Rev Limit Customs delivers faster custom hot rod design & manufacturing with fewer people
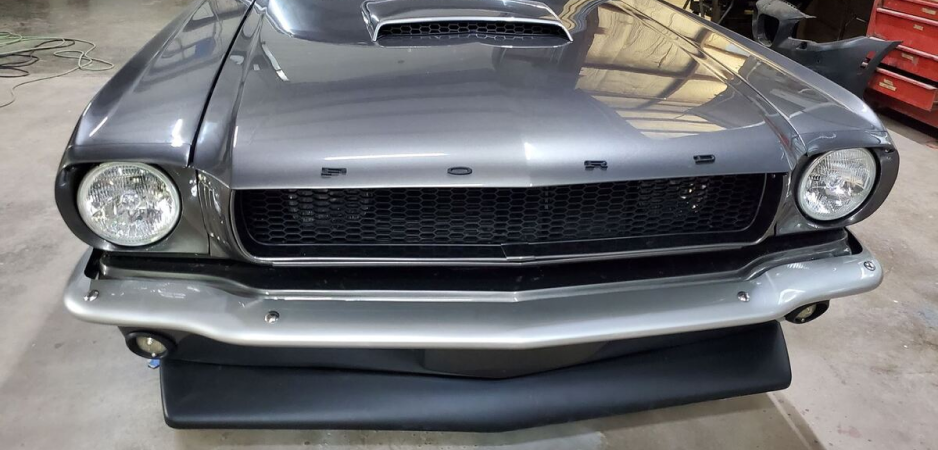
Overview
With the shutdowns of 2020 and 2021, Rev Limit Customs of Lubbock, Texas found themselves restricted in completing projects. Soon the custom hot rod shop was working with a backlog of projects and a lean crew due to industry-wide shortages. Building hot rods requires constant problem-solving.
The nature of building hot rods is that it requires problem-solving all the time - a crew excels when it has the flexibility to build on the fly. The challenge was to find best practices and implement them to solve the problem of delivering more efficiently long-term. Rev Limit Customs needed to bounce back from recently-mandated closures and worker shortages in the business.
With over half of the team turning to Shapr3D CAD to use in their workflow, the shop is back at full speed, delivering more with fewer people.
About Rev Limit Customs & Kyle
Rev Limit Customs delivers custom hot rods, muscle cars, and custom sheet metal fabrication along with parts production and delivery to clients in Texas and the surrounding states. Kyle Harder acts as the Project Manager, directing design work using Shapr3D, while also taking care of tasks such as estimating projects, carrying out billing and payroll, and meeting with clients.
With a packed day of responsibilities and a backlog of work to catch up on post-shutdowns, the instinctive ability to design parts quickly on the shopfloor is key. In addition to Kyle, the shop owner, Trevor, shop manager, Ryan, two fabricators, and a recent addition of a CNC machinist, use Shapr3D to design parts and speed up production.
Together, the crew has made a lot of progress over the past couple of years in turning around projects and building up their stockpile of parts for quick delivery.
Why Shapr3D
Kyle bought his first iPad strictly because of Shapr3D. While working in Colorado, he was tasked with building a large fireplace mantle and doing an art-hanging project. The structure was extensive in scale, fabrication, and design, but when the team was able to complete the final installation in an hour and a half, he was hooked.
Kyle’s experience with Shapr3D was that it was natural to use and quick to learn. Now Kyle speeds up project delivery at Rev Limit Customs by designing the parts that the guys need to keep them moving forward.
“It’s very relaxing and it’s a lot of fun. I’ll design for hours and hours without even looking up. I won’t even notice.”
Challenges
- Limited design communication can hinder buy-in & business growth
- Reverse engineering with cardboard can be time-consuming & cumbersome
- Worker shortage can limit design speed & innovation
Solutions
- Quick design finalization with Visualization and Webviewer
- Multidevice workflow & adaptive UI to boost reverse engineering efficiency
- Accessible CAD as a problem-solving tool
Finalizing products fast
Drawing out a part design can take time to do and for clients to understand. By switching from pencil and paper to drawing with pen on his iPad, Kyle can model a part design and show a lifelike 3D-rendered image of a part model using Visualization. This difference means he can communicate designs visually for clients to understand at their own pace, on their own time.
He gets to production more quickly with feedback from clients as well as other decision-makers like his boss or a team fabricator who let him know what to change.
“It really allows them to check out the designs at their own pace to see how things interact in spaces. [Using Visualization and Webviewer] relieves stress for people who don’t really get CAD or have difficulty visualizing a part, allowing them comfort in the process.”
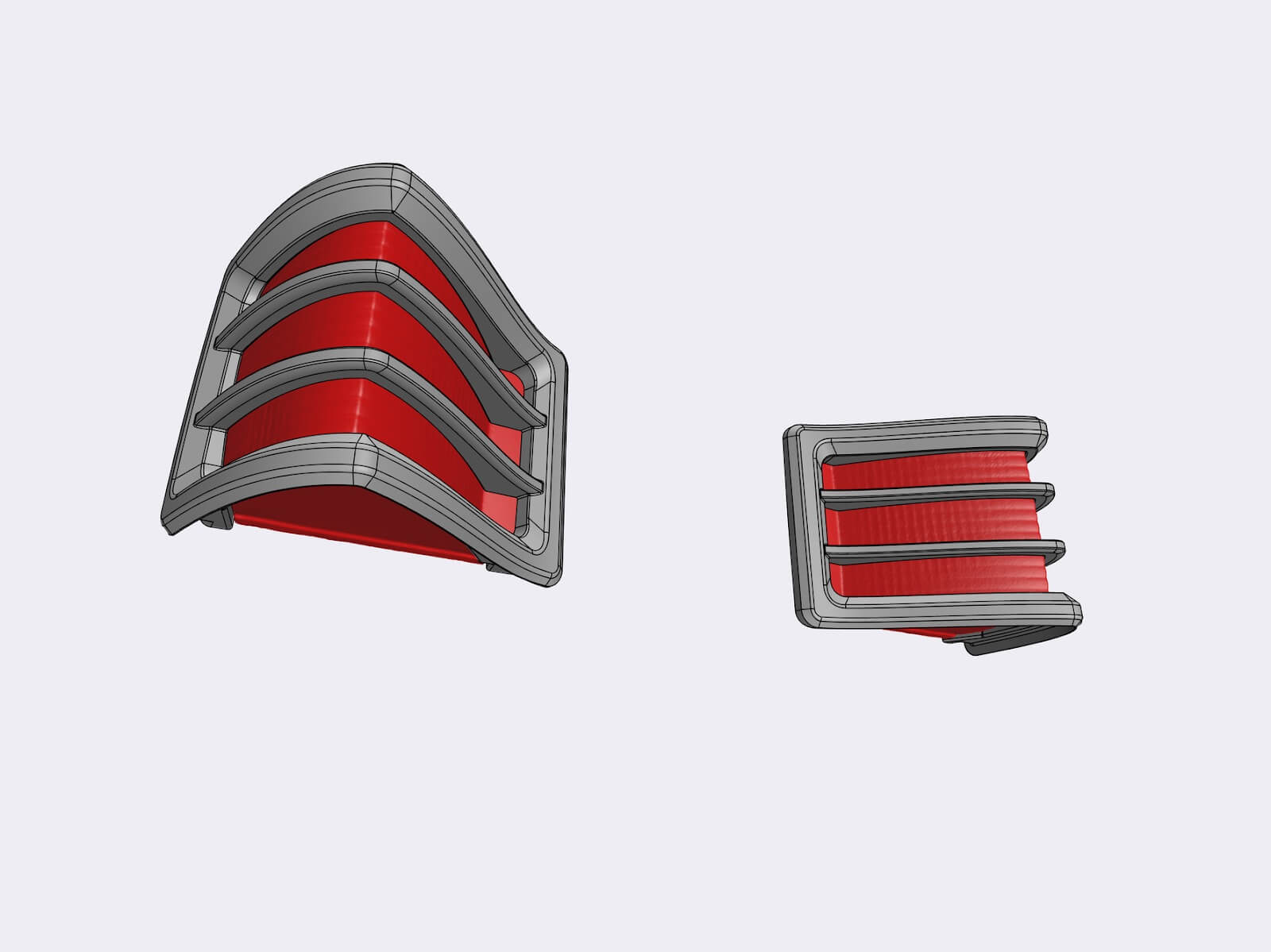
Often, he’ll use Webviewer to email over a model for a client to check out at their leisure. The immediacy of this bridge in communication translates into providing high-quality services for long-distance clients. Currently, he’s working with a client in Colorado who gave him a hand drawing to show what he’s hoping to build.
Kyle took the drawing and put it into Shapr3D, created a model around it, and sent it right back through Webviewer. This led to Kyle and his client taking on a slew of projects together using Webviewer to communicate and tweak final designs.
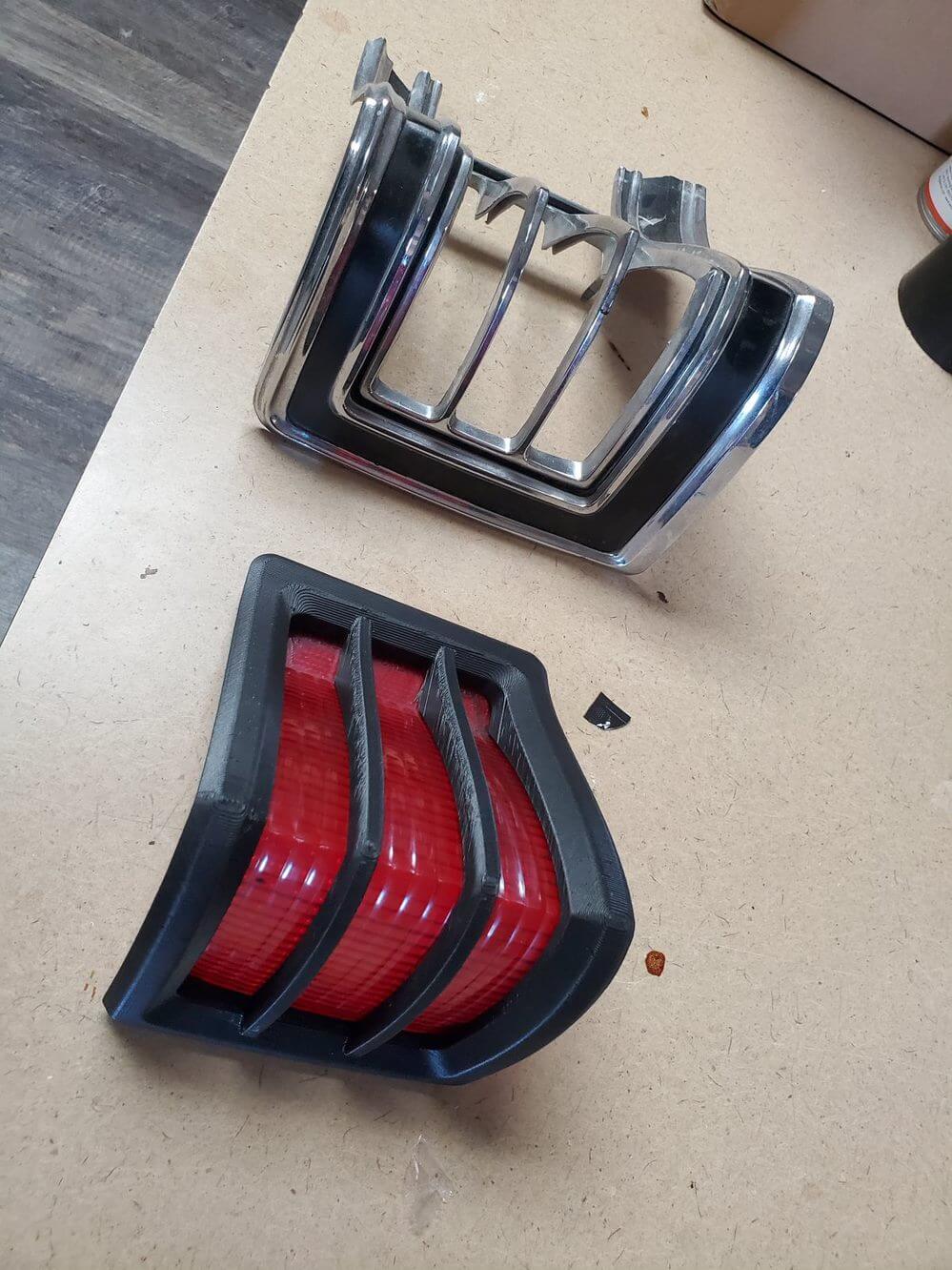
Design-ready with reverse-engineered parts on file
Recently, Kyle and crew supercharged a Lincoln they’re building out by putting on a motor from a Mustang. The catch was this didn’t leave a lot of room for the steering pump. To make the build work, Kyle decided to reverse engineer an electronic power steering pump that’s usually found on a 2015 Volvo.
Using his Einstar scanner, Kyle 3D scanned the part, found the shape, and went through sections and planes to find outlines. He “used Shapr3D magic” to fill in the design.
“I reach for Shapr3D first no matter what. I draw everything in Shapr3D. It’s fast and pleasurable to work in. I love drawing with the pen and using my hands to zoom in and out. It’s a quick and natural feeling. The enjoyment of Shapr3D is why I love using it so much. It’s just a blast.”
How would Kyle have done this in the past? “You can do it by hand with cardboard like how they used to but it takes forever,” he notes. Using Shapr3D means it speeds up the process a lot and makes it easier. Kyle gets to design on his couch at home instead of wrestling underneath or around a build in the shop.
Overall, the time that he spends creating an accurate model pays off. Whenever he creates a new design, he can select from a stash of designs, just pop it in, and design around it quickly. For Rev Limit Customs, 3D modeling with Shapr3D to reverse engineer designs is more mobile and effective and saves the team time.
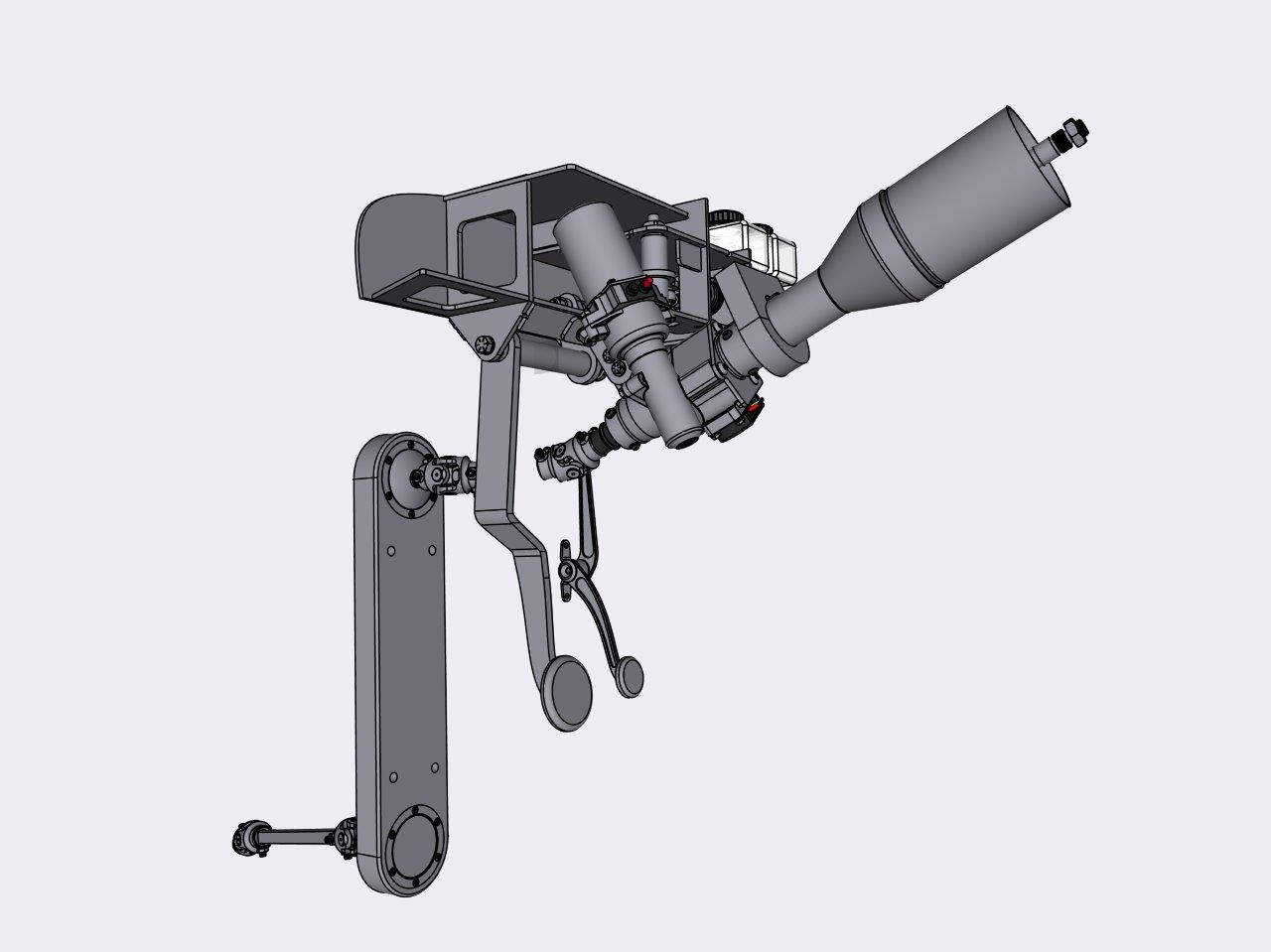
Instinctive CAD gives the team a problem-solving tool
With a smaller crew, the company needs to finish production for each part and build at a high level of efficiency. Shapr3D has saved a lot of time for the crew, especially in the beginning stages of drafting out concepts for parts. When Kyle joined Rev Limit Customs, the owner, Trevor, was already well-versed in Shapr3D.
Since that time, three of the builders, Harrison, Sheehan, and Caleb, have also picked up Shapr3D quickly to contribute to designing parts. Caleb, who specializes in the body portion of the builds, recently built a 29 Cadillac limo out with a diesel engine using Shapr3D. Kyle and Caleb scanned the original body and chassis and then created a 3D design.
“There’s no real hurdles as far as Shapr3D is concerned. Shapr3D is the problem solver, not the problem. It’s [helps with] working with constraints that we have like time, people, and materials - those kinds of things.”
The team of five using Shapr3D is set to grow to six with the addition of a CNC machinist who plans to use Shapr3D as a major tool in his workflow. Though Kyle is the main person designing parts, having others on the team proficient in CAD means that the group’s collective problem-solving ability is amplified. Now crew members who are proficient in their set area of expertise can create parts that match the needs that stand out to them.
The small shop tackles a full hand of projects. With a productive workflow, the team is moving on after cutting down its backlog to offering a competitive selection of high-quality parts and meticulously designed hot rods.
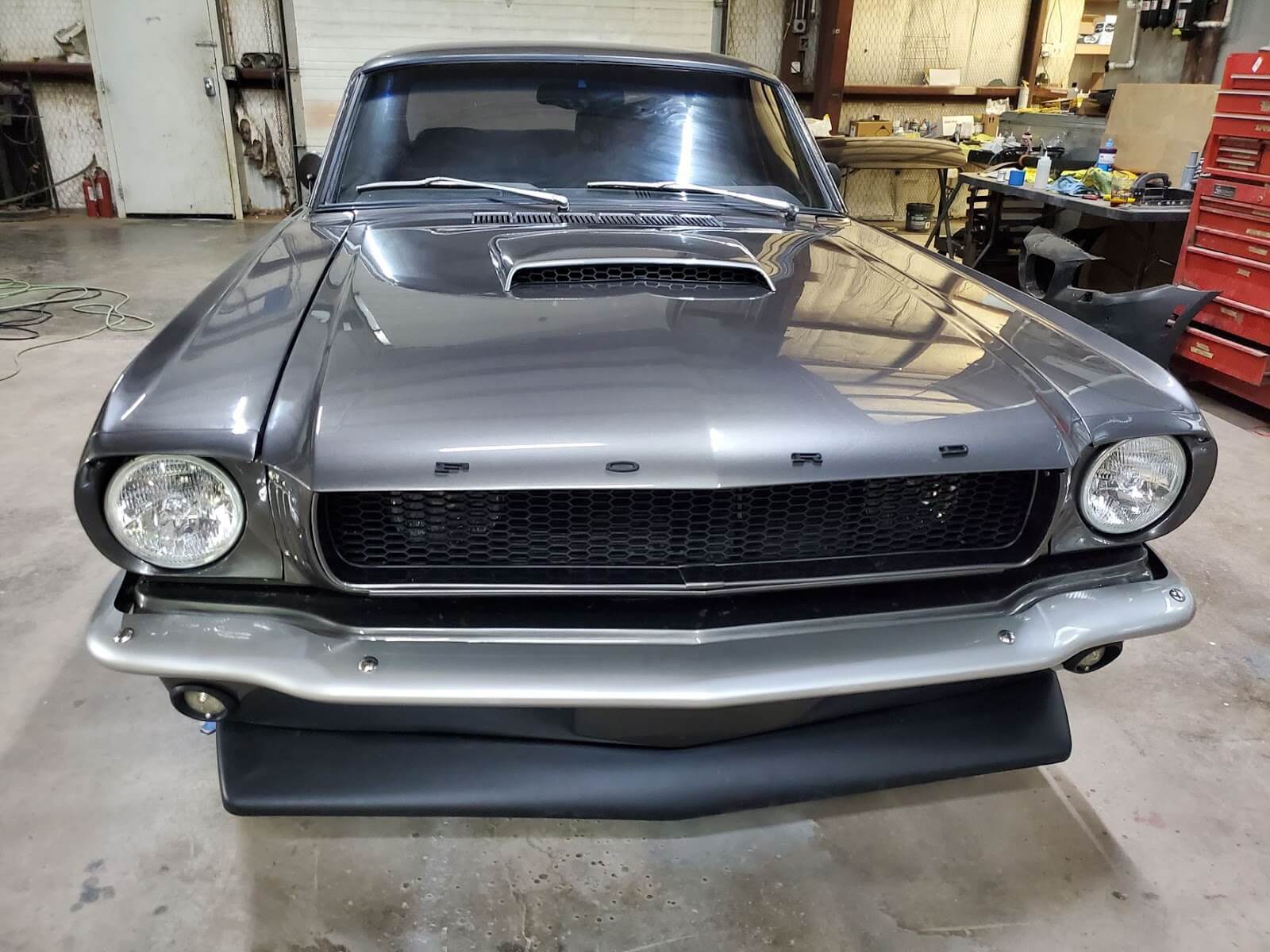