Rewriting automotive design: One German OEM’s success in shaving weeks off prototyping with Shapr3D
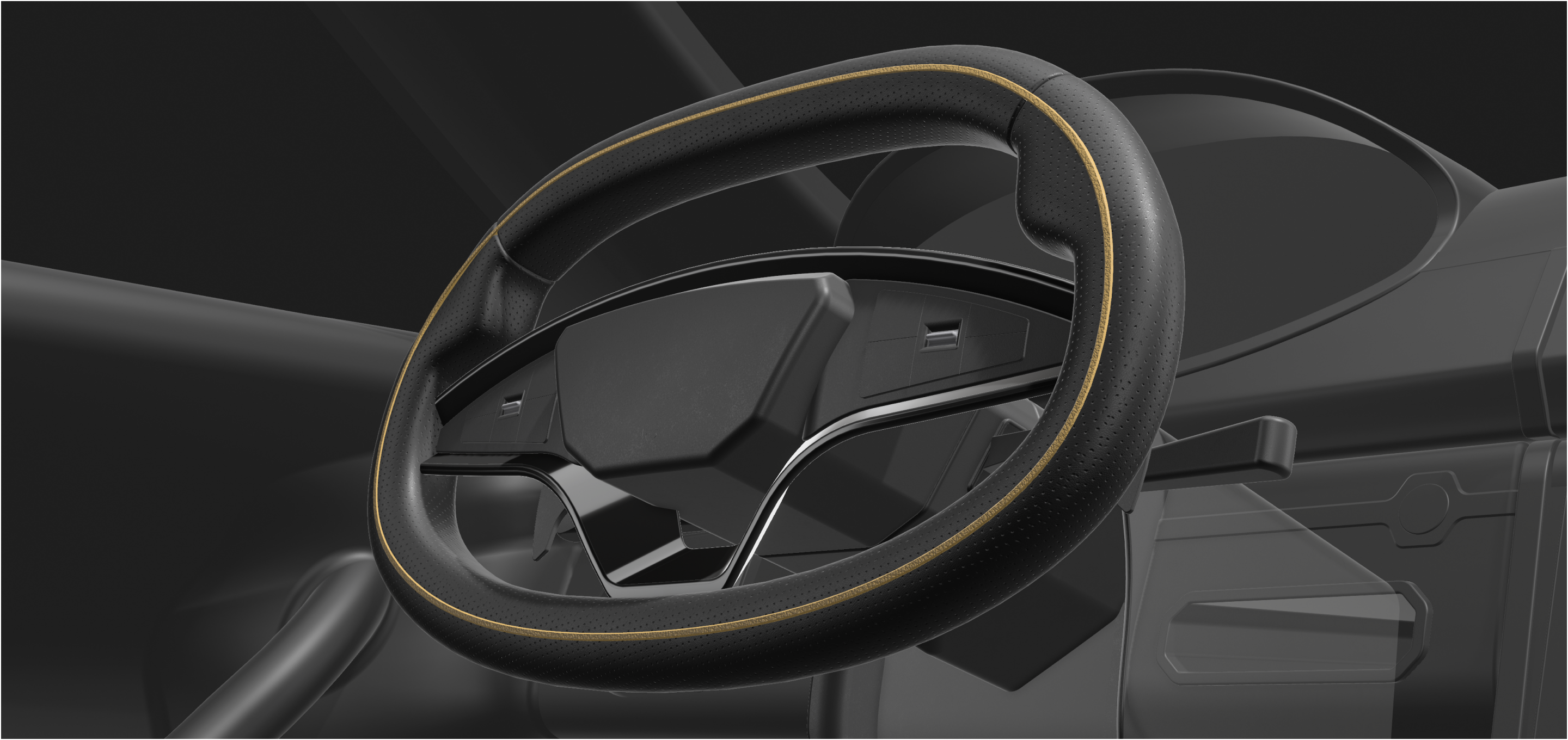
Automotive design today demands meeting a rigorous 100-week development cycle—a feat of speed and unerring precision that only a willingness to challenge engrained processes can achieve. Recognizing the limitations of conventional design practices, a German OEM reexamined every step of its process, from initial concept to finished product, to eliminate friction and boost efficiency. By adopting Shapr3D, the team has transformed its approach, drastically reducing prototyping time and streamlining collaboration among multiple stakeholders.
Revisiting traditional workflows
The design process at this German OEM historically involved numerous touchpoints and a diverse set of tools. Multiple different stakeholders were responsible for various aspects of the process, yet challenges abounded. Communicating complex designs via static PowerPoint presentations, transitioning between multiple toolsets, and managing cumbersome design reviews all contributed to inefficiencies. Moreover, setting up immersive experiences, such as VR environments, required various personnel to configure and deploy, significantly delaying feedback. These traditional workflows led to substantial delays and increased costs, underscoring the need for a more streamlined approach.
- Delayed prototyping: Physical prototypes emerged late in the design cycle, often stalling decision-making. For instance, an industrial designer’s innovative idea got lost in a cluttered PowerPoint process and was initially rejected by a high-level decision-maker. With Vision Pro streamlining communication, the idea was successfully realized—leaving even its toughest critic impressed.
- Fragmented toolsets: Transitions between disparate design and engineering platforms created bottlenecks and inconsistencies.
- Inefficient communication: Static visuals for design reviews limited stakeholder engagement and clarity.
- Excessive engineering dependencies: Designers often used tools like Blender or Alias, which produced geometry that wasn't optimal for downstream operations such as 3D printing. As a result, engineers working with CATIA had to spend additional time correcting these issues, leading to significant backlogs and inefficiencies.
While these methods had been the norm, they increasingly hindered the company’s ability to innovate quickly and effectively.
Faced with these challenges, the OEM undertook a comprehensive review of its design operations.
The Shapr3D transformation: Four key use cases
Through a comprehensive evaluation, the German OEM’s design team identified four core areas where Shapr3D provided significant improvements, effectively serving as the central link in their design ecosystem.
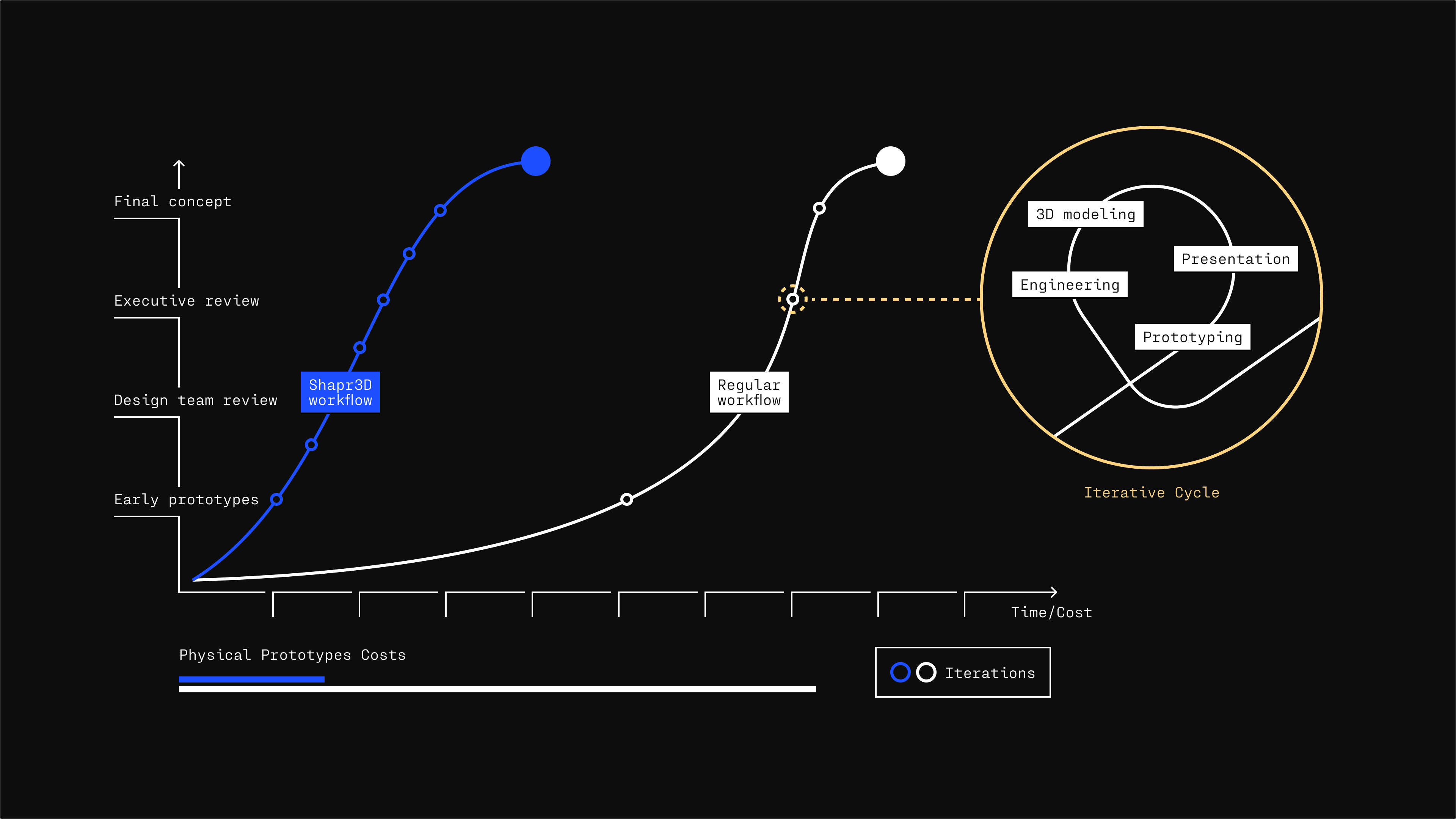
Rapid prototyping with XR integration
Before Shapr3D: Prototyping relied on lengthy physical models and complex setups, with XR design reviews taking up to two weeks.
With Shapr3D: The turnaround for XR prototype presentations has plummeted to just two hours. Additionally, any team member can now independently manage XR sessions, enabling real-time collaboration across global teams. This has led to faster, more informed decision-making, accelerating the transition from concept to production.
Immersive, high-fidelity presentations
Before Shapr3D: Design concepts were communicated via static slides and 2D visuals, reducing clarity and extending preparation times.
With Shapr3D: Presentations now occur in immersive XR environments, dramatically increasing the fidelity of design concepts. Presentation preparation time has been reduced from 16 hours to just 2 hours, with the cost per presentation dropping by over 80%.
Democratized 3D modeling
Before Shapr3D: Complex models required collaborative efforts using tools like Alias and Designer—often involving two specialists over a week, and non-CAD experts spending up to 16 hours on 3D modeling tasks.
With Shapr3D: An impressive 10x improvement in team productivity. How? The same complex model could be created by a single expert in just 3 hours, while non-CAD users finished similar tasks in approximately 1.6 hours. One industrial designer leveraged Shapr3D to quickly sketch concepts and streamline communication, reducing time spent debating 2D ideas. This democratization also enabled the independent development of simpler designs, such as a special key or solar charging stations, without relying on a dedicated surface modeler.
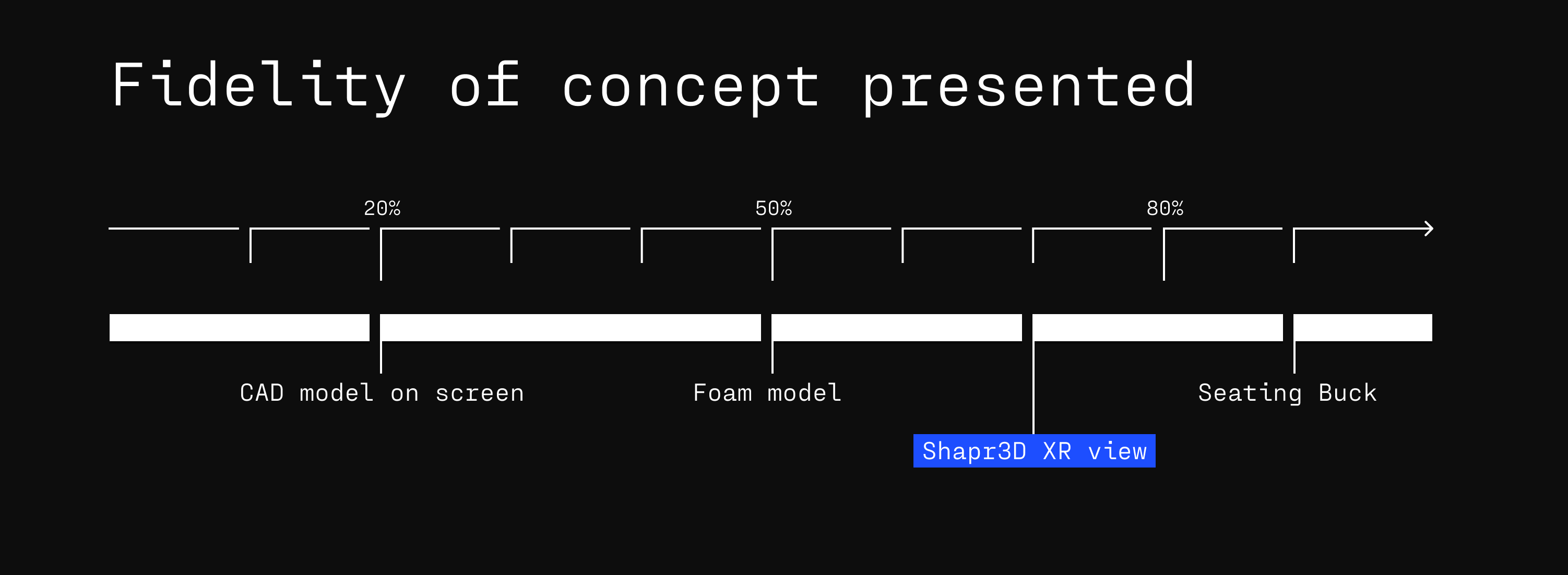
Eliminating engineering bottlenecks
Before Shapr3D: Designers frequently depended on engineering teams to fix geometry issues, with engineers spending up to 80 hours per year on corrections, while collaborative review time between designers and engineers was as high as 20 hours per project.
With Shapr3D: Designers now handle geometry fixes independently, reducing engineer intervention to 0 hours per year. Collaborative review time has been halved to 10 hours per project.
A blueprint for future innovation
With a successful pilot under its belt, the German OEM now plans to roll out Shapr3D more broadly across its design teams. The roadmap moving forward includes expanding access beyond the core concepting teams to encompass engineering and cross-functional groups, ensuring that every phase of the design-to-production workflow benefits from faster, more cohesive alignment.
In an industry where innovation is one of the foremost concerns, this German OEM’s adoption of Shapr3D demonstrates that even a cumbersome process can be significantly enhanced with modern, flexible tools. Shapr3D is proving indispensable for driving better collaboration and expediting design cycles.