terminal, the DS 1080, which emulated the 5080 and was priced at $17,900.
A new company, CGX Corporation, announced both vector and raster IBMcompatible displays in October 1982. CGX was founded by two brothers, Ken and John Leavitt in Acton, Massachusetts. John Leavitt had been manager of software development at Adage.[15] The company was able to reduce the cost of its systems by combining the display controller with the display itself. This reduced the cost for small configurations of just one or two terminals. CGX’s channel control unit cost $30,000 and supported 16 displays which individually cost $30,000 for monochromatic and $40,000 for color raster. [16]
More than just plug-compatible displays, Vector General announced a complete CADAM system including software and 12 displays for $540,000.[17] Once IBM announced its aggressively priced 5080 color raster display in late 1983, the plugcompatible vendors started coming under increased pricing pressure. Spectragraphics, as an example, reduced the price of its Model 1500 color display terminal from $42,000 to just $22,000 in December 1983.[18]
Adage introduced its first color raster display which emulated the IBM 3250 in August 1983. The 19-inch 4250 had 1280 by 1024 resolution and sold for about $43,000.[19] In January 1985, Adage introduced the Adage Model 6080 raster display which had specifications nearly identical to the IBM 5080. Prices started at $18,000 for a monochromatic unit and $22,000 for a color unit.
Perhaps the most interesting business developing involving display terminals for CADAM and CATIA occurred in September 1986 when Lockheed acquired Sanders Associates, the manufacturer of IBM’s 5080 terminals. Sanders also owned California Computer Products (CalComp) which sold a product line of CAD systems as well as the plotters for which it was best known.
CalComp had expanded into the disk drive business in the late 1960s, a move that proved to be financially disastrous. That business was sold piecemeal to several companies including Xerox in 1979 and the rest of the company including the plotter and CAD activities was acquired by Sanders towards the end of 1979. While there was some early talk of merging Lockheed’s CADAM, Inc. with CalComp after the Sanders acquisition, it never happened.
The most serious clone of CADAM was produced by Adra Systems. Adage was an early financial backer of Adra Systems and in July 1984 Adage introduced the CADstation 2/50 which had been developed by Adra and used command menus and graphical construction techniques similar to CADAM. It sold for $22,000. In January 1986 CADAM, Inc. filed suit against Adage and Adra claiming copyright infringement.
Over time, Adra moved away from proprietary hardware and began supporting its CADAM-like software, now known as Cadra, on a variety of UNIX workstations and IBM-compatible PCs. By 1990, numerous companies such as Sikorsky Aircraft were using Cadra as an alternative to the more expensive CADAM for two-dimensional drafting.[20] As the 1990s progressed, the Cadra become less of a direct clone of CADAM and added features and capabilities conceived by Adra’s own developers.
By 1996 there were perhaps 17,000 Cadra seats in use at somewhat over 1,500 customer sites. This was probably the highpoint for the software as the company began to focus on its Matrix PDM software to the extent that the company’s name was eventually changed to MatrixOne. The Cadra software was sold in1998 to SofTech which still markets the software. See Chapter 21.
In the late 1980s, the 5080 terminal business went through a period of consolidation. Adage acquired CGX (Jim Norrod, previously vice president of sales at Auto-trol Technology was president of CGX at the time[21]) in 1987 even as it continued to lose money. In August 1988 Adage sold its service business to National Computer Systems (NCS), a vendor of optical scanning systems used by educational institutions. In December 1988, NCS also acquired the service business of VG Systems (formerly Vector General) then in late 1989 NCS acquired the balance of Adage’s and VG Systems’ graphics business. This basically left two companies in the 5080-compatible business, NCS and Spectragraphics. The world-wide market for 5080-type terminals was about 16,000 units per year and IBM probably had an 80 percent market share.
The days’ of graphic terminals connected to mainframes were numbered as the CAD industry switched to networked workstations. Spectragraphics was active in developing hardware and software that enabled systems from Digital, Hewlett-Packard, SGI, Apollo and even IBM to function as 5080 terminals. Although useful in specialized circumstances, this never became a large market. Neither NCS nor Spectragraphics attempted to emulate IBM’s new 6090 terminals. NCS eventually disappeared while Spectragraphics managed to stay around. After an aborted attempt to develop workgroup collaboration software, Spectragraphics became a contract electronics manufacturer.[22]
IBM enters the workstation market
By 1985, it was increasingly apparent that engineering workstations from Apollo,
Sun Microsystems, Digital and others were quickly becoming the preferred platform for CAD applications and were going to be serious competition for minicomputers and mainframes in this market space. IBM had long been rumored to be developing a competitive product and eventually introduced the RT-PC in January 1986.
The RT-PC used a new microprocessor architecture called RISC(Reduced Instruction Set Computer) that significantly reduced the number of machine language instructions the computer supported. The IBM RISC processor supported 118 instructions compared to the 304 supported by Digital’s VAX systems. Each RISC instruction was less complex than traditional instructions but could typically be executed much faster. While it might take more instructions to accomplish a given task, the expectation was that the total time would be less. This was a debate that would go on for the next several decades. (The RT stood for Reduced instruction set computer Technology.)
The RT processor was a true 32-bit device with a 32-bit memory bus and 32-bit registers. Virtual memory (40-bit) was managed by a program called the Virtual Resource Manager providing access to a potential terabyte of data. There were four RT models announced at introduction ranging in price from $11,700 to $19,510. In addition customers had to pay an additional $3,500 for AIX (Advanced Interactive Executive), IBM’s implementation of AT&T’s UNIX operating system.
Half a dozen graphics options were available for use with the RT but only one, the existing 5080, was really applicable for CAD applications. A floating-point co-processor was also available for $1,995. See Figure 13.6. By the time it was all added up, A RT-PC configured for CAD applications (a 6150 Model A25 with floating point processor, 4MB of memory, AIX and a 5080 display subsystem with a 19-inch color monitor) cost about $45,000 without any application software. Although the RT-PC had about twice the performance of a PC AT, it was priced far more than twice as much.
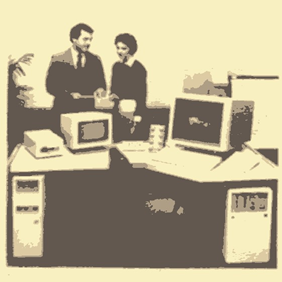
The major problem for the RT was that it was slow compared to competitive systems. In one comparison in Computer Aided Design Report, Digital’s Microvax II was
twice as fast and only cost 38 percent more.[23] Except for the 5080, RT graphics were fairly weak compared to competitive products. While the RT was scheduled for March 1986 delivery, some capabilities were not expected until September. Meanwhile, companies such as Sun and Apollo were expected to introduce new higher performance systems at probably lower prices. According to Dave Burdick who was with Dataquest at the time; “It’s a good start for IBM, but they’ve got a long way to go.”[24]
RT-PC sales started off slowly due to a lack of application software as well as price and performance problems. In September 1986 IBM dropped prices by 20 to 32 percent and beefed up the machine’s performance. Maximum memory was increased to 8MB, bigger and faster, although quite expensive, disk drives were added to the product line and a new floating-point accelerator that was three times faster than the initial unit was made available. By comparison, an Apollo DN3000 offered 30 percent more performance at 20 percent lower cost.[25]
A year later, in February 1987, IBM announced a faster version of the RT-PC. It used a 10 megahertz processor, either a Motorola 68881 math coprocessor or an optional floating point card, a compact 5080 graphics adapter called the Megapel that was less expensive than the previous 5080 adapter and support for new graphics system software. The new RT was about a match for the Apollo DN3000 in both price and performance. The product continued to struggle, however, and software vendors started to give up on it. The major problem was IBM would move a step ahead in performance and the competition would take a much bigger jump. In January 1988, Autodesk announced that AutoCAD would no longer be supported on this platform.
Although IBM was trying to develop a viable workstation product line and CADAM had been ported to UNIX workstations, IBM was still committed to “big iron” mainframes. As late as November 1989, the company stated that mainframes would be a key platform for at least another decade, especially in situations where they were needed for controlling large libraries of engineering data.[26]
RS/6000 puts new life in IBM’s workstation operation
The RT never gained much market share and it was not until IBM introduced its successor, the RS/6000, on February 15, 1990 that IBM offered a competitive product in this space. When IBM wants to get serious about a particular market it can get very serious and it apparently decided at some point to get serious about the UNIX workstation market. The RS/6000, when introduced, consisted of a number of graphic workstations and servers built around a nine-chip processor running at 20 to 30 MHz. The RS/6000 was not just an improved RT-PC, it was a totally new design with a new instruction set, a new memory bus design, a new I/O bus and new graphics adapters. Although it was still classified as a RISC design, the processor supported 184 different instructions compared to the 118 in the RT-PC.
The product line incorporated a number of monochromatic and color display processors with 1280 by 1024 resolution. These were a match for anything then being sold by competitors. Typical graphic workstations ranged in price from $19,300 for a RS/6000-320 to $104,705 for a RS/6000-730. Overall, the RS/6000 leapfrogged the performance of competitive products offered at comparable prices. In November 1990 the company introduced the model 550 which was rated at 23 MFLOPS and priced at $130,000 with no graphics. It was apparently intended to be a compute server.
Software-wise, IBM used the introduction of the RS/6000 product line to commit to industry standard software. It adopted MIT’s X-Windows graphical user interface environment as well as graPHIGS and SGI’s Graphics Language (GL) for application development. It was later in 1990 before either IBM applications such as CADAM and CATIA or third party applications such as Pro/ENGINEER, PDA PATRAN or MCS Anvil 5000 were available on this platform.
The version of CATIA introduced to run on the RS/6000 in December 1990 required an IBM 5086 graphics terminal in order to function – costly, awkward and with less than impressive performance. The result was that CATIA shaded images took several minutes to generate and were not particularly smooth. The problem was that CATIA had been implemented using low-level graphic primitives in order to achieve good 5080series performance. Rewriting this software using graPHIGS was taking more time than customers who wanted to switch to the RS/6000 were happy with. A CATIA system, including a RS/6000 and 5086 terminal, cost over $90,000, probably twice as much as Pro/ENGINEER on a Sun SPARCstation. One result of this was that IBM continued to sell mainframe based CATIA systems for some time after the RS/6000 was introduced. A new line of graphic interfaces for the RS/6000 were introduced in the fall of 1991. The Gt3, Gt4 and Gt4x offered two-dimensional and three-dimensional capabilities at prices that ranged from $3,500 to $17,000. In 1992 IBM renamed this activity the Advanced Workstations and Systems Division (AWSD). In the fall of that year the company introduced a new high-end workstation, the POWERstation 580 which for a period of time was the fastest UNIX workstation available. It was one of the first workstations that could support 1GB of main memory. The 580s were fairly expensive units starting at nearly $70,000 for the monochromatic model.
IBM was very blunt that it intended to increase its share of the UNIX workstation market from about two percent in 1989 to 30 percent of a much larger market by 1993.[27] By early 1993, the company was offering RS/6000 systems ranging from less than $4,000 to supercomputers capable of 8 GFLOPS performance. Fourteen years later, RS/6000 servers are still a part of IBM’s product line although graphic workstations have been superceded by high performance PCs.
IBM supports the PowerPC as an alternative to Intel microprocessors
In the early 1990s, Intel was taking on an increasingly dominating role as the vendor of choice for PC microprocessors. In late 1991, IBM agreed to work with Apple Computer and Motorola in the development of a new microprocessor called the PowerPC. The development operation, called Somerset, was based in Austin, Texas. The PowerPC used the RISC architecture of IBM’s Power processor used in the RS/6000 product line and Motorola’s 88000 bus architecture.
The three companies were also working on developing a new object-oriented operating system called Taligent and new multimedia technology called Kaleida. Overall, the objective seemed to be to develop PC product lines at Apple and IBM that would not be dependent on either Intel or Microsoft technology. The PowerPC never had any significant impact on the PC industry although it was used extensively by Apple.
IBM tried to market PowerPC-based PCs but soon gave it up as a hopeless cause. Eventually the PowerPC was relegated to powering RS/6000 workstations and servers. Even before the PowerPC began shipping IBM was already working on a next generation version. Referred to as the Power Plus, it was expected to double the number of instructions executed each clock cycle. Taligent never got off the ground nor did Kaleida.
The initial PowerPC microprocessor was the 601. It had about the same performance as a 66-MHz Pentium chip but cost roughly half as much. It was also physically smaller and generated less heat. In the fall of 1993 IBM introduced its first workstations based on the PowerPC. Called the POWERstation 25T it started at $9,395 for a unit with a 17-inch color monitor. Overall, performance was comparable to similar systems sold by Hewlett-Packard and Sun Microsystems.
IBM did not give up on its own processor architecture just yet. Shortly after the first POWERstation was introduced, IBM announced a new high-performance POWER2 processor (actually a set of eight chips rather than a single monolithic microprocessor.) and several servers using it. These were given the POWERserver name.[28] Eventually, IBM would switch much of the RS/6000 product line to PowerPC microprocessors. Other than for Apple PCs, this microprocessor never caught on in the PC market space and IBM eventually dropped support of PCs using the PowerPC chip.
In mid-1994 the PowerPC and POWER2 systems were split between groups within IBM targeting end users and large systems buyers. Low cost POWERstations were lumped in with PC products as part of the IBM Personal Computer Company while the Advanced Workstation and Systems Division was renamed the not very creative RISC System/6000 Division and imbedded in the Large Systems Division. Shortly thereafter IBM announced a number of new workstations and servers using both the PowerPC and the POWER2 processors. In addition, the company announced that it would sell high-end Evans & Sutherland Freedom Series graphics for automotive styling and industrial design. These latter systems sold for over $100,000 each.
As time progressed, IBM introduced additional POWER2-based workstations and servers. In early 1995, a 67-MHz POWER2 processor was launched capable of 130 SPECint92 and 267 SPECfp92 performance. The floating point performance was particularly impressive considering the growing use of complex solids models. A RS/6000 Model 3CT with 64MB of main memory, a 1GB disk, a GXT150M graphics accelerator and a 17-inch color display had a list price of $38,795.
Professional CADAM introduced
Until early 1986, CADAM had strictly been a mainframe-based application running on large IBM computers. The introduction of the PC-RT provided CADAM, Inc. with the opportunity to implement the software on workstation class machines, especially those running some version of UNIX. Professional CADAM was launched in parallel with the introduction of the PC-RT. Priced at $16,000 per copy for the software, Professional CADAM was definitely not expected to be competition for Autodesk’s AutoCAD. The software only worked with the version of the PC-RT equipped with a 5080 display. Total system prices ranged from $50,000 for a system with a 15-inch monochromatic display to $67,000 for a system with a top-of-the-line 19-inch color display.
Professional CADAM was not simply a port of the mainframe CADAM software to the PC-RT platform. Much of the software was actually rewritten for this new offering. The data structure of the two programs were different and a translation program was required to move data files from one machine type to the other. Professional CADAM actually had several significant enhancements compared to the original CADAM software.
- It could handle unlimited size models while CADAM models were limited to about 20,000 words (about 120KB).
- Graphic entities were double precision compared to the single precision format used in CADAM.
- Professional CADAM supported an unlimited number of views compared to the 64 in CADAM.
A system manager could set Professional CADAM to limit model size and utilize single precision so that models would be compatible with mainframe CADAM. While Professional CADAM had the enhancements described above compared to the mainframe version of the software, it also had several limitations. The initial version Professional CADAM was strictly a two-dimensional design and drafting solution with no surface geometry capabilities. There also were no NC or analysis modules available. According to Computer Aided Design Report the pre-release version of Professional CADAM it evaluated was slow, taking 30 seconds to zoom into a 50,000word drawing file. Delivery was not expected until September 1986.[29]
CADAM, Inc. launches MICRO CADAM
In 1984 Lockheed established a joint venture in Japan with Kawasaki Heavy Industries called CADAM Systems Company (CSC). The initial purpose of this joint venture was the marketing and support of CADAM in Japan. CSC realized that there was a need for a low cost version of CADAM and began to develop MICRO CADAM on the PS/5500 personal computer which IBM sold in Japan and was quite different from the PCs sold in the United States and elsewhere. This software was launched in Japan in 1985. A PC/AT version for sale in the United States and elsewhere around the world was introduced the following year. The PC/AT version was typically referred to as the International version.
Although the International version used many of the same menu commands as the mainframe version of CADAM, it was essentially new software. The International version of MICRO CADAM was designed to work on PC/ATs equipped with either IBM’s “Professional”, “Enhanced” or “3270 PC/GX” displays. Popular display systems such as the graphics cards produced by Hercules were not supported. The required configuration included a hard disk drive, a math co-processor and 640KB of memory as well as a function box similar to that used with CADAM.
MICRO CADAM software plus a special purpose function box was priced at $8,000. Initially it was stated that this package would be sold directly by CADAM, Inc.
Shortly thereafter, IBM announced that it would also sell MICRO CADAM.[30] Sales took off rather slowly due to the high price, somewhat poor performance and the limited range of hardware supported. In what was probably a major mistake, IBM decided that MICRO CADAM would only be sold by its direct sales staff and not by its PC dealers, many of whom were probably already selling AutoCAD.
At about the same time CSC introduced MICRO CADAM, McDonnell Douglas introduced Crossroads CAD and Intergraph acquired a 50 percent interest in CNR Research, the developer of an IGDS knockoff called C-CAD. With three major firms jumping into the PC CAD market, Computer Aided Design Report thought AutoCAD’s days were numbered. “Back when AutoCAD was the only game on the PC, we could understand why people bought it. But now that most of the big guys are offering “starter kits” for prices near AutoCAD’s there seems little need for AutoCAD anymore.” Steve Wolf was often a very insightful prognosticator during his many years of editing his newsletter, but this was not one of those moments.
The summer of 1986 also saw CADAM, Inc. run into some financial problems for the first time as sales during the first five months of the year failed to grow as fast as expected. As a result, the company laid off 53 employees even though it was still hiring specialist such as programmers familiar with solids modeling.
MICRO CADAM was slow to take off, most likely because of its $8,000 price tag. To accelerate penetration of the PC CAD market, CADAM, Inc. introduced a new lower-priced package called Cornerstone. At $2,995 it was competitive with packages such as AutoCAD, Computervision’s Microdraft and MCS’ Anvil 100MD. Cornerstone did away with the special function box used with MICRO CADAM and mainframe CADAM. Also, data files could not be exchanged with the more expensive versions of CADAM. Obviously, the company was torn between establishing a position in the rapidly expanding PC CAD market and protecting its higher priced products.
In 1988, Cornerstone became MICRO CADAM Plus priced at $3,995. MICRO CADAM Plus used Pharlap memory extension software to get around the 640KB limitation of Microsoft’s DOS operating system. It took nearly 18 months to get a relatively bug-free version of the software.[31] A low cost data management option, MC*EDM was launched in mid-1989 at just $295 per seat.
IBM becomes major player in CAD industry
Between 1979 and 1985 the CAD industry grew from $340 million to $3.5 billion according to Daratech.35 During this six year period, IBM’s share went from 8.8 percent to an industry leading 21.3 percent. The latter number meant that IBM’s CAD-related sales totaled nearly $750 million in 1985. What the reader needs to clearly keep in mind is that during those years, the revenue numbers reported by market research firms such as Daratech included computer hardware as well as software whereas today’s numbers mostly reflect just software and services. When IBM sold a $1.2 million CAD system, it probably reflected $1 million for a 4381 computer and 16 graphic terminals and just $200,000 for the CADAM software this system supported.[32] This relationship between hardware and software was comparable to what other turnkey systems vendors charged.
There was a serious flaw, however, in how the market research companies reported industry statistics. Basically, companies reported their revenue data to companies such as Daratech. For those companies that were publicly traded such as Computervision and Auto-trol Technology it was easy to compare the numbers provided to market research firms with the firms’ published financial reports. Since virtually all these companies’ revenue was related to the CAD industry, the numbers were quite accurate.
For computer manufacturers such as IBM, Prime Computer and Control Data the situation was quite different in two regards. Because the CAD system business was a minor part of their overall revenue, it was not possible to confirm the industry numbers they reported with public financial reports and they had many reasons to see the CADrelated numbers as large as possible. The other problem was when the sold a large computer system, perhaps for $1 million or more, they often reported the entire sale as CAD-related even if only a small portion of the computer was being used to run CAD software. Many industry insiders viewed the numbers reported by the computer manufacturers with some skepticism.
By early 1986 the CAD industry was undergoing several structural changes. As reported in an excellent Computer Aided Design Report article on IBM in April 1986 Charles Foundyller, the president of Daratech is quoted as stating that: “The rise of IBM is part of a larger trend benefiting general-purpose computer builders at the expense of turnkey systems.” As the use of CAD increased, corporate information technology managers began to exert their influence over purchase decisions. Typically, they were comfortable dealing with IBM and if that company offered a reasonable solution that satisfied the basic needs of the engineering department they would push for an IBM decision. In many situations top engineering managers were happy to have IT personnel take over the responsibility for purchasing and maintaining these systems. That way, they could concentrate on their primary mission, designing products. Foundyller went on to state that “The end of the turnkey CAD/CAM business is now in sight.”[33]
IBM in the mid-1980s was a company struggling to meet the challenges of a rapidly changing computer industry. It was not unusual for the company to have several different divisions develop similar products on the expectation that the best product would eventually win out. Since IBM was such as major player in the computer industry, it often ended up being its own competitor. As an example, two groups were responsible for promoting the sale of CAD systems, an Engineering/Scientific Market Development group under Robert Tiel and a CAD/CAM Marketing Support group under Dick Burkley and then Mike Corse. Burkley subsequently went to work for Auto-trol Technology.
E/S MD was the organization that identified the software needed to compete in this market and managed the relationship with developers such as Lockheed’s CADAM, Inc. CAD/CAM Marketing Support provided the technical field support for CAD sales. While these two groups were pushing the sale of IBM CAD systems another organization, the National Distribution Division, was encouraging other companies to offer IBM systems as part of their CAD offering. That is how the company ended up with vendors such as McAuto and Computervision offering IBM computers running their software in competition with IBM selling the same computers running CADAM or CATIA.
At this point in time, IBM had three computer product lines applicable to engineering and scientific users.
- Mainframe “host” computers such as the 3090 and 4300 series which ran IBM proprietary operating systems.
- Stand-alone 32-bit computers such as the recently announced RT/ PC which ran AIX, IBM’s implementation of UNIX. The RT was IBM’s first implementation of RISC technology. For graphics applications the RT was equipped with IBM’s 5080 graphics terminal.
- Personal computers including the PC/AT which ran Microsoft’s DOS operating system.
While each of these systems was manufactured by a different IBM division, E/S MD had as an objective to create software, what it called “user services,” that would hide operating system functions behind a common user interface. Tasks such as finding and copying files would be more consistent and users would be able to exchange files via a common network, especially between UNIX systems and IBM’s own SNA (System Network Architecture) networks. The latter capability was handled by DCS (Data Communication Services). IBM also launched a program called GDQF (Graphical Display Query Facility) for displaying graphical files on dumb terminals.
Around this same time, IBM began promoting the use of PHIGS (Programmers Hierarchical Interactive Graphics Standard) as a cross-platform device-independent graphics standard for three-dimensional applications. Although PHIGS was a wellrespected standard and is still offered by IBM on several systems, it never became the vehicle for platform independent applications its proponents expected.
Graphics terminals, which were such a key element of CAD systems were designed and produced by another group, Engineering Systems Products. The company was still offering the 3250 vector refresh terminal as well as the newer 5080 raster terminals. Both monochromatic and color versions of the latter were being marketed. Bob Blumberg, the president of Spectragraphics, estimated that IBM sold between 75 and 80 percent of the 5080-compatible displays while the plug-compatible vendors sold the balance. Where relatively small quantities of display terminals were required, the nonIBM vendors offered comparable performance at lower prices. When a large customer was involved, IBM’s quantity discounts often offset these price advantages.[34]
The bulk of IBM’s CAD business involved the sale of CADAM although Dassault’s CATIA was starting to take on increased importance. As described in Chapter 17, IBM continued to sell SDRC’s I-DEAS software as CAEDS. In late 1993, IBM began to sell the SDRC software under the I-DEAS name, recognizing the I-DEAS Master Series had brand recognition of its own that IBM needed to take advantage of. Compared to its other software products in this area, IBM never sold a substantial volume of SDRC software and one wonders if the marketing resources would have been better spent promoting CADAM and CATIA more aggressively.
By this point in time, it was already apparent that CADAM, Inc. and Dassault Systemes were on a collision course. CADAM was being extended to include threedimension surfaces while drafting capabilities were being added to CATIA.
CATIA provides alternative to CADAM
Dassault Aviation of France first became seriously interested in applying computer technology to aircraft design in the late 1960s. One of its first efforts using interactive graphics was an internally developed application for smoothing graph data. In 1974, the company was one of the first licensees of Lockheed’s CADAM software which it used for two-dimensional drafting work. Dassault recognized fairly early that there would be significant benefits in applying interactive graphics to manufacturing applications. The first such internally developed project was called the DRAPO (Définition et Réalisation d’Avions Par Ordinateur) program. It entered industrial service at the end of 1975.
In 1978, Jean Cabrière, Dassault Aviation’s managing director, called for the development of a three- dimensional design tool. A new DRAPO system program, called CATI (Conception Assistée Tridimensionnelle Interactive) was developed by the company’s CAD Department. It was initially used to machine complex parts such as wind tunnel models, working from outline drawings defined with DRAPO. With CATI it was possible to design and machine a first wind tunnel wing in four weeks instead of the six months it previously took. In 1981, CATI was renamed CATIA (Conception Assistée Tridimensionnelle Inter Active or Computer-Aided Three-Dimensional Interactive Application in English). This computer program made it possible reduce cycle times, improve quality and optimize production efficiencies.
Some of the underlying work on what eventually became CATIA started in 1960 at Renault where the mathematician Pierre Bezier developed a series of mathematical techniques for describing the curved surfaces of automobile bodies. Bezier’s work led to the eventual development of the widely used Bezier Curves for describing mathematical surfaces. In 1976, Dassault Aviation acquired the technology, then known as UNISURF, from Renault for in-house use to complement its CADAM system.
Over the next several years, Dassault programmers under the direction of Francis Bernard expanded this software into a three-dimensional modeler that worked with the more limited CADAM software. The desire was to be able to create surfaces that could then be machined with a minimum of operator intervention. This was especially important in the aircraft industry for rapidly making wind tunnel models.
Bernard subsequently convinced the aircraft manufacturer to commercialize CATIA and to establish a separate subsidiary, Dassault Systemes, on June 5, 1981 to further develop and market this software. Although Dassault Systemes has sold some CATIA directly, the bulk of the sales activity for this product has been handled by IBM since 1982.
Initially, IBM was comfortable handling both CADAM and CATIA since they incorporated different capabilities. CATIA was intended to be used for complex modeling applications and the machining of surface geometry. The production of engineering drawings was still done with CADAM. As described earlier, the typical IBM mainframe could handle a large number of CADAM terminals. That was not the case with CATIA. In the early 1980s CATIA required about four times the computational power of CADAM. CATIA also required an alphanumeric display in addition to the graphics display used for CADAM.[35]
In the 1984 time frame, a major debate took place within IBM over whether to promote the three-dimensional version of CADAM or to switch the company’s marketing focus and put its resources behind the newer CATIA software. Eventually, CATIA won out, but not immediately. It was well known that CADAM, Inc. had developed a threedimensional version of CADAM in the early 1980s but it was late 1984 before IBM agreed to market the software as CADAM Version 20.0. Meanwhile, Dassault was adding drafting capabilities to CATIA in Version 2 Release 1.0.
By 1987, the two packages were in direct competition with each other. The July 1987 issue of Computer Aided Design Report led off an excellent review of CATIA with “There’s a major battle looming in the high priced CAD/CAM world between Lockheed Corporation’s CADAM subsidiary and Dassault Systems, a division of Dassault Aircraft of France. The prize will be the leadership of IBM’s CAD/CAM software line.”[36] The surprise was how quickly Dassault became the dominating vendor in this market space, eventually swallowing up CADAM and spitting out the pieces like watermelon seeds.
By 1987, CATIA’s surface modeling capabilities were as good as those of any other CAD vendor. As an example, the software could blend fillets of unequal radius, a task not many competitive products could handle. All data was stored in a double precision floating point format. CATIA also incorporated a faceted solid modeler. Once the precision of the facets were defined, they could not be changed. Competitive modelers such as Matra Datavision’s Euclid allowed designers to use a coarse model during conceptual design and switch to smaller facets for visual representation or NC tape preparation. With this limitation, CATIA could bring a large IBM mainframe to its knees with just a few users working on fairly small models if they defined fine resolution facets.[37]
Typically, CATIA users built fairly coarse models for design studies. When they transitioned to detailed design, these solid models were converted to surface defined models using an operator-directed interactive procedure. It was time-consuming and rather awkward, but it worked. CATIA also provided excellent NC software capable of generating tool paths across multiple surfaces in a single pass. Unlike most other CAM packages, CATIA NC generated an APT source file that was then processed, typically by a mainframe APT program, to generate actual tooling commands. Other applications included electrical schematic drafting, robotic programming and piping design. The latter was not a process plant design package but it did lay the groundwork for moving in that direction.
Although there were far more CADAM installations than CATIA installations, the later was growing rapidly while new CADAM sales seemed to be stalled. New CATIA customers were either replacing legacy turnkey systems or were CADAM users who wanted more advanced modeling capabilities. Perhaps the most significant convert in the 1987 time frame was Boeing Commercial Airplane Company which switched from VAX-based Intergraph systems to mainframe CATIA to support development of the 7J7 aircraft, what eventually became known as the Boeing 777.[38]
By the end of 1988, IBM had installed 1,100 mainframe CATIA systems worldwide. Dassault introduced a RT-PC version of CATIA that was priced around $60,000 per seat. It supposedly used the same source code as the mainframe version of CATIA. This never became a popular product.
Lockheed offers CADAM on non-IBM platforms
Since it first started selling CADAM through the IBM sales force, CADAM, Inc.
had only supported IBM computer systems, at least in public. Beginning around 1985, the company’s software developers began experimenting with a UNIX version of CADAM and the company had occasionally shown this software running on Apollo workstations to potential prospects. This was not a particularly well kept secret.
At the 1988 AUTOFACT conference, CADAM, Inc. had its own booth and demonstrated Professional CADAM on a SPARC-based Sun 4 workstation. Then in February 1989, the company announced that it would begin selling Professional CADAM unbundled on both Sun and Apollo workstations for $10,000 per copy. In addition, a program for accessing the CADAM database, CADAM Access, was also available for $2,000 per copy. The company’s PRANCE electronic design software was also offered on these workstations as well as CADEX, a schematic drafting and wire list generation program.[39]
Once IBM acquired CADAM, Inc. as described below, the company announced that it would now longer support Sun and Hewlett-Packard (new owner of Apollo) UNIX workstations although this did not happen immediately. The reason eventually given was that since CADAM, Inc. was an IBM company it could no longer sign non-disclosure agreements with other computer manufacturers and that this prevented them from supporting new systems until they were fully announced products.[40]
This was not absolute, however. EDS, which had tentatively selected CADAM along with Unigraphics as the preferred CAD solutions for General Motor’s C4 program, announced in May 1990 that it would continue to sell CADAM on Sun and HP platforms both within and outside GM.45
Expanding CADAM’s PC product line with P-CAD
In February 1989, CADAM, Inc. acquired Personal CAD Systems, a developer of electronic design software running on IBM-compatible PCs. P-CAD had been founded by Doug Stone who continued as president after the acquisition. About 11,000 copies of PCAD’s Master Designer II software, a printed circuit board design package, had been sold at the time of the acquisition. In addition to expanding its market reach more into the electronics arena, CADAM was also interested in the fact that P-CAD had developed a domestic dealer network. Up to this point, CADAM, Inc. had been relatively successful in selling MICRO CADAM through IBM’s sales force and in Japan through CADAM Systems Company. Sales in the United States through independent dealers had been disappointing, however.[41]
In 1988, P-CAD agreed to sell an automatic PCB router from Router Solutions called Superoute under the brand label of “Rip-up-Router.” By mid -1989, the relationship between the two companies had deteriorated, primarily because P-CAD had failed to meet its contractual obligation to sell a specific volume of Superoute. Lawsuits soon followed. After its acquisition by CADAM, Inc. P-CAD switched to an internally developed router called “Rip-N-Route.”
CADAM developments in the late 1980s
CADAM, Inc. introduced its Interactive Solid Design module in 1987. Called “Interactive Solid Design” or ISD, this software was derived from MAGI’s Synthavision package and supported ray traced shaded models which were of high quality but consumed considerable amounts of computing resources. While ISD was a separate program, it was capable of exchanging data with the two-dimensional CADAM software.
Assemblies were created by overlaying individual part models. These assembly definitions could then be saved, something CATIA was not yet able to do. Although CADAM introduced three-dimensional geometry with Release 20 in 1985, it took the company until late 1987 to introduce surface NC milling. This latter package was called NC II and it produced a cutter location file rather than the APT source that CATIA generated.[42]
Lockheed decides to sell CADAM, Inc.
Lockheed always seemed to be on the edge of financial disaster. In 1971 it took a federal government $250 million bailout to keep the company afloat. In 1982 the company cancelled the L-1011 wide-body commercial aircraft and took a $300 million write-off leaving it perilously close to bankruptcy once again. By early 1989 the company was grappling with a hostile takeover bid by Harold Simmons, often described as a corporate raider.
As one step in turning itself into a leaner and more financially solvent company, Lockheed announced publicly in April 1989 that it was interested in sell both its CADAM and CalComp subsidiaries. CADAM was no longer a strategic tool at Lockheed in that the company was now using CATIA and SDRC software for its advanced projects. By fall, rumors were that IBM, Fujitsu and SDRC along with a group of venture capitalists were looking at buying CADAM, Inc.
Fujitsu was considered a prime candidate to acquire CADAM, Inc. since it built IBM-compatible mainframes and CADAM was selling very well in Japan. Everyone perceived this to be a threat to IBM’s position in this market and on November 9, 1989, IBM announced that it intended to acquire CADAM, Inc. from Lockheed. The plan was to have CADAM, Inc. operate as a wholly owned IBM subsidiary with its employees CADAM, Inc. employees rather than IBM employees. Frank Puhl, the president of CADAM, Inc. retained this position with IBM, reporting to Edward Kfoury, IBM vice president of industrial sector marketing.
IBM paid approximately $100 million for CADAM, Inc., about $80 million in cash and the balance in “non-cash” consideration. This was about one time the company’s revenue. Considering that a large part of IBM’s $1.35 billion of total system revenue from the CAD market came from selling or leasing hardware in support of CADAM, this was probably a wise investment.
What it did do, however, was confuse the issue over what would be the preferred CAD system of the future – CADAM or CATIA, especially as user requirements were increasingly shifting to three-dimensional modeling versus two-dimensional drafting. In this regard, Dassault was clearly ahead of CADAM, Inc. in the development of advanced software.
In late 1991, Puhl and six other CADAM, Inc. executives filed suit against Lockheed claiming that they were not compensated as expected when Lockheed sold the company to IBM. They believed they should have been paid bonuses based upon the total amount IBM paid for the company, not just the cash portion.
IBM had been subtly favoring CATIA for several years and it was not clear that owning CADAM outright would change this stance since the bottom line was that IBM wanted to sell as much hardware as possible. As Steve Wolfe commented in Computer Aided Design Report:
“The favoring of CATIA did not go unnoticed by CADAM’s managers and they were resentful. CADAM had been IBM’s faithful wife, and even if she was not as attractive as she once was, that was no excuse for IBM to go running off with a new French mistress. Relations grew strained and CADAM began developing its own sales and marketing arm to seek distribution outside of IBM’s main sales channels.”
By the time of IBM’s acquisition CADAM, Inc. had 16 sales offices and its own dealer network to distribute MICRO CADAM. This sales organizations was expected to be disbanded and sales responsibilities taken over by IBM.[43]
Contrary to earlier plans, Lockheed did not sell CalComp at this time and instead continued to operate it as a wholly owned subsidiary.
Dassault Systèmes takes over CADAM
In November 1991, IBM sold Dassault the mainframe and workstation versions of CADAM in return for a minority interest in Dassault Systèmes estimated at somewhat over ten percent. Approximately 200 of CADAM, Inc’s 500 employees subsequently transferred to Dassault. CADAM Inc. retained development responsibility for MICRO CADAM, IBM CAD and P-CAD although IBM’s interest in the P-CAD electronic design software waned fairly quickly. This deal had been brewing for nearly a year, initially with the intent that IBM would acquire CATIA from Dassault. Eventually, it ended up the other way around.
It was not entirely clear at the time how Dassault would blend the two product lines together. Although CADAM was still the better drafting solution, few customers were acquiring new licenses strictly for that purpose. CATIA’s drafting, which at one time was virtually non-existent, was gradually improving.
On the flip side, while CADAM’s three-dimensional modeling was slowly improving, it was no match for CATIA. As a result, most new licenses were CATIA. The expectation was that Dassault would take the good stuff from CADAM and eventually add it to CATIA but that this could take some time.[44]
CADAM, Inc. becomes ALTIUM
In the spring of 1993, CADAM, Inc. took on a new identity. It would henceforth be called ALTIUM. Not much else happened at that point in time. ALTIUM was headed by Lee Murray and had about 425 employees with revenues of about $150 million.[45] At the time, IBM was going through a major restructuring of its own and Engineering Automation Report thought that ALTIUM might actually be a model for the future of IBM. The common perception at the time was that IBM would become a collaboration of semi-autonomous business units each focused on a specific product or market area.
Altium operated as an independent company with its own salary and benefit plan. Its employees were considered ALTIUM employees – not IBM employees. When IBM acquired CADAM, Inc. from Lockheed only Murray and one other employee were transferred in from IBM. Perhaps IBM learned a lesson from the way General Electric mismanaged Calma when it acquired that company and replaced nearly its entire top management with GE employees who knew little about CAD/CAM. In addition, IBM did not load Altium down with corporate overhead charges. According to Murray, they were running it “as a typical California software company.”[46]
By the time ALTIUM was established, there were perhaps 75,000 copies of MICRO CADAM in use, many of them in Japan where it was a very popular software package. It was basically a 2 ½ -dimensional drafting package that used a technique the company called “Auxiliary Views” in order to provide three-dimensional capabilities. The primary competition in the PC mechanical drafting market were Autodesk’s AutoCAD and packages from Computervision and CADKEY. In relation to AutoCAD specifically, MICRO CADAM had strong data management capabilities, dimensioning, support of drafting standards, symbol libraries and its user interface. However, its price at $3995 was twice that of AutoCAD and ALTIUM had yet to develop the third party software support and channel distribution capabilities Autodesk had.
When Engineering Automation Report interviewed ALTIUM in the summer of 1993, the company was planning a new release of MICRO CADAM that would incorporate solids and surface geometry modeling as well as three-dimensional AutoCAD DWG and IGES translators. The company was known to be looking at two solid modeling kernels, ACIS from Spatial Technology and Designbase from Japan’s RICOH.
ALTIUM also continued to market IBM CAD which was now being maintained by a group of former IBM programmers who had set up their own company, JMI. Only 15,000 copies of IBM CAD had been sold and over 20 percent of these were used internally by IBM and another 30 to 40 percent were being used by educational institutions. In retrospect, there did not seem to be a good business case to keep this package in the product line and it was eventually dropped.
The third portion of the company’s product line was the P-CAD electrical design software that was primarily sold for use on PCs but was also available for UNIX workstations. ALTIUM never was able to create significant momentum in the electronics design market and dropped this product also.
This semi-independent operation had a relatively brief honeymoon. In October, 1993 it was announced that Alitum was dropping the development of a solids-based version of MICRO CADAM, was reducing its staff by 24 percent and that future development of the MICRO CADAM software would be handled by CADAM Systems Company in Japan. It was also noted that future solids development by CSC would utilize the Ricoh Designbase modeler rather than Spatial’s ACIS. At the same Altium was given the task of marketing electronic design software developed internally at IBM. These products included ProFrame and Logic-Bench which had been used by IBM Microelectronics to design the POWER line of processors.
In early 1994, the ALTIUM situation changed again, this time rather significantly. IBM’s management assigned 16 different hardware and software products to ALTIUM ranging from data collection terminals to the architectural design software (AES) that IBM had developed years earlier with Skidmore Owens & Merrill. The company still had marketing responsibility for MICRO CADAM, IBM CAD and P-CAD. As part of this reorganization, ALTIUM headquarters were relocated from Burbank, California to Charlotte, North Carolina.
MICRO CADAM Inc. enters the picture
As part of the 1994 restructuring of ALTIUM, IBM sold the development and marketing rights to MICRO CADAM to CSC although IBM continued to handle the marketing and sales of the package outside of Japan. By 1995, IBM’s sales organization was showing little interest in selling additional copies of MICRO CADAM and CSC was faced with the need of building its own worldwide distribution organization, especially in North America and Europe.
One result of the MICRO CADAM sale was that about 35 former U.S.-based employees of ALTIUM became employees of a new CSC-owned company called MICROCADAM, Inc. This group relocated from the former ALTIUM facility in Burbank to new offices in downtown Los Angeles. Hiroshi Hara, the president of CSC since its founding in 1984 was also president of the new MICROCADAM subsidiary. Dr. Jack Horgan, who had been with Applicon and was a co-founder of Aries Technology, soon became senior vice-president of MICROCADAM, Inc and basically ran the Los Angeles operation. Another key individual was Lee Whitney who was vicepresident of product planning. As mentioned earlier, Whitney had been involved with CADAM since its start in 1965.
What started out as two similar versions of the same software had, by 1994, diverged significantly. Japan was starting to ship MICRO CADAM V3 while ALTIUM was launching MICRO CADAM Release 14. One example of the differences was that V3 was available in an OS/2 version while Release 14 was not. By late 1995 there were about 75,000 copies of MICRO CADAM in use including 40,000 copies in Japan. The primary product was MICRO CADAM PLUS although it was often referred to simply as MICRO CADAM. It was available in DOS, Windows and UNIX versions ranging in price from $3,995 to $4,795.
Version 14 had a much improved user interface with pull-down menus and popup dialog boxes. Up to five independent viewports, each with its own coordinate system, were supported. A change in one viewport was immediately reflected in the other viewports. There was also bi-directional DXF translation as well as direct translation between MICRO CADAM and AutoCAD. A user development capability called Access had been added as well as a low-cost viewing program.
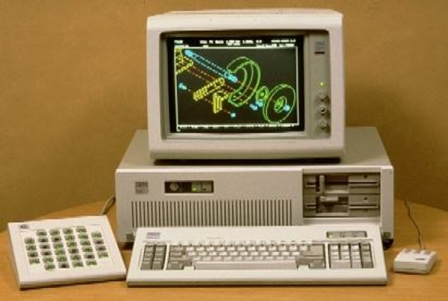
The most significant development in the 1995 time frame was the introduction of a solid modeling package called MICRO CADAM●Helix which used the Ricoh Designbase kernel. It was a fairly decent package with parametric design support, variational geometry implemented using D-Cube’s constraint management software, assembly modeling, visualization and the ability to export data to MICRO CADAM for drafting. It was initially implemented on IBM and Hewlett-Packard UNIX workstations and sold for $3,495 or $7,895 with MICRO CADAM.
Engineering Automation Report summed up the situation at MICROCADAM in its September 1995 issue as follows:
“We believe that MICROCADAM, Inc. has a tough, but not insurmountable, task ahead of itself in re-establishing marketplace momentum. Its products currently appeal to users who are heavily focused on production drafting. This market will diminish over time as interest in parametric modeling and variational geometry grows…….. In order to be successful, the company needs to focus on three critical issues: 1) expanding its product line so that it can offer users a broader solution suite, 2) increasing the number of third-party software developers interested in MICRO CADAM applications, and 3) building an effective North American and European distribution organization.” [47]
Unfortunately, CSC and MICROCADAM were never able to pull this off. Although CSC continued to sell a substantial amount of drafting software in Japan where parametric modeling application had yet to take off, the U.S. market was slow to accept MICROCADAM as a viable vendor. Overall, CSC, including MICROCADAM, was doing about $160 million in annual revenues in 1997.
MICRO CADAM had long been sold as a low-cost alternative to mainframe CADAM. By 1997, most of those users had already switched to a PC or workstation substitute for design and drafting applications and this market for MICRO CADAM was drying up. As a consequence, the company changed its product and marketing strategy somewhat. MICRO CADAM as a separate product went away and was replaced by Helix Parametric Drafting. Priced at $5,695, it was available on both Windows systems and IBM RS/6000 UNIX workstations. A second product combined the Parametric Drafting software with the previously described Helix Modeling package as Helix Engineering. It sold for $8,695 and was only available on Windows. These packages replaced the separate versions on MICRO CADAM that had previously been sold in Japan and the U.S.
In March 2000, IBM acquired the remaining share of CSC it did not already own from Kawasaki, and announced the end of CSC and MICROCADAM. CSC had been successful in Asia but IBM felt that they could make better use of the CSC assets in support of CATIA. There was no need to keep any support outside Japan. IBM did continue to provide CSC products to existing customers for a period of time.
IBM’s Product Data Management activity
Until the late 1980s, managing large volumes of engineering design data had not been a focused issue for either software vendors or users. For the most part, model and drawing files were managed simply using the computer’s basic file management system. IBM offered a program called “Data Communication Service” or DCS that never really caught on with CADAM and CATIA users. In November 1989 a newer product, “CIM Communications and Data Facility” or CIM CDF was introduced. Like DCS, the new software used IBM’s DB2 relational database management system on mainframe computers running the MVS operating system and SDQ/DS on VM systems.
Since CAD data was not organized in a format conducive to storing in a relational database form, IBM created a data structure it called a “long object.” This enabled CIM CDF to store data about the data file such as which application created it, drawing title, version number, etc in the relational database and rapidly retrieve drawings and models based upon this information.
An additional layer of software was implemented by IBM to facilitate the use of CIM CDF. Called “IBM Product Manager: Engineering Management Edition” this software provided capabilities such as product structure management, product change management, routing data to manufacturing systems and cost evaluation. It was the start of a comprehensive Product Data Management or PDM solution. CIM CDF was fairly expensive software. On a large mainframe, the upfront software cost could exceed $400,000 along with subsequent support costs in excess of $60,000 per year. Initially, there were also concerns about the responsiveness of this complex software.[48]
IBM business goes through a major transformation
Many books and articles have been written about IBM’s problems in the late 1980s and early 1990s and how Louis Gerstner was brought in from R.J. Reynolds to turn the company around – a task he did brilliantly. I will not attempt to duplicate that story here but will just cover enough to put this critical transformation into perspective for the rest of our story.
In the first quarter of 1991, IBM’s product sales slid 11 percent followed by a devastating 17 percent drop in the second quarter. The media saw this as possibly the beginning of the end for a company that had once so totally dominated the computer industry. Overall, 1991 was the first year in the company’s then 81-year history to show a sales decline. Total revenue was down 4 percent to $64.8 billion and the company incurred a $2.8 billion loss.
The major problem was that IBM was still wedded to the mainframe at a time when UNIX-based client/server systems were providing more throughput for the dollar and the PC was starting to become a viable business and engineering platform. The mainframe was far more profitable for the company than these alternative platforms would prove to be. IBM was slow to react to these changes, perhaps because its employees had simply become too comfortable with the status quo. IBM maintained a “no layoff” policy through the early 1990s and was only able to reduce its staff through early retirement, attrition and other incentives to quit.[49] The no layoff policy went into the trash can after the poor 1991 results and IBM announced a $3 billion special charge based on plans to layoff 20,000 employees.
Over the years, IBM had become too inwardly focused. Managers saw other IBM divisions as the competition rather than external firms. Far too much effort was spent in positioning each organization for these internal battles over who should be responsible for what. Internal management presentations were critical to ones success and promotion and producing quality slide shows became an art form. When Gerstner became CEO in 1993, one of the first actions he took was to inform those reporting to him that he wanted them to discuss issues without the help of slides and projectors. It was the start of a healthy rebirth of creative activity within the company.
For a period of time after Gerstner came on board, the Advanced Workstation and Systems unit seemed to function much like the other players in the technical workstation market. Likewise, this was the period of time when the company picked up considerable momentum in marketing CATIA and related software products. To keep the nomenclature straight, as of early 1994 the CADAM and CATIA marketing along with related software products was being handled by IBM Applications Solutions Division’s Manufacturing Technology Center in Boca Raton, Florida.
A chink in the IBM/Dassault relationship?
For a time in mid-1992 it appeared that IBM and Dassault Systèmes might be going their separate ways. Dassault set up a sales organization in the United States called Dassault Systèmes Services and announced that it would become a reseller of IBM RS/6000 workstations, apparently with Dassault software. The word in the industry was that Dassault was actively recruiting sales professionals to staff this new organization.
This was not a totally new activity on the part of Dassault. A sales and support organization, Dassault Systèmes U.S.A had actually been established as early as July 1984. If there were major disagreements between the two parties, they managed to keep them mostly private and IBM continued to be the primary sales channel for CATIA as well as handling any residual CADAM activity.
Dassault initiates a major upgrade of CATIA
At the fall 1992 CATIA user conferences – the European CATIA User Association (ECUA) and the CATIA Operators Exchange (COE – as well as at AUTOFACT ’92, Dassault announced a major CATIA upgrade planned for introduction in the second half of 1993. This was the first major overhaul of the software since 1988. Known as CATIA Version 4 it was planned to contain 1,567 functional enhancements including the following features:
- A precise solids modeler to replace the existing faceted modeler used in CATIA.
- The ability to mix surface and solid models.
- Dimension-driven parametric design including feature-based modeling.
- Real-time shading when the software was run on IBM RS/6000 workstations that incorporated GTO graphics cards.
- Assembly modeling.
- A MOTIF-like user interface.
- Associativity between the base model and drafting and NC applications.
Overall, this was an ambitious upgrade to what was a fairly complex product to start with. In order to compete with PTC and other modern design solutions, it was necessary to make these changes as soon as possible.[50] Version 4 was launched in October 1993 just before AUTOFACT’93. It was offered on both mainframes and RS/6000 workstations with the comment that other platforms would be supported starting in 1995. Shipment of both the RS/6000 and mainframe versions began in February 1994.
Dassault shifts into high gear
With the release of CATIA Version 4, Dassault Systèmes and IBM seemed to shift into a higher gear in regards to their sales and marketing momentum. By mid-1994 the installed base of both CADAM and CATIA was impressive as shown in the accompanying table:
CADAMCATIACustomers3,0003,500Host Systems2,2001,200Host-Based Seats55,00027,000Workstation Seats5,00013,000Total Seats60,00040,000
Approximately 40 percent of the CATIA seats were in the automotive industry and 30 percent in aircraft and aerospace. CADAM was more prevalent at aircraft and aerospace companies and was not used as extensively by automobile manufacturers and their suppliers. According to Dassault, about half these seats were installed at customers who used both CADAM and CATIA. Major CATIA accounts were Boeing, Chrysler and BMW.[51]
Organizationally, the former CADAM, Inc. operation in Burbank was now called Dassault Systèms of America (DSA). It functioned as a wholly owned subsidiary of Dassault Systèms and was headed by president Richard Merrill. One of the tasks facing the company at this time was convincing CADAM users that there was a future for that product and that they should stick with Dassault products rather than switching to competitive systems such as Pro/ENGINEER or I-DEAS. One way they did this was by referring to a number of software products as “CATIA/CADAM.” Although maintenance work continued on CADAM it was fairly clear to nearly everyone that eventually that it would be phased out and replaced entirely by CATIA.
Although only IBM RS/6000 workstations in addition to mainframes were supported by CATIA V4 at this time, it was clear to nearly everyone that workstations from multiple vendors and PCs were the wave of the future and that the mainframes’ time had come and passed in regards to interactive technical software. IBM was starting to realize that it had to be prepared to sell design and data management software on platforms the company did not manufacture if it were to continue being a major player in this industry. Plans were underway to start selling Professional CADAM on HewlettPackard Series 700 workstations towards the end of 1994 and CATIA on non-IBM workstations in 1995.
The February release of Version 4 was quickly followed up with Version 4 Release 1.2 (V4R1.2) which added feature based modeling to CATIA. The package now came with about 100 predefined geometric features such as pads, bosses, shafts, pockets, filets, and grooves. To these, users could add their own features that were stored in a feature library. When a feature was inserted into a part, its location and orientation were easily established and key dimension could be entered to determine the size and shape of the feature. An additional V4R1.2 capability was bi-directional associativity between CATIA drawings and the model these drawings were derived from. A change to the model would change the drawing while a dimension change in a drawing would update the model.
The CATIA product line consisted of 54 distinct software packages. Typically, they were combined in 20 different task related bundles targeting specific application requirements. Prices ranged from $6,000 for Mechanical Drawing Production, to $20,500 for Mechanical Advanced Part Design and $40,000 for Mechanical Advanced Assembly Design. IBM sold bundled systems as well as per seat software licenses. An RS/6000 Model 365 workstation with the Advanced Part Design software cost $50,794.
In the 1994 time frame, the CADAM and CATIA installed base was under ferocious attack from two directions. Autodesk was pushing AutoCAD as a low cost alternative to CADAM with a fair amount of success while PTC, SDRC and UGS were pushing their conceptual design solutions as an alternative to both CADAM and CATIA on the basis that the Dassault products were obsolete technology. With the launch of V4 and particularly with V4R1.2, CATIA was generally competitive with these newer designs solutions. On the other hand, Dassault did not yet have a good answer to
AutoCAD in regards to the low-cost PC market. MICRO CADAM was the responsibility of a different company and had basically disappeared from the user community’s radar screen, especially in North America.
Also with the release of V4, the relationship between IBM and Dassault seemed to solidify and the talk about Dassault setting up a separate sales channel for CATIA simply melted away.
CATIA-CADAM and plant design
Although most of Dassault’s and IBM’s focus was on the mechanical market, CADAM and CATIA were also used for AEC applications, primarily process plant design and shipbuilding. Some companies, particularly General Motors, also used CADAM for facility design work such as the layout of manufacturing plants. CADAM, Inc. began developing piping design and drafting software in 1978, working with Avondale Shipyards.
The initial CADAM product used a combination of three-dimensional techniques for piping tasks and two-dimensional representation of non-pipe plant elements such as tanks and pumps. The software was intended to reduce the manual effort required to produce dimensioned spool diagrams (sections of pipe that would be fabricated as an assembly).[52] The Avondale software, referred to as Phase I and based on CADAM Release 18.3, was delivered to customers in October 1978.
Subsequently, CADAM Inc. signed a joint development agreement with Chiyoda Chemical of Japan in December 1982. The result of this endeavor, Phase II or CADAM 3D Piping, was first shown at the Systems ’83 show in June 1983 in Dallas. My impression at the time was that it was very fast compared to other piping design systems I had seen. IBM also began pushing CADAM at about the same time for architectural and facility design.
The following year, IBM demonstrated CADAM DBM (Design, Build and Manage), an application layer that sat on top of CADAM and contained software for drafting wall layouts, generating component schedules and a library of standard details. The wall software worked in single line mode and then converted the layout to a traditional double line version in a batch process. IBM also demonstrated using CATIA to create building models. This was 1984 and the interactive performance was just not there. It would be another decade before we would see significant architectural work done with CATIA by architects such as Frank Gehry.
By 1985, there was confusion over whether CADAM or CATIA would be IBM’s preferred AEC product. At Systems ‘85 the company had demonstrations using both packages. One problem with using CADAM for architectural design was that it could not generate shaded images on the 5080 display. Data had to be transferred to CATIA to do that.
A-E-C Automation Newsletter had an extensive review of CADAM’s Plant Design System in its January 1987 issue. At the time, there was supposedly 150 installations of CADAM’s plant design software which consisted of ten different modules. The piping design aspects of this software were fairly impressive. The software came with a basic library of 4,500 piping components along with the ability to create custom libraries.
Piping layouts could be displayed in a variety of single line and double line modes. Users could route piping components in multiple different ways and display the results in both orthographic and isometric modes. There was one major problems with using CADAM for plant design – that was the software’s 64 KB file size limit. As a result, large plant designs were done as a series of overlay models, perhaps as many as 200 of which 20 could be viewed simultaneously.[53]
Eventually there were two versions of the plant design software, one built around CADAM, the other based on CATIA. After Dassault took over CADAM from IBM the plan was to bring these two versions together to support what the company called the “Virtual Plant.” Much of this development work was untaken at the DSA facility in California.
The new software was database intensive with object oriented features. It had parametric design capabilities, rule-based model checking and open platform support. Initially it was called CATIA/CADAM AEC Plant Solutions and supported detailed piping design, interference checking, and space management. This was the start of the move towards supporting process plant and shipbuilding design with software utilizing solids modeling at its core. It required the software architecture to mature to the point where these tasks could be done swiftly and accurately and the processing power of moderately priced workstations to progress to the point where they could handle largescale modeling tasks effectively.[54]
The obvious question is why wasn’t IBM more successful selling AEC software, especially to plant engineering and construction organizations. My personal opinion, supported by other industry observers, was that IBM simply never had industry knowledgeable sales personnel in sufficient numbers focused on this market.
IBM and Skidmore, Owings and Merrill attack the architecture market
Skidmore, Owings and Merrill (SOM), the large Chicago-based engineering and architectural firm, was an early adopter of computer technology. The company began developing structural engineering software in 1962 using an IBM 1620. In 1967, G. Neil Harper[55] and David Sides implemented a building planning program on an IBM 1130 computer. Building Optimization Program (BOP) used a linear programming technique to determine the optimum number of floors, number of elevators, structural bay size, etc. for a given size site and required floor space. SOM also developed other applications for hospital space planning and the storage and analysis of client requirement information.
In the early 1970s, Douglas Stoker became involved in SOM computer activity, initially developing software that was used to prepare input data for the structural analysis of buildings such as the Sears Tower in Chicago. This work was also done on the IBM 1130. By the mid-1970s, Stoker, along with Bill Kovacs[56], Nick Weingarten and others at SOM, began developing a comprehensive suite of architectural design and engineering programs.
Initially this work was done on a Digital PDP 11/45 and a PDP 11/70 using Tektronix graphics terminals. Eventually, the PDP 11s were replaced by a VAX 11/780. The software was used to create three-dimensional wireframe models of buildings as well as produce construction drawings. The early version of the software was simply called DRAFT.[57] Stoker and others at SOM were convinced that the traditional CAD companies could never understand the intricacies of building design as well as a design firm could. Except for some analysis software, SOM primarily used software it developed internally for many years.
By 1986, SOM sensed that minicomputers such as Digital’s VAX systems were falling behind technically and the firm began switching to the new IBM RT-PC described earlier. It is not clear exactly when SOM began discussion with IBM to have the latter company market SOM’s architectural and engineering software. In November 1986 the two companies signed an agreement that called for SOM to convert and extend the DRAFT software to run on the RT-PC using the IBM 5081 display. The overall project, which had nearly 50 people assigned to it, was called the SOM-SKYLINE Project. The first DRAFT module planned for delivery to IBM customers was to be called Base Graphics System.
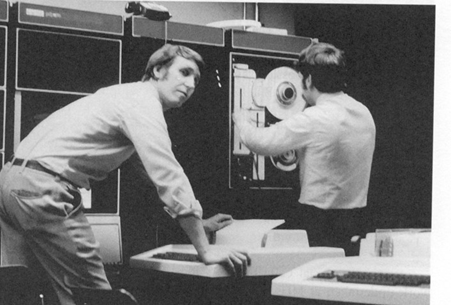
Ed Forrest, writing in the May 1987 issue of A-E-C Automation Newsletter was extremely excited by this new collaboration between SOM and IBM. “Having been shown the master plan of the software products proposed to IBM by SOM, I assure you I know of no existing product(s) anywhere near it nor am I aware of any being proposed.”
Stoker was equally enthusiastic in the same issue of the newsletter about the potential for this new software to be used to manage the entire lifecycle of a building. “That’s where we’re heading with SOM-SKYLINE. We’re heading to create a design tool that can be used as a geometric access method to information describing the built-environment.[59]
The SOM software was renamed AES (Architecture Engineering Series) and was sold by IBM for a number of years. When SOM dropped support of AES, it was picked up by Premisys Corporation where Weingarten was involved in maintaining the software.
SOM itself, has moved on from using AES to Autodesk’s AutoCAD and Revit.
Dassault adds multi-platform support
Dassault Systèms continued to roll out new releases of CATIA at a fairly regular clip. CATIA Version 4 Release 1.4 was announced in March 1995. This release contained improved geometric modeling capabilities, improve data handling between applications and improved CADAM/CATIA interoperability. The most significant step, however, was the announcement that the software would be supported on both HewlettPackard and Silicon Graphics workstations. Obviously, IBM sales personnel were not going to promote these versions over the RS/6000 implementation but if the customer was an HP or SGI shop they still wanted to sell them the software. CATIA became available first on SGI workstations in March 1996. In the first two years, nearly 10,000 copies of CATIA were sold on the SGI platform.[60]
Dassault continued to roll out new releases about every six months. V4R1.5 came out in October 1995 with new modeling capabilities and increased the number of distinct modules to 78. The most significant development was the introduction of the CATIA/CADAM AEC Plant Solutions package described earlier. It was built around CADAM’s two-dimensional drafting and CATIA’s three-dimensional modeling capabilities. There was also a new CATIA Shipbuilding module that could be used to design ship hulls and superstructure while Plant Solutions was used to design the interior of ships.
By the spring of 1996, V4R1.6 was being shipped to customers and the term CATIA/CADAM Solutions was being used with more frequency. This software had improved dynamic sketching capabilities, a two-dimensional freehand tool that automatically constrained geometry called Sketchit! and the integration of Imageware software for free form surface design. At this point, many CADAM users had migrated to competitive systems and IBM and Dassault wanted to project an image that there was still a future for these users by installing software that blended together the best of CADAM and CATIA. Also, the first Windows NT implementation was available, CATIA/CADAM Drafting.[61]
An example of the two companies determination to make the multi-platform concept work was at the spring 1996 CATIA Operators Exchange meeting in Miami Beach where the presentation on the future of computer technology was given by Hewlett-Packard’s Dick Lampman. IBM management emphasized that its CAD sales personnel were platform independent and received the same commission irrespective of the platform the software ran on.[62]
As mentioned earlier, marketing and support of CATIA was handled by IBM’s 800-person Engineering Technology Solutions (ETS) group which was part of the larger Manufacturing Industries Solutions business unit. Dr. Frank Lerchenmuller, the IBM vice-president in charge of ETS, was located in Paris just a few minutes from Dassault Systèmes. IBM was focused on selling to large accounts and was developing a distribution channel to handle smaller accounts. Engineering Automation Report felt positive about Dassault and IBM’s future in the CAD industry:
“…EAReport believes that the coming five years will see significant consolidation in the industry. Our expectation is that the IBM/Dassault partnership will be one of the survivors and will probably be in one of the top two or three positions.”
This definitely is what eventually happened. By mid-1996 Dassault Systèmes was planning an initial public offering.[63]
One of the more difficult tasks facing CATIA users was that it could take up to several days to load CATIA on an RS/6000 workstation using software from multiple sources. In April 1997 IBM began shipping a new CD called “The RS/6000 Operating Environment for CATIA” that included all the software needed to run CATIA. It reduced the time needed to load a typical implementation to just a few hours.
By the time V4R1.8 came out in mid-1997, the entire CATIA-CADAM product suite consisted of 108 distinct programs. One reason behind this large number of modules was that Dassault tended to split functionality into more separate programs than did most other vendors.
The relationship between Dassault’s data management capabilities and those of IBM was starting to coalesce about this time. The CATIA Data Management (CDM) program provided graphical product structure management while IBM’s ProductManager handled configuration management and change control. Slowly but surely, IBM’s PDM software was taking on more Internet characteristics. A Java-based Web browser was added to the ProductManager client software.
CATIA V4R2.0 came out in the late summer of 1998. A major effort was put into enhancing the software capabilities to support the digital mockup of complex assemblies and visualizing the resulting models. CATIA 4D Navigator was the primary module for supporting this task. By now there were 115 CATIA modules in the entire V4 product suite.
Dassault goes public and acquires SolidWorks
In 1995, Bernard Charlès became president of the Dassault Systèmes. He had been in charge of the company’s R&D efforts as well planning its long term strategy. In 1996 the company went public with its shares listed on both the Paris bourse and NASDAQ.
On June 24, 1997 Dassault Systèmes and SolidWorks Corporation announced that Dassault would be acquiring SolidWorks for $310 million. At the time SolidWorks had sold about 6,000 copies of its SolidWorks software to about 3,000 accounts and was generating approximately $25 million in annual revenue. This meant Dassault was paying over 12 times annual revenue for a fairly new company. Rich but not unheard of in the heady days of the period as the dot com boom was starting to explode.
The July issue of Engineering Automation Report commented;
“Miller (Dick Miller, then vice-president of ANSYS) and others seem to think that this acquisition will put pressure on Parametric Technology in that it will squeeze that company between a well positioned high-end vendor and the fastest growing mid-range software provider in the CAD industry. Our observation is somewhat different in that we believe it will have a greater impact on other mid-range mechanical CAD Vendors such as Intergraph (then vendor of Solid Edge), Autodesk, Bentley and Cad.Lab. Time will tell.”
In retrospect, both Miller and EAReport were probably correct.[64]
As noted elsewhere, since Dassault operated SolidWorks very much as an independent subsidiary, it will be cover in a separate chapter. (See Chapter 18.)
Establishing a presence in manufacturing automation
Until late 1997, Dassault focused primarily on automating design and drafting tasks with a moderate amount of strength in the NC area. This began to change in December 1997 when the company announced plans to acquire Deneb, an Auburn Hills, Michigan vendor of robotics programming software, for $105 million in cash. Estimates were that Deneb had $18 to $20 million in annual revenues at the time of the acquisition meaning that Dassault was paying five to six times revenue, substantially less than the 12 times revenue it paid for SolidWorks.
The company made several subsequent acquisitions in this area including the Delta subsidiary of Engineering Animation which developed process planning software and Safework, a vendor of ergonometric software. In June 2000, this group of companies were put together as a single business unit named DELMIA. For the most part, the software products developed by this group continued to be distributed by a separate distribution channel, independent of IBM.
Dassault gets serious about PDM
In early 1998 it was obvious to industry observers that there was a serious disconnect in Dassault Systèmes’ product and marketing strategy. While CATIACADAM was becoming a strong enterprise level design solution, between IBM and Dassault they offered fairly mediocre Product Data Management software, especially when compared to products such as SDRC’s Metaphase. A major step towards resolving this shortcoming occurred in February 1998 when Dassault announced that it was establishing a new PDM business unit in Charlotte, NC called ENOVIA. It was to be managed by Joel Lemke who previously had been general manager of IBM’s Global Manufacturing Industries Unit. Putting someone with Lemke’s experience in charge of this new group sent the message that Dassault was serious about the PDM market.
The reason that this new group was set up in Charlotte was because the primary software it would be working with was IBM’s ProductManager which Dassault acquired from IBM for $45 million. IBM’s commitment to the PDM market consisted of establishing two new worldwide organizations. IBM PDM II Solutions marketed and sold ENOVIA products independently of the group that sold CATIA and IBM Enterprise Engineering Services provided consulting and implementation services in the PDM area.
This latter activity was in recognition that much of the money to be made in regards to PDM software was in helping users understand the technology and the steps necessary in successfully implementing it. The plan was clearly to sell PDM software to users of design software other than CATIA. Subsequently those two business units were renamed IBM PLM[65] Solutions and IBM Global Services (IGS), respectively.
ENOVIA was actually Dassault’s second acquisition in the PDM space. In early 1999, the company had acquired a 75 percent interest in Smart Solutions, Ltd., a vendor of moderately priced department-level PDM solutions based in Tel Aviv, Israel. Initially it was closely linked with SolidWorks but eventually came to be seen as an alternative to ENOVIA, especially for use with CATIA V5. Smart Solutions is now known as SMARTEAM. IBM PLM Solutions handles the sales and marketing of SMARTEAM software used with CATIA and non-Dassault CAD systems while a separate SMARTEAM channel works with SolidWorks users.
CATIA Version 5 breaks with the past
At the Design Engineering Show in March 1998, Dassault Systèmes previewed CATIA Version 5. The company had been working on this new software for some time under the code name “CNext.” The software was being written specifically for Windows NT in C++ used object-oriented programming methodologies. It was developed from the start using newer standards such as STEP and OpenGL. Only a limited amount of functionality was ready to be demonstrated at NDES but the software was fast and the user interface was streamlined from what CATIA V4 used.
It appeared at this early date that V4 and V5 would have to co-exist for some period of time. Engineering Automation Report was cognizant of the potential problems the transition from V4 to V5 might cause. “We believe that IBM and Dassault need to plan the transition from 4 to 5 very carefully or the two companies stand the risk of duplicating the disaster Computervision went through several years ago when that company moved its customers from CADDS 4X to CADDS 5.”[66] Without getting ahead of the story, they eventually did an admirable job managing the transition although nearly a decade later, many customers are still using V4.
In 1998, Dassault shipped V5 to an initial group of 25 customers with widespread distribution planned for 1999. It was obvious that moving model data between V4 and V5 was as difficult as moving it between software packages from two different vendors. V5 began shipping with both Windows NT and UNIX implementations in volume in March 1999, nearly a year after it was first announced.
In August 1999, Dassault began shipping Release 2 (V5R2) which included a lower priced yet quite functional version called Platform 1 (P1). It was intended to attract
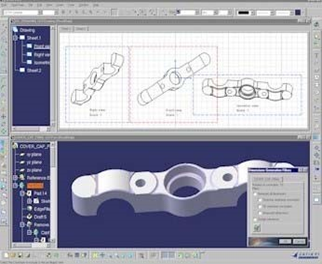
CATIA V5R2 Generative Drafting created multiple drawing views from a solid model potential customers in the machinery, consumer goods and electronics markets. The fullfunction version of V5 was subsequently called Platform 2 (P2). V5R2 incorporated much of the two-dimensional drafting and three-dimensional surfacing capabilities that had not made it into the first release. P1 offered about 80% of the functionality of P2 and the two versions were bi-directionally compatible. While P2 ran on both UNIX and Windows NT, P1 also was available for use on Windows 95 and Windows 98. Pricing for P1 began at $4,500 for the two-dimensional solution and under $10,000 for the threedimensional solution. P2 was priced at $7,500 and $13,000 respectively.
V5R3 was released in early 2000 with design rule checking and assembly mockup. The Windows NT version was gaining increased acceptance, especially since it outperformed some of the UNIX implementations.[67]
Dassault picks up remnants of Matra Datavision
Matra Datavision, (discussed in Chapter 21) the developer of the EUCLID suite of design, analysis and manufacturing applications had been struggling for some time.
The company had some very good surfacing software after it acquired Cisigraph and its STRIM soft several years earlier. Two companies were thought to be interested in acquiring Matra Datavision, Autodesk and SDRC. Autodesk turned out to not be interested and SDRC basically took itself out of the running when it acquired Imageware Corporation, another vendor of surface geometry software.
Few people were terribly surprised when Matra Datavision, Dassault Systemes and IBM announced a three-party agreement under which:
- Dassault acquired a Matra Datavision subsidiary to which ownership of EUCLID STYLER, EUCLID MACHINIST, STRIM AND STRIMFLOW had been transferred. In addition, Dassault picked up a license to use Matra’s CAS.CADE software development technology. Approximately 90 developers who had been working for Matra became Dassault employees.
- Dassault planned to integrate the acquired packages into CATIA V5. This was intended to provide users with enhanced free-form surface definition, machining and plastic part design capabilities.
- Matra Datavision announced that it would continue to support EUCLID 3 and CAS.CADE but not solicit new customers for that software
- Matra Datavision then became a reseller of Dassault software including CATIA, CATWEB, ENOVIA and Deneb’s Digital Manufacturing software as an IBM International Business Partner.
The expectation was that that many of Matra’s EUCLID customers would eventually move to CATIA, particularly the new Windows NT-oriented V5. Dassault did not pay a lot for the Matra software products, perhaps $40 to $50 million.
Dassault acquires Spatial Technology
In July 2000 Dassault Systèmes and Spatial Technology announced that Dassault would acquire Spatial’s component software operation including the ACIS 3D Toolkit for $21.5 million in cash. Spatial had been putting an increasing amount of its efforts into developing Web-centric services for the design community and had decided that its future lay in this area rather than in the solids modeling kernel business. The money from Dassault was intended to finance Spatial’s Web activity known as PlanetCAD.
Subsequent to the acquisition, Dassault would own the Spatial name and the remainder of the company would be renamed PlanetCAD, Inc.
Several months later the offer was increased by $4.5 million to a total of $25 million. This was done in reaction to a counter offer for Spatial from SDRC for $26 million plus a guarantee of an additional $2 million in revenues for PlanetCAD services from SDRC customers. Dassault also agreed to a number of technology sharing agreements and joint marketing efforts with PlanetCAD. Spatial’s board considered the revised Dassault offer to be “functionally equivalent” to that of SDRC.
According to a Spatial’s filing with the SEC regarding the acquisition, “the board determined that given their relative size and market positions, the future support and relationship with Dassault and Dassault Systèmes would be more beneficial to PlanetCAD than the relationship proposed by SDRC.”[68] The deal was completed in November.
Bruce Morgan, then CEO of Spatial, stayed with the PanetCAD portion of the business and Mike Payne who had been a founder of both PTC and SolidWorks took over running Spatial for the next several years. The issue that made this acquisition hard to understand was that Dassault’s SolidWorks subsidiary was using UGS’ Parasolid kernel and showed no interest in switching back to ACIS just because Dassault now owned it.
Under Dassault, Spatial continued to enhance ACIS using existing and new Dassault technology and while not thriving, continues to have a fairly respectable component software business as this is being written.
IBM and Dassault in the 21st century
By mid-2000 the relative positioning of CATIA Version 4 and Version 5, at least in the near term, was starting to become clearer. V4 continued to be Dassault’s flagship product in the automotive and aerospace industry as long those customers were willing to stick with UNIX-based solutions. V5 was targeted more at small to medium sized user organizations that were looking for a tightly integrated solution from a single vendor. Since V5 came in both UNIX and Windows flavors, it also served as the replacement package for UNIX-based V4 users who wanted to migrate to Windows. Dassault’s SolidWorks was a traditional mid-range product that required third-party packages to provide a complete design, analysis and manufacturing solution. The latter product continued to be marketed separately from CATIA.
In July 2000 new versions of both V4 and V5 were announced. It was obvious the predominant amount of development effort was going into V5, but Dassault was still enhancing V4, not just doing cosmetic maintenance. V4R2.3 contained modeling, analysis and manufacturing enhancements. These paled, however, compared to the 12 new V5 modules the company introduced along with enhancements to 39 other V5 modules that covered everything from generative drafting to freestyle sketching and structural analysis. V5 was rapidly becoming an industrial strength suite of software products.
Dassault continued to make acquisitions to expand its product offerings. On March 30, 2001 it announced that it would acquire Structural Research and Analysis Corporation of Los Angeles for $22 million in stock. SRAC was the developer of the well-respected COSMOS family of structural analysis software products that were used extensively with mid-range CAD solutions. In particular, it was the analysis software used most frequently with SolidWorks. As described in Chapter 22, SRAC became a subsidiary of SolidWorks and the COSMOS software was tightly integrated with SolidWorks and in fairly short order the company began distributing the analysis software as COSMOSWorks.[69]
Dassault Systèmes of America was the Woodland Hills, CA remnant of the original CADAM organization. Under Phillippe Forestier, it was responsible for the development of CATIA-CADAM Plant, CATIA-CADAM Drafting and support of the legacy CADAM software that was still being used extensively. In what is probably a CAD industry longevity record, Rick Watanabe celebrated 40 continuous years involved with CADAM in 2007 – initially as a CADAM user and manager at Lockheed, as a manager at CADAM, Inc. and as CADAM support manager at Dassault Systèmes of America
The company was more frequently referring to the combination of CATIA, ENOVIA and DELMIA as its overall PLM or Product Lifecycle Management solution.
At the Fall 2001 CATIA Operator Exchange meeting in Orlando, Florida the company made a pitch that henceforth it wanted to be referred to simply as DS rather than Dassault Systèmes and at the same time introduced a new corporate logo using the term “3DS”[70].
The major development in early 2002 was that Toyota Motor Corporation had selected CATIA V5 as its primary vehicle design system replacing its internally developed TOGO CAD. The latter software had been developed since 1993 by a subsidiary, Toyota Caelum, The procurement was a $150 million deal for 10,000 seats, not counting new hardware and support services to be provided by IBM. It should be noted that PTC retained much of its powertrain design business at Toyota.
An extensive article by Brad Holtz in the July 2002 issue of Engineering Automation Report explored the relationship between IBM and Dassault in some depth. A substantial portion of the article described how the two companies saw the PLM market evolving. Dassault used the term “3D PLM” to describe the design software that constituted this area. IBM took a broader view where it saw “PLM” as a solution for sharing product data across all aspects of a company. In IBM’s eyes, PLM consisted of software, middleware, hardware and services.
IBM is clearly focused on selling enterprise-level solutions to large organizations. These solutions consist primarily of CATIA, Enovia and SMARTEAM software from Dassault complemented by other software products and services from IBM itself as well as other business partners. It does not seem to bother IBM that Dassault has other products such as SolidWorks, COSMOSWorks and ACIS that are sold through other channels. Hotz’s summary of the relationship between the two companies was that “The relationship is stronger than ever” but that “Right now, IBM and Dassault Systemes need to coordinate their message”[71].
By 2006, Dassault Systèmes was a $1 billion company growing over 25 percent annually. In May of 2006 it completed the acquisition of MatrixOne for $410 million in cash. Now known as ENOVIA MatrixOne, it greatly enhanced the company’s PLM offering. In mid-2007, Dassault acquired ICEM, Ltd., the vendor of ICEM SURF, for the equivalent of $69 million. (See Chapter 21)