How Shapr3D helped a European OEM slash equipment design time from 12 to 6 weeks
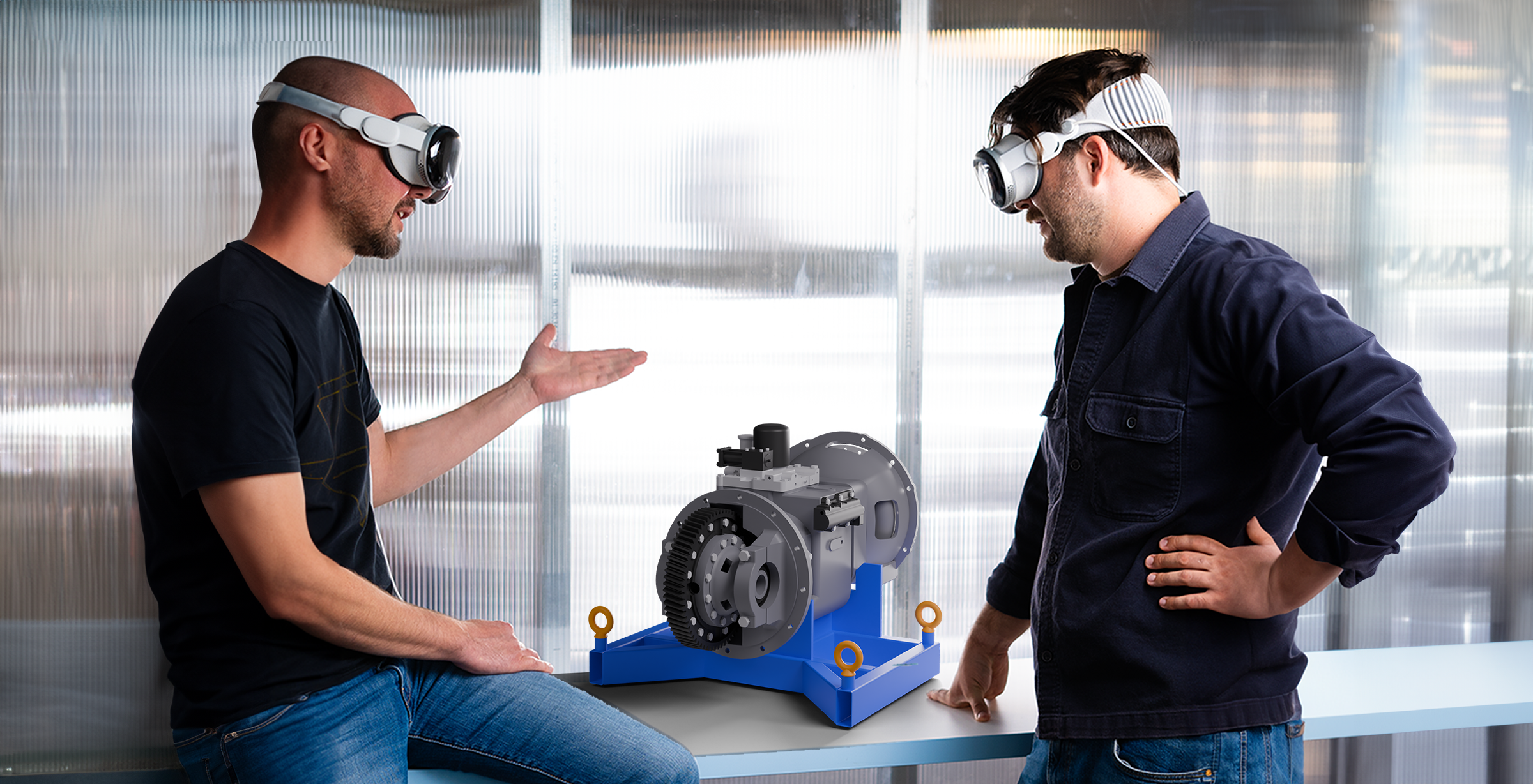
Today’s automotive market is defined by speed and adaptation. Once comfortable with 200- to 220-week development cycles, European OEMs now compete with new players like NIO, which has compressed those timelines to nearly half. But while competition heats up, many manufacturers face the same bottleneck: their process engineering teams are bogged down by outdated workflows and limited access to efficient tools.
Recognizing the urgent need to stay competitive, one leading European OEM launched a sweeping cost-reduction initiative aimed at saving billions of euros and accelerating production.
During this effort, the OEM’s Head of Digital Solutions and Flow Department realized that modern digital tools could mitigate production bottlenecks. However, steep software training demands, protracted 12-week design tasks, and prohibitively high CAD license fees made large-scale adoption challenging. These constraints prevented process engineers from quickly acting on improvement ideas, ultimately slowing production schedules.
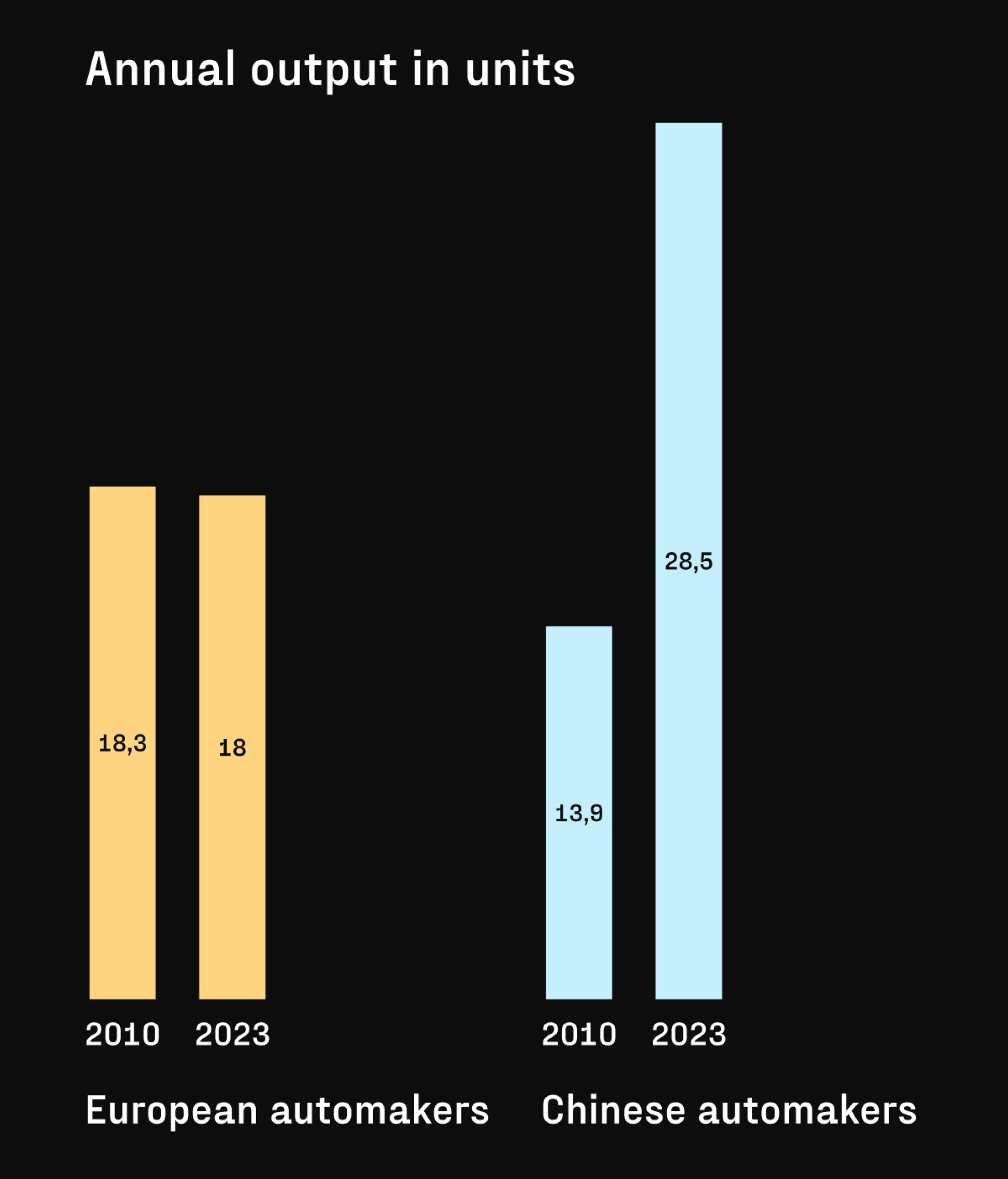
The challenges legacy CAD systems pose for process specialists
In analyzing their established workflows, the OEM pinpointed four primary issues:
- Lengthy design cycles: Standard equipment design tasks often took up to 12 weeks to complete, delaying production improvements.
- Restricted access: The system could only be operated effectively by trained CAD specialists, leaving process engineers dependent on an overburdened design team.
- Limited mobility: Desktop-based CAD systems were disconnected from shop floor workflows, making real-time validation and adjustments nearly impossible.
- High costs: At €15,000 per seat annually, the licensing costs of their existing system limited scalability across departments.
These limitations prevented process engineers from contributing directly to improvement projects, resulting in stalled workflows and a growing backlog of unaddressed design challenges.
Evaluating solutions: The role of Shapr3D
When faced with mounting delays and a growing backlog of unimplemented improvement ideas, this European OEM conducted a detailed study to find the best CAD solution for their process engineering teams. The evaluation compared tools like CATIA, Fusion 360, and Shapr3D, using key criteria such as onboarding speed, scalability, usability, and the ability to reduce equipment design timelines.
Shapr3D emerged as a strong candidate based on the following attributes:
- Rapid onboarding: Teams transitioned from CATIA to Shapr3D in roughly two days, bypassing the more extended training periods associated with traditional CAD systems.
- Significant time savings: Shapr3D shortened the typical 12-week equipment design process to 6 weeks, enabling more rapid integration of improvement ideas.
- Real-time mobility: Compatibility with tablets and mobile devices allowed process engineers to validate and refine designs directly on the shop floor.
- Cost efficiency: At €1,500 per seat annually (approximately 90% lower than CATIA), licensing Shapr3D was more feasible for company-wide deployment.
Real-world impact: Transforming workflows and reducing delays
The adoption of Shapr3D profoundly and immediately affected the OEM’s operations, particularly in addressing long-standing bottlenecks in their process engineering workflows. With traditional CAD tools, equipment design often took up to 12 weeks, stretching production schedules and limiting the company’s ability to implement continuous improvement initiatives. Shapr3D changed this dynamic completely.
By replacing legacy CAD systems with an intuitive, mobile-first solution, the OEM’s process engineers reduced equipment design timelines by 50%, completing projects in six weeks instead of 12. This acceleration allowed the company to keep pace with tightening production deadlines while freeing valuable time to address new improvement opportunities.
Beyond speed, Shapr3D fostered a level of cross-departmental collaboration that had previously been unattainable. Teams from logistics, prototyping, and ergonomics, who once worked in silos, were now able to co-create designs in real-time. For example, the logistics team, which had long relied on external CAD designers for equipment studies, could now independently design and validate 3D models for critical tools like trolleys and fixtures. This shift saved weeks of back-and-forth and ensured that designs were aligned with on-the-ground realities from the start.
One standout example of Shapr3D’s impact was in the logistics department, where equipment design and validation processes were historically bottlenecked by slow iteration cycles. With Shapr3D, process engineers used tablets to refine designs on the shop floor, validate them in real time, and implement changes within hours rather than weeks. This capability accelerated production workflows and reduced the risk of costly errors.
Key insights for manufacturing leaders
This case offers valuable insights for manufacturers aiming to streamline workflows and enhance productivity:
- Empower process engineers with accessible tools: Shapr3D’s intuitive interface enabled engineers to create and refine designs independently, reducing delays caused by reliance on CAD specialists.
- Integrate mobility into workflows: The ability to validate designs directly on the shop floor ensured faster alignment and better outcomes.
- Scale design access affordably: Lower licensing costs allowed broader access to 3D tools, democratizing the design process and enabling more voices to contribute to innovation.
Bridging concept and execution
As automotive manufacturing becomes increasingly competitive, tools that support rapid iteration and broad collaboration are becoming more important. By shifting from traditional CAD platforms to Shapr3D, this European OEM realized a faster, more inclusive equipment design process. In doing so, they established a model for continuous improvement that leverages accessibility, mobility, and cost savings to streamline product development.
The OEM’s experience suggests that a user-friendly, mobile-ready CAD solution can be instrumental for organizations aiming to shorten timelines and involve more stakeholders in design. In this instance, Shapr3D not only accelerated workflow but also fostered an environment where process engineers, logistics teams, and ergonomics specialists worked together to develop practical and innovative solutions.