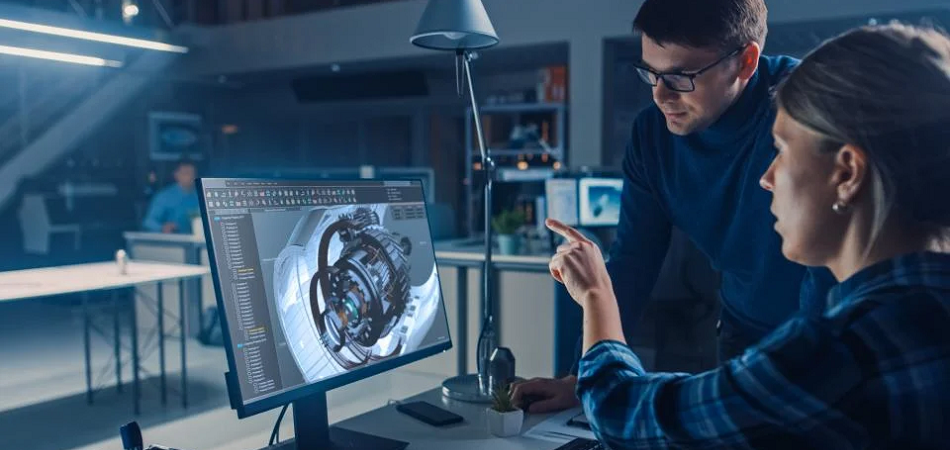
Space restrictions simply do not permit me to go into the depth of detail I would like on every company that participated in the early days of the CAD industry nor cover numerous in-house systems developed at major automobile and aerospace companies. Readers will have to be satisfied with the brief descriptions included in this chapter and even then, I have only been able to cover what I consider to be the companies that had the biggest impact. There are hundreds if not thousands of companies that at one time marketed engineering design software. Some of the companies described in this chapter offered just software while other provided both hardware and software. While many have changed names, I have decided to list them alphabetically based upon the name they are best been known by along with earlier and subsequent name changes.
Adra Systems (Matrix One)
Adra Systems was founded in Lowell, Massachusetts in July 1983 by William Mason, who had been at Applicon from 1973 to 1983, most recently as vice president of operations, James Stenzel, who had been vice president of engineering at Hastech, Inc., and Peter Stoupas, who had earlier been a regional sales manager at Adage and had also worked for Applicon. Mason became the president and CEO, Stenzel the vice president of product development and Stoupas the vice president of marketing. Between 1983 and 1986, the company raised $11.6 million of venture funding from a number of firms including American Research & Development, the company that also provided the initial funding for Digital Equipment Corporation.
Adra’s initial product, introduced in January 1985, was a CADAM-compatible combination of hardware and software that was marketed by Adage, Inc as the CADStation 2/50. At the time, Adage was one of the major non-IBM manufacturers of graphic terminals used to support the mainframe CADAM software sold by IBM. The software component, which was called Cadra-1, emulated the look and feel of CADAM. It could extract a drawing from a mainframe database, work on the drawing and then refile it on the mainframe.
CADAM, Inc. did not take kindly to this product introduction since it competed directly with the sale of CADAM. A lawsuit was filed against both Adage and Adra which settled out of court in 1987. CADAM, Inc. received a payment “in excess of one million dollars” and Adage agreed to no longer sell the CADStation 2/50 once its existing inventory was depleted.[1]
The company introduced the Adra 1000 system in November 1985. Similar to the CADStation 2/50, it consisted of a 10-MHz Motorola 68010 microprocessor with 2.5MB of main memory, UNIX, a custom graphics processor and a 19-inch 1024×1024 monochromatic or color monitor. No local hard disk was provided. Graphics performance, particularly pan and zoom operations, was very fast. The major difference from the earlier system was that the Adra 1000 with its Cadra-2 software was intended to be used as a standalone two-dimensional drafting system. The initial price for a basic system was $15,750.
A year later, Adra Systems introduced the Adra 3000, similar to the 1000 except with a Motorola 68020 microprocessor, a higher performance graphics accelerator, better communication capabilities and an optional 20MB disk drive. With the company’s Cadra-2 software, the Adra 3000 could be used as an adjunct to a CADAM system or as a low-cost alternative. These systems started at $14,750 for the monochromatic version and $18,750 for the color system. Meanwhile, the price of the Adra 1000 was dropped to $11,750.
In August 1988, Adra introduced a PC-based system called Acclaim. The key element was an external co-processor that included the company’s bit-sliced graphics processor and 4MB of memory. The Cadra software actually ran in this co-processor which plugged into one of the PC’s parallel ports. The software and co-processor sold for $10, 795 while a complete system including a 16-MHz 386 PC and 19-inch monitor was priced at $21,190.
Eventually, Adra got out of the hardware end of the business and concentrated on the Cadra software. It positioned itself as providing a low-cost alternative to the large enterprise-type systems sold by Computervision, IBM Applicon, etc. The company stressed Cadra’s ease of use and the user’s ability to customize the software using a programming tool called “Autogeometry.” This latter software was also used to interface Cadra to systems other than CADAM. Both PCs and UNIX workstations were supported.
By 1996, the company had installed about 17,000 copies of its software at 1,500 to 1,600 customers. Adra offered a number of different packages at this point. Cadra Design Drafting was the company’s flagship product. Selling for $3,995, it was no longer simply a CADAM clone. Adra had added many of its own concepts including intelligent dimensioning, variational and parametric editing, unlimited drawing size (this was one of the major limitations of CADAM), display of up to 200 views and license management that allowed copies of the software to be shared over a local network.
The software was available on most UNIX platforms as well as on Windows. To make the transition to Windows less painful for existing users, the company left the older user interface in the software and the user could select either the Windows paradigm or the older interface.
Adra also developed a solids modeling package, Cadra Solids, based on the DesignBase geometric kernel from Ricoh Corporation. This was a hybrid modeler that allowed users to mix wireframe, surface and solid geometry. While other low-cost packages tended to use faceted surface geometry, Cadra Solids used precise B-REP techniques. Editing was done by grabbing a vertex, edge or surface with a mouse click and dragging it to a new location. The user could also directly modify a model by editing its history tree. Initially, Cadra Solids, which was only available on UNIX workstations, sold for $5,995, the same as the UNIX version of the basic Cadra package. Combined, the two packages cost $10,995. Several years later this price was down to $6,500 which was still nearly twice what SolidWorks sold for at the time. Adra also offered NC software as well as a package for electrical control and power system.
In 1992, Adra established a new operation in Shelton, Connecticut to develop product data management (PDM) software. This group, initially called the “Looking Glass Project” and subsequently the Matrix Division, was headed by Joseph Pieto who had previously developed IGOR[2], a document management package, at the Sikorsky Division of United Technology. The company introduced this software as a PDM product called Matrix. It used a relatively new object-oriented database, Objectivity DB from Objectivity, Inc. The system had impressive capabilities but like many other early objectoriented systems, suffered performance issues when it was scaled up to handle a large volume of data.
Like Cadra, Matrix had an easy-to-use user interface, good document routing capabilities, a distributed database that eliminated the need for a centralized server and the ability to manage a wide range of documents. Mark O’Connell joined Adra as vice president of marketing in 1995. He had previously held a series of financial and marketing management jobs at Digital Equipment Corporation. O’Connell became president of Adra in 1996 and CEO in 1997.
Within a few years, the tail began to wag the dog. In an interview in 1996, Mason stated that the portion of the company’s business represented by Matrix had gone from 15 percent in 1995 to 33 percent in 1996 and would be 50 percent in 1997. Eventually, he thought it would become 80 percent of Adra’s business.[3] It actually became 100 percent in 1998 when in May of that year Adra sold the design and manufacturing software portion of Adra Systems to SofTech for $11.4 million. At the time the Cadra product line was generating about $15 million in annual revenues while Matrix was responsible for $21 million.
The company used these funds to shift its PDM business into high gear. It changed its name to MatrixOne and the product became eMatrix to reflect its Internet focus. Sales increased to nearly $75 million in fiscal 2000 (the company’s fiscal year ended July 1) and the company went public on March 6, 2000, selling 6.2 million shares at $25 per share. Almost immediately, the price increased to over $70.
The next year revenues nearly doubled to $145 million, resulting in profits of $8.8 million. This was the company’s peak year. Revenue dropped over the next several years to $109 million in fiscal 2003 and 2004 and the company incurred substantial losses before heading back into the black in late 2004. By October 2002, the company’s stock had lost over 95 percent of its value from its earlier high and only improved moderately over the next few years. On March 2, 2006, Dassault Systèmes announced that it was acquiring MatrixOne for $7.25 per share (approximately $408 million) or about 3.3 times revenue. The acquisition was completed on May 11, 2006 and MatrixOne became ENOVIA MatrixOne.
Alibre
Alibre was founded in Richardson, Texas in 1997 by J. Paul Grayson and Stephen Emmons. The company was initially called Entity Systems but changed its name to Alibre before any software was shown to the public. Grayson was the founder and former CEO of Micrografx, a vendor of low-cost PC graphics software including PC-Draw. Emmons was also formerly at Micrografix where he was the principal developer of Micrografix Designer. Grayson, who put up the initial funding for Alibre, was the CEO and Emmons chief technology officer. Over the next several years the company raised over $18 million in venture funding.
During its first two years the company concentrated on developing a new mechanical design package that could be provided to users over the Internet. The delivery mechanism was referred to as an Application Service Provider or ASP. Users would access the software with nothing more than a web browser on their desktop or notebook computer. The actual application software resided on servers operated by Alibre.
The software, Alibre Design, was first shown publicly at the M/TECH ’99 conference in Chicago in November 1999. It used Spatial Technology’s ACIS kernel, DCube’s constraint manager as well as component software from several other providers. Engineering Automation Report was fairly enthusiastic, probably overly so, about this new concept for providing CAD software:
“Just when you figure that the mechanical CAD industry has more software vendors than it can rationally support, along comes a new company with new ideas that forces you to realize that there really is room for another vendor…… Since the software runs on servers managed by Alibre, there is no need to invest in expensive computer hardware. In addition, if a designer is visiting a supplier, he or she can log on to the service from any available computer. No need to have the design software locally loaded. Within a few years, you might be able to work on designs from your seat on an airplane. ……..The design software that we viewed seems to be comparable to the early stages of most other mid-range solutions……. We have a gut feeling that this company is going to make it big. It is well financed and appears to have a strategy right on target. Many computer industry observers, including this newsletter, believe that ASPs are the wave of the future.” [4]
The software as provided in a “preview version” a few months later differed somewhat from what had been presented at M/TECH. In addition to the pure ASP implementation described above, the company offered a version where the model creation and editing software was moved to the user’s desktop system and the ASP server was used to store and manage the user’s data. Initial performance was relatively slow, probably because the software was written in Java which still executed interpretively rather than in compiled mode. The software turned out to lack some of the capabilities users had come to associate with most mid-range packages such as variable radius fillets and free-form surfaces. In a significant change of focus, the company began shifting its marketing message from pure mechanical design to design collaboration.
Alibre Design 1.0 went live on April 10, 2000. It was made available on a subscription basis at $100 per month per user or on a self hosted basis at a price of $5,000 for six months use. Virtually all of the company’s sales and support activities were web based. Meanwhile the company’s management team was growing rapidly. Tommy Steele, who had previously been president of Intergraph Software Solutions, was COO, Tom Kopinski, who had been with Autodesk and SolidWorks, was vice president of sales and Greg Milliken, who had been with Knowledge Revolution before it was acquired by MSC.Software, was vice president of marketing. Neither Steele nor Kopinski stayed long but Milliken eventually became president and CEO of the company.
Grayson and company were strong believers in Microsoft technology and Alibre was one of the first applications to support Windows 2000. In fact, Bill Gates used it as a demonstration tool for the Windows 2000 launch.
Alibre evolved into a four-tier product:
- A web browser-based client that handled the display and manipulation of wireframe and shaded models.
- An application design server that supported model creation and editing as well as drawing production.
- A database server the handled access privileges, revision control and check in/out. This was often referred to as the repository server.
- An administration server that tied this all together.
The separation of the browser-based client from the design and data management servers allowed the client to run locally while the design and data management services could be either local or remote. By October 2000, Alibre had changed its business model and was providing the modeler as a free 18MB download and charging for the collaboration services it was providing on a subscription basis. About the same time it released Alibre Design 2.0 which addressed some of the performance issues.
Alibre got off to a slower start than expected. Although thousands of potential customer downloaded free trial software, less than 1,000 signed up for the company’s subscription service as of February 2001. Those that were using it were probably more intrigued by the software’s collaboration capabilities than by its design prowess which lagged competitive packages such as SolidWorks. About this time, Microsoft and Sun Microsystems settled their dispute over Java and Microsoft introduced a new programming language, C# as its web-centric programming language of the future and Alibre stated that it would convert from Java to C# in the future.
With Alibre Design 4.0, released in May 2002, the software became a Windows application rather than being browser based. The software could be used either off-line or in a collaboration mode over the Internet.
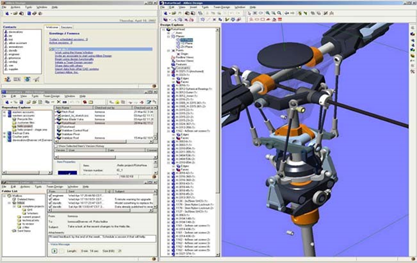
The company’s business model changed once again with the $100 monthly subscription fee dropped and replaced by a $995 annual fee. Then a $495 promotion, which was offered when 4.0 was released, soon became the new price point. Self-hosted licenses were also available at prices based on the number of users. By 2002, however, the company was no longer aggressively pushing this type of business. The software was provided either on a CD-ROM or as a 25MB download. Increasingly, the company emphasized its collaboration capabilities and the ability to work with data from other CAD systems.
In late 2002, the company’s focus changed once again and Alibre began promoting its software as a low-cost alternative to competitive mid-range packages. An enhanced version of the software, Alibre Design Professional, was released in April 2003, priced at $995 for an annual license, while the basic version of the software was increased to $695 per year.
One of the more interesting aspects of the Alibre story was the outright theft of its software by a Russian programmer, Roman Voznyuk, who had been laid off in 2003 during a corporate reorganization. Voznyuk returned to Russia and began offering a slightly modified version of Alibre Design as RaceCAD Design Professional. Alibre filed lawsuits in both Russian and American courts claiming that RaceCAD was created directly from source code for Alibre Design, and that RaceCAD also incorporated software stolen from Spatial, D-Cubed, the OpenDWG Alliance, and others. Criminal charges were also filed.
According to Grayson: “he offered to ‘settle’ with us and discontinue the English version if we gave him the Russian version. Clearly, the only thing he is going to get is a stiff penalty and likely jail time.”[5] While the lawsuits were never resolved, RaceCAD simply faded from the scene. Then in August 2007, Voznyuk was arrested in upstate New York as he attempted to enter the United States from Canada where he had been working.
In February 2004, Milliken became president and CEO while Grayson remained chairman of the board. One of Milliken’s first steps was to raise the price of the company’s products to $795 annually for Alibre Design, $1,295 for Alibre Design Professional, and $1,795 for Alibre Design Expert, a newer more expanded version of the software. A free stripped down version, Alibre Design Xpress was launched in mid-2004. Xpress drew large numbers of prospective users to the company’s web site and a significant number ended up as paying customers for Alibre Design.
Alibre never became the $100 million business Grayson expected, but it did become a profitable business. It continues to be an interesting chapter in the evolution of the CAD industry. As this is written, the company’s software is being sold by VARs as well as on-line although the on-line approach is the company’s preferred sales and support vehicle. Its board of directors include individuals such as Jeremy Jaech, the founder of Visio and Mike Maples, a former executive vice president of Microsoft.
Aries Technology
Aries Technology was organized in Lowell, Massachusetts in November 1984 by Larry McArthur, Richard Miller and several other ex-Applicon and Computervision managers including Gerald Christopher, Peter Pritchard, Dr. Jack Horgan, Arthur McCray and Jerry Sabath. McArthur was the only one who had not previously worked for one of the early CAD vendors. He had been president and general manager of Gould’s Measurement Systems Division.
McArthur was Aries’ president and CEO, Miller headed up marketing, Christopher finance, Pritchard sales, Horgan product development McCray software development and Sabath hardware development. The company raised $22.5 million in venture funding over the next three years including an investment from Eastech Limited Partners, one of whose principals was Fontaine Richardson, a founder and former vice president of Applicon.
The company’s objective was to provide software that could be used during the conceptual phase of product design. The term they used to describe this process was “predictive engineering.” Two years after being founded, Aries introduced its first product, the IBM PC AT-based Aries ConceptStation, at AUTOFACT ’86 in Detroit. Both bundled (AT200) and unbundled (AT1200) versions were sold with prices starting at $32,000 for the unbundled version and $49,900 for a bundled configuration. The early ConceptStation systems required a Aries-built Graphics Engine in order to achieve reasonable interactive performance on the PC AT.
In an attempt to provide an “open system” Aries selected Microsoft’s Xenix implementation of UNIX as its PC operating system. The early Aries’ application software included a precise solids modeler, kinematics analysis and finite element modeling as well as other analysis software. A Design Rule Processor enabled engineers to tailor this process to incorporate the design steps most applicable to the product being worked on. A lower cost version of the ConceptStation, the AT1100, was introduced a few months later with prices starting at $21,850.
Over the next few years, Aries developed partnerships with a number of other software firms including Swanson Analysis Systems, Mechanical Dynamics Incorporated, MacNeal-Schwendler Corporation (MSC) and Autodesk. As a result of these relationships, Aries began to include subsets of analysis programs such as Swanson’s ANSYS and MDI’s ADAMS in its ConceptStation software. The company also began to support most commonly available UNIX workstations as well as Intelbased PCs. As the hardware performance increased, the need for a custom graphics accelerator decreased and Aries ceased manufacturing its proprietary Graphics Engine.
In August 1989, Aries signed an agreement with Ford Motor Company under which Ford invested $6 million in the company and agreed to purchase an unspecified amount of Aries software products. This turned out to be an important relationship in that Ford had previously established a major technology project, Alpha Simultaneous Engineering. This was a 450-person organization under the leadership of Dr. Howard Crabb[6] whose mission was to develop improved products and processes that could be transferred to the rest of the company. Much of their efforts centered around the use of ConceptStation as the conceptual design tool that could help the company significantly reduce design time as well as create better products.
A major product change occurred in November 1991 when Aries announced that it would incorporate the ACIS solids modeling kernel in the ConceptStation, replacing its proprietary modeler. This turned out to be a problematic decision in that ACIS in 1991 was not ready for prime time. At this point in time, ConceptStation consisted of about a dozen software modules including:
- ConceptSolids (ACIS-based solids modeler)
- ConceptParametrics (parametric design)
- ConceptFEM (finite element modeling with automatic mesh generation and post processing)
- ConceptFEA (a subset of the ANSYS analysis package • ConceptCompose (drawing production)
- ConceptDraw (drawing dimensioning).
In July 1992, Aries signed a significant joint development and marketing agreement with MSC. A few months later, Miller was made executive vice president and chief operating officer of Aries. A number of new products were introduced that linked Aries and MSC software together more tightly than before.
The next big change occurred in September 1993 when Aries was acquired by MSC and became the MSC/Aries division of that company. McArthur moved to Los Angeles and assumed the title of chief operating officer for MSC and Miller continued to run the Aries division in Lowell. McArthur left MSC after about a year and worked for a period of time at SGI as director in mechanical industry marketing. Later, he became president and CEO of Saxonyx, a company that developed information management software for the drug industry. Miller stayed for another year before leaving to become an industry consultant.
The company’s plan was to position MSC/Aries primarily as a graphic pre- and pos-processor for MSC’s analysis software. This concept changed after MSC acquired PDA Engineering about a year later. PDA’s PATRAN software for pre- and postprocessing FEA models was substantially more mature and had a larger installed base than did the Aries software. As a result, PATRAN became the more heavily promoted package and MSC/Aries faded into the background although some customers were still using it six or eight years later.
Ashlar
Ashlar was founded by Dr. Martin Newell in 1988 after he left Cadlinc, another company he help start in 1981 as described below. Newell had also worked at the CAD Center in Cambridge, England and then at the Xerox Palo Alto Research Center (PARC). He was well recognized as one of the industry’s leading authorities on graphical user interfaces. Other ex-Cadlinc managers who were involved in Ashlar included Grant Munsey and Dan Fitzpatrick. Ashlar was funded in part by Hambrecht and Quist which had high expectations for this new startup. Bill Hambrecht, the head of Hambrecht and Quist sat on Ashlar’s board of directors for a number of years.
The company’s initial product, Ashlar Vellum, was significant predominately because of the package’s user interface. Newell’s intent was to create a design package where the interaction between the user and the software flowed in a natural rhythm. The focal point of the Vellum software was patented technology the company called the Geometric Inference Engine. This software formed the basis for Vellum’s user interface which was referred to as the Drafting Assistant. It used a technique called a “Smart Cursor” to speed user interaction by inferring what the user might want to do next. As an example, if the user placed one end of a line near a circle, the logical next step might be to make the line tangent to the circle. If the user had a different intention, this operation could easily be overridden.
Initial versions of Vellum were implemented on the Apple Macintosh computer with a Windows PC version following in the early 1990s. Unfortunately, Apple owned a software group at the time called Claris which also sold a two-dimensional drafting package called Claris CAD. Therefore, it was not particularly interested in helping to promote the Ashlar software.
The first released version of Vellum handled two-dimensional design. It was followed in early 1992 by Vellum 3D, initially for the Macintosh and later that year in a Windows version. This new software soon became the company’s primary focus. Vellum 3D extended the Drafting Assistant into the Z dimension, enabling users to create graphics on the equivalent of a three dimensional isometric grid. Ashlar also added a graphical trackball display. By rotating the trackball with a graphic cursor, the user could rotate the model being worked on in any combination of the three axes.
The major drawback of the software in the early 1992 time frame was the lack of any surface or solid geometry capabilities. Hidden lines had to be removed manually at a time when most competitive systems did it automatically. In addition, there was limited capability to create assemblies. The two-dimensional version of Vellum sold for $1,995[7] while the three-dimensional version was $2,495[8]. In the first three years, Ashlar sold about 5,000 copies of Vellum. Then in August 1993, the Claris Corporation subsidiary of Apple withdrew Claris CAD from the market and recommended that its customers purchase a low-cost upgrade to Vellum. This move provided Ashlar with several thousand new users.
During the company’s early years, Newell was both the company’s chairman and chief technology officer while day to day operations were run by Jack Hendren, the company’s president and CEO. Hendren had earlier been with CADAM, Inc. where he led that company’s EDA business unit.. In November 1994, Frank Puhl, the former president of CADAM, Inc. joined Ashlar’s board of directors.
By the mid-1990s, Vellum was a well respected product but one that still did not have a lot of market traction. Some users, including Burt Rutan, the designer of advanced aircraft at Scaled Composites including the recent Space Ship One, were enthusiastic about the software’s capabilities as a conceptual design tool. Ashlar simply could not match the marketing clout of Autodesk and as a result the company became a niche player in the industry.
Vellum 3D Version 3.0, introduced in 1996, boosted Ashlar into a new realm of design tools with NURBS surfaces, shading, hidden line removal, and interfaces to higher-end solid modeling products offered by other vendors. Ashlar was still a fairly small company with about 20 employees at its Sunnyvale, California headquarters and another 12 in Japan. There were also three to four people at CADSoft Solutions in Dallas, TX who were helping develop ACIS-based Vellum Solids, which was released in early 1998. It was priced at $4,995 when combined with Vellum 3D. The company, by then, was basically being run by Nathan (Nat) Natarajan, its executive vice president, who had joined the company in 1993 from Autodesk.
In 1994, Ashlar filed patent infringement suits against Structural Dynamics Research Corp. (SDRC) and Diehl Graphsoft. The suits alleged that the graphical user interfaces used in their respective products, I-DEAS Master Series and MiniCAD, violated a pair of patents held by Ashlar related to the Geometric Inference Engine and interactive drawing system technologies. Ashlar contended that the SDRC’s “Dynamic Navigator” found in I-DEAS Master Series and Diehl Graphsoft’s “SmartCursor” found in MiniCAD made inappropriate use of its technology. Ashlar had negotiated licensing agreements with a number of other companies regarding use of this technology.
SDRC eventually won this case when the patents in question were ruled invalid although the case dragged on for years as Ashlar repeatedly appealed court verdicts.
In 2000 Ashlar moved its operations to Austin, Texas and new versions of the Vellum software were periodically released for both the Macintosh and Windows platforms. Robert Bou became president and then in early 2005, the company was acquired by Vellum Investment Partners which consisted of Bou and his wife Julie. This was followed by the opening of a software development office in Kiev, Ukraine.
While the company name is still Ashlar Corporation, it tends to use the term Ashlar-Vellum when it describes itself. Ashlar’s products consist of Graphite ($995) for two dimensional drafting and Argon ($995), Xenon ($2,995) and Cobalt ($3,995) for three dimension design where the latter two incorporate solids modeling. Ashlar’s licensing agreement allows a user to install the software on multiple machines (i.e. a PC at work and a Apple computer at home) as long as only one license is being used at a time. For users who need the software for short periods of time, the company offers annual and monthly licensing agreements.
Automation Technology Products (CIMPLEX Corporation, Technology Answers) Automation Technology Products (ATP) was started in April 1983 by Robert Benders, the former president and CEO of Calma, John Benbow, vice president of product development at Calma and Lem Bishop, the chief financial officer at Calma.. Between 1983 and 1987, the company raised a substantial amount of venture funding from investors including The Mayfield Fund, Arthur Rock and Hambrecht & Quist. Benders was CEO of the new company, Benbow was senior vice president, technology and Bishop was vice president of finance and administration.
ATP’s plan was to develop a comprehensive design, analysis and manufacturing system based on parametric solids modeling that ran on IBM mainframe computers, initially using that company’s VM operating systems and 5080 graphics terminals. The company’s software was also one of the first products to incorporate the concept of feature-based design and manufacturing. Rather than developing this software in a vacuum, the company signed technical cooperation agreements with Ingersoll Milling Machine Company and the Vought Aero Products Division of LTV Corporation.
The software product was called CIMPLEX and it consisted of feature-based solids modeling, analysis, manufacturing and data management modules. The CIMPLEX software enabled the user to work with three-dimensional shaded and edge-highlighted solid models as well as with wireframe and hidden line removed images.
In retrospect, selecting IBM mainframes for the software’s primary platform may well have been a fatal mistake in that UNIX workstations were starting to make a significant impact on technical computing. At the time, ATP was led to believe that IBM was planning to introduce a VM workstation much as Digital eventually introduced VMS workstations. At IBM, it just never happened. The IBM mainframe decision was further complicated when prospects pushed the company into porting the software to the MVS/XA operating system. This turned out to be a substantial task and for a time involved a third of the company’s R&D staff. Selecting PL/1 as the programming language also turned out to be a problem as it did at Applicon.
For the most part, ATP developed the entire CIMPLEX suite of software rather than licensing external components. This was probably an additional contributing factor to the company’s eventual downfall. Developing solid modeling, finite element modeling, manufacturing and data exchange software would have filled any company’s plate. But in support of these applications, the company also wrote its own database program, rewrote IBM’s disk handling routines and created its own VM and MVS command language. CIMPLEX was fairly expensive software. The mainframe version of the basic design module was priced at $100,000 while the entire suite was $350,000.[9]
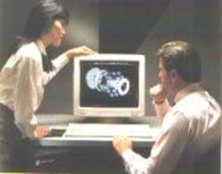
Ralph Ezard, who was working for ICL in England, was recruited by Benbow in 1984 to run the company’s consulting services business and Jay Orlando, previously with Computervision, was hired as vice president of sales. Peter Marks, formerly with SDRC where he was general manager of product planning and marketing, joined ATP in February 1985 as vice president of product planning and marketing. The company closed its first sale to Ingersoll in late 1985. Over the next several years its customers included Northrop, Sikorsky Aircraft, Boeing and Chrysler Corporation. As with earlier technical partners, these companies also worked closely with ATP in defining and testing the company’s software.
Benders resigned as CEO in June 1986 and subsequently became president and CEO of Megatek Corporation, a vendor of high performance graphics terminals owned by United Technologies, the same company that once owned Calma. Benders was replaced a few months later by Dr. Russell Henke, the president and general manager of Gould Incorporated’s Imaging and Graphics Division. Henke had earlier been executive vice president of Applicon and president and COO at SDRC. (see chapters 7 and 17).
A major task facing the company was porting the CIMPLEX software to UNIX. This was done in two steps. First, the software was modified to support Silicon Graphics workstations as an alternative to the IBM 5080. SGI produced a PL/1 compiler for its workstation systems that enabled ATP to port the full suite of CIMPLEX software to run in native mode on SGI workstations.
In 1987, Henke negotiated a $5 million investment in ATP by Chrysler for a 10 percent interest in the company. It was too little, too late, however. The company continued to struggle for the next two years before it finally filed for Chapter 11 bankruptcy in the latter part of 1989. By then, investors had poured a total of nearly $36 million into the company with very little return on their investment. One result of the bankruptcy proceedings was that ownership of the CIMPLEX software was transferred to a new company, CIMPLEX Corporation, which was financed by a $1 million investment from Morgan Stanley. The new CEO was Ted Sarbin who was new to the CAD industry.
For the next 15 years development of the CIMPLEX automated manufacturing software continued although at a somewhat reduced rate of investment. From 1990 until 1998 the company’s president and CEO was Jerry Robertson. Up through at least 1996, this software was referred to as Manufacturing Analyst. CIMdata felt that the company had some of the leading software for what is referred to as generative machining but that CIMPLEX never seemed to be able to become a significant factor in the NC industry.[10] The company also developed some effective NC verification software under the direction of Peter Atherton.
In 1998 the CIMPLEX technology was acquired by Technology Answers, Inc. and the software was renamed Cimskil. The current version of the Cimskil allows a user to import a CAD model and using data describing the organization’s NC machine capabilities, automatically generate optimized tool paths. The software does this by recognizing model features such as slots, bosses, pockets, etc and selecting the best tool and machining method for that feature. Users can override any aspect of the automatically generated tool path and insert their own tool selection and procedures.
An article in the April 2002 issue of Modern Machine Shop described one project where Cimskil was used to program a 5-axis machine tool for a set of parts that had previous been done on 3- and 4-axis machines. The results were impressive. Working with Cimskil, the part programming took from a third to a tenth of the time compared to conventional NC part programming and production time was also a half or less of the previously recorded time.[11] Much of the software development was done under contract to the U.S. Department of Defense which was interested in being able to rapidly produce aircraft spare parts.
BruningCAD
Bruning was a division of AM International that sold engineering supplies and reproduction equipment. In April 1981 it began selling a low-cost drafting system called Easydraf2 that was based on two-dimensional drafting software licensed from Graphcon.
A complete system, which sold for $69,500, included a Hewlett-Packard 9845B desktop computer with a 13-inch raster display.[12] This was subsequently replaced by HP 9000 Series 200 computers with either a 9-inch or 12-inch color display.
Graphcon was started in 1977 by Livingston Daniels in Tulsa, Oklahoma. Its Easydraf software was available on Tektronix 4050 graphic systems as well as the HP 9800 series. AM International acquired Graphcon in July 1983 and Daniels became president and CEO of the renamed BruningCAD. In September 1983, Lou Epstein who had previously been with Tektronix and Intergraph, joined as vice president of sales and marketing.
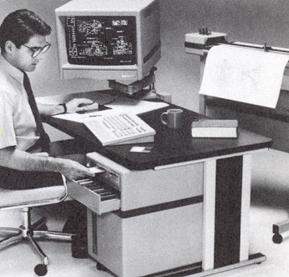
During the next several years, BruningCAD developed its own workstation built around a Motorola 68000 microprocessor, a 19-inch 16-color 1024×768 display and a 14.5MB disk. Two version of the software were offered, Easydraf2 Architectural and Easydraf2 Mechanical. Prices started at $41,900 which was considerably higher than comparable PC-based system.
In October 1984, AM International, which was in the process of emerging from bankruptcy, folded BruningCAD into the rest of the Bruning operation in order to reduce overhead expenses. A year later, the company’s CAD-related staff had been reduced from 46 to just 15 people and the remnants of this activity were sold to Holguin Corporation of El Paso, Texas. At the time, there were perhaps 1,500 Easydraf2 systems installed worldwide, 900 of which were in the U.S. Mutoh Industry Ltd. acquired the Japanese rights to the software. Although Holguin maintained the staff in Tulsa for a period of time, the business eventually faded away.
Cadkey (Micro Control Systems, Baystate, Kubotek)
This company was founded in 1981 in Windsor, Connecticut by Livingston Davies and Peter Smith as Micro Control Systems. Its first product was a threedimensional digitizer called the Perceptor. This was followed by a similar device called the Space Tablet. In 1982 the company introduced a simple software package that enabled users to view the scanned data as three-dimensional isometric or perspective images. The package, which ran on both Apple II and IBM-compatible PCs, was called Space Graphics and sold for just $475.
The company launched CADKEY in 1985 as a PC/DOS program partially to utilize the data generated by its three dimensional scanners. It targeted mechanical designers, especially those who were creating products that involved NC manufacturing operations but were also interested in producing quality mechanical drawings. CADKEY’s share of the PC CAD market peaked in the late 1980s at about 14 percent, behind AutoCAD and VersaCAD. CADKEY was a functionally rich three dimensional wireframe design and drafting package. Many customers, including Boeing, purchased it to complement the high-end design systems they also used.
By 1992, the company was doing about $12 million per year and Livingston Davies recruited Malcolm Davies, who had recently left Autodesk, as president.[13] Livingston Davies and Peter Smith left their day-to-day management roles at the company although they remained members of its board of directors. In an attempt to jump-start its business momentum, the company reduced the list price of the CADKEY software from $3,500 to $495 and DataCAD (an architectural drafting package it had acquired several years earlier) from $2,000 to $150. This greatly increased the number of users. As an example, the DataCAD user base went from a few thousand to over 50,000 in less than 12 months.
By late 1994 it was obvious that the market was not as price-elastic as expected and overall revenue was not growing. Malcolm Davies left and Livingston Davies returned as president and the price of CADKEY edged up to $795. In early 1995, Cadkey released CADKEY for Windows and before the year was over shipped 25,000 copies.
The company also marketed several third party packages as part of its product line including FastSURF from a company by the same name that incorporated NURBS surfaces and DRAFT-PAK, a mechanical drafting symbol library developed by Baystate Technologies, one of the company’s dealers. In late 1995 the company was also developing ADVANCED MODELER, a solid modeling program that used the Shapes geometric kernel from XOX Corporation. At the start of 1996 the company underwent a substantial retrenchment and shifted to a software publishing business model and CADKEY development was moved to India. Baystate was signed up as the master distributor for CADKEY.
In mid-1996, Baystate, headed by Robert Bean and located in Malborough, Massachusetts, acquired all rights to the CADKEY package and related Cadkey software products. At that point, there were about 200,000 copies of CADKEY in use. One of the first steps Bean took was to replace the XOX geometric kernel with ACIS from Spatial Technologies.[14] In March 1997, Baystate began selling CADKEY 97 that incorporated ACIS 2.1 solids modeling. The price was now $1,995, up substantially from a few years earlier but still half the cost of competitive systems such as SolidWorks or Autodesk Mechanical Desktop.
A year later, Baystate acquired FastSolid and FastSURF from a joint venture consisting of FastSURF Incorporated and Advancing Geometrics. A combination of CADKEY, Draft-Pak, FastSolid and FastSURF was sold as the CADKEY DESIGN SUITE for $3,995 while the base package remained $1,995. Baystate changed its name to CADKEY Corporation later in 1998.
With CADKEY 99, the company had a reasonable modeling solution although it still did not incorporate parametric definitions nor was assembly modeling easy. The program’s modeling capabilities were quite fast since CADKEY 99 did not incorporate a history tree describing how the model was constructed. The downside was it increased the effort required to modify models. CADKEY also began using the Web as a sales vehicle in late 1999. In December 2001, the company announced a totally redesigned package called CADKEY GraphX Version 20 that incorporated object-oriented software techniques, the HOOPS graphics routines and ACIS 6.3.6.
While its products were improving, the company itself hit a major snag in 2003.
Back in 1991, Baystate had been sued by another vendor of add-on CADKEY software, Harold L. Bowers, who operated as HLB Technologies. HLB accused Baystate of copying one of its software products. The case dragged on for 12 years but was finally decided in HLB’s favor in 2003. Baystate was required to pay HLB $5.27 million ($3.87 million plus interest), money that Baystate did not have. In August 2003, Baystate filed for Chapter 11 bankruptcy.
Initially, it was thought that International Microcomputer Software, Inc. (IMSI), the vendor of TurboCAD, would acquire the company. In November 2003, Kubotek, a Japanese company that had acquired a 17 percent interest in Baystate in 1996, purchased the company for $3.6 million. HLB got about $750,000 as a result of this deal. The company was renamed Kubotek USA with Naotake Kakishita as president and Bean as chief operating officer. The CADKEY product itself was renamed KeyCreator.
CalComp Systems (ISICAD)
CalComp Computer Products was founded by three engineers from Rockwell’s Autonetics Division in 1959. Initially focused on military research, the company launched the industry’s first incremental digital plotter in 1961. By the early 1970s it was the leading manufacturer of digital plotters and had expanded into other areas including plug-compatible peripherals for IBM mainframe computer. This latter activity involved the acquisition of Century Data Systems and was a financial disaster that is outside the scope of this book.
The data storage business was sold to Xerox in 1979 and the company, itself, was acquired by Sanders Associates in 1980. In addition to its own product line of graphics terminals, Sanders manufactured the 3250 display for IBM during the early and mid 1980s. This business eventually dried up when IBM introduced the 5080 raster graphics system. Most of the company’s plotter sales were in support of other companies’ CAD systems. Sanders grouped together the CalComp Systems business described below, the CalComp plotter business, the Talos digitizer business which it had also acquired and its own graphics terminal business in a single organization and marketed all these products under the CalComp brand name.
CalComp began the development of its own CAD system in 1975. The company’s first CAD product, the IGS-500, was introduced in 1979, about the same time that CalComp Systems was established. The IGS product line also included the IGS-300 and the IGS-400. These systems were based on a 16-bit minicomputer manufactured under license from a French electronics firm, Société Européenne de Mini-Informatique et de Systèmes (SEMS), a division of Thomson-CSF. Each terminal incorporated a high speed graphics processor called the Picture Processor which handled operations such as pan and zoom locally. Each terminal contained a 250KB high-speed memory that held the entire active drawing. The basic unit had a 15-inch monitor with 416 by 300 resolution. A 20inch unit was 1024 by 768 resolution was also available.
The basic IGS-300 was intended to be a satellite system to an IGS-500. It had a 192KB memory, a 40MB disk, a 15-inch low resolution graphics display, and a separate alphanumeric display. The IGS-400 incorporated a hard disk drive, dual floppy drives and supported one or two terminals. The IGS-500 was a more powerful system capable of supporting six or more local terminals or remote IGS-300 systems. A high resolution 20inch display was also available. Basic systems ranged from $90,000 to $160,000 while additional terminals cost $55,000 each with the smaller display. A color raster display was introduced in mid-1982 for $78,000.
The IGS software handled two-dimensional drafting fairly well. One problem was that the computer being used was not generally available to other commercial accounts and CalComp had to create its own operating system as well as a FORTRAN compiler. Another problem was that the company offered few task-specific applications other than architectural drafting and piping and instrumentation diagrams (P&IDs).
In mid-1984, CalComp Systems introduced a new product line, the System 25. It was based on a Masscomp computer and the CalComp built Picture Processor. The initial Masscomp systems used dual 10-MHz Motorola 68000 microprocessors, UNIX and Ethernet. The typical configuration included an alphanumeric display, a 20MB disk and either a 20-inch monochromatic or 19-inch color display. The software supported basic drafting functions with an emphasis on facilities planning and architectural design.
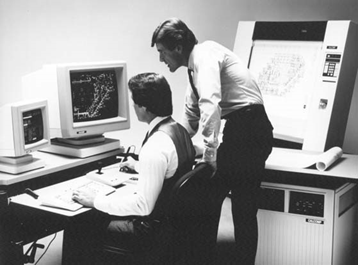
The System 25 software was functionally identical to the earlier IGS software. Each Masscomp computer was capable of supporting two workstations. A single system with a monochromatic terminal and a CalComp 945 plotter had a list price of $95,000. A second workstation cost $$37,000.
The management staff in mid-1985 consisted in part of:
- William Conlin – president of CalComp Computer Products
- Louis DeBartolo – vice president and general manager of CalComp Systems
- William O’Brien – group vice president, marketing and sales
- Jim Gowan – vice president and general manager, international
- Doyle Cavin – vice president, technology
- Joe Fornataro – vice president, system sales
- Warren Winterbottom – vice president, OEM product sales (previously vice president of marketing for the Systems division)
Conlin eventually joined SDRC’s board of directors after retiring from CalComp. O’Brien[15], Gowan and Cavin were all former Tektronix executives while Winterbottom went on to work for both Intergraph and Bentley Systems.
CalComp Systems never had much more than about $30 million in annual revenues. In mid-1985, the CalComp Systems Division of Sanders Associates acquired the CADplan software product line from Personal CAD Systems (P-CAD) for $7.5 million and renamed it CADVANCE. This software initially sold for $2,500 per copy. The acquisition did not go well and Sanders sued P-CAD for $22 million claiming that the company had misled it about the financial health of its AEC business prior to the acquisition.[16] A major problem that CalComp faced trying to sell CAD systems and software was that it competed with turnkey CAD systems vendors who were some of CalComp’s largest customers for plotters and other peripheral devices. Sanders Associates was acquired in 1986 by Lockheed which also owned CADAM, Inc. When Lockheed ran into it own financial problems, it sold off several divisions including CADAM. It was expected that CalComp was also going to be sold but either no buyer emerged or Lockheed changed its mind and kept the company. For the next few years CalComp did fairly well as an independent division of Lockheed focused on plotters and other peripheral devices.[17]
CalComp pulled out of the CAD systems business in May 1987 when it sold CalComp Systems to ISICAD based it Ellwangen, Germany and subsequently focused its resources on three primary product lines: plotters, printers and digitizers. ISICAD opened an office in Anaheim, California and marketed CADVANCE for a number of years. The president of the U. S. operation was John Arnold.
CalComp continued to produce a wide range of plotters using just about every technology currently available including increasingly popular inkjet units that were quickly replacing pen plotters and expensive electrostatic devices. Lockheed merged with Martin Marietta in 1995 to form Lockheed Martin.
CalComp Computer Products and Summagraphics merged in July 1996 and became CalComp Technology, Inc. This new entity assumed Summagraphics’ position on NASDAQ with Lockheed Martin owning about 90 percent of the new company. The next few years saw CalComp Technology’s sales slowly decline as the company struggled with new inkjet technology and increased plotter competition from HewlettPackard. Trading in CalComp Technology stock was terminated in January 1999 and the company was liquidated in May 1999.
CADVANCE software was acquired in 1995 from ISICAD by Furukawa Information Technology, Inc., a software distributor located in Anaheim, California. Founded by Takashi Furukawa, the company continues to sell CADVANCE, currently priced at $1,995 per copy. See section below on ISICAD.
Cimlinc(Cadlinc)[18]
Cadlinc was founded in April1981 by John West who had previously been involved with the sale of NC supplies and Mike Sterling, the founder of Systems Associates, a manufacturing consulting company established in 1973. The latter company was the U. S. distributor of an NC software package, Graphical Numerical Control (GNC) and a surface geometry package, Polysurf, both developed by the CAD Centre in Cambridge, England. The GNC software was also sold by Prime Computer. In the process of starting Cadlinc, Systems Associates was folded into the new company. West was primarily the public face of the company while Sterling became vice president of product development for the new company.
The third key member of the start-up team was Dr. Martin Newell who had earlier been associated with the CAD Centre in Cambridge and then at the Xerox Palo Alto Research Center (PARC) where he worked on interactive graphic systems with John Warnock who subsequently co-founded Adobe Systems. While Cadlinc was initially headquartered in Elk Grove, Illinois, Newell stayed in Palo Alto and ran the company’s research center there while Sterling ran other software development from Troy, Michigan. Eventually, the company’s operations were consolidated in Itasca, Illinois.
In four rounds of funding, the company raised $24 million in venture capital from a number of investment firms including Kleiner, Perkins, Caufield and Byers and The Hillman Group.[19] The company’s early products fell into three categories. Initially, it manufactured its own UNIX workstations built around the Motorola 68000 microprocessor, Ethernet and a proprietary graphics processor. It also developed design and drafting software and adapted the GNC NC software to work on the Cadlinc workstation. It probably can lay claim to being the first vendor to sell turnkey CAD/CAM systems on networked UNIX workstations since the Apollo workstations being used by Auto-trol Technology and Calma were not true UNIX systems.
According to Sterling, he knew Jim Clark, the founder of Silicon Graphics, and attempted unsuccessfully to get Cadlinc’s financial backers to fund Clark’s early graphics work. This was about six months after Auto-trol had likewise turned down an opportunity to work with Clark as discussed in Chapter 9.
Throughout the 1980s Cadlinc invested considerable resources in its proprietary workstations at a time when other turnkey vendors such as Calma, Computervision and Auto-trol Technology were switching to industry standard workstations manufactured by Apollo Computer, Sun Microsystems and others. While, its workstations and user interface were fine tuned for its own software, building computer hardware, including a proprietary floating point processor, turned out to have a negative impact on the company. Cadlinc always seemed to be playing catch-up to other workstation vendors. For example, for some time after Apollo had switched to Motorola’s 68020 microprocessor, Cadlinc was still using the 68000.
The company’s systems were reasonably priced. In mid-1985, a CIM Station (a basic workstation with 2.5MB of memory, a 30MB disk and a 19-inch 256 color monitor) sold for $39,500. Basic design software was an additional $10,500 while surface design and NC software packages were $9,500 each. One can assume that packaged solutions sold for less than the sum of these prices. The company also sold the CIM Manager, a server with up to 800MB of disk storage. Very little third-party software was available.
The company’s strongest marketing points were that West and Sterling had been involved in the NC business for over ten years and the software’s user interface was one of the best then on the market. West was a very dynamic individual and the company received substantial positive press coverage. In November 1985, the company changed its name to Cimlinc. The following year revenues reached $25 million with over 200 employees and everyone expected the company to go public. While the company’s revenues subsequently increased to over $35 million (about half hardware and half software), the IPO never happened.
In 1986 the company changed the system nomenclature to Power CIM. The new workstation used a 68020 processor, a Motorola 68881 floating point processor and a separate 68000 to control input/output. The system had 4MB of memory, an 86MB disk (expandable to 2GB) and a 19-inch 1024 by 792 color display. This was one of the first systems where the user interface consisted primarily of on-screen menus and a mouse. The software was renamed CIM CAD and included solid modeling functions. The manufacturing software was called CIM CAM. Monochromatic workstations started at $11,990 and color workstations at $16,990. CIM CAD software was $4,495 while CIM CAM was $6,495.
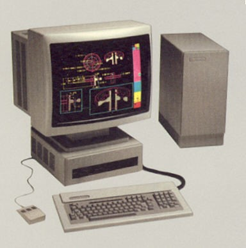
By late 1987 the company realized that it could no longer compete in the workstation market and Cimlinc became a pure software vendor. PCs were coming on strong and the sales force was finding itself spending a considerable portion of its time defending the company’s hardware strategy. Cinlinc ported its software to Sun Microsystems SPARCstations and in mid-1989 the company reduced its software prices by as much as 77 percent. A Sun workstation with basic CAD software sold for just $19,500.
In 1990 the company was split into two operating units, the AMT (Advanced Manufacturing Technology) division which continued to maintain its CAD/CAM applications and a new group that began to pursue information management applications. The design and NC packages were renamed ExpertCAD, ExpertCAM and ExpertCAD 3D with prices ranging from $2,995 to $8,995. The software was supported on both Sun UNIX workstations and on Windows PCs. AMT also offered a more advanced UNIX software solution for tool and die production called ToolDesigner that was initially priced at $10,000.
Gradually, Cimlinc began to refocus its energies in the data management area. Its target was managing the flow of design and manufacturing information with a product called LINKAGE which was introduced in 1991. This software was built around a macro language, ScriptLINK, used in its CAD/CAM software. LINKAGE ran on UNIX workstations at a time when it probably should have been ported to the PC. Mike Sterling left the company around 1995 due to the change in the company’s direction.
The AMT division of Cimlinc was acquired for $6 million by Softech in late 1997 which it still operates it as this is being written. Among other products, Softech is also the current vendor of CADRA. By 2001, the data management portion of Cimlinc simply disappeared as a company.
CoCreate (Hewlett-Packard Mechanical Design Division)
Hewlett-Packard was an early vendor of minicomputers and desktop graphics systems used for engineering design and analysis, either as a supplier to various turnkey systems vendors or by selling this equipment directly to end users. The two centers of activity for desktop computer systems were Fort Collins, Colorado and Boeblingen, Germany.
From an application point of view, Fort Collins concentrated on electronic design and drafting, especially electronic schematics. HP spent a significant amount of energy trying to develop electronic CAE software internally. This effort, led by C. Richard Moore, who subsequently left to become CEO of Valid Logic, was terminated in October, 1984. HP then acquired Salt Lake City, Utah-based Cericor in late 1985 for $32.5 million. By 1990, this operation proved incapable of competing with companies such as Mentor Graphics and the EDA business was closed down.
Separately, HP’s facility in Boeblingen began developing mechanical software. The first product, introduced in 1980, was an object-oriented two-dimension package called HP Design. It used parametric techniques that proved to be hard to use. Although they added a FEA package from a software firm in England and a NC package from another vendor Germany, HP Design was not widely used outside of HP itself. This package focused on design tasks at a time when customers were looking for desktop drafting solutions. Some of the problems HP had with the parametric features of this software led it down a development path that avoided history-based software solutions as described below.
In late 1981, HP introduced a new product, HP Draft. This was a drafting package the company licensed from Skok Systems, a South African software firm. HP licensed the package for resale to mechanical users while Skok continued to sell it to AEC users. The HP development staff in Boeblingen, under the direction of Tillman Schad, worked from about 1981 to 1984 developing a new package specifically intended for mechanical drafting called ME Series 10.
At about the same time, HP restructured this operation as its Mechanical Design Division (MDD). In addition to ME 10, MDD also developed a three-dimensional design package using the Romulus solids modeler. Introduced in 1985 as ME Series 30, it was primarily an analytical modeler with no free-form surface capability. The price in the U. S. was $14,500.
To satisfy the need for three-dimensional surface modeling, HP introduced ME Series 50 in late 1985. This package was based on Graftek (a division of Burroughs at the time) software. (See section on Graftek below.) The timing was bad in that HP earnings had been declining and in a cost-savings move, ME 50 was withdrawn from the market within nine months of its introduction.
A typical ME 10 systems sold for about $40,000 including an HP workstation. At the time, both MDD and the electronic CAE systems were managed by HP’s Design Systems Group which was also responsible the company’s engineering workstation business. The company also sold a reduced function version of ME 10 called ME Series 5 which sold for about $20,000 including hardware. The latter product was not particularly successful in that there was growing interest in PC-based solutions such as Autodesk’s AutoCAD which sold for less than half the cost including hardware and software.
The Design Systems Group was managed by Bill Parzybok while the electronic engineering activity was run by Larry Porter and the mechanical engineering operation in Boeblingen was run by Tilman Schad. At about the same time, HP became a major player in the engineering plotter business and also acquired Apollo Computer, significantly increasing its share of the engineering workstation market.
The company’s entry into the CAD software market put it on a collision course with many of Apollo’s OEM customers who were not particularly pleased to be competing with one of their primary suppliers. HP tried to dampen objections without much success by establishing a separate sales force for its CAD systems.
In early 1992, HP renamed the existing products Precision Engineering/ME 10 and Precision Engineering/ME 30. At the same time, it introduced a new solids-based system called Precision Engineering /SolidDesigner. This latter package was initially based upon Spatial Technology’s ACIS geometric kernel. At the time, HP owned about a 10 percent interest in Spatial. Being an early adopter, HP had to develop a fair amount of add-on technology to ACIS, especially in the surface modeling area. HP proceeded down its own development path and never implemented newer releases of ACIS. Within several releases, little of the original ACIS code remained in SolidDesigner.
SolidDesigner differed from most contemporary CAD systems that used history trees to maintain the relationships between graphic features. It used an approach called dynamic modeling that allows users to manipulate geometry irrespective of what was done to the model earlier. There are pros and cons of both approaches – suffice it to say that the HP approach was different than most other systems on the market. SolidDesigner retained many of the functional characteristics of ME 30 except that it no longer supported tablet menus. A multi-dial function box was used to pan, zoom and rotate shaded models on HP workstations. Detailed mechanical drafting continued to be done with ME 10. Solid Designer software prices started at $7,500 which was competitive with PTC’s Pro/ENGINEER.
Separately, the company marketed a PDM package called WorkManager which was an upgraded version of an earlier package called the Data Management System. WorkManager was implemented to work with data from design and drafting systems other than just the ones sold by HP. The intent was to provide a data management solution that did not require a dedicated system administrator.[20]
The friction between HP and its OEM customers in the mechanical CAD market eventually led HP to restructure MMD as a separate wholly-owned subsidiary in 1996 called CoCreate with Schad as president. In September 2000 CoCreate was acquired from HP by two European investment firms, 3i PLC and Triton Fund, and the company’s employees. The two investment firms probably owned over 90 percent of the company. Schad continued as CEO of the newly independent company which was still located in Fort Collins, Colorado. The company’s chief operating officer was Gert Deiss and vice president of product development was Ulrich Mahle, both of whom were long term HP and CoCreate employees.
In the late 1990s CoCreate began promoting a new collaborative engineering package called OneSpace that enabled engineers and others located at geographically separate locations to work together on the same design. One participant controlled the design review session while other participants viewed any changes made to the product model. This control could be shifted between participants although changes could only be made by someone who actually had the design software on their computer. Eventually Solid Designer was renamed Designer Modeling, ME 10 became Designer Drafting and WorkManager morphed into Model Manager. By 2006 the software was being fully developed using Microsoft’s .NET platform and it no longer retained any vestiges of its UNIX roots.
Schad was replaced as CEO in March 2002 by William Gascoigne who had been vice president of worldwide marketing at Applicon and more recently executive vice president of worldwide operations at SDRC. Hansjoerg Pleggemars, who joined the company in 2000 as CFO was appointed COO in July 2006. At the same time, ownership of the company changed once again when HBK Investments L.P., a large U.S.-based hedge fund, acquired CoCreate.
From 2000 through 2006, CoCreate’s revenues were in the $75 million per year range although profits improved significantly during the period. One reason revenues stagnated was that the company began offering its software on a monthly subscription basis in addition to selling fully paid-up licenses. While this generated many new customers, it did defer some revenue to future years. The company’s headquarters were basically split between Fort Collins and Sindelfingen, Germany with its approximately 300 employees about evenly divided between Europe, The U. S. and Asia.
Ownership of CoCreate changed once again in December 2007 when PTC completed the acquisition of the company for about $250 million. At the time it committed to continue support of CoCreate’s software as stand-alone products as well as integrate the technology with its own products. At the time of this latest acquisition, CoCreate had about 5,000 customers.
Cognition
Other than the fact that it has exhibited impressive staying power and has been run by some of the CAD industry’s early pioneers, I probably would not have included Cognition in this chapter. Cognition Incorporated was founded in February 1985 by a group of 11 experienced industry managers led by Philippe Villers, a founder of Computervision as well as Automatix, a manufacturer of robotic and artificial vision systems. Villers had started Automatix in 1980 along with Mike Cronin who had been vice president of sales and later vice president of R&D at Computervision. In 1984, investors in Automatix felt a change in management was needed and Cronin replaced Villars as CEO of the company.
Villars, being a serial entrepreneur, started Cognition to focused on the development and marketing of mechanical computer-aided engineering (MCAE) solutions. Among the other founders were George Stienke, vice president of marketing who was formerly executive vice president of marketing at Intergraph, Kenneth Schroeder, vice president of research and development who was formerly manager of General Electric’s Industrial Electronics Development Laboratory, Robert Light, product line manager for MCAE who was formerly technical manager of MIT’s CAD Laboratory and Douglas Wilson, manager of systems architecture who was formerly a manager of MIT’s project Athena, a 1,000 terminal computing network. Other founders and early employees had equally strong backgrounds.
Based on Villers reputation within the financial community, the company was able to raise $15.5 million in two rounds of funding during its first two years including $2 million from the founders. One has to assume that much of the latter amount came from Villers. Investors included Harvard Management Corporation, MIT, and Eastech Limited Partnership. As mentioned above, Eastech was also an early backer of Aries Technology.
The company’s initial product, Mechanical Advantage 1000 (MA1000) was introduced at AUTOFACT ’85 in Detroit that November. The company planned to offer both unbundled software and complete turnkey systems that consisted of a Digital MicroVAX II host and up to five IBM PC AT workstations. The software enabled users to sketch, analyze and optimize conceptual designs. The intent was to have this data passed on to traditional CAD systems via IGES in order to complete the designs and produce engineering drawings.
The MA1000 software was called The Optimizer. It included SketchPad, MathSolve, first-order analysis tools, online engineering handbooks and a data management tool called the Intelligent Notebook. MathSolve equations could be linked to specific dimensions defined with SketchPad. The engineering handbook content resulted from an agreement the company negotiated with McGraw-Hill. A three-seat MA1000 was priced at $130,000. Unbundled Optimizer software was $37,500.
After some development delays, the company began shipping MA1000 systems in late 1986. Revenues in 1986 were only $730,000 and with 95 employees it was burning up cash at a rapid rate. A higher performance system, the MA1500/GPX, using the Digital VAXstation II/GPX was introduced in late 1986. While these systems demonstrated very well, they just did not seem to create the necessary level of interest among potential buyers who were mostly still trying to automate basic drafting tasks.
The early expectations were that Cognition would take off like a rocket. It never happened. One problem was that the technology appealed to individual engineers but senior managers, those who controlled budgets, were still focused on automating basic design and drafting tasks. George Stienke resigned in early 1987 and the company started looking for ways to expand its product offerings. One area it focused on was cost estimating. The resulting product, Cost and Manufacturability Guide, was eventually a key part of the company’s survival as a viable business entity. Over time, the company phased out of the hardware business and became a pure software play.
One aspect of this transition was the acquisition of SuperCads, Inc., a software firm started by Shyamal Roy in 1981. The SuperCads software was a three-dimensional wireframe package. Cognition marketed SuperCads without a great deal of success.
By early 1988 the company was in substantial financial difficulty and Automatix, under Mike Cronin, acquired the assets of Cognition Inc. and hired most of the company’s remaining employees. Automatix ran the former Cognition activity as a subsidiary legally named Supercads, Inc. but utilizing the Cognition trade name. This subsidiary, of which outside investors owned about 29 percent, continued to struggle with revenue running between $1 and $2 million annually. Cronin stepped down as CEO of Automatix in 1990 to become full time CEO of SuperCads. He was replaced at Automatix by Ofer Gneezy.
By July 1992 Automatix had incurred losses on this activity of $4.3 million and it sold the Cognition business (still legally SuperCads, Inc.) to Cadema Corporation for $1.8 million in cash and notes and Cronin took over running Cadema.[21] Before this transaction, Cadema was nothing more than a shell corporation which had earlier been engaged in medical research activities. It had some cash left over from these previous endeavors and was looking for opportunities to invest it. This new ownership did not last long and in May 1993 Cadema sold the Cognition assets to Cronin and a group of other investors.
Over the next few years, Mechanical Advantage was refined to provide three main capabilities: tolerance analysis, functional modeling and parameter analysis. In the 1999 time frame, about 30 percent of the Mechanical Advantage customers were using the software just for tolerance analysis. Prices started at $12,000 per license.
Cost and Manufacturability Guide eventually morphed into a product called Cost Advantage that assisted companies in predicting manufacturing costs before a design was completed. A key component of this software was called Model Builder. It provided the information needed to link manufacturing costs to design features. Cost Advantage software started at $20,000 for Model Builder plus one floating user license. Additional software was $5,000 per copy.[22] This turned out to be Cognition’s key product activity for the next few years.
Today, the surviving company, Cognition Corporation, still markets Mechanical Advantage and Cost Advantage but with increased emphasis on two new initiatives, Cognition Cockpit and Enterprise Cost Management (ECM). According to the company, Cockpit is a tool set and knowledge management system which can be used to support Design For Six Sigma. ECM is a product cost management system. In 2006, Dale Gallaher was named president of Cognition. Mike Cronin is still chairman and CEO while his son David is manager of business development.
Control Data Corporation (Control Data Systems, ICEM Technologies)
Control Data Corporation (CDC) was one of the early manufacturers of largescale scientific computers including one of the first “super computers,” the CDC 6600, introduced in 1964. CDC first became involved with CAD solutions in 1963 when it acquired the rights to Itek Corporation’s Electronic Drafting Machine and established its Digigraphics Division in Bedford, Massachusetts as described in Chapter 6. In the late 1960s, CDC realized that the Digigraphics operation was “wine before its time” and shut the money-loosing operation down.
In the early 1970s, CDC was a profitable computer vendor selling a broad range of machines to scientific research centers and manufacturing companies. It was also a leading participant in the business of selling time-sharing services. Given the communication capabilities then available, it was not feasible to provide highly interactive applications such as CAD on a time-sharing basis.
Alan Christman joined CDC in 1970 as general manager of manufacturing industry marketing. Over the next few years the company began to look at ways it could provide more complete design and manufacturing solutions to its customers. One option that was fairly quickly rejected was to resurrect the Digigraphics activity. CDC also decided that it did not want to develop CAD software from scratch. The result was that the company signed a license agreement with Manufacturing & Consulting Services (MCS) in the mid-1970s for that company’s AD-2000 software as described in Chapter 15.
AD-2000 formed the basis of what CDC called its ICEM (Integrated Computeraided Engineering and Manufacturing) program. The software was implemented on the company’s 32-bit mid-range computers as well as on its 60-bit supercomputers such as the CDC 6600. The primary user terminal at the time was the Tektronix 4014. CDC established its own software group to extend the capabilities of AD-2000 as well as support the company’s computer systems. Working with MCS-provided updates to AD2000 proved to be difficult for CDC and, in early 1982, the company acquired a fully paid-up license for AD-2000 much as Auto-trol Technology did around the same time. At this point the name for the product was changed to CD/2000 and then later ICEM DDN.
While the company put substantial effort into making CD/2000 a viable product, the impression most people had was that CDC was simply using the software to help sell mainframe and minicomputer computer systems. The company invested a fair amount of effort in making the software run efficiently on its computer systems but relatively less on actually improving CD/2000’s functional capabilities. CDC also continued to provide technical time-sharing services through a division called CYBERNET, particularly in the area of structural analysis and electronic circuit design.
One area of interest was solids modeling which the company saw as an emerging technology. Christman remembers reading an article in Business Week that described how Boeing was experimenting with Synthavision solids modeling software from MAGI. CDC subsequently licensed Synthavision and created a link to CD/2000 for exchanging data between the two packages. The company ended up selling relatively few copies of Synthavision, primarily because of performance issues. Christman, who is now a principal at CIMdata, described the software as “watching paint dry.”[23]
Eventually the software expanded to encompass a broader range of engineering tasks including data management and NC applications. The company also added software, ICEM Electronics, that enabled engineers to merge electronic design with mechanical design. A single user system utilizing the company’s Cyber 120-40 computer with a subset of the ICEM software was introduced in mid 1983 for $50,000. The Cyber 120-40 was actually a repackaged Data General S20 computer. A six-user system started at $161,000.[24]
Major customers included Bendix in Kansas City, Los Alamos National Laboratory, Volkswagen and Fischer-Price, the manufacturer of children’s toys. In June 1986, CDC acquired an NC software firm, ICAM Technologies, of Pointe Claire, Quebec to expand its NC capabilities. Also, about the same time, CDC began selling a product line of UNIX workstations, the CYBER 910-300 Series, which were basically repackaged Silicon Graphics workstations.
In the late 1980s CDC began to put increased focus on PDM software. The company’s product was called EDL (Engineering Data Library). Initially it was implemented on CDC computers but by mid-1991 CDC was also supporting Sun and SGI UNIX workstations with Hewlett Packard, IBM and Digital versions in development. EDL software was sold on a per workstation basis with the basic network information manager priced at $3,500 per seat. A complete system including a release manager and product structure software was $6,500 per seat.[25] The portion of CDC that included the company’s CAD/CAM and PDM activity was subsequently renamed Control Data Systems, Inc. or CDSI.
As described in Chapter 17, CDSI and SDRC established a joint venture in 1992, Metaphase Technology, Inc., to pursue the PDM market. CDC contributed the EDL software and a number of individuals to this venture. SDRC soon became the driving force behind Metaphase in regards to both development and marketing. Then in late 1996, SDRC bought out Control Data’s interest in Metaphase.
In 1993, CDSI became ICEM Technologies with ICEM DDN (previously called CD/2000) as the company’s primary product. One change was increased interest in surface geometry software developed by the company’s European operation in Frankfurt, Germany. ICEM SURF started out as an internal development project at Volkswagen. It soon gained a reputation within the automotive industry as one of the leading tools for body styling and eventually it became ICEM Technologies’ primary product with ICEM DDN deemphasized. ICEM SURF quickly gained a reputation as a leading package for automotive styling, particularly for creating and editing what that industry referred to as Class A surfaces. The company also renewed its focus on manufacturing software with the introduction of PART, an NC package that used feature recognition and generative expert system technology. Another package, ICEM Solidify was introduced that facilitated the conversion of wireframe data to ACIS-based solids models.
In 1998, ICEM Technologies was acquired by PTC as described in Chapter 16, primarily for its ICEM SURF software. PTC spent several years attempting to integrate ICEM software with Pro/ENGINEER and eventually decided that it had more on its plate than it could deal with. ICEM was sold to a group of English investors in August 2002 and was subsequently operated as ICEM Ltd. in Southampton, England. In 2005, the company expanded its product line with the introduction of ICEM Shape Design (ISD), a parametric modeling package developed on Dassault Systèmes CAA V5 architecture. Then in mid-2007, Dassault acquired ICEM for the equivalent of $69 million.
Gerber Systems Technology (Gerber Scientific)
The Gerber Scientific Instrument Company was founded in 1948 by H. Joseph Gerber, the 1994 recipient of the National Medal of Technology. Initially the company produced mechanical data reduction instruments used before electronics and computers revolutionized that field. Over the years, Joe Gerber was awarded 675 patents, including a number after he passed away in 1996 at the age of 72. Gerber is perhaps best known today for the precision cutting machines he developed for the apparel and shoe industries.
Gerber went public in 1961 at $6 per share and shortly thereafter developed the photoplotter which revolutionized the production of printed circuit board artwork. For many years the company was the leading vendor of photoplotters. The company also began manufacturing numerically-controlled sewing machines and CAD/CAM systems.
The company’s name was changed to Gerber Scientific, Incorporated in 1978. By 1980 the company had overall revenues of about $75 million and its stock was listed on the New York Stock Exchange. Gerber Scientific was organized as a holding company with four primary operating units.
- Gerber Scientific Instruments – precision plotting systems including photoplotters and precision pen plotters.
- Gerber Systems Technology – CAD/CAM systems.
- Gerber Scientific Products – custom computer-controlled manufacturing system.
- Gerber Garment Technology – layout and cutting systems for the garment industry.
In addition to a wide range of plotters and photoplotters, Gerber Scientific Instruments (GSI) marketed a PCB layout and artwork system called the PC-800. Various version of this system sold for $35,000 to $50,000 plus the cost of a plotter and/or photoplotter. The latter typically sold for $60,000 to over $500,000. The PC-800 used a Hewlett-Packard 2100 Series 16-bit minicomputer with 32KB of memory and dual 8-inch floppy disks. The user terminal consisted of a relatively small monochromatic raster display and a Gerber 8200 digitizer. Typical operation involved the user manually laying out a circuit board, digitizing the layout, editing the data, plotting the layout for checking purposes and then outputting the data to either an on-line or off-line photoplotter.[26]
The PC-800 was a fairly simple system but it worked well. By 1981, the company was selling $12 million annually of PC-800 products and had an installed base of 250 systems.[27] By 1987 it had installed 775 such systems. GSI also sold flatbed plotters as large as 6 feet by 24 feet and drum plotters up to 48 inches wide. These were all extremely accurate and reliable machines.
Gerber System Technology (GST), originally Gerber’s Systems Division, became a quasi-independent company in 1981 with Wilbur (Bill) Mann as president. It was 80 percent owned by Gerber Scientific and 20 percent by the public. GST went public in 1981 at $12.50 per share. At the time it had about 300 employees and was doing over $17 million in annual revenue. Gerber was an early licensee of Pat Hanratty’s ADAM software which served as the starting point for the company’s mechanical design and NC software, first introduced in 1974 as the IDS-3. About 100 of these systems were sold before it was replaced by the IDS-80, launched in April 1980.
The IDS-80 was a traditional multi-user turnkey CAD system that used a HewlettPackard 1000F minicomputer (also called the 2117F) as its host with up to 512KB of main memory. Each workstation also included a smaller HP 1000E computer to handle local graphic functions. Since early systems used Tektronix storage tube displays, this configuration enable the software to redraw images on the displays without putting a heavy processing load on the host computer. A color raster version of the workstation using Lexidata components was introduced in 1982. An IDS-80 system with a single workstation was priced at $190,000 while a six workstation system cost about $450,000.
Although still based on the early ADAM software, the IDS-80 incorporated a more sophisticated database capability and Gerber-developed NC software. The system was particularly adept at machining compound curved surfaces. Autopost was software used to create NC post processors. The company also marketed a finite element modeling package based upon an early version of SDRC’s Supertab software. This was partially a byproduct of a joint working relationship between the two companies in the late 1970s.
In April 1982, GST introduced the Autograph series, a lower cost single user system that also used the HP1000F. The company sold both low resolution monochromatic and high resolution color versions of these workstations which could be linked together using the IBM 2780 communications protocol. The black and white units sold for $79,000 including mechanical design and drafting software while the color unit was priced at $120,000. The NC software was particularly good and Gerber’s systems were well accepted by customers doing tool and die production.
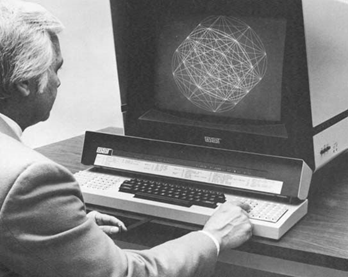
(Note lever under keyboard used to control cursor and the two 40-button function keyboards bracketing the alphanumeric keyboard)
A sheet metal package developed by a user organization, Pako Corporation, was announced at AUTOFACT in November 1982 and began shipping a year later. This software, which sold for $16,800 on a IDS-80 system, unfolded a sheet metal part and automatically created a drawing with bend lines and dimensions in a single batch operation.
In April 1985, the company introduced a new system called the SABRE-5000. It was a 32-bit UNIX turnkey system that came in two versions. A low-end system was built around a Masscomp MC-500 computer, 2MB of memory, a Lexidata LEX 90 color 19-inch display with 1280 by 1024 resolution and a separate alphanumeric display. The high-end version used a Hewlett-Packard HP-9000 Series 500 computer with 3MB of memory. The Masscomp-based system, including IDS software, was $79,000 while the HP system was $98,000. Solids modeling, sheet metal design, FEA and NC software was available as options. At the time, GST was generating about $22 million in annual revenue or about 10 percent of Gerber Scientific’s total.
The SABRE systems suffered from several problems. At a time when other turnkey vendors were switching to standard workstation platforms, Gerber decided to build its own, relatively expensive, workstation. Supporting both Masscomp and HP computers with relatively low volume of each added considerable expense to the company’s R&D.
GST also marketed the SABRE-PC which included the Micro Control System’s CADKEY software described earlier. These system sold for $25,000 which was far more than other PC-based CAD systems.
While the company was a serious contender for mechanical business in the early and mid 1980s, it seemed to loose momentum in the latter part of the decade. By 1990 the CAD business had faded away and this group began focusing on graphic design systems for the shoe industry. GST was then merged with Gerber Scientific Instrument to form Gerber Systems Corporation.
Although no longer in the CAD systems or software business, Gerber Scientific continues as a viable company. Revenue from 1985 through 1994 oscillated between about $200 million and $300 million. During the past ten years revenue has climbed to over $600 million while the company has a market value of only $250 million.
GRAFTEK (Graphics Technology Corporation, Unisys CAD/CAM)
GRAFTEK was formed in Boulder, Colorado in 1980 by a group of software developers and marketing people previously employed by Auto-trol Technology (see Chapter 9). The initial group included Jim Starnes, Ron McElhaney and Milan Marz although Starnes kept a fairly low profile due to a legal dispute with Auto-trol in regards to his leaving that company. Venture funding was provided by American Research and Development (the company that helped start Digital Equipment), Adler and Company and Jesse Aweida, the founder of Storage Technology Corporation.
While recruiting potential employees, McElhaney used the name “Sidney Greenstreet,” an actor from the 1940s whose credits include a supporting role in “Casablanca.” Among those recruited from Auto-trol were Dick Sowar who eventually became vice president of research and development and Chad Alber.
Sowar was the key hire in that he had a strong background in both software architecture and graphics. Although he never completed all the requirements for a Ph.D., his thesis subject was “Parametric Design in a CAD/CAM Environment.” This was nearly six years before Sam Geisberg began the development of Pro/ENGINEER at PTC.
Like most companies in the CAD industry in the early 1980s, their business plan was based on both building graphics hardware and developing application software. The company’s first workstation was the Meteor introduced in 1981. This was followed by the Meteor II in April 1985 that included a 19-inch 16-color monitor (expandable to 256 colors) with 1024 by 768 resolution and an optional graphics processor capable of handling local three-dimensional rotations as well as dynamic pan and zoom. The Meteor II could be used as a terminal for 32-bit minicomputers from Hewlett-Packard, Digital Equipment and Systems Engineering Laboratories with the SEL system being the company’s preferred platform.
The company’s primary software was GMS (Geometric Modeling Software). It was a three-dimensional wireframe and surface modeling package that used commands entered via a keyboard, function keypad or data tablet. GMS was based on MCS’ AD2000 which was a logical move considering that McElhaney had worked for MCS before joining Auto-trol and that at Auto-trol he had been responsible for implementing AD2000 for that company. Up to 20 different views of a model could be generated and selectively displayed. The drafting software included a library of “intelligent symbols” that could be placed, oriented and sized in drawings.
GMS was complemented by analysis software, a graphics programming language called AGILE (Algorithmic Graphic Interface Language), finite element modeling software and NC software capable of handling 5-axis machine tools. A third party injection molding analysis package, OptiMold from Optimold Limited of England, was also available from the company as was a solids package, Romulus, developed by Shape Data, a subsidiary of Evans & Sutherland located in England. Eventually, GRAFTEK became Shape Data’s largest OEM customer. Customers tended to be companies needing mechanical design and NC operations, particularly in the tool and die industry.
While the company’s software was well regarded within it target markets, GRAFTEK never built up the sales momentum to be considered a serious player in this industry. By 1983 it was obvious that the company was struggling and the company’s investors hired Cy Lynch as the new CEO. It was then acquired by Burroughs Corporation in 1984 for $23 million. Shortly thereafter, Lynch resigned from the company to return to Texas and Burroughs brought in Stanley Eaton as the new CEO. Sowar stayed with GRAFTEK until 1986 at which time he left to start Spatial Technology. At its peak, the company probably had about 60 or 70 employees.
A number of GRAFTEK’s developers led by Ron McElhaney left at that point and formed UNICAD with the intent of creating a software development platform that could be used to build either proprietary or commercial CAD software. He was joined by Bert Hertzog, a graphics industry pioneer and the former head of the University of Colorado Computer Center. Evans & Sutherland was a major investor in this new endeavor. UNICAD never gained much traction and McElhaney subsequently went to work for Autodesk.
In 1986, Burroughs and Sperry merged to form Unisys Corporation and GRAFTEK became Unisys CAD/CAM. In early 1992 GRAFTEK was acquired from Unisys Corporation by Gores Group[28] (Gores subsequently acquired Applicon as described in Chapter 7) which operated the company until it was sold to C-Tech, an Austrian distributor in 1996. C-Tech set up a subsidiary in Boulder, C-Solutions, that continues to maintain and support GRAFTEK’s GMS software now called GMSWorks.
Information Displays Incorporated (IDI)
Information Displays, Inc. (IDI) was one of the earliest vendors of commercial graphics hardware. Founded in 1960, the company manufactured a product line of vector refresh displays. I worked with IDI from 1965 to 1969 developing a graphics system used to control refinery operations at Lago Oil and Transport, an Exxon subsidiary, in Aruba, Netherlands Antilles. The executive vice president of IDI at that time was Carl Machover, a well respected industry pioneer and consultant.
In 1975, IDI was acquired by a Bennet LeBow, who would make an attempt to take over Prime Computer 13 years later. LeBow installed Dr. William Weksel as president and IDI switched its focus to turnkey CAD systems. Its primary product was known as the System 150 and the software, itself, as IDRAW. While IDRAW was primarily sold to AEC users, a separate version called Graphic Design/Illustrator (GDI) was sold to organizations doing technical illustrations. GDI subsequently was renamed ICAPS.
The IDRAW software had more flexibility for creating line art than most contemporary systems. It could shade lines, inset broken dimension lines, create drawings in dimetric or trimetric projections and handle multiple fonts. Line weights were display by adjusting the intensity with which the lines were displayed. Overall, the GDI/ICAPS system contained many features that are routine today but were fairly novel in 1980.
The system used a Sperry-Univac V77-600 16-bit minicomputer that supported four IDI displays. A basic system had just 32KB of memory and a 40 or 80MB disk drive although a 300MB unit with a removal cartridge was also available. This was the same hardware configuration used by Auto-trol Technology in its early systems. A single workstation system cost $150,000 while a four-seat configuration went for $300,000.
IDI also took a business-like approach to financing its systems. You could lease a system for 5% of the purchase price per month with 50% of your payments going towards subsequent purchase. The company also offered a $200 per day rebate if your system was inoperable.
IDI began loosing momentum in the early 1980s. In 1983, the company lost $7 million on revenues of just $10 million. In January 1983, IDI introduced a technical illustration system, CADalyst, that incorporated a new workstation built by the company along with the ICAPS software. The system was plagued with problems and never worked properly. In March 1984, control of the company was taken over by a group of investors led by Leonard Levy who immediately stop production of CADalyst systems and reduced the company’s employment from 185 to about 100.
Levy and his partners had purchased shares of IDI on margin and as IDI’s stock price dropped, they were unable or unwilling to meet margin calls. IDI filed for Chapter 11 bankruptcy in May 1984. In early 1985, the bankruptcy court changed this to a chapter 7 liquidation and the company’s remaining assets were sold off in a series of auctions.
IronCAD (3D/EYE, Visionary Design Systems, Alventive)
IronCAD’s roots go back to a company called 3D/EYE founded in 1981 by Dr. Donald Greenberg and Dr. John Abel, both of whom were associated with the Program for Computer Graphics at Cornell University. At the time, Cornell was one of the leading graphics research centers in the world. 3D/EYE was established to give Greenberg and Abel and their students a vehicle for developing commercial computer solutions.
One of the first such products was a structural steel design and analysis program called STEEL 3D, developed for Auto-trol Technology (See Chapter 9). For the first 12 or so years of the company’s existence, 3D/EYE functioned as a technology boutique doing graphics software work for companies such as Hewlett-Packard. In the mid-1990s, Dr. Samir Hanna, who had been with 3D/EYE since the STEEL 3D days, realized that it was becoming feasible to develop low cost 3D modeling and visualization products that could be used by both professionals and non-professionals. The two enabling technologies were:
- Functionally rich PC operating systems such as Windows 95 and Windows NT which incorporated much of the “house keeping” functionality that previously application programmers had to develop and maintain.
- Solution vendors no longer had to develop entire products by themselves. Modular components such as geometric modeling engines could be licensed at reasonable costs. In this case, 3D/EYE decided to work with Spatial Technology and incorporated the ACIS geometric kernel into its packages.
In April 1995 3D/EYE, which by now was located in Atlanta, Georgia, got Paul Allen, the co-founder of Microsoft, to purchase a minority equity position in the company through Allen’s Vulcan Ventures investment firm. In October 1995, the company began shipping two revolutionary new products, TriSpectives and TriSpectives Professional. The software used a method of building three-dimensional models by dragging and dropping pre-made parametric shapes called IntelliShapes and then subsequently interactively refining them. Users could also build model element using traditional sketching and extrusion techniques. The packages sold for between $300 and $500, far less than SolidWorks or Solid Edge.
3D/EYE started a rather aggressive marketing campaign quoting Evan Yares as saying that TriSpectives was a “Pro/ENGINEER killer” – a statement Yares denies making as quoted. While it was not a replacement for traditional CAD software, TriSpectives was an excellent conceptual design tool. Although a large number of copies of this software were sold, sales did not live up to expectations and in March 1997, the TriSpectives technology was acquired by Visionary Design Systems of Palo Alto, California. Visionary Design Systems (VDS) was founded by David Tiley, a former Hewlett-Packard salesman. Its primary business at the time was reselling CoCreate software described earlier. The 3D/EYE development staff including Samir Hanna stayed in Atlanta. A new version of the software, TriSpectives Technical, was released later that year priced around $1,000.
At the National Design Engineering Show in Chicago in March 1998, VDS introduced a new product that was closer to being a full-function CAD system. Called IronCAD, it was based on the TriSpectives foundation but included more comprehensive geometric modeling capabilities. It had a list price of $3,995 and began shipping that June. Engineering Automation Report was suitably impressed:
“In developing IronCAD, VDS retained and improved upon much of TriSpectives’ ease-of-use but added real geometric modeling under the covers. The underlying method for building geometry is very powerful and unlike any other package on the market. This is probably the easiest program to rapidly develop geometry; it really has to be seen to be appreciated.”[29]
By late 1999, IronCAD 3.1 was being shipped with a list price of $4,995. It was one of the first packages that used both Spatial Technology’s ACIS geometric kernel as well as UGS’ Parasolid. The result was improved interoperability with other software packages. The key aspect of the software was that used a combination of explicit modeling such as CoCreate’s SolidDesigner as well as history-based parametric modeling used by Pro/ENGINEER, SolidWorks and others.
Eventually, VDS changed its name to Alventive then in March 2001 it spun off the IronCAD activity as a separate employee-owned Atlanta-based company also called IronCAD. The company subsequently continued to enhance this software with IronCAD 9.0 released in June 2006. Alventive it self was eventually acquired by BlueSky Solutions in 2004.
ISICAD (Personal CAD Systems, FIT)
CADVANCE was introduced in 1982 as CADplan by Personal CAD Systems (PCAD) of San Jose, California. The company’s drafting software business was acquired by the CalComp division of Sanders Associates in March 1985 for $7.5 million and renamed CADVANCE. As described above, CalComp’s CAD systems business unit was sold in
1987 to ISICAD, GmbH of Ellwangen, Germany, a wholly owned subsidiary of ISIMAT, a machine tool manufacturer. A new company, ISICAD, Inc. was established in California to market the software acquired from CalComp. Under ISICAD, CADVANCE software sold for $3,295. The initial head of this operation was John Arnold who had spent 18 years with CalComp, most recently as director of product development for the Systems Division.
The CADVANCE software was sold primarily for architectural and facility management tasks. The company also launched a solids modeling package called Solid Vision and a Motorola 68020-based workstation, the PRISMA. Neither of these latter two products ever seemed to achieve much sales momentum.
CADVANCE used an integer data structure that resulted in relatively fast graphic operations without the need for a graphic accelerator. The software also worked directly with Ashton-Tate’s dBase database management system. CADVANCE 5, released in 1992, was one of the first CAD packages adapted to the Windows operating system, initially for Windows 3.1. Over the years, the software has predominately been used for architectural design and drafting. Users have historically liked its ease of use and the ability to rapidly train new users.
Among the key executives in the early 1990s was Yoav Etiel who was later hired by Bentley Systems as its vice president of marketing. Over the next few years, ISICAD struggled to compete against AutoCAD and MicroStation. In 1995, Furukawa Information Technology (F I T) was established by Takashi Furukawa and John Milius in Anaheim, California for the express purpose of acquiring ISICAD. Both had previously worked for CalComp. For the next decade, F I T continued to expand the capabilities of CADVANCE and to market it in a relatively low-key manner.
By 2006, CADVANCE 12 was being shipped at a list price of $1,995. A CADVANCE LiTe version of CADVANCE 12 was also available $495. The software was sold directly by the company and through a small group of domestic and international dealers. The company also offered CADVANCE 6.5 which was developed for Windows 3.1 but also runs on Windows 95/98 and NT systems. It was available as a free download from FIT’s web site for users who were using these older operating systems. In mid-2004, over 700 copies of this free version were being downloaded monthly.
Matra Datavision
If this book were being written in Europe, Matra Datavision would undoubtedly deserve an entire chapter. Its impact in the United States was relatively limited, however, and, therefore, it has been relegated to this chapter.
Matra Datavision was the CAD/CAM division of Matra, a broad-based French industrial concern with defense and aerospace operations in the United States. The company’s flagship product was a solids-based CAD/CAM package called EUCLID-IS where the IS stood for Integral Solution. It was initially developed at the French National Center for Scientific Research in the 1970s as a batch-oriented computer programming language and was used on projects such as the Concorde supersonic transport. A company called Datavision was formed to commercialize this technology. The software implemented a boundary representation solid modeler with tessellated surfaces. This latter feature resulted in fairly rapid display of shaded surfaces and hidden line views of solid models once the software began using interactive graphics.
One early customer was the aerospace division of Matra. They liked the product so much that they bought the company in 1980 and renamed it Matra Datavision. In 1981, a U. S. operation was set up in Burlington, Massachusetts, partially owned by Matra and partially owned by the employees. While the European version of the software had been implemented on IBM mainframes, the U.S. version ran on Digital VAX computers using Tektronix displays. The VAX version of the software was licensed for $120,000 to $140,000 depending upon the options selected. Tektronix display terminals were about $15,000 each while a VAX systems capable of supporting eight EUCLID users cost over $550,000.[30]
The company also had an agreement with IBM to resell IBM 4300 computers and 5080 graphic displays running EUCLID but as far as I can tell, this never resulted in any significant number of installations in North America. Like most other CAD vendors in the early 1980s, Matra Datavision also designed and manufactured its own graphics terminals. By 1987 the company shipped over 2,000 of these terminals.
Matra Datavision had a strong relationship with Renault dating back to 1984. A number of technical advances in EUCLID including improved surface geometry and NC machining functions came from Renault under this agreement. Renault subsequently purchased about a quarter of the company and in 1989 its development staff was merged with Matra Datavision’s at a new facility in Les Ulis, France.
In 1988, the company signed an agreement with Digital under which the latter firm became a major distributor of EUCLID systems. This adversely impacted the company’s relationship with other computer manufacturers and eventually it was terminated. Matra Datavision had tailored a number of functions specifically for the Digital hardware and this tended to defocus the company’s development efforts for several years.
EUCLID-IS was built around a solids modeler that combined boundary representation and constructive solids geometry techniques as well as an object-oriented database. In many regards, EUCLID-IS was one of the most advanced CAD systems on the market in the early 1990s. Unfortunately, the company was never able to match its technology with effective marketing. The EUCLID-IS software consisted of about 30 modules. A basic system started at around $10,000 with typical software configurations selling for about twice that. Matra Datavision used a combination of direct sales and dealers. The latter became important when the company introduced a lower-cost system in North America called Prelude/Solids in 1992 which sold for $3,995 and was initially available on Sun and SGI UNIX workstations.
Also in the early 1990s, the company began working on a new development environment called CAS:CADE. It was a C++ tool set that was planned to be used for both internal development and to be licensed to independent developers.
Matra merged with communications giant Hanchette in 1993. Hanchette published magazines such as Road & Track and together with Matra was an $11 billion enterprise of which Matra Datavision was probably a $100 million piece. The parent corporation was subsequently renamed the Lagardère Groupe. Also in 1993, the company launched a PC-based design and manufacturing package called PRELUDE.
By mid-1994, the software was being called EUCLID 3 and the company was supporting a variety of UNIX workstations as well as Digital VAX/VMS systems. The primary workstations being used by customers were those manufactured by Silicon Graphics. In 1994 the company acquired Cisigraph and its STRIM styling and surface geometry software. Within two years, Matra Datavision was doing $160 million worldwide and growing 30 percent annually. By then, the company had 18,500 seats of its software installed at 4,700 customer sites. Its North American business, however, never got much above $15 million annually. The company had 720 employees and its chairman and CEO was Michel Neuve Eglise while the president and COO was Hugues Rougier.
In late 1996, Matra Datavision introduced a new CAD/CAM system called EUCLID QUANTUM that used CAS:CADE as the development environment. It had a very attractive user interface, used object-oriented software technology extensively, incorporated a STEP-compliant data model and contained a broad suite of applications. The basic mechanical design software had an initial list price of $14,900 in the United States. Unfortunately, the execution of this new system did not match the fanfare with which it was introduced and the company’s market position began to slowly deteriorate.
On February 24, 1999, Dassault Systèmes announced that it had completed the acquisition Matra Datavision’s styling software products including EUCLID STYLER, EUCLID MACHINIST, STRIM and STRIMFLOW as well as a license to use the CAS:CADE development tool set for FF 200 million. The intent was to integrate this software into CATIA Version 5. While Matra Datavision retained ownership of the basic EUCLID product, the plan was that while it would support existing users, the company would not solicit additional customers.
Matra signed a separate agreement with IBM to become a reseller and system integrator of Dassault software including CATIA and ENOVIA. The expectation at the time was that Matra would encourage its customers to migrate to CATIA V5. The company was subsequently renamed MDTVISION and continues as a consulting and service company supporting IBM PLM solutions.
Spatial Technology (PlanetCAD)
Spatial Technology was founded in Boulder, Colorado in 1986 by Dick Sowar, who had previously been vice president of research and technology at GRAFTEK. The initial product plan was to develop NC software that worked directly on solid models. Sowar felt that it was a step backwards to build a part model using solids and then reduce the model to its surface representation in order to generate NC tool paths.
The initial funding for Spatial was provided by Fred Nazem who had also been one of the early GRAFTEK investors. He invested $1 million in the company and placed Cy Lynch, who had been CEO of GRAFTEK, as CEO of Spatial with Sowar as CTO. The company formally started functioning in September 1986. The first order of business was to license a solids modeler that could serve as the base for the applications the company planned to develop. Sowar spoke to a number of potential providers including Dave Albert at Vulcan Systems, Peter Veenman at Shape Data and even Sam Geisberg at PTC.
None of these contacts proved fruitful and Sowar and Lynch eventually met in London with the principals of Three-Space Ltd., located in Cambridge, England. ThreeSpace was headed by Ian Braid and consisted simply of himself along with Charles Lang and Alan Grayer – thus the Three in Three-Space. They had earlier been involved in the development of BUILD I, BUILD II and ROMULUS solids modelers as well as the definition of what eventually became Shape Data’s Parasolid. They agreed to create a solids package for Spatial on the understanding that Spatial would turn it into a marketable product.
The NC software was known as Strata which continued as a Spatial product until around 1992. It was the solids modeling component technology, however, that quickly became the company’s focus of attention. Rather than trying to become just another CAD vendor with some neat technology, Sowar decided that there was a significant future in selling component solids modeling technology that others could use to develop end-user applications not necessarily limited to CAD products. Spatial worked with a number of other firms to create a more complete product offering. These partners included Lightworks Design which provided photo-realistic rendering and D-Cubed which provided constraint management software. In fact, Spatial provided the seed money that enabled John Owen to start D-Cubed, a developer of constraint management software.
Meanwhile, Spatial continued to work on Strata. One substantial project involved porting Strata to work with SDRC’s GEOMOD solids modeling package. SDRC paid Spatial $1.5 million for this work.
Although Lynch was CEO, he never moved to Colorado and continued to operate from his home in Texas visiting Boulder every few weeks. In 1987 he was replaced as CEO by Fred Schumacher who had previously been with Control Data Corporation. He was also recruited by Fred Nazem. Schumacher never fit in at Spatial and left within a year.
A search firm then introduced John Rowley to the company and he was hired as president and CEO in 1988. Rowley was an extremely high-energy individual who had previously been with Tektronix, Intel and Digital Research.[31] Around this time the geometric kernel became known as ACIS.[32] This core software component, written in C++, was introduced in 1989. By this point, Nazem alone had invested $4.4 million in the company. This was an unusually situation since, typically, most high tech startups have multiple venture capital firms funding them.
Fairly soon after deciding to market ACIS as component technology the company signed Hewlett-Packard’s Mechanical Design Division as an ACIS licensee and HP purchased a 10 percent interest in the company as part of a $7 million private placement. Other investors included Union Carbide and Allied Signal, both potential users. Fairly soon thereafter Spatial signed Control Data and Autodesk as licensees as well as about ten other firms.
The typical contract called for an initial license fee plus royalties for each application package sold based upon the value of that package. The first contract with Autodesk called for a royalty of $25 per copy of AutoCAD. At the time, Ron McElhany, who had worked with Sowar at GRAFTEK, was Autodesk’s vice president of R&D. Autodesk subsequently asked to renegotiate its agreement with Spatial and sent Len Rand to discuss the situation with Rowley. The two got into an argument over the coming importance of Microsoft’s Windows NT and negotiation broke down. Autodesk subsequently announced publicly that it was looking at alternative strategies.
A key marketing executive until 1996 was Bruce Morgan who, after a stint as ANSYS, would return in 1999 as the company’s president and COO. Morgan was able to get Autodesk back to the table in 1991 at which time they negotiated a new agreement that provided Autodesk with the option of paying $6 per software package or a flat $1 million per year. ACIS was initially used in AutoCAD beginning with Release 13 and eventually became core technology for Autodesk’s Inventor mechanical design package. Until it decided to go its own way a decade later, Autodesk routinely paid the $1 million each year.
While Three-Space developed the basic ACIS geometric kernel, other software was need to flesh out the product. Spatial called these additional modules “husks.” An example was a NURBS surface geometry husk that was being developed by Bob Blomgren at Applied Geometry Corporation in Seattle, Washington. Other husks included software for turning solid objects into thin-shell models, generating shaded images, constraint management, finite element modeling and translators to other data formats. A key feature of ACIS was its import/export format called SAT (Save As Text) that the company published for use by other software developers. ACIS was available for a variety of UNIX platforms as well as PCs running MS/DOS.
For several years, Spatial ran a periodic technical meeting called TECH-EX for licensees and other interested industry participants. The first was in Detroit in 1991 at AUTOFACT, while the next was in Berlin in 1992, then Boca Raton, Florida in 1994 and
New Orleans, Louisiana in 1996. One purpose was to promote a user organization called ACIS Open that in addition to Aries and HP included companies such as Digital, Ford and Mercedes-Benz.
Rowley’s relationship with the company’s major investors deteriorated starting around 1991 and he left the company in 1993. Sowar became CEO while continuing as chief technical officer. Chuck Bay, who had previously worked for Steve Jobs at NeXT Computer and was Spatial’s CFO, became the company’s COO. The company seemed to be riding high. Bentley Systems, SolidWorks and Intergraph were all developing packages using ACIS.
The concept of component software technology was now an accepted strategy in the CAD industry. Jerry Sisson, who had joined the company in a sales management role, became president and COO when Bay left to return to California in 1994. Ron Belcher was vice president of development. Overall, the company appeared to have a fairly strong management team.
Spatial gradually moved from being a marketing company that packaged software developed by others to more of a development company although it was still dependent on other firms for much of the software it licensed. Also, it was taking longer for these licensees to bring products to market than originally expected. Since Spatial’s business model was predicated on royalty revenue from each package sold, the company struggled to generate enough revenue to kept extending ACIS as its customers were requesting. One problem was that end user packages such as Bentley’s MicroStation Modeler demonstrated very well, as long as known problems with ACIS were avoided. End users, however, needed bullet-proof software and ACIS was not yet there.
To facilitate application development, Spatial introduced the ACIS 3D Toolkit in 1994. In addition to ACIS, it included a set of kernel extensions and a development language based on Scheme, a LISP-like scripting language used extensively as an educational tool. By mid-1996 ACIS based software was shipping from Autodesk, Intergraph, 3D/EYE, Applicon and Bentley as well as many point solution vendors. Overall, the company claimed that it had more than 350 licensees who were shipping nearly 60 commercial products.
ACIS 2.0 incorporated improved surface blending, deformable surfaces, the healing of imported geometry and shelling. The latter software was developed by an Indian software firm, Godrej and Boyce, subsequently known as GSSL and now known as Geometric. One major problem was that HP was no longer using new ACIS releases but was making its own extensions to the initial ACIS code it had used in SolidDesigner. Things were going well enough, however, that Spatial went public in October 1996. Morgan, who had left to join ANSYS in 1996, returned in July 1997 as president and COO. ACIS 3.0 was released in mid-1997.
In late 1997, Spatial was hit with the defection of several key customers including Bentley Systems and Intergraph who announced they were switching to UGS’ Parasolid software. Their complaints centered on a combination of functionality and performance issues. In addition, Computervision selected Parasolid for its new DesignWave package. Spatial worked hard to respond to these defections. ACIS 4.0 was released in mid-1998. While there were a number of functional enhancements in areas such as surface blending and lofting, the major focus was improved performance and software reliability. Many tasks were done 40 percent to several hundred percent faster than with ACIS 3.0.
Over the next several years Spatial made a number of acquisitions, especially in the area of data translation and viewing including InterDATA Access, Inc. In addition, Spatial acquired Three-Space, Ltd. and its founders became Spatial employees. The InterDATA acquisition and several licensing agreements with other companies led to an interoperability product called 3D ModelServer and a web-based service called
3Dmodelserver.com introduced in 1999. The latter product was soon renamed 3Dshare.com. The intent was that customers would submit models to Spatial and for a fee based on the model’s size, Spatial would translate and heal the data. Initially, I was very excited about this business concept. Unfortunately, the software never lived up to the hype. Spatial’s revenue peaked in 1999 at $14.9 million but the company lost $2.9 million due to investment in its new on-line services. It was running through the cash raised in its public offering at an alarming rate.
By early 2000, Spatial was focused on two business activities, its software component business which produced the bulk of the company’s revenue and an emerging business of providing data translation and other services on the Internet. The latter services were dubbed PlanetCAD. In August 2000, Spatial agreed to sell its software component business to Dassault Systèmes for $25 million. (After various fees and reimbursement of loans from Dassault, the net was only $17.4 million.) Dassault was not the only CAD company interested in ACIS. SDRC also made an offer worth about $25 million.
The deal with Dassault closed in November 2000. Dassault retained the Spatial name and the remainder of the company was renamed PlanetCAD with Bruce Morgan as CEO. A key part of the new PlanetCAD was software obtained when Spatial acquired Prescient Technologies in July 2000. Prescient, formerly a division of Stone & Webster, was the developer of software that could be used to verify the integrity of mechanical models. This software was marketed by PlanetCAD as Prescient QA.
Dassault continued to operate Spatial as a vendor of geometric kernel technology under the management of Michael Payne, one of the founders of SolidWorks. Interestingly, seven years later, SolidWorks, another Dassault subsidiary, still used Parasolid as its primary geometric kernel. Keith Mountain, who had earlier worked for Computervision, joined Spatial as vice president of marketing in May 2002 and became president and COO in 2004. He replaced Payne as CEO in 2005 Payne left Dassault and started a new company, SpaceClaim, in Concord, Massachusetts that is currently developing three-dimensional modeling software.
PlanetCAD struggled from the start. The company attempted to market a number of on-line services including model quality assurance (also sold as stand-alone software), CAD data translation and healing and rapid prototype cost estimating without much success. Morgan left the company in late 2000 and was replaced by Jim Bracking, who had headed several other high tech companies but none in the engineering software field. In 2001 PlanetCAD had revenues of $1.8 million and lost $12.4 million. Sowar left the company in October 2001 and in January 2002 Bracking was replaced as CEO by David Hushbeck. Sowar subsequently started another company focused on geometry creation called FreeDesign.
The end of the line for PlanetCAD came in November 2002 when the company was merged with Avatech Solutions, a major reseller of Autodesk software. The intent from Avatech’s position was to gain access to the several million dollars in cash PlanetCAD still had and to have its stock listed on the American Stock Exchange by taking advantage of PlanetCAD’s listing. PlanetCAD’s products were of secondary interest. Avatech’s stockholders ended up owning 75 percent of the company which retained the Avatech Solutions name while PlanetCAD’s stockholders received 25 percent.
Avatech split PrescientQA into two products, one version which is still called PrescientQA for high-end systems such as Pro/ENGINEER and CATIA and a separate version called Proof Positive for mid-range systems such as Autodesk’s Inventor. PrescientQA was sold to European-based TDCi in 2003 while Proof Positive was sold to Autodesk in 2005.
think3 (CAD.Lab)
CAD.Lab was started in 1979 in Bologna, Italy by Filippo Zuccarello to offer two-dimension drafting software. By 1997, the company had sold over 10,000 copies of its software to about 2,500 customers, mostly in Italy and had about $34 million in annual revenues. CAD.Lab had also developed a full-function Windows-based solids modeling package called Eureka Gold 97 that incorporated a proprietary geometric modeling kernel.
Zuccarello intended to become a worldwide player in the mechanical CAD market and to do so, he believed he had to relocate to the United States. The company set up a new corporate headquarters in Santa Clara, California in 1997, raised $7 million in new financing from U.S. Venture Partners and hired Joe DeNucci away from SGI to be the company’s president with Zuccarello remaining as CEO. DeNucci lasted just a few months and was gone before the year was over.
Eureka Gold had a clean user interface and easily combined surface defined geometry with solid models. The initial expectation was that this package would sell well to stylists and industrial designers competing against SolidWorks, Solid Edge and Autodesk Mechanical Desktop. The major problem was the fact that at $12,000, it was priced more like Pro/ENGINEER than the products it was most likely to be compared to. When all the functionality included in Eureka Gold was added to other mid-range packages, usually via third party products, the gap narrowed considerably but that was not the way potential users viewed the situation.
In early February 1998 CAD.Lab surprised nearly everyone by naming Joe Costello as chairman and managing director. Costello had been CEO at Cadence Design Systems until 1997 when he resigned and was considered by some as a potential CEO at either Apple or SGI, both of which were looking for new leaders at the time. Costello is a high-energy executive with an imposing physical presence. Although Zuccarello retained the CEO title it was obvious fairly quickly that Costello was really running the company. He was not shy of criticizing competitors and was extremely optimistic about the company’s prospects. He stated in public that the mechanical CAD industry was stagnant and there had been little innovation for over a decade. In November he was formally named CEO.
Costello felt from the start that CAD.Lab offered high end CAD capabilities at a mid range price. That fall he decided to hold a contest to find a new name for the company. For a while CAD.Lab was known (seriously) as The Company Formerly Known as CAD.Lab. By December 1998 the company received over 40,000 entries from around the world. The winner of the $50,000 prize with his suggestion of “think3” was an Italian, Fabio Orsi. The company began calling itself “the mechanical design upstart” and referring to Costello as a “Silicon Valley icon and technopreneur.”
In March 1999, think3 launched a new product line consisting primarily of thinkdesign, a three-dimension wireframe, surface geometry and solids modeling package and thinkshape which added extensive surface geometry capabilities to thinkdesign. The target market was clearly that of moving two-dimensional users of AutoCAD to threedimensional modeling. Rather than selling fully paid licenses, the company initiated an annual subscription model. Including software maintenance and technical support, thinkdesign cost $1,995 annually while thinkshape was $2,995. Richard Cuneo, who was instrumental in developing Autodesk’s reseller channel was hired to do the same for think3. A visualization module, thinkreal, based on software from LightWork Design, cost an additional $350 annually.
think3 placed substantial effort into developing new techniques for training thinkdesign users, especially those who were making the transition from two-dimensional AutoCAD drafting to three-dimensional modeling. The tutorials gave designers an interesting combination of gaming, video demonstrations, and step-by-step instructions for using the actual CAD system to perform tasks. The gaming portion – “The Monkey Wrench Conspiracy” –involved a level of violence more associated with the then popular game Doom. In the course of killing violent enemies, the game required users to repair necessary items by designing replacements or performing other actions that taught solid modeling skills.
In September 1999, Costello personally took over worldwide sales replacing Cuneo. The company began selling its software on the Web at this point. A month later the company launched thinkdesign 4.0 with improved drafting and part library capabilities. During the second half of 1999 the company signed up over 3,000 thinkdesign subscribers. In March 2000 the company announced that it had closed a third round of financing for $20 million. This was on top of the $18.5 million it had raised in 1988, shortly after Costello joined the company.
Like most other companies in the CAD industry, think3 revenue growth slowed with the recession during the early part of the 2000s. There were personnel cutbacks, a switch from focusing on industrial design to machine design and a relocation of the company’s headquarters from Pleasanton, California to Cincinnati, Ohio. The company’s business did continue to grow, however, with revenues of $40 million in 2004. Costello is no longer involved in running the company’s operations but is still chairman of the board. Zuccarello is once again CEO while Fabrizio Giudici is COO. Most of the software development continues to be done in Italy and India.
Unicad[33]
Unicad is significant in that it was one of the first companies to offer component software that other organizations could use to create engineering design and analysis applications that were not available from traditional CAD vendors. The company was founded in March 1983 by Dr. Ronald McElhaney and Dr. Bert Herzog with funding from Evans & Sutherland Computer Corporation.
McElhaney had been in charge of Auto-trol Technology’s mechanical CAD software development activity in the late 1970s. He left Auto-trol in early 1980 to join GRAFTEK as one of that company’s founders. Herzog had been involved with computer graphics since 1963 and was a former professor of computer science at the University of Michigan and the University of Colorado. He was also instrumental in the establishment of SIGGRAPH.[34] Other early employees involved in software development included David Prawel, Chad Alber, Griff Hamlin, Doug Hakala and Phillip Poirier. Dan Woods and Brian Doyle joined about a year later to handle sales and marketing for the company. The company initial planned to offer a graphics software environment called the Universal CAD System that other companies could use to create CAD applications. Hence the name Unicad. The company’s intent was to provide a software toolkit that would handle graphical user interface issues (using a PHIGS library), database management (primarily using Sybase) and geometric modeling including the Romulus solids modeler which was property of E&S at the time.
The initial version of the company’s software was released in late 1984. The target market consisted of companies that wanted to implement specialized graphics applications that were not readily available from traditional software vendors. Early licensees included Westinghouse and the National Bureau of Standards. The latter organization planned to use the software in its Automated Manufacturing Research Facility. According to Prawel, in nine months they had written over 300,000 lines of code. Unfortunately, the rush to demonstrate a complete set of development tools resulted in some relatively unstable software. He describes McElhaney as a brilliant technologist who was always pushing the envelope. As an example, as the programmers were trying to complete programs written in C, he wanted them to begin the transition to C++ which was a relatively untested programming language at the time.[35]
In late 1985 Unicad announced that it would offer a pair of CAD systems itself. Unicad DD/1 (Design-Drafting/1) was to be a three-dimensional wireframe design and drafting system. Unicad M/P/E (Modifiable/Portable/Extendable) incorporated the same user interface as DD/1 plus surface geometry and an optional solid modeling module. The concept was that customers would be able to use the Unicad tool set to modify the basic system to meet their specific requirements. About this time, both McElhaney and Herzog left Unicad and Jose Villalobos took over as president and CEO. McElhaney went to work for Autodesk where he became vice president of technology while Herzog joined Fraunhofer Center for Research in Computer Graphics in Providence, Rhode Island.
For the next several years UNICAD tried to gain traction without much success. In addition to Westinghouse, other key accounts included Framatome, the French nuclear engineering firm, and Jonathan Corporation, a naval defense contractor in Norfolk, Virginia. One of the major problems the company faced was that nearly every one of its customers wanted the software ported to a different UNIX platforms. In 1987 UNICAD’s investors pushed the firms management to find a buyer for the company. Eventually Jonathan Corporation bought the company and moved the operation to Norfolk. Only a few of UNICAD’s technical staff made the move. Many of the others ended up working at Spatial Technology with Dick Sowar. Jonathan primarily used the software for internal projects and eventually the UNICAD technology as well as Jonathan simply faded away.
Visio (Axon, Shapeware, IntelliCADD, Boomerang Technology, IntelliCAD Technology Consortium)
Visio was founded in Seattle in September 1990 as Axon Corporation by Jeremy Jaech (president), Ted Johnson (vice president, product development) and Dave Walter (chief architect). All three had previously been employed by Aldus Corporation where they worked on the development of PageMaker. The name was changed in 1992 to Shapeware, about the same time that its first product, Visio 1.0, began shipping.
The focus was on what the company called “business diagramming.” Visio created “drag-and-drop” pre-drawn shapes called SmartShapes. Users were able to quickly create diagrams such as flowcharts, organization charts, network diagrams and other non-dimensioned drawings using these pre-constructed shapes and connectors. The company changed its name to Visio Corporation and went public in 1995. This initial version of Visio subsequently evolved into a product called Visio Standard.
By mid-1997 Visio Technical, an improved version of Visio Standard, provided considerable capabilities for a package that routinely sold for less than $300. Running on a PC that cost about $3,000, it was capable of handling basic drafting tasks such as electrical diagrams that a decade earlier required CAD systems costing over $50,000 per seat. Visio Technical’s symbol library contained over 3,800 SmartShapes. About this same time, Visio also introduced Visio Maps, a GIS application built on top of the underlying Visio technology. Other versions of the basic Visio software were released in 1997 and 1998 with list prices for the product line ranging from $129 to $995. As described in Chapter 8, Softdesk had acquired a company in San Diego, California called IntelliCADD in 1994. Shortly thereafter, IntelliCAD began developing an database and command clone of AutoCAD called Phoenix. After several years of effort, Softdesk decided to suspend development and a number of the developers set up a company called Boomerang Technology with the intent of acquiring the Phoenix technology from Softdesk.
At about the same time, Autodesk made an offer to acquire Softdesk, effectively putting a stop to plans for selling Phoenix to Boomerang. As part of its approval of Autodesk’s acquisition of Softdesk, the Federal Trade Commission encouraged the sale of Phoenix to Boomerang and the parties entered into a consent decree that provided that for ten years Autodesk would do nothing to hinder the development and marketing of this software or acquire any company that controlled it.
On February 21, 1997, Softdesk sold Phoenix to Boomerang which promptly was acquired by Visio for $6.7 million. Many of the programmers working on Phoenix, had already gone to work for Visio. At this point in time, Visio had annual revenues of $80 million and profits of $20 million. The expectation was that Phoenix would end up being somewhere between Visio Technical and AutoCAD.
The plan was to release Phoenix by the end of 1997 including DWG interoperability with the then current release of AutoCAD and capable of executing AutoLISP routines. The Phoenix nomenclature was dropped before the end of 1997 and the product was renamed IntelliCAD. It used DWG as its native file format and the command structure was similar to AutoCAD. The major exception was that IntelliCAD did not support Autodesk’s ObjectARX . Other than ARX objects, Visio claimed that the software was compatible with AutoCAD from Release 10 through Release 14. The list price was initially expected to be set at $695 with the thought that dealers would sell it for under $500. Several thousand beta test copies were shipped in November 1997. For the quarter ending December 31, 1997, Visio generated revenues of $37 million, up nearly 95 percent over the prior year.
In early 1998, Visio was the driving force behind the establishment of the OpenDWG Alliance (subsequently known as the Open Design Alliance or simply ODA), an industry group focused on reverse engineering Autodesk’s DWG format and making software for reading and writing DWG files available to members of the alliance. One of the first steps the alliance took was to run a full page ad in the Wall Street Journal attacking Autodesk for not making DWG information readily available to other software vendors. Visio had early acquired MarComp, the leading vendor of software tools for reading and writing DWG files and the company subsequently made the MarComp technology available to the alliance.
IntelliCAD 98 was finally released at the National Design Engineering Show in March 1998 in Chicago. As John Forbes, Visio’s vice president of technical products stated “When you launch a new product such as IntelliCAD, you only get one chance to do it right.”[36] At launch, the typical street price was only $349. This was a tremendous amount of technology for a very low price. IntelliCAD had some features, such as the ability to edit multiple drawings simultaneously, that the then current version of AutoCAD, Release 14, did not have.
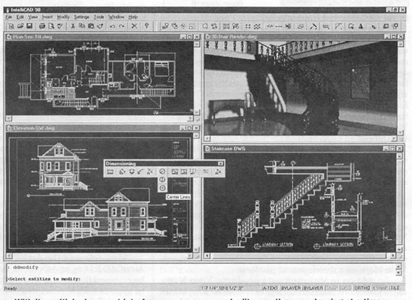
A few months later, Visio began offering Visio Technical Design Suite which consisted of Visio Technical and IntelliCAD 98 for a street price of less than $500. Marketing CAD software did not seem to be a Visio strength and around late-1999, IntelliCAD was turned over to a group of software vendors organized as the IntelliCAD Technology Consortium. The consortium was given a perpetual license to the software and was allowed to sub-license it to anyone who joined the organization. The company’s revenues in fiscal 1999 were $166 million, but it was apparent that Visio was starting to have growth pains.
In September 1999 Microsoft announced that it was acquiring Visio for $1.3 billion or $42 a share, a moderate premium over Visio’s current stock price of $30. Visio became an operating division in Microsoft’s Business Productivity Group, the same organization responsible for the company’s Office software. Both Jaech and Johnson became Microsoft vice presidents.
IntelliCAD, meanwhile continues to be supported by the consortium and is available in seven languages in 30 countries. The organization is managed by a board of directors made up of individuals from the companies that license the software, some of which are interesting stories in themselves if only space permitted. There are over 30 members of the consortium and it is headed by Arnold van der Weide, president who also became chairman of the ODA board in late 2006. Much of the IntelliCAD software development is now done in Russia.