Northwestern Cathodic slashes costs by 70% while manufacturing 60% faster
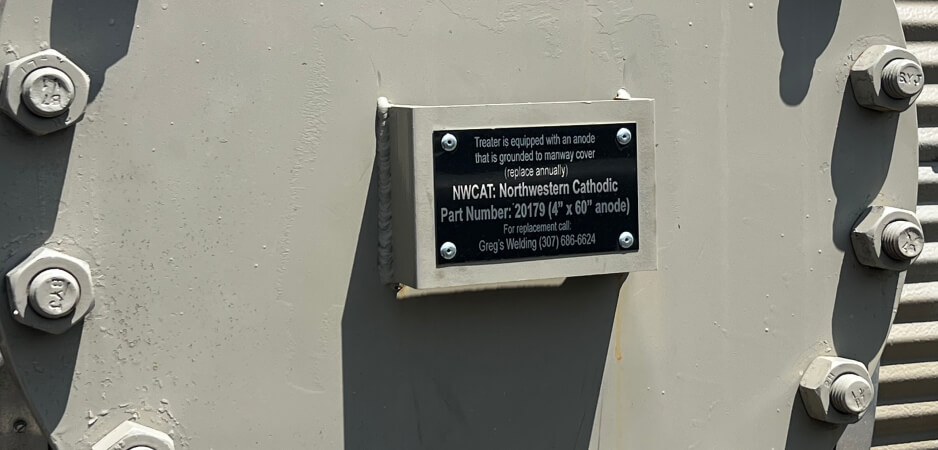
Overview
Without anodes, steel tanks will rust and fail. Though anodes prevent this corrosion, they are typically an afterthought of steel infrastructure manufacturers such as for tanks, pipes, and pilings. This leaves the end user to problem-solve. For businesses looking to provide a solution, the opportunity here is significant: reducing corrosion damage can save the typical economy $300 billion and prevent catastrophic events.
This is where Northwestern Cathodic (NWCAT, or “Newcat,”) lends a hand. “In oil and gas, for example, there are hundreds of oil manufacturers in the US and when you add that all up, you have many different types of tanks that require anodes. Yet very few of them were designed to support anodes,” notes Chris, the owner of NWCAT. NWCAT rises to the demand to set up safeguards not previously available on the market. Learn how the company used Shapr3D to reduce design-to-manufacturing time by over 60% to custom-fit products for clients.
About Chris & Northwestern Cathodic
Northwestern Cathodic is a design-to-manufacturing company specializing in making anodes that prevent corrosion. Chris is the owner and oversees all the design work and prototyping carried out. Overall, the company houses 22 people on the production floor manufacturing products. They make 90% of their products needed by clients to implement or resell anodes for tanks in-house. The company includes sales, administration, design, operations, prototyping, and manufacturing.
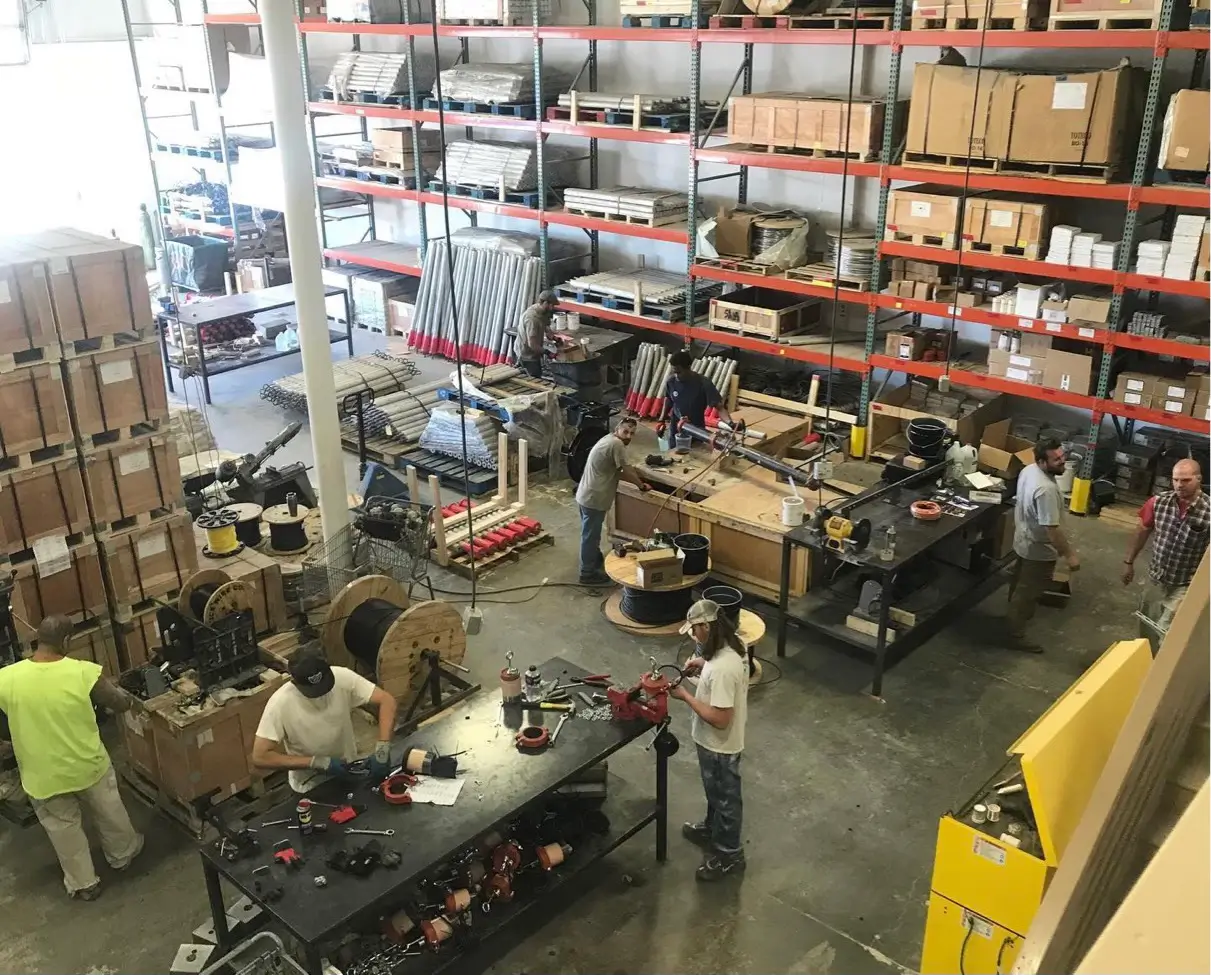
Why Shapr3D
After a 4-month period of back-and-forth with clients and job shops trying to get a product right, Chris was ready for a change. He and the team needed to transition from using 2D Drawings and blueprints to communicating ideas more effectively. Outsourcing prototyping drained company resources and time so he considered bringing prototyping in-house. He turned to CAD, his number one priority to compare the intuitiveness of different software so he set out with one simple test: to draw a globe. Finally, he tried Shapr3D. “I never did draw the globe,” he admits. “It was obvious right off the bat that you could do anything with Shapr3D.” He had found the CAD that met his criteria: fast, instinctive, and inexpensive.
“With Shapr3D, you didn’t need any training. You could draw whatever you needed. Sky’s the limit: that changed everything. What previously took months took a week using Shapr3D.”
Challenges
- Lack of collaborative design limits business operations
- Outsourcing prototyping is expensive and frustrating
- Communicating custom designs to engineers and stakeholders
Solutions
- Streamlined CAD communication makes team members’ work more effective
- Bringing design-to-manufacturing in-house significantly cuts production time
- Quickly finalizing ideas for custom solutions increases productivity & wins deals
Everyone contributes more using Shapr3D
With his own schedule blocked to the last 5-minute increment, Chris fuels the company with tight organization. Once Chris got his hands on Shapr3D, it didn’t take long before the entire company of 22 personnel incorporated the CAD tool into their daily tasks. The company uses Shapr3D as baseline infrastructure to connect each company division: sales, administration, design, operations, manufacturing, and production.
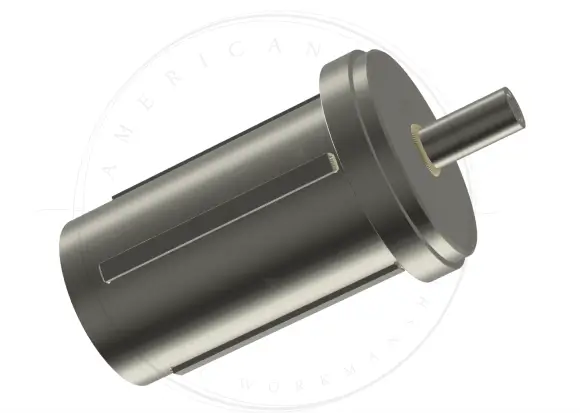
Every aspect of the company utilizes Shapr3D to make their work more efficient and to communicate across divisions. Using 3D models and 2D Drawings, the company has built up a repertoire of communication materials including job sheets, line cards, and assembly operation instructions while also using Shapr3D on the floor to communicate products visually. This enables a direct flow of communication from the client to sales and administration all the way to production, minimizing error and increasing productivity.
All in-house: speeding up product finalization
Bringing design-to-manufacturing in-house has transformed NWCAT operations. A couple of years ago, the company’s process hinged on drafting 2D models in AutoCAD and blueprints to communicate designs to clients and job shops. At that time, a client manufacturing a line of products approached NWCAT for a necessary component.
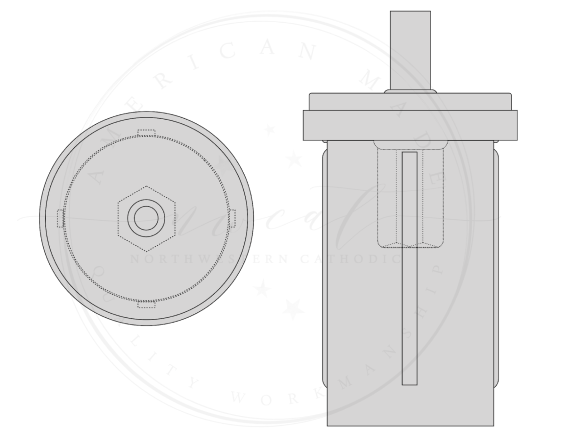
Completing the product was a tiresome process with multiple back-and-forth rounds between the job shop and the client. Overall it took four months to get to the final product. Though the customer was satisfied, Chris was gearing up for a change to increase productivity. He thought, “If I could print 3D prototypes, that’d be cool. How do I do that?” That’s when Chris started using Shapr3D.
“Prototyping is a big part of what I do as the owner and Shapr3D is my primary program for that. If I’m going to design something, I’ve found that designing in Shapr3D is just as fast as designing on a notepad with a pen and you get a much better product and more robust feedback more quickly.”
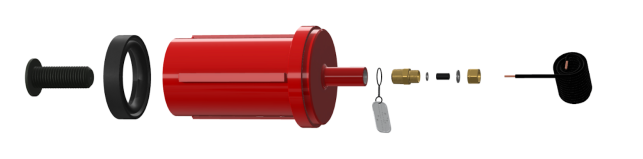
Fast-forward two years and NWCAT’s customer has come back with a need for a revisited product. Now Team NWCAT can do everything in Shapr3D without having to outsource. Chris tests out multiple ideas quickly, test-fits components, and shows models in Shapr3D during meetings to get immediate feedback.
“We were able to design and prototype version two of this item in a fraction of the time and a fraction of the cost. We took design-to-production from six months down to two weeks.”
Altogether, with a quick approval process the team was able to shave off 60% of design-to-manufacture time with a significant reduction in spending. Chris comments, “We spend our time, which is minimal, and on filaments for printers. That’s it.”
Communication in the field wins in meetings & with the bottom line
NWCAT uses Shapr3D on iPad in the field to work with engineers to troubleshoot problems as they arise. Chris recently patented the sixth version of their NWCAT steel mounting cap. Before Shapr3D, the team went through multiple iterations and version six was by far the fastest to complete. Chris and his engineering team could examine component interferences, test different ideas for where a weld should go or how big a weld can be, or what size threads will fit.
Before a product is okayed for production, an engineer inspects the prototype to determine if it meets industry standards.
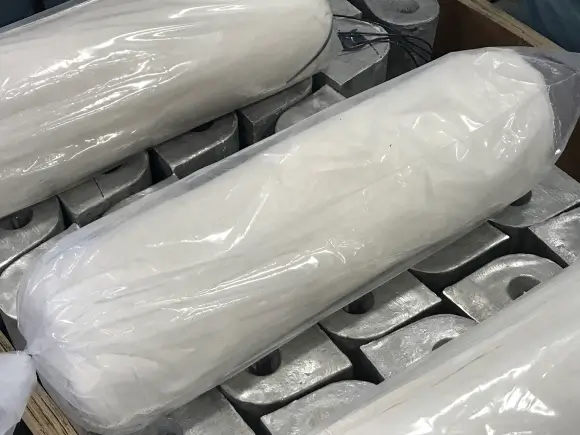
This process is much smoother using Shapr3D to communicate the model in the field and make adjustments as necessary. This type of troubleshooting in the field has resulted in significant cost savings. By adjusting a gap in the 3D model, the team was able to match their in-house tooling instead of needing to resort to outsourcing and built the final at two-thirds of the original cost. With the mass manufacturing of over 50,000 products per year and the building of 770 different assemblies that the team takes on, this cut to costs adds up.
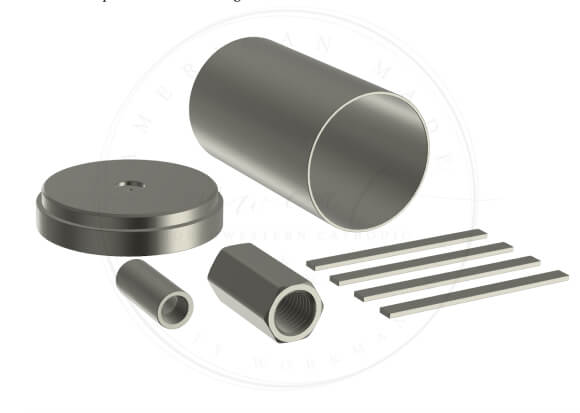
“Shapr3D is a very integral part of our business. A big part of any business is communicating ideas. We find that 3D models communicate ideas very well. Shapr3D is our primary tool for that.”
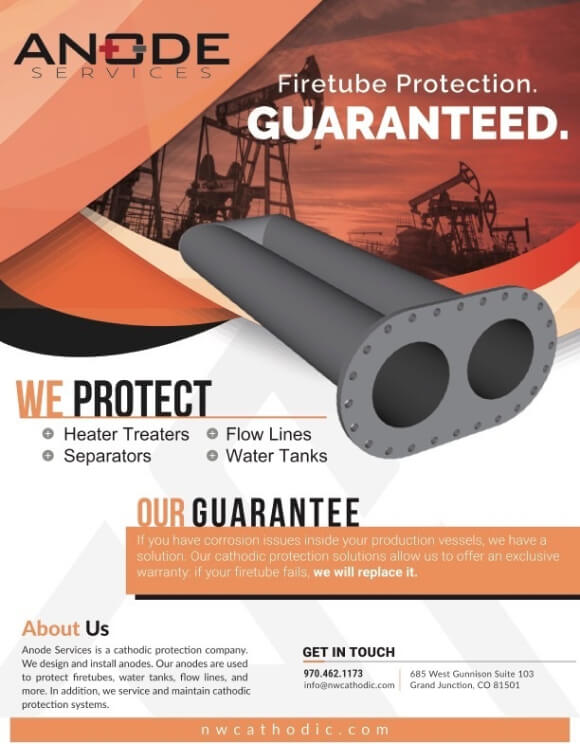
Mobility in communication trickles over into the company’s bottom line. By finalizing products fast, NWCAT can move on production sooner. Recently, NWCAT designed a safety product used in the utility space that prevents gas leaks in the ground. Without Shapr3D, they would likely still be in the midst of back-and-forth communication. Instead, the product took two weeks to produce. Last year the company sold over $750,000 of a product that otherwise would still be in the design process. Now it’s out on the market and they produce it every day.