How Sohbi Craft implemented a production line in under 4 months
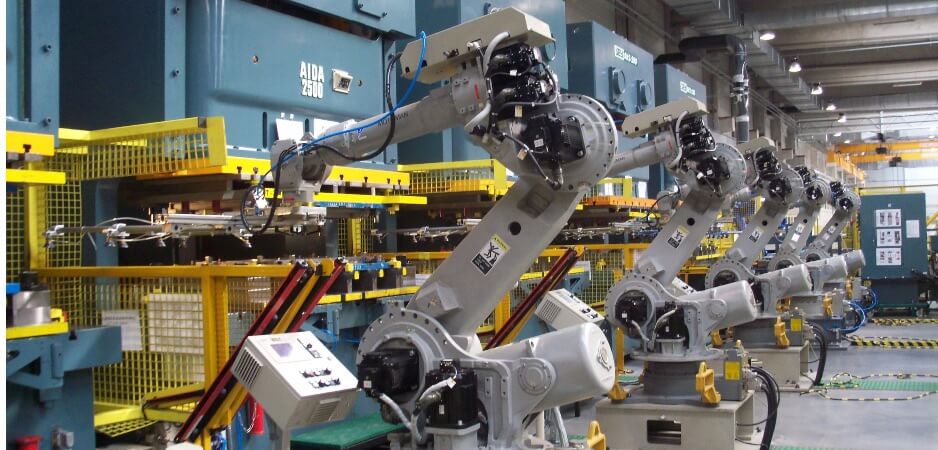
Overview
With a production line simulation project to design and implement in just a few months, Expert in Production Engineering, Marcin of Sohbi Craft Poland picked up Shapr3D. Fresh to CAD, the initially intimidating task of learning CAD became enjoyable while the ability to design parts came naturally.
Now Marcin has the first phase of implementation secured. He and his colleagues from various global branches consider Shapr3D to build team efficiency with accessible CAD. Let’s explore why.
About Marcin & Sohbi Craft
Marcin is an Expert in Production Engineering with Sohbi Group, an international automotive part manufacturing company. The global enterprise creates high-quality parts made from sheet metal stamping using mass production technology alongside mold technology.
While Marcin works at a Sohbi Group branch in Poland, he frequently travels to the company’s headquarters located in Japan and to other branches throughout Asia. Currently, he is implementing a line simulation project he designed using Shapr3D that increases efficiency and speeds up production. He recently traveled to the Philippines and Japan to meet with engineers, designers, and technicians to implement the first phase.
Why Shapr3D
Marcin found that in order to simulate lines properly, he needed to access equipment models. In order to test out the equipment of production lines, he needed accurate models of the various parts to test their spatial requirements, reliability, and capacity. Many 2D or 3D models of equipment were hard to come by either due to the model being older or because companies hadn’t kept documentation of models created in the past.
Marcin’s other option was to turn to designers or engineers on his team to create the models he needed. This involved potential delays in turnaround and saddled his colleagues with extra work. Marcin quickly realized CAD was indispensable to achieve the flexibility and speed he needed to create equipment models. The catch was he had no prior CAD experience.
Then Marcin came across Shapr3D. The CAD tool gave him the ability to create his own designs quickly, communicate them to design and engineering teams, and implement them in simulations for manufacturing. Marcin’s team looked to Shapr3D for a similar boost in CAD proficiency to boost cross-team collaboration and production efficiency.
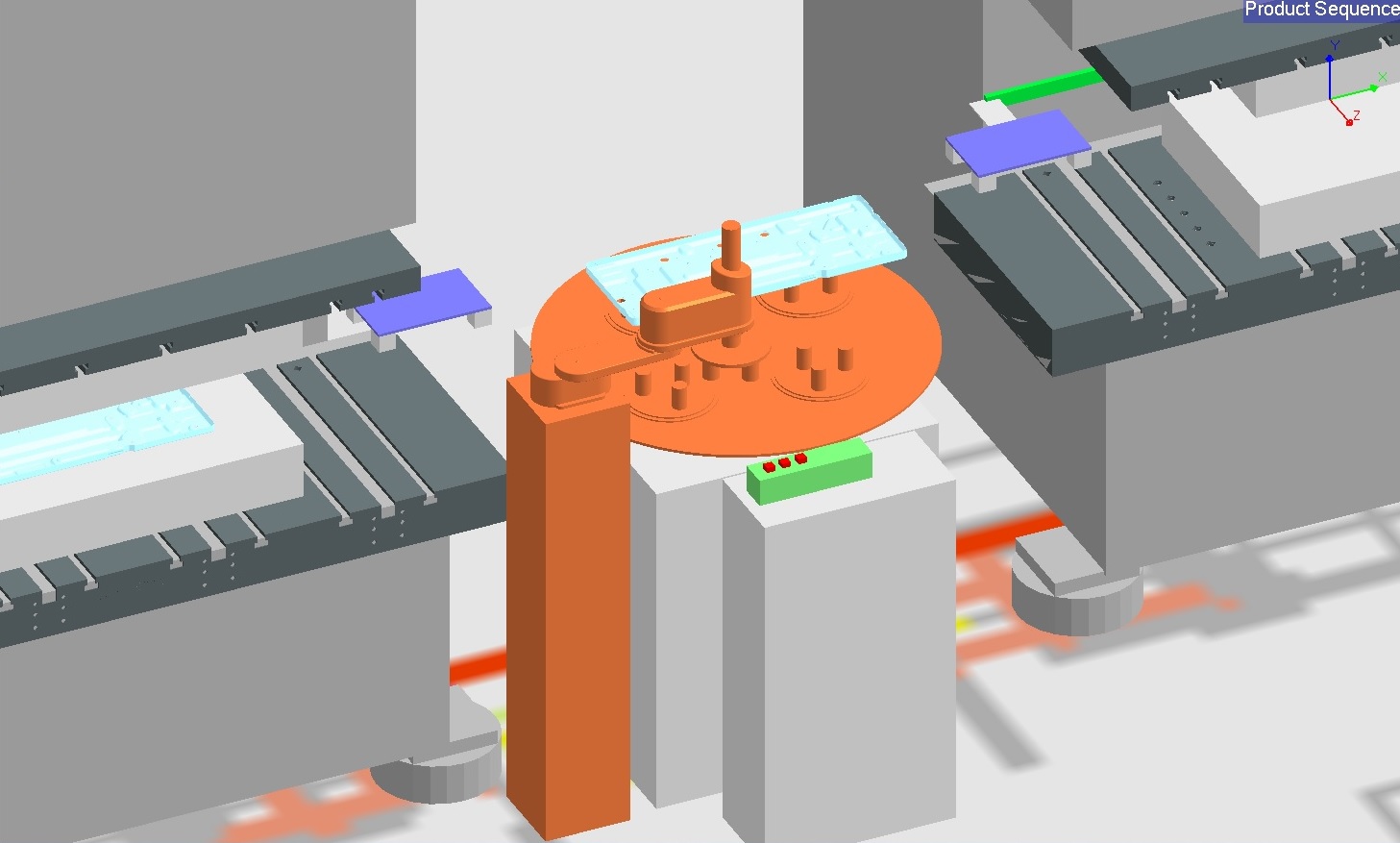
Challenges
- Outsourcing design takes extra time & personnel
- Cumbersome software limits design flexibility
- Limited design accessibility impedes communication for teams
Solutions
- Short CAD learning curve enables independent design
- Multidevice capability & interoperability enable a frictionless workflow
- Teams equipped with Shapr3D communicate more efficiently
A short CAD learning curve speeds up production line implementation
Marcin started using Shapr3D in December of 2022. By March of 2023, his newfound CAD skills had enabled him to complete line production design and successfully implement the first phase. Marcin didn’t have any prior experience using CAD and was looking for a tool that he could learn fast amid his hectic schedule of traveling and strategizing.
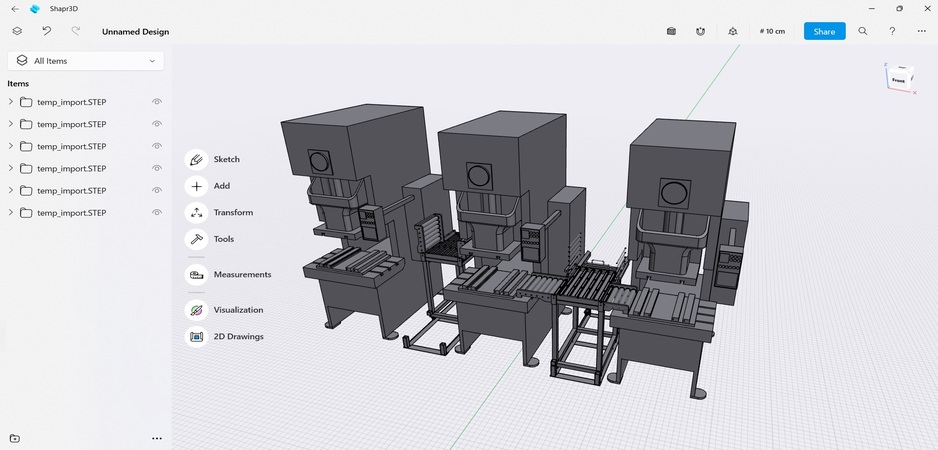
Previously, he needed to turn to in-house designers to communicate and then create models he needed to test out in line simulations. This process could take extra time. In an effort to conserve team resources and speed up the design process, Marcin began using Shapr3D. For Marcin, Shapr3D was quick and easy to learn and gave him the independence he needed to design parts.
“95% of the time I need to prepare [line assembly components] quickly so I use Shapr3D.”
Similarly, Marcin’s team in the Philippines is interested in increasing overall team capability to join in on the design process. Technicians can design parts such as boxes and jigs and fixtures for mass production lines to increase efficiency.
Designing from anywhere, connected with all needed tools
Marcin gets requests from internal and external clients and does visits to observe their existing or new production lines. Shapr3D’s multidevice capability enables him to document and address their needs quickly. For Marcin, it’s important to have the freedom to take measurements while observing assembly lines, particularly of parts with unique shapes for which models don’t exist.
He can design parts right on the floor on his iPad, throw them together in the Shapr3D environment, and use seamless file export to put them in a simulation in his go-to virtual line production software, GP4D from Fujitsu. He reflects on the process, noting that Shapr3D allowed him to design assembly lines “super fast.”
“I’m not sure if that was the intended use of Shapr3D. I know that it can be used to create quick 3D designs and share them with customers. But I have found that in my line of work, actually, it was super useful and super easy to use with the simulation.”
While Marcin can move around freely in order to create his designs, he also finds all-around compatibility essential to import-export freely with other software he uses in his workflow. Marcin compiles models he needs for line production by importing them into Shapr3D, and then modifying them to fit his own needs. He frequently imports models as OBJ, STL, or VRML files from GP4D. In order to animate equipment in GP4D, he uses models he’s modified in Shapr3D as pieces he can use in simulation.
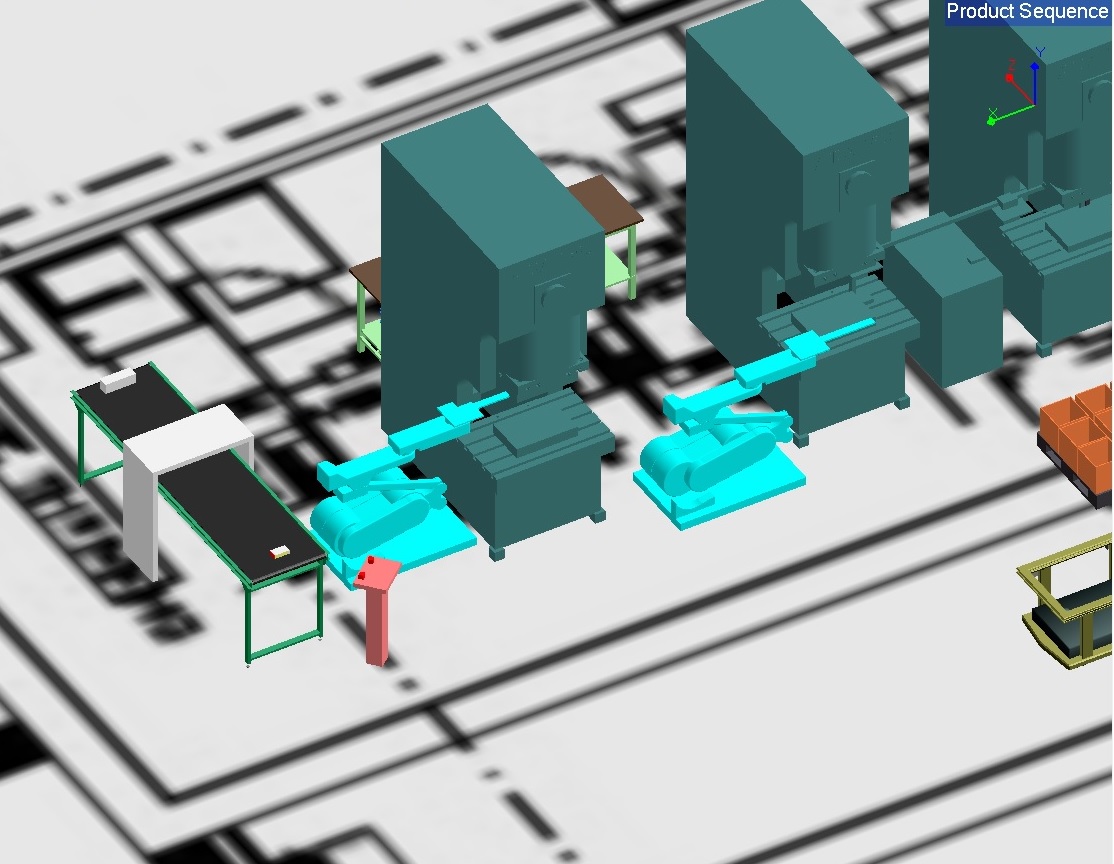
To do so, he exports a model from Shapr3D as an OBJ file to GP4D. Then he uses a conversion tool, GP4SGS, to import the models in an OBJ format and convert them to a GPE file. While GP4D has a very simple and accessible functionality, developing his own equipment using Shapr3D allows Marcin to speed up the design process.
Veteran and rookie CAD users turn to instinctive CAD
In the past, communicating his design ideas to engineers and designers was challenging. Now, Marcin can use Shapr3D to show his ideas as 2D Drawings or a full-fledged 3D model using Visualization. And alongside colleagues working on the floor on production lines, engineers using SolidWorks are also looking to design parts in Shapr3D due to the speed of concepting.
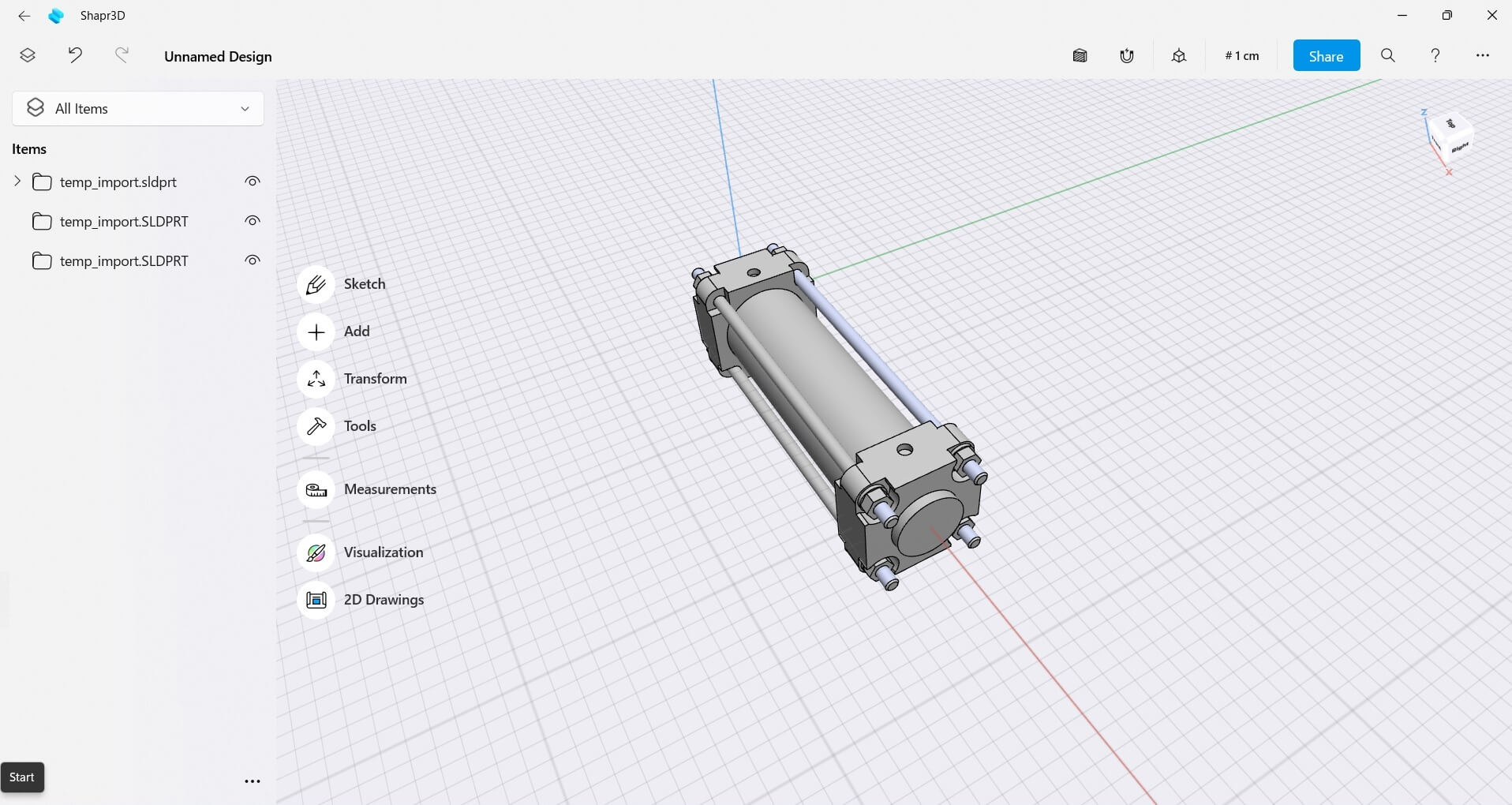
For the engineers, using SolidWorks requires daily sustained use to maintain proficiency, so the instinctiveness is a draw. Since Shapr3D is built on the same geometric kernel as SolidWorks, he can easily export any model from Shapr3D as an X_T or STEP file to share with colleagues. This process speeds up overall implementation of a part.
“I love Shapr3D. It allows me to skip learning CAD software which would take me a good couple of months. I can prepare a model within minutes or a few hours. I can show it to project engineering management and they can understand it and we can discuss the simulation and it works.”
Marcin and his colleagues came across barriers when considering implementing CAD across teams. He notes that most CAD tools can be very costly and take a long time to be able to use properly. With Marcin’s recent success of implementing a new production line simulation in just four months, his colleagues in the Philippines are interested in trying it out to build assembly line boxes and jigs and fixtures among other parts.
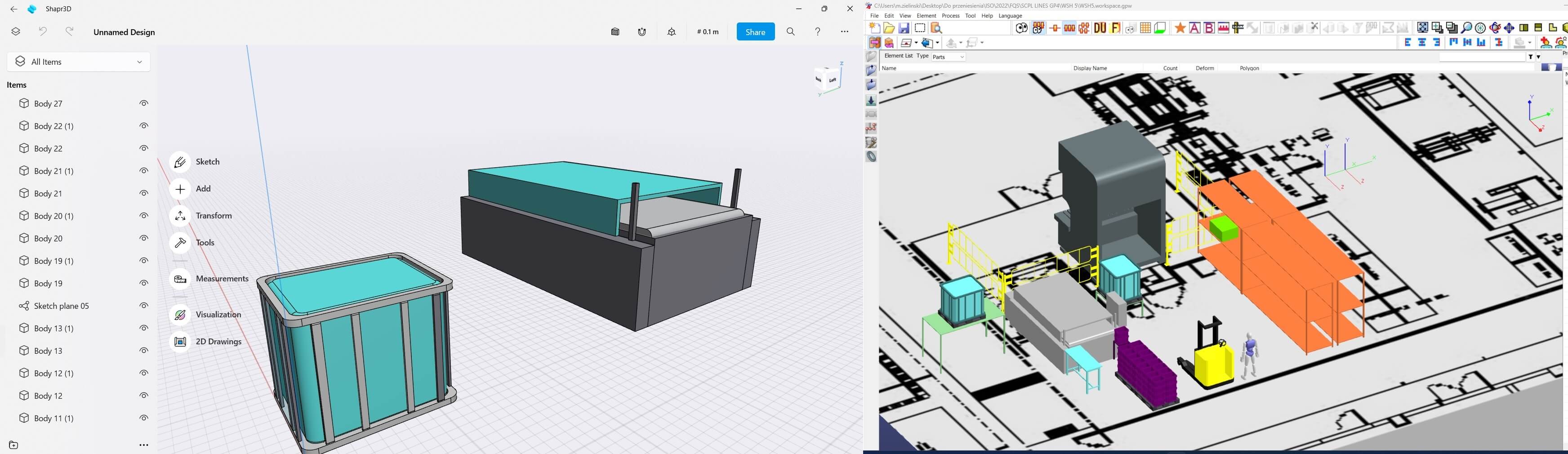
The team noted how Marcin’s ability to communicate designs was important for his project. Reflecting on the timeline of the project, Marcin takes pause to emphasize, “The first stage of implementation wouldn’t have been possible without Shapr3D.”